Abstract
In this paper authors address the issue of local damage detection in rolling element bearings in the presence of non-Gaussian noise. Typically damage detection problems concern the techniques of filtration, decomposition, separation, extraction etc. In such real-life cases, main difficulty lies in non-Gausianity of the noise present in the operational environment, hence popular denoising techniques cannot be used. In presented article, a real-life industrial scenario will be discussed and a new approach to cyclic component extraction will be presented. Classical detection methods are often not sufficient for the task because of high energy of impulsive noise in comparison to spectral structure of the damage. Proposed method utilizes Cyclic Spectral Coherence map as two-dimensional data representation, and Nonnegative Matrix Factorization as analytical tool to extract individual components.
1. Introduction
Identification and diagnostics of damage in rotating machines is still an open subject. For such kind of analysis the most frequently used medium is vibration signal. In case of local damage, faults like cracks, pitting or breakage manifest themselves in the vibration signal as cyclic, impulsive and typically nonstationary components. It is critical to detect such anomalies in early stage of damage evolution to avoid unexpected and costly stoppages in the future. From the perspective of signal processing, the problem comes down to identification of impulsive component buried in wideband stationary background, that can consist of Gaussian noise and deterministic components, for example meshing components for gearboxes [1].
In general vibration signal needs to be preprocessed to extract so-called Signal of Interest (SOI). Such preprocessing can be performed using techniques such as bandpass filtering, wavelet decomposition [2], adaptive filtering [3], statistical modeling [4, 5], time-frequency analysis [6] or cyclostationary analysis [7, 8]. Unfortunately, in case of real-life industrial signals such classical methods of diagnostic analysis are prone to insufficient effectiveness. It is necessary to introduce specialized multidimensional representations of the data that are able to tackle the issue of frequency-related analysis. In relation to such representations, it is required to incorporate specialized analytical techniques that can extract information in a different way.
In presented paper authors reach for the bi-frequency representation called Cyclic Spectral Coherence map (CSC), that can reveal modulation spectra related to different carrier frequencies. To analyze such representation, Nonnegative Matrix Factorization (NMF) is used for differentiation of spectra that are connected to different processes occurring within the signal [9-11].
1.1. Object of interest
The studied machine is a gas compressor of a type Dresser Rand C-VIP, that has been already studied by Barszcz et al. [12]. The key issue is that vibration signals generated by the compressor contain a number of external disturbances, the most influential being the piston-related and valve related ones. It has been discovered that the analyzed signal has been recorded when the bearing inner ring has been severely defected in one of the main shaft bearings. Details including the SOI parameters are presented in Table 1.
Table 1Machine-related frequencies
Parameter | Frequency [Hz] |
Sampling frequency | 24000 |
Shaft speed | 12.35 |
BPFI | 127.9 |
Impulses at the rate of approximately 12.35 Hz are observable. They reveal themselves directly on the DFT spectrum, dominating its low-frequency part (up to about 3 kHz), while the further part of the spectrum appears to be a noise-like behavior. Since the 12.35 Hz is the rotational speed, it is obvious that the main impulsive component is piston and valve-related. Bearing fault related impacts are not detectable on the spectrum.
2. Methodology
In this section the presented methodology is described. Firstly Cyclic Spectral Coherence map is calculated for raw input data, which is then provided to Nonnegative Matrix Factorization algorithm for selector bank definition. When selectors are defined, they are used as ordinary filters used to filter the original signal. Filtration with each of the filters outputs one of the signal components. General flowchart of the procedure is presented in Fig. 1.
Fig. 1Flowchart of proposed procedure
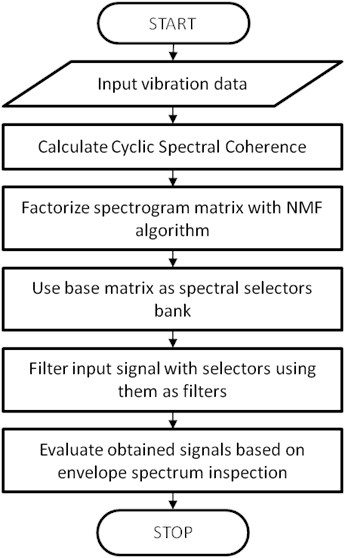
2.1. Cyclic spectral coherence
In signals coming from rotating machinery for each carrier frequency different modulation frequencies can arise. Hence, bi-frequency method should be used in such analysis. In order to describe this effect Antoni in 2007 introduced the spectral coherence (SC) [13]. Let us remind the cyclic power spectrum (CPS) of the signal :
where is Fourier transform of the signal calculated on interval of length . According to Eq. ((1)) the CPS describes dependence of the spectral components being apart by given modulation frequency for carrier frequency . Obviously, the cyclostationary signal is expected to reveal for modulation frequency . Given the definition of CPS, the formula for SC can be defined [13]:
Obtained statistic is normalized. Therefore, SC quantifies the spectral cyclic autocorrelation of the signal. Indeed, when is close to one then signal reveals the cyclostationarity property at carrier frequency f with modulation period equal to . According to Eq. ((2)) the estimation of SC can be directly performed with estimator of CPS. Namely, the estimator of SC is given by formula:
where is an estimator of the CPS.
2.2. NMF
Nonnegative Matrix Factorization has been selected as separation method. Thanks to general inherent clustering properties of NMF-type algorithms such method can be used to aggregate different types of behavior within the analyzed matrix into separate classes. Presented methodology uses classic NMF with Euclidean objective function and multiplicative update rule [14].
3. Application to real data
Fig. 2 illustrates a short section of vibration measurement that has been used for analysis. As a first step, CSC map has been calculated for full Nyquist range and up to 300 Hz of modulating frequency, with the 128-sample Hamming window, 110-sample overlap and 256 FFT points (see Fig. 3).
After that the map has been provided to NMF algorithm that recognized different spectral signatures of the desired components (see Fig. 4).
Fig. 2Raw vibration data
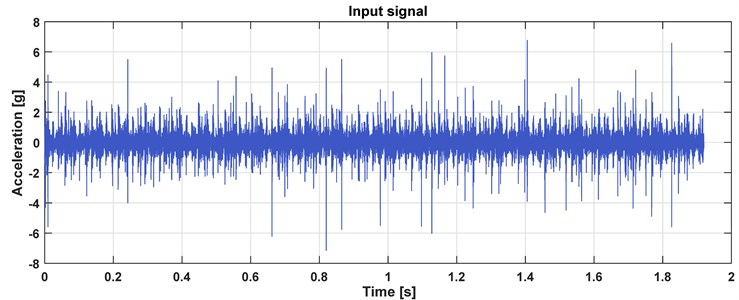
Fig. 3Cyclic spectral coherence map
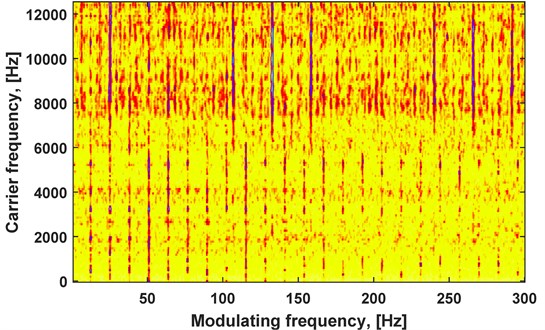
Fig. 4Construction of filter bank using NMF base matrix
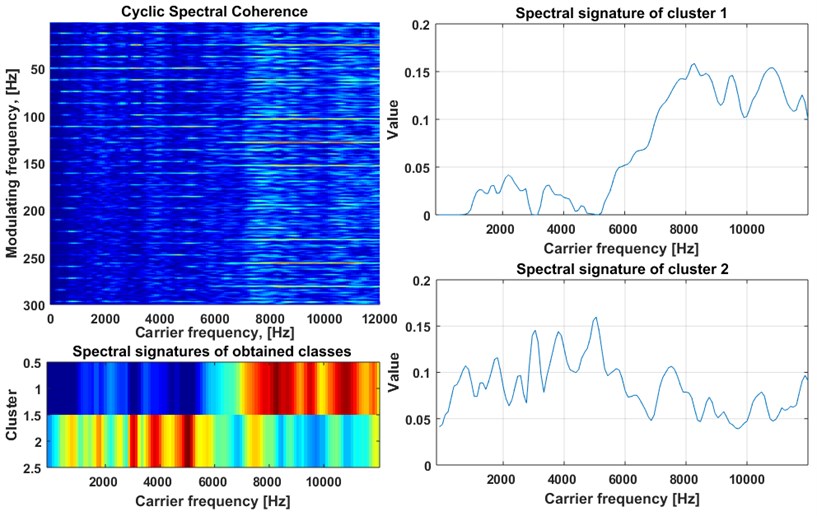
Input signal has been then filtered with both of the spectral signatures to produce two output signals, each dominantly carrying one of regarded cyclic components.
While time series of obtained components reveal impulsive components much more clearly than the original signal (Fig. 5(a)), their regarded periodicity is most pronounced in the envelope modulation spectra (Fig. 5(b)). First cluster reveals desired information about bearing fault cycle recognized as 127.8 Hz for the fundamental modulating frequency, and second cluster presents expected shaft cycle with fundamental modulating frequency recognized as 12.45 Hz, which corresponds perfectly with theoretical frequencies calculated based on machine kinematics, down to FFT sample precision.
Fig. 5Results of method operation: a) extracted time series, b) corresponding envelope spectra
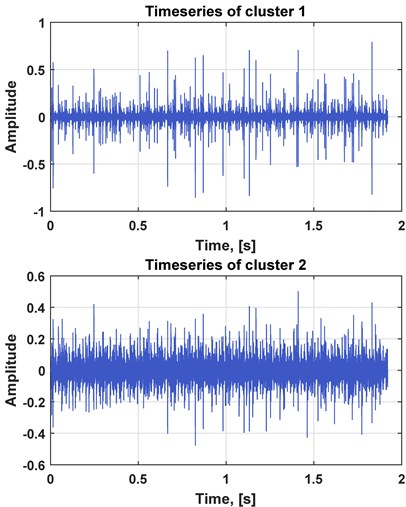
a)
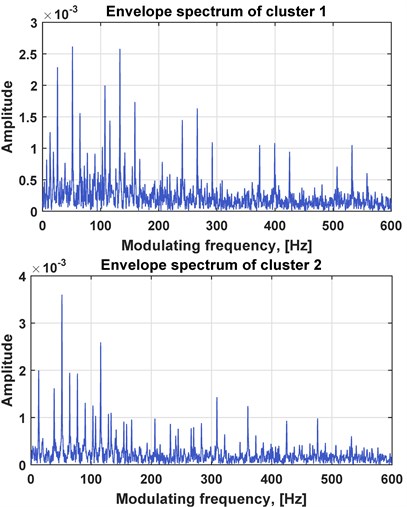
b)
4. Conclusions
In presented article authors focused on the problem of fault frequency component identification in vibration data from gas compressor. Cyclic Spectral Density map is used as multidimensional signal representation, and it is used for informative frequency band identification performed further by classic Nonnegative Matrix Factorization algorithm. One of the matrices provided by NMF, called base matrix, is used as a filter bank for raw signal filtration. In opposition to classical methods of frequency or time-frequency analysis, presented algorithm was able to pinpoint the fault frequency connected to the bearing operation, which was difficult to recognize in the original signal. Further research will be focused on enhancing the performance of NMF algorithm by algebraic preprocessing of the CSC map, that is expected to improve the conditioning properties of spectral signatures distinction.
References
-
Randall R. B., Antoni J. Rolling element bearing diagnostics – a tutorial. Mechanical Systems and Signal Processing, Vol. 25, 2011, p. 485-520.
-
Lin J., Zuo M. Gearbox fault diagnosis using adaptive wavelet filter. Mechanical Systems and Signal Processing, Vol. 17, 2003, p. 1259-1269.
-
Makowski R., Zimroz R. New techniques of local damage detection in machinery based on stochastic modelling using adaptive Schur filter. Applied Acoustics, Vol. 77, 2014, p. 130-137.
-
Zak G., Obuchowski J., Wylomanska A., Zimroz R. Application of arma modelling and alpha-stable distribution for local damage detection in bearings. Diagnostyka, Vol. 15, 2014, p. 3-10.
-
Nowicka Zagrajek J., Wylomanska A. The dependence structure for parma models with alpha-stable innovations. Acta Physica Polonica B, Vol. 37, 2006, p. 3071-3081.
-
Wodecki J., Stefaniak P., Obuchowski J., Wylomanska A., Zimroz R. Combination of principal component analysis and time-frequency representations of multichannel vibration data for gearbox fault detection. Journal of Vibroengineering, Vol. 18, 2016, p. 2167-2175.
-
Boustany R., Antoni J. A subspace method for the blind extraction of a cyclostationary source: Application to rolling element bearing diagnostics. Mechanical Systems and Signal Processing, Vol. 19, 2005, p. 1245-1259.
-
Kruczek P., Obuchowski J., Wylomanska A., Zimroz R. Cyclic sources extraction from complex multiple-component vibration signal via periodically time varying filter. Applied Acoustics, Vol. 126, 2017, p. 170-181.
-
Wang Y.-X., Zhang Y.-J. Nonnegative matrix factorization: A comprehensive review. IEEE Transactions on Knowledge and Data Engineering, Vol. 25, 2013, p. 1336-1353.
-
Lee D. D., Seung H. S. Learning the parts of objects by non-negative matrix factorization. Nature, Vol. 401, 1999, p. 788-791.
-
He Z., Xie S., Zdunek R., Zhou G., Cichocki A. Symmetric Nonnegative Matrix Factorization: Algorithms and applications to probabilistic clustering. IEEE Transactions on Neural Networks, Vol. 22, 2011, p. 2117-2131.
-
Barszcz T., Zimroz R., Urbanek J., Jablonski A., Bartelmus W. Bearings fault detection in gas compressor in presence of high level of non-gaussian impulsive noise. Key Engineering Materials, Vol. 569, 2013, p. 473-480.
-
Antoni J. Cyclic spectral analysis of rolling-element bearing signals: facts and fictions. Journal of Sound and Vibration, Vol. 304, 2007, p. 497-529.
-
Wodecki J., Zdunek R., Wylomanska A., Zimroz R. Local fault detection of rolling element bearing components by spectrogram clustering with semi-binary NMF. Diagnostyka, Vol. 18, 2017, p. 3-8.