What's new
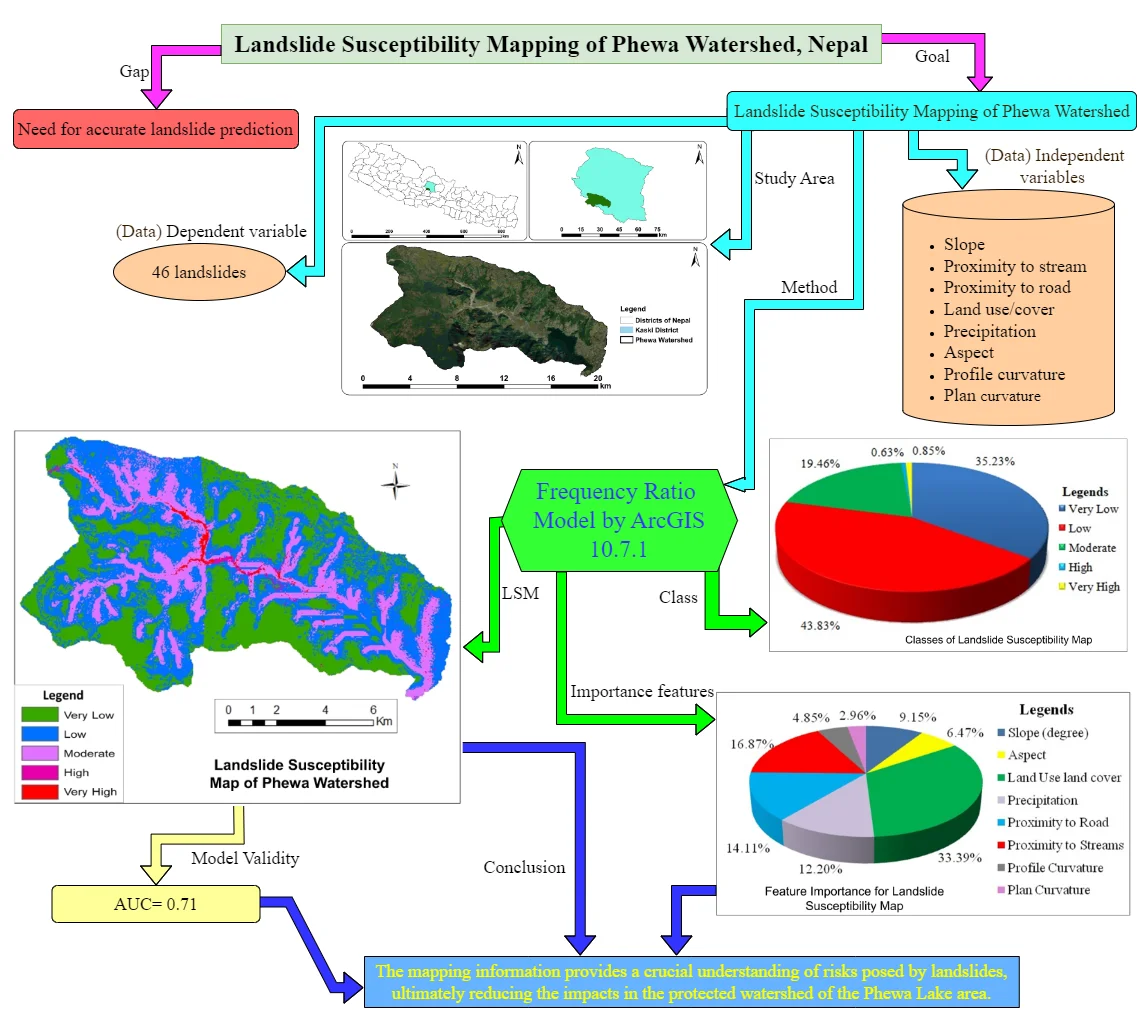
Editor's pick
Research Article
Landslide susceptibility mapping of Phewa Watershed, Kaski, Nepal
By Bimal Bahadur Kunwar, Nantakan Muensit, Kuaanan Techato, Saroj Gyawali
Heavy and incessant rainfall in Nepal, particularly during the monsoon season, leads to water-induced risks like landslides, necessitating the use of Landslide Susceptibility Mapping (LSM) for the prediction of landslide risks. We aim to determine the degrees of connection and connective factors among landslide incidents to generate an updated landslide susceptibility map of the Phewa watershed in Kaski District, Nepal. The most dependable and popular statistical approach for determining LSMs is the frequency ratio model, which was created in ArcGIS 10.7.1 by identifying 46 landslides in the area and analyzing eight causal factors. The LSM categorized the area into five classes, with the low class representing a large percentage (43.27 %) and the high class a small percentage (0.63 %). In FR techniques, slope, proximity to a stream or road, land use/cover, and precipitation were assigned greater weight than aspect, profile curvature, and plan curvature. Using the area under the curve approach, the applied model’s accuracy revealed a good performance value of 0.717. Taken together, the mapping information provides a crucial understanding of risks posed by landslides, ultimately reducing the impacts in the protected watershed of the Phewa Lake area.
August 22, 2024
Informatics
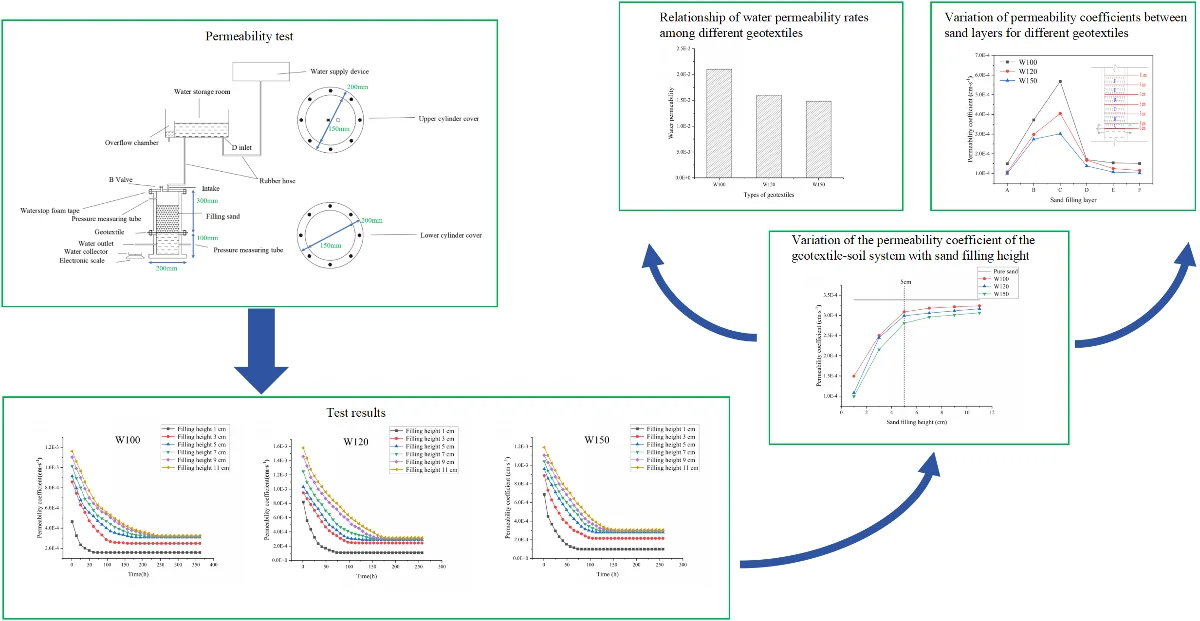
Research Article
Permeability test of geotextile-soil system under different sand filling heights
Geotube dams are constructed by stacking geotubes, which are non-homogeneous structures composed of geotextiles and filled sand. Therefore, studying the permeability characteristics of the geotextile-soil system is of great significance for seepage analysis in geotube dams. While the permeability characteristics of geotextiles and filled sand have been extensively studied individually, there has been relatively little research on the permeability characteristics of the geotextile-soil system formed by the combination of geotextiles and soil. In this study, a self-designed permeameter was used to investigate the permeability characteristics of the geotextile-soil system under different sand filling heights. The test results indicate that the permeability coefficient of the geotextile-soil system decreases continuously with the increase in permeation time and eventually stabilizes. The permeability coefficient of the geotextile-soil system increases with the sand-filling height and finally approaches but remains slightly smaller than that of pure sand with the same gradation. The influence of geotextiles on the permeability of the geotextile-soil system is significant within the range of 0 to 5 cm. Additionally, the water permeability of geotextiles affects the permeability performance of the geotextile-soil system. Specifically, a larger porosity corresponds to higher water permeability, and a greater permeability coefficient of the geotextile leads to a higher permeability coefficient of the geotextile-soil system.
March 9, 2025
Informatics
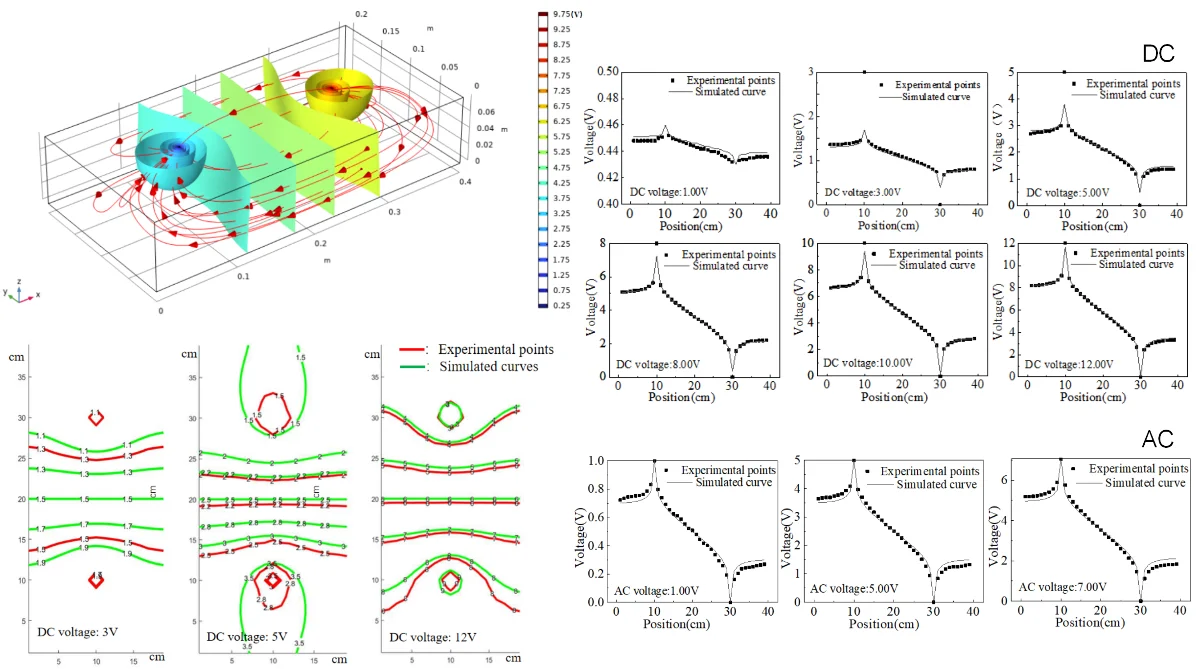
Research Article
Equipotential lines in liquids
Understanding the potential distribution in liquids is critical due to its significant differences from general media. The main problem addressed in this research is the lack of clarity on how electrode polarization affects potential distribution in liquid electrolytes. To investigate this, we experimentally measured the potential distribution characteristics in liquids under DC and AC voltages, explaining the variability through electrode polarization theory. Our action included introducing electrode polarization potential correction in COMSOL software simulations, which showed strong agreement with our experimental results. Further, we investigated the potential distribution characteristics in Na2SO4 solutions with varying concentrations, using ionic potential to explain voltage formation inside the liquids. The results highlight the improved accuracy in modeling potential distributions in liquid electrolytes, which is significant for advancing various electrochemical processes.
March 4, 2025
Applied Physics
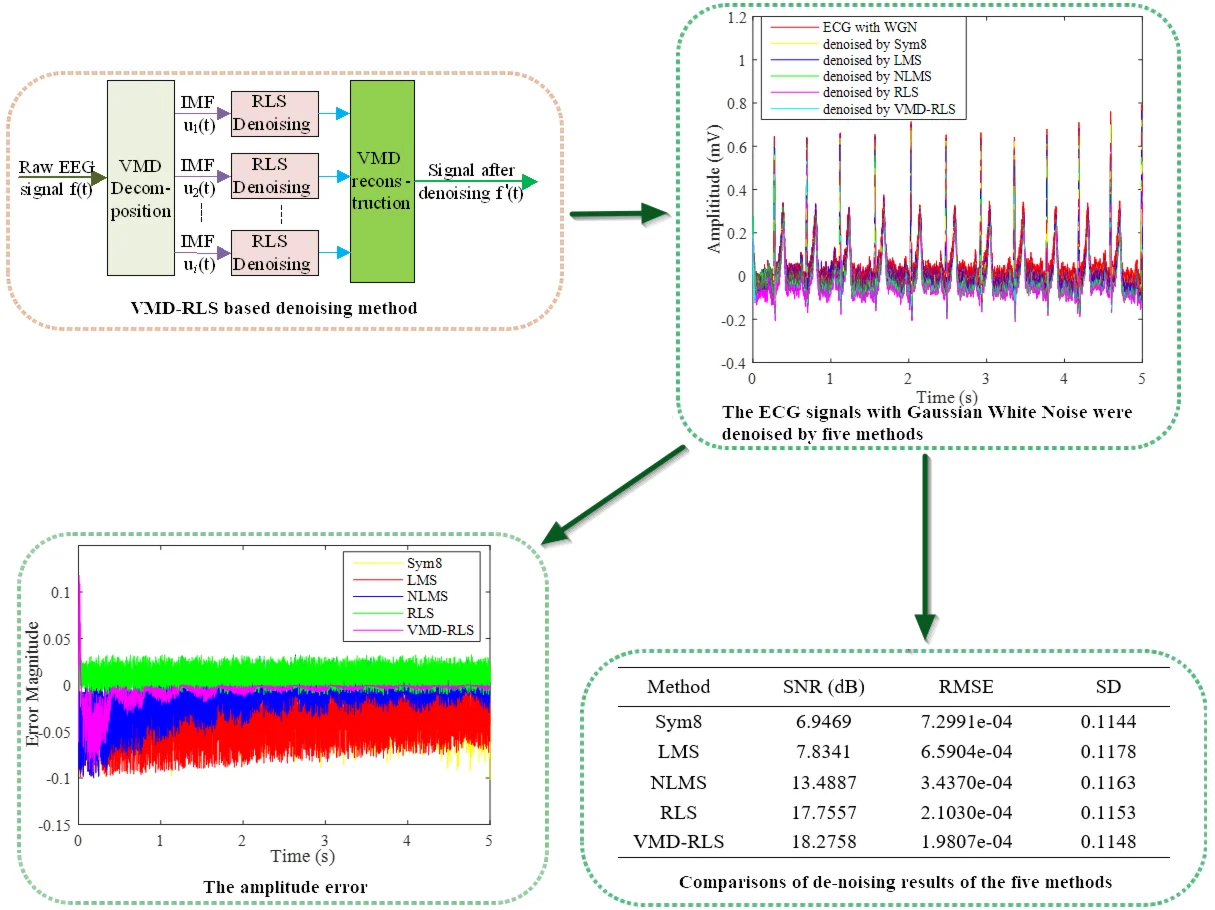
Research Article
Denoising for ECG signals based on VMD and RLS
Electrocardiogram (ECG) signals often encounter various types of noise interference, which annihilates their waveform characteristics and exhibits strong instability. To facilitate clinical diagnosis and analysis, it is necessary to perform denoising processing in advance. A denoising method for ECG signals based on variational mode decomposition (VMD) and recursive least square (RLS) has been proposed. VMD was used for the modal decomposition of noisy ECG signals, and the recursive least square (RLS) algorithm was used for adaptive filtering of various intrinsic mode functions (IMFs) components. The problem construction, solution, and decomposition characteristics of VMD were analyzed. The IMFs filtered by RLS were reconstructed. This achieved the elimination of interference noise in the ECG signal. The Sym8 wavelet basis, LMS, NLMS, RLS, and VMD-RLS denoising method were compared by using ECG signals including Gaussian white noise, baseband drift, electrode motion, electromyographic interference, and electrical interference noise. The experimental results showed that the VMD-RLS denoising method has significantly better denoising performance than the other four methods, achieving better values in the quantitative evaluation indicators. This algorithm improved convergence speed and signal estimation accuracy, and it has good effectiveness, superiority, and practicality. Therefore, the VMD-RLS denoising method can enable doctors and researchers to analyze and diagnose ECG signals of heart diseases more accurately.
March 1, 2025
Informatics
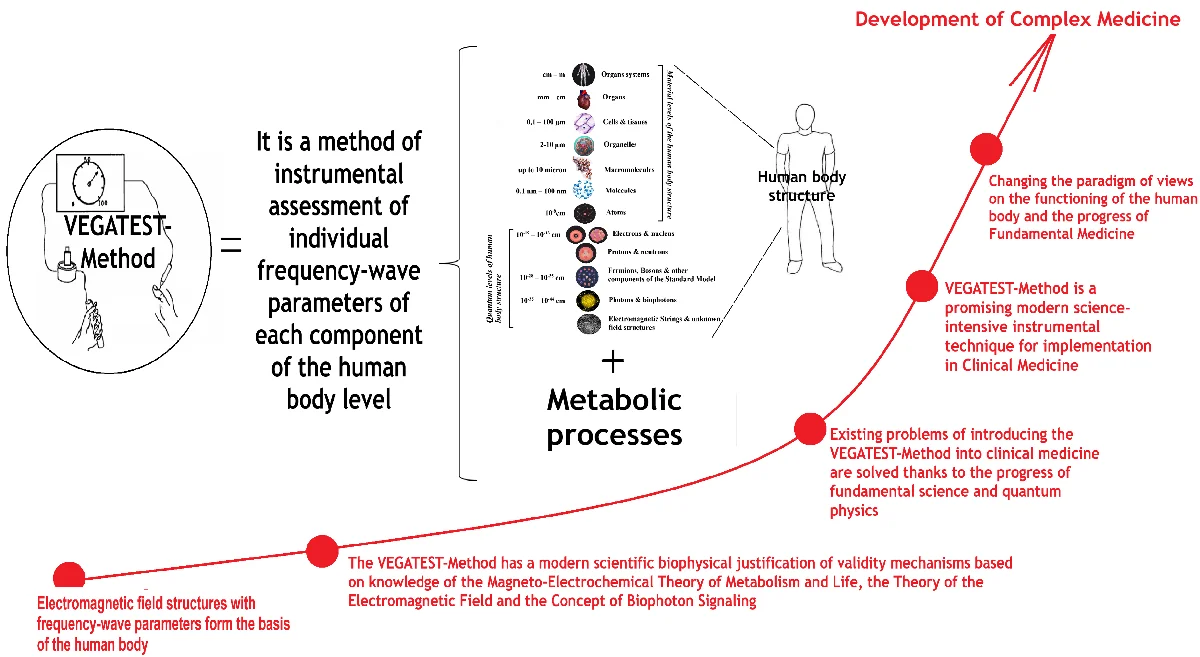
Research Article
Vega test method and diagnosis of non-communicable Diseases: problems, biophysical diagnostic mechanisms and prospects
This theoretical research is part of the educational and scientific project “Bioelectronic medicine or look at medicine differently” of research work of the Department of Internal Medicine and Emergency Medicine of Poltava State Medical University (23, Shevchenko St., 36011, Poltava, Ukraine) on “Development of algorithms and technologies for implementing a Healthy Lifestyle in patients with Non-Communicable Diseases (NCDs) based on the study of functional status” (state registration number 0121U108237: UDC 613 616-056-06: 616.1 / 9-03). The aim of this theoretical research was to create a systemic medical analysis of the nutrition of the scientific evidence of the Vega Test Method in the complex clinical treatment of patients with Non-Сommunicable Diseases, to determine the current state of health problems and prospects for using the method from the perspective of Complex Medicine. Conclusions: Vega Test Method is a promising modern science-intensive computerized instrumental technique that should be introduced into Clinical Medicine for the examination of patients with NCDs. Existing problems of introducing the Vega Test Method into Clinical Medicine are solved thanks to the progress of fundamental science and Quantum Physics, which leads to a paradigm shift in views on the functioning of the human body. The Vega Test Method has a modern scientific biophysical justification of validity mechanisms based on knowledge of the Magneto-Electrochemical Theory of Metabolism and Life, the Theory of the Electromagnetic Field, and the Concept of Biophoton Signaling. The use of the Vega Test Method in Clinical Medicine for the examination of patients with NCDs is important for the development of Complex Medicine.
March 1, 2025
Public Health
Latest from engineering
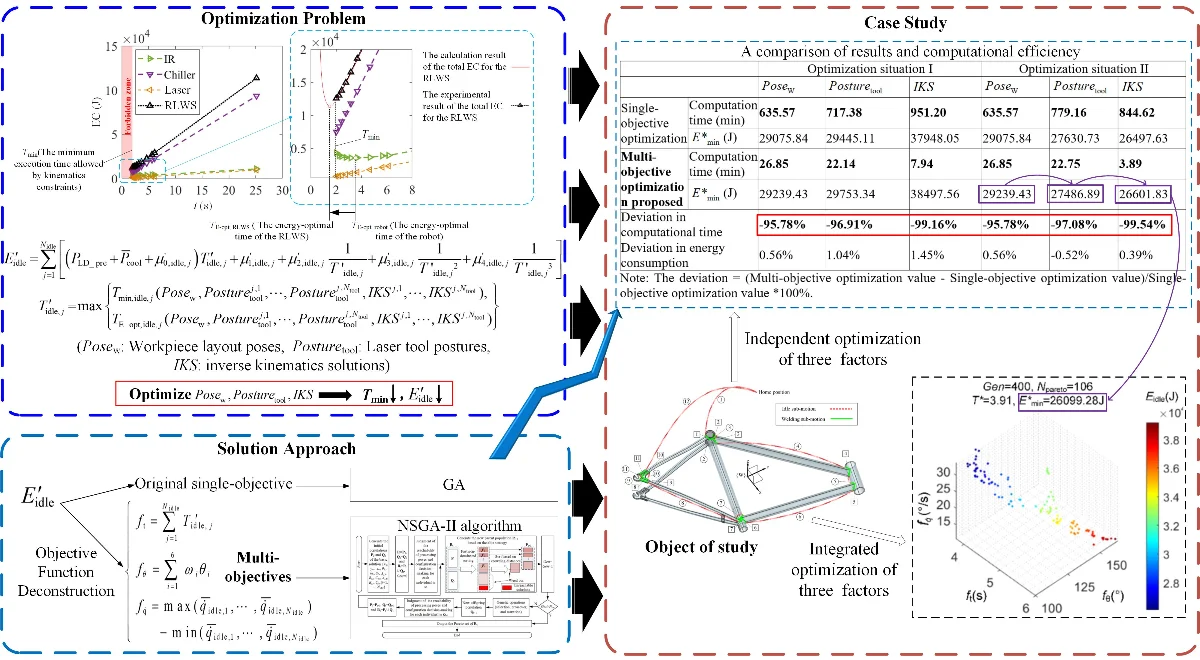
Research Article
An energy-saving optimization method for robot laser welding systems based on multi-objective metaheuristic algorithms
Reducing the energy consumption of robot manufacturing systems has become one of the increasingly important issues in industry. However, for robot manufacturing systems, the traditional optimization method with energy consumption as the objective function always suffers from low efficiency. In view of this, a novel energy-saving optimization method is proposed for robot laser welding systems based on the multi-objective optimization in this paper. This method deconstructs the energy consumption objective into three computationally inexpensive feature objectives and uses these three feature objectives as the objective functions of optimization, thus significantly improving the optimization efficiency. And a comprehensive optimization model of robot laser welding systems, which simultaneously considers three factors: the layout pose of workpieces, the posture of laser tools, and the inverse kinematics solution of robots, is established by utilizing a task energy characteristic model based on the time-scaling method. Furthermore, an integrated optimization process based on the NSGA-II algorithm is presented. A case study is described in detail. The results of the case study demonstrate that the proposed optimization method leads to a remarkable increase of over 95 % in optimization efficiency, that three factors exhibit interdependence, and that the integrated optimization of these factors yields superior results compared to optimizing them individually. In the case study, at a 95 % confidence level, the optimization scheme reduces the energy consumption of idle motion by 34.91 % and the total energy consumption by 7.29 %, compared to the original scheme.
February 27, 2025
Informatics
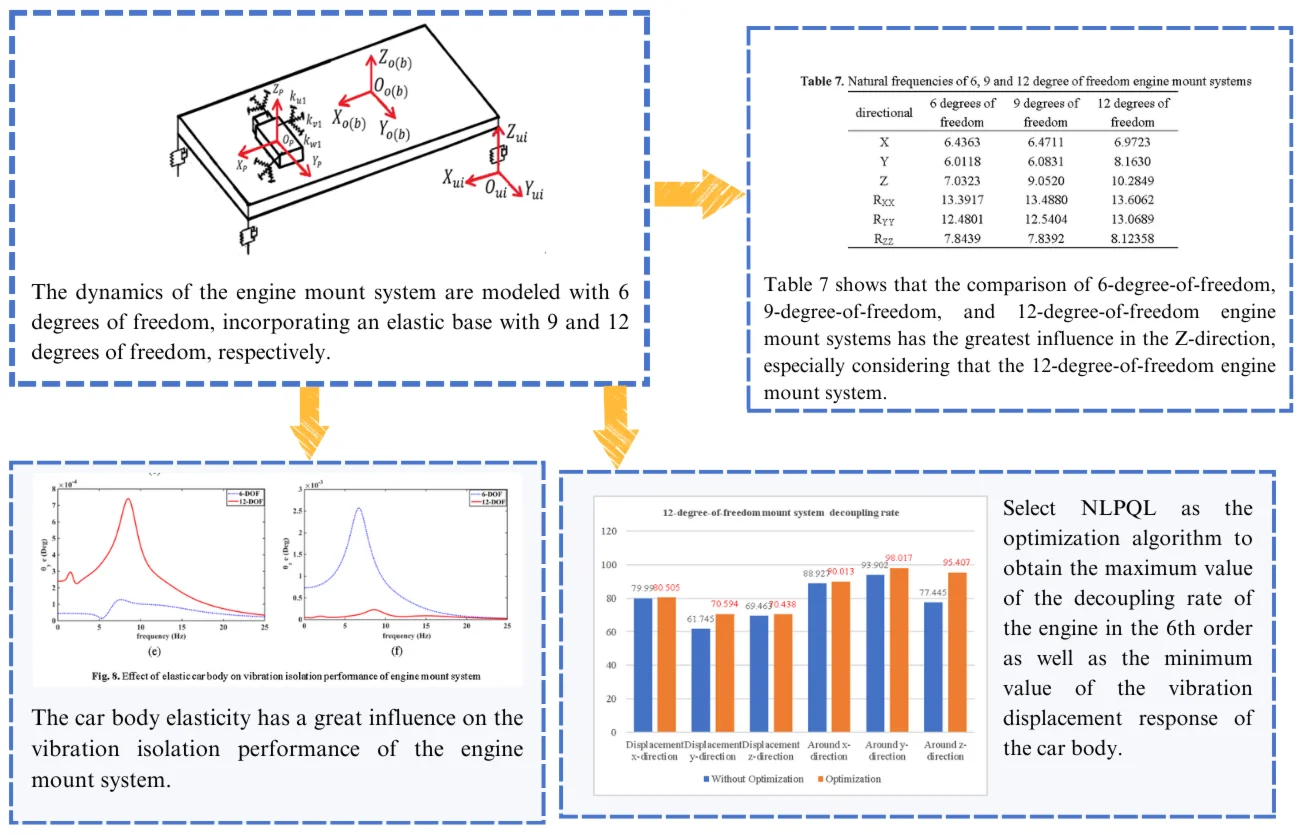
Research Article
Modal and optimization analysis of a 12-degree-of-freedom engine mount system considering engine elasticity
The multi-degree-of-freedom engine mount system presents a coupling issue that significantly impacting its vibration isolation performance. Although the optimization theories for decoupling 6-degree-of-freedom (6-DOF) and 12-degree-of-freedom (12-DOF) engine mount systems are relatively well-developed, previous studies have predominantly focused on engine response and often overlook the impact of car body vibrations. To address this gap, this article conducts an in-depth investigation into how the elasticity of the car body affects the vibration isolation performance of the engine mount system. Initially, the dynamics of the engine mount system are modeled with 6 degrees of freedom, incorporating an elastic base with 9 and 12 degrees of freedom, respectively. The study then analyzes how body elasticity influences the natural frequencies and modal shapes of the engine mount system. Subsequently, the sensitivity of the engine mount system is assessed using Isight analysis to evaluate the three directional stiffnesses of the mount. Finally, the decoupling optimization of the 12-degree-of-freedom engine mount system is performed using the NLPQL (Sequential Quadratic Programming) method. The findings indicate that: (1) considering the car body’s influence directly affects the natural characteristics and decoupling efficiency of the engine mount system; (2) body elasticity in the Z-direction has the greatest impact on the system’s vertical natural frequency; and (3) the NLPQL method effectively enhances the decoupling rate of the engine mount system.
February 19, 2025
Vibration Engineering
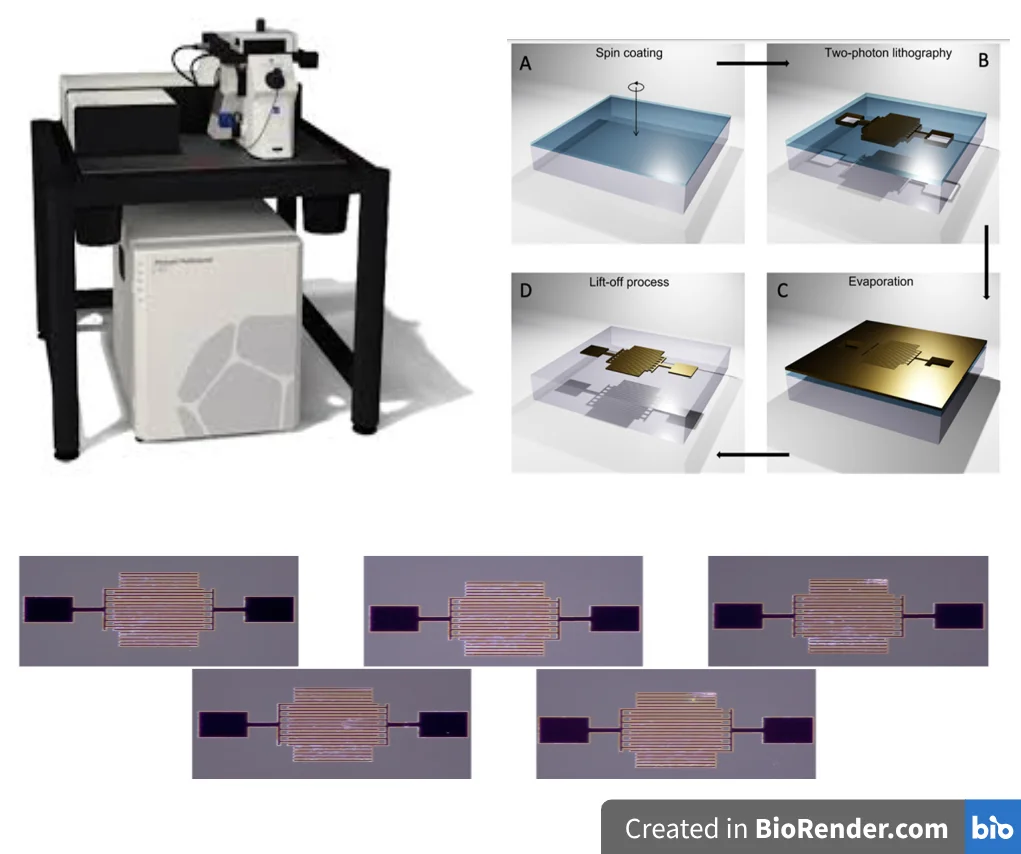
Research Article
Fabrication and characterization of interdigital transducer structures as temperature sensors by two-photon lithography
Continuous developments in the field of 3D printing techniques and equipment have enabled their usage in the field of electronics structures, circuits, and device fabrication in addition to many other fields. This advancement has enabled the potential fabrication of sensors using silicon-based micro or even Nanoelectronics. Currently, the manufacturing and packaging of such devices and structures are heavily reliant on lithography, which can be slow and can involve substantial processing requirements. In this paper, a temperature-sensing Interdigital Transducer (IDT) structure was designed and fabricated using Direct Laser Writing (DLW) based on Two-Photon Lithography (TPL), which is a high-resolution 3D printing technology. The TPL in a positive photoresist was combined with the physical vapor deposition method and the lift-off process to create gold IDT microstructures. The developed sensing structures were characterized using a network analyzer to determine the resonance frequency and its dependence on the temperature changes. The results showed that the IDT structures exhibit a linear response toward the changes in temperature with an average sensitivity of 0.123 MHz/°C. The most important advantage in producing the IDT structure with the additive manufacturing technique is that a very small-sized structure is produced error-free and efficiently.
February 18, 2025
Applied Physics
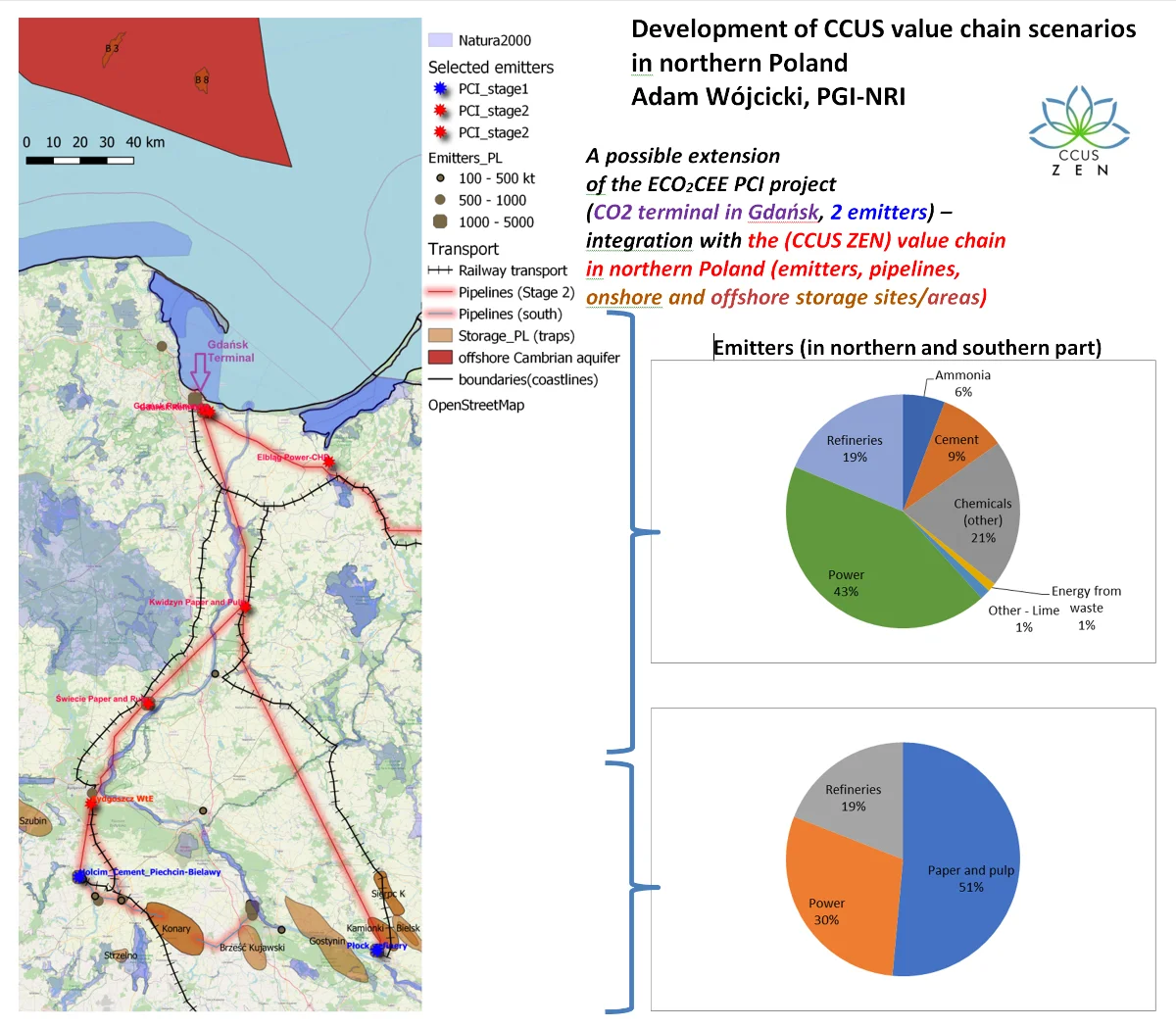
Research Article
Development of CCUS value chain scenarios in northern Poland
In CCUS ZEN project one of value chains considered includes emission sources located in the region of northern Poland. The value chain is intertwined with the scope of ECO2CEE Project of Common Interest on CO2 terminal in Port of Gdańsk. The ECO2CEE project in its first stage is to include railway transport of CO2 captured in two of the installations of the studied value chain. Carbon dioxide delivered to the terminal is to be transported by ship and stored under North Sea. However, within the region and its immediate vicinity there is notable storage potential. About 120 km north of Gdańsk, offshore, there is saline aquifer in Cambrian sandstones of storage capacity likely sufficient to store emissions of all selected 16 emitters of the region. The main barrier to such approach is the interpretation of Article 11 of Helsinki Convention suggesting ban of CO2 storage under the Baltic Sea. In southern part of the region where also ECO2CEE emitters are located there are several saline aquifer structures in Lower Jurassic and Lower Cretaceous of estimated storage capacity significantly exceeding the possible demand of emitters of the local cluster. Hence, the work is to propose the further development of the PCI value chain in northern Poland, beyond the original concept.
February 18, 2025
Industrial Engineering
Recently published
Research article
January 19, 2025
Anomaly detection method of traction motor bearing based on multi-scale sub-band fuzzy entropy manifold fusion index
By Guangbin Wang, Shubiao Zhao, Zhixian Zhong, Ying Lv, Changsheng Shao, Hui Zhang
Recently published
Research article
December 31, 2024
Object localization of channel robot using laser triangulation
By Muhammad Zulkifal, Vytautas Bučinskas, Andrius Dzedzickis, Vygantas Ušinskis
73rd International Conference on VIBROENGINEERING
Vibration Processes and Systems in Engineering and Industry
Date
September 25-28, 2025
Submission deadline
August 31, 2025
Conference format
Hybrid
Best of engineering
Editor's pick
Research article
January 19, 2025
Study on vortex-induced vibration response of large-scale two-lay steel trusses bridge under large wind angle of attack
By Jialin Yao, Huanhuan Li, Yang Yang, Dawu Wang, Hui Yu
Editor's pick
Research article
December 30, 2024
Enhancing technical proposal evaluation in consultant selection in Department of Water Resources and Irrigation, Nepal: a fuzzy analytic hierarchy process and fuzzy TOPSIS
By Nischal Silwal, Subash Kumar Bhattarai, Dinesh Sukamani
Editor's pick
Research article
October 10, 2024
Optimal trajectory control for the yaw system vibration and crawling jitter of a wind turbine
By Tingrui Liu, Qinghu Cui, Dan Xu
Editor's pick
Research article
September 8, 2024
Study on dynamic characteristics and wind-vibration control of transmission tower considering local damage and destruction
By Chen Chen, Liang Zhang, Kai Niu, Mengqi Zhai, Fengkai Han, Kunjie Rong, Li Tian
You might also like
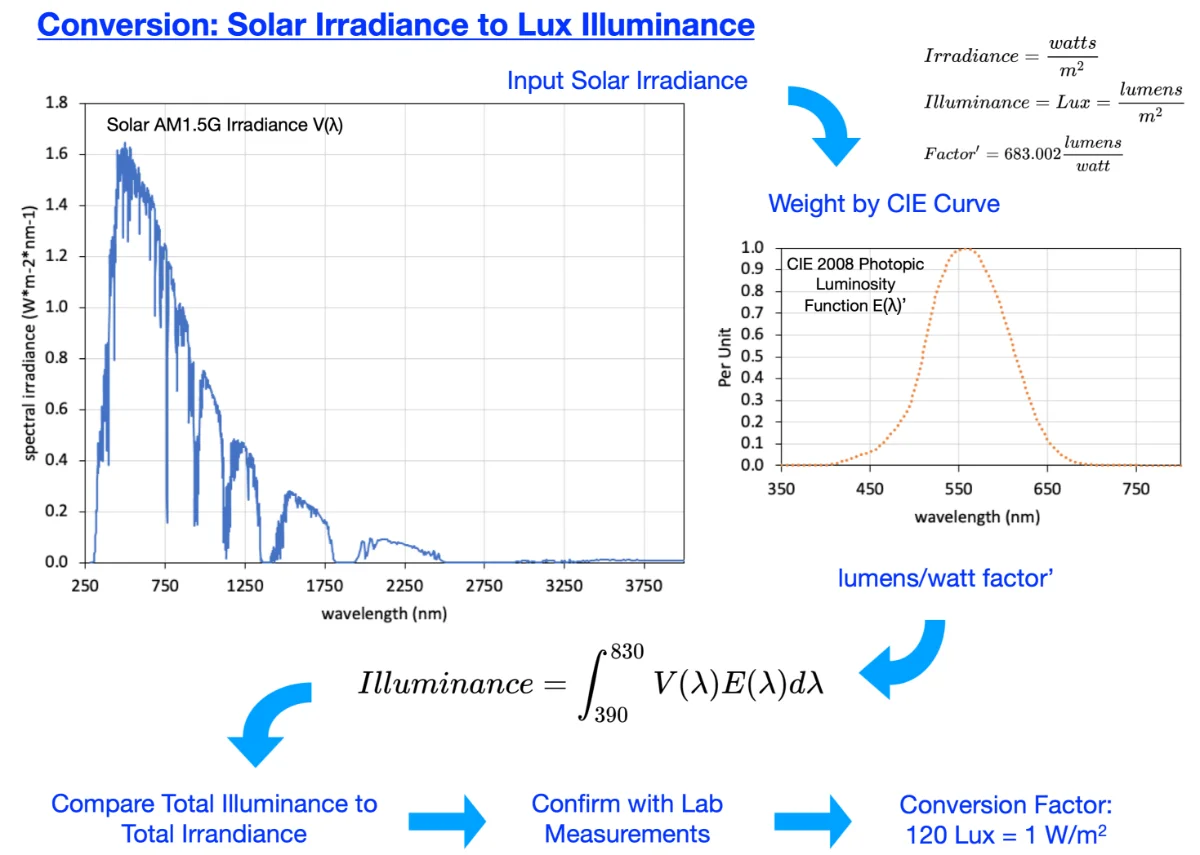
Most downloaded
Research Article
A conversion guide: solar irradiance and lux illuminance
By Peter R. Michael, Danvers E. Johnston, Wilfrido Moreno
The standard for measuring solar irradiance utilizes the units of watts per meter squared (W/m2). Irradiance meters are both costly and limited in the ability to measure low irradiance values. With a lower cost and higher sensitivity in low light conditions, light meters measure luminous flux per unit area (illuminance) utilizing the units of lumens per meter squared or lux (lx). An effective conversion factor between W/m2 and lx would enable the use of light meters to evaluate photovoltaic performance under low solar irradiance conditions. A survey of the literature found no definitive and readily available “rule of thumb” conversion standard between solar irradiance and illuminance. Easy-to-find Internet sources contain conflicting and widely varying values ranging from 688449 to 21000 lx for 1000 W/m2 (1 Sun) of solar irradiance. Peer-reviewed literature contains Luminous Efficacy equivalent values ranging from 21 to 131 lx per W/m2. This manuscript explores the relationship and establishes a theoretical and laboratory measurement guide for the conversion between solar irradiance and illuminance. The conversion factor includes standards data, equipment calibration accuracy, and uncertainty estimates. Solar Irradiance of 1 Sun (1000 W/m2) for an LED-based solar simulator is (116 ± 3) klx and (122 ± 1) klx for outdoor sunlight.
December 4, 2020
Applied Physics
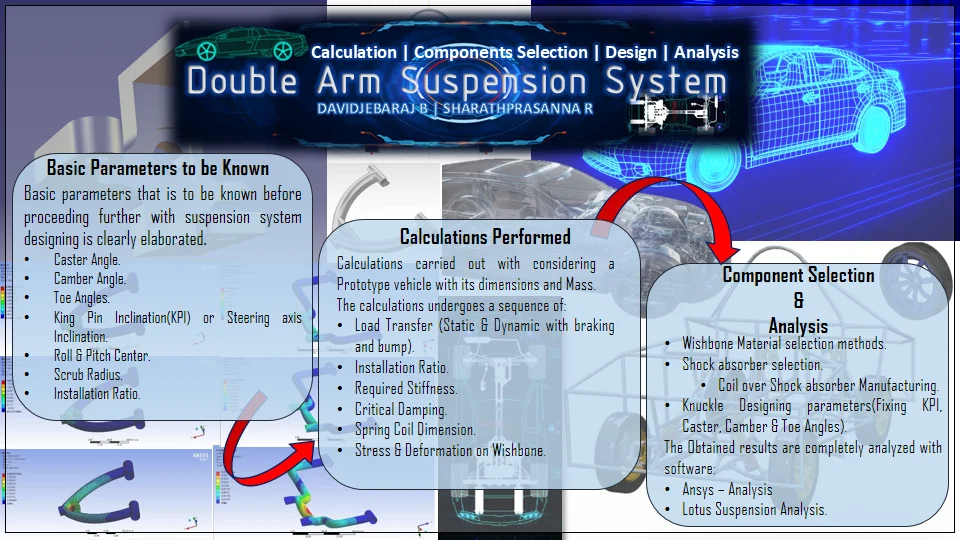
Most downloaded
Research Article
Design and calculation of double arm suspension of a car
By David Jebaraj B, Sharath Prasanna R
Suspension system is one of the challenging portions in designing a vehicle. The complete stability of the vehicle under dynamic conditions depends on the suspension system of the vehicle. Suspension system of a vehicle is interlinked with other systems such as steering, Wheels and Brakes. The main objective of this document is to provide complete guidance in designing and calculation of an independent suspension system with double control arms. The required parameters are calculated on considering a prototype vehicle with gross weight of 350 kg such as required stiffness of shock absorbers, Ride frequency, Motion ratio, Coefficient of damping etc. A CADD model was made with CATIA v5 r20 and SOLIDWORKS on the basis of calculations obtained and stress analysis was carried out for this model in various software such as Ansys. The complete assembled model was tested in LOTUS Shark and the result was obtained.
June 30, 2020
Industrial Engineering
Modal finite element analysis of PCBs and the role of material anisotropy
Printed Circuit Boards (PCBs) are epoxy resin-impregnated and cured sheets of counter woven glass fabric (e.g. FR4) laminated between thin sheets of Copper. The nature of the PCB is inherently anisotropic and inhomogeneous but previous modal FEMs of PCBs have assumed isotropic, anisotropic (transversely isotropic and orthotropic) material properties and shown good correlation with test data for specific scenarios [1-3]. This paper details part of a research program aimed at gaining a better understanding of accurately modeling PCB’s dynamic behavior. New investigations into the impact of material anisotropy and, in particular, the effect of material orthogonal plane definition (Ex and Ey) on eigenfrequencies is analysed. A modal FEM of a JEDEC PCB is created, verified, and validated using well established theories by Steinberg and empirical data by others [4, 5]. The relative contributions of Ex, Ey and Ez on PCB eigenfrequencies is examined using a parametric modal FEM, analysing the role of material isotropy verses anisotropy. The impact of transversely isotropic material properties is also analysed for a typical JEDEC PCB. This analysis details the mesh density required for accurately modeling the PCB eigenfrequencies. The results show that a 100 % increase in Ez has only a 0.2 % difference in the eigenfrequency where as a 100 % increase in Ey has a 1.2 % difference in the eigenfrequency. The effect of orthotropic plane definition (alternating Ex with Ey) on the JEDEC PCB amount to a 7.95 % delta in eigenfrequency.
Coilgun design and evaluation without capacitor
Capacitors with high voltage and capacity values are used in most induction coilguns that are designed and constructed. The fact that capacitors are quite bulky and slow in energy transfer and how a coilgun can be made without using capacitors is the study subject of this article. Two and four coil gun samples were made to find the essential components of an electric gun, and the results are reported in this article. The accuracy of the results is also confirmed by FEMM analysis for these models. The harmony of experimental and theoretical results shows that smaller and low cost portable electrical weapons can be a powerful alternative to firearms in the future.