Abstract
This paper provides an analysis of a solution proposed for the design of the chassis of a special-purpose vehicle’s mobile platform using an example of the high mobility wheel platform (KPWM) manufactured by the company Szczęśniak Pojazdy Specjalne. The basic requirements pertaining to vehicle chassis are related to requirements concerning mechanical strength and lightness of structures, being difficult to satisfy at the same time. The suspension system used in the high mobility wheel platform in question represents a typical design, comprising a frame made of high-strength steel and based on stringers. The high mobility wheel platform’s suspension system uses reinforced parabolic leaf springs and half-elliptic springs as the elastic elements, whereas shock absorbers and stabilisers as the damping and propelling elements, aimed to reduce tilts of the vehicle body while driving in a curvilinear track. By shifting the front driving axle towards the front vehicle section, a higher approach angle could be obtained. On account of difficult operating conditions and for off-road driving purposes, specific solutions have been applied to protect the vehicle chassis against damage when moving in difficult terrain. Moreover, bearing in mind the vehicle’s intended use in military operations, where unplanned repairs of chassis components must often be conducted in the field, the designers have taken the necessity of using a very limited set of tools into account.
1. Introduction
The suspension system is generally used to connect wheels with the vehicle frame. Its main task is isolation of vibrations from the vehicle body, i.e. damping vibrations generated at the wheels by moving over uneven surfaces, the wheel adhesion to the road surface as well as enabling the wheels to ensure maximum transfer of the driving forces and braking. The technical elements of the suspension system are divided into:
- steering – defining the geometry of movement of wheels relative to the vehicle (e.g. A-arms);
- springs – storing vibration energy, oscillating motion (e.g. leaf spring, coil spring);
- damping – vibration energy dissipation (e.g. shock-absorbers).
These suspension elements transfer the forces generated at the space between the wheels and the surface to the rest of the vehicle. On account of the passenger comfort and minimisation of forces acting on the vehicle load, the suspension system should be characterised by large vertical travel, since it is responsible for good off-road driving properties. Suspension systems should also be characterised to some degree by longitudinal flexibility and some transverse flexibility as well. Strong transverse rigidity allows for precise guidance of the vehicle (stabiliserroll). Consequently, one can be defined that a vehicle suspension system, which consists of damping, springing and steering elements, are responsible to a considerable extent for damping of vibrations generated by road roughness. Parameters of those elements have nonlinear characteristics which determine the system’s response to vehicle vibrations from road roughness [1-3].
Typical spring elements (coil spring, torsion bar, leaf spring and air spring) used in vehicle suspension systems are presented in Fig. 1.
The suspension system with a coil spring, a torsion bar or a leaf spring absorbs additional load through compression. The ride height depends on the loading condition. The air spring is a rubber cylinder filled with compressed air and the vehicle ride height can be corrected by adjusting the air pressure [4-6].
Fig. 1Vehicle spring elements [7]
![Vehicle spring elements [7]](https://static-01.extrica.com/articles/17295/17295-img1.jpg)
Because of numerous advantages, special-purpose vehicles often use suspension systems based on leaf springs. The evolution of a conventional laminated leaf spring into a parabolic spring is illustrated in Fig. 2. Application of a small number of leaves in the spring particularly contributes to the reduction of frictional forces in a positive manner. This is possible not by the use of additional spring leaves but by the use of stronger leaves capable of withstanding higher bending forces at the spring centre. This leads to a higher degree of material utilisation. The bending stress along the leaf is constant if the spring halves display a parabolic profile in the longitudinal section. Leaf springs with such leaves are called parabolic springs [7-11].
Fig. 2Comparison of leaf spring elements: a) conventional trapezoidal b) improved trapezoidal parabolic [5] c) parabolic
![Comparison of leaf spring elements: a) conventional trapezoidal b) improved trapezoidal parabolic [5] c) parabolic](https://static-01.extrica.com/articles/17295/17295-img2.jpg)
a) Conventional trapezoidal spring, 128 kg
![Comparison of leaf spring elements: a) conventional trapezoidal b) improved trapezoidal parabolic [5] c) parabolic](https://static-01.extrica.com/articles/17295/17295-img3.jpg)
b) Improved trapezoidal spring, 94 kg
![Comparison of leaf spring elements: a) conventional trapezoidal b) improved trapezoidal parabolic [5] c) parabolic](https://static-01.extrica.com/articles/17295/17295-img4.jpg)
c) Parabolic spring, 61 kg
The three springs considered here are characterised by the same length, spring rate and nominal load. The advantage of the parabolic spring, apart from the decrease of friction, is the decrease of the spring weight by around 50 % (minimisation of unsprung masses). The main advantage of the leaf spring is the combination of suspension and axle location, which is partially lost with the transition to parabolic springs featuring fewer leaves. In the course of braking, the parabolic springs tend to be affected by the impact, which must be prevented using additional torque support. Otherwise, relative velocities between the road and tyres can result in brake-hopping [10].
2. Parameters of the high mobility wheel platform
The high mobility wheel platform (KPWM) is presented on Fig. 3. It is one of vehicles developed by the Szcześniak company for military applications.
The technical parameters of the high mobility wheel platform are presented in Table 1.
Fig. 3High mobility wheel platform [12]
![High mobility wheel platform [12]](https://static-01.extrica.com/articles/17295/17295-img5.jpg)
Table 1Technical parameters of the high mobility wheel platform [12]
Power transmission system | 6×6 |
Transfer case | Permanent all-wheel drive |
Tyres | 16 00 R20 |
Front suspension | Reinforced parabolic leaf spring, stabiliser, shock absorbers |
Rear suspension | Half-elliptic springs |
Wheel base | 3,780 mm |
Maximum actual weight | 10,600 kg |
Permissible total weight | 34,000 kg (8,000 + 13,000 + 13,000) |
Permissible total weight of wheel set | 40,000 kg |
Motor | IVECO Cursor 13 |
Engine | 420 KM /309 kW |
Engine cubic capacity | 12,880 ccm |
Emission | EURO 3 |
Transmission | Automatic |
Clutch | Single-plate type |
Fuel tank | 300 litres |
Batteries | 2×175 Ah |
Maximum speed | 120 km/h – limited by tyres |
Vehicle main frame | Steel stringers |
Front axle | Fixed, driving-type |
Rear axle | Fixed, driving type |
Parking brake | Mechanical, rear wheels locking, manually controlled |
Brakes | Drum type |
Clearance | 395 mm |
Approach/departure angle | 44°/38° |
Fording | 1,500 mm |
Height/width/length | 2,850 mm / 2,550 mm / 8,000 mm |
The 6×6 power transmission system enables driving in both paved roads and off-road routes. A block diagram of the 6×6 power transmission system has been provided in Fig. 4. Torque generated in the engine is transferred via the clutch and the transmission to the drive shaft, the drive shaft transfers the torque to the transfer case, and then, via drive shafts, 3 driving axles are propelled. All driving wheels are propelled, and such a solution has been applied in order to increase the driving force in wheels. This has made it possible to improve drive properties of the vehicle as well as its off-road mobility.
Fig. 4Block diagram of the 6x6 power transmission: 1 – engine, 2 – clutch, 3 – transmission, 4 – transfer case, 5 – driving axle, 6 – drive shaft
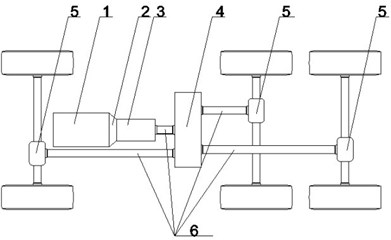
The high mobility wheel platform (KPWM) is, by definition, intended to be a lorry of superior drive properties compared to the heavy vehicles currently available in the market. Unlike in commercial vehicles, the design of the vehicle in question is intended for driving in difficult terrain, carrying heavy load and operating under adverse weather conditions. One of the characteristic features of the design is also that it enables finding an assembly line in the country of the party interested in the purchase and licenced assembly of the chassis. The design in question is not intended for a single customer only, but rather for a target group of parties sharing needs, best represented by armed forces [13-16].
The main frame (Fig. 5) of KPWM is a backbone of the entire vehicle, which supports all elements. It should meet the strength requirements set up to carry the burden of rough roads as well as the load from the body and its parts and the cargo being transported. The material used for making the frame is resistant to static and dynamic loads as well as resistant to the conditions during the vehicle’s operation. The frame is made of steel elements forming a flat grid: stringers and cross beams connecting them in accordance with the design.
Fig. 5Frame of the special-purpose vehicle (KPWM) [15]
![Frame of the special-purpose vehicle (KPWM) [15]](https://static-01.extrica.com/articles/17295/17295-img7.jpg)
The suspension system features build-in elastic elements, such as reinforced parabolic leaf springs in the front suspension (Fig. 6(a)) and semi-elliptic leaf springs in the rear suspension (Fig. 6(b)). Also shock absorbers and a stabilizer were used to reduce lateral body roll during cornering.
Fig. 6Front (a) and rear (b) suspension of the special vehicle (KPWM) [15]
![Front (a) and rear (b) suspension of the special vehicle (KPWM) [15]](https://static-01.extrica.com/articles/17295/17295-img8.jpg)
a)
![Front (a) and rear (b) suspension of the special vehicle (KPWM) [15]](https://static-01.extrica.com/articles/17295/17295-img9.jpg)
b)
3. Conclusions
The high mobility wheel platform (KPWM) is an example of a vehicle offering improved off-road mobility capabilities. The solutions assumed while designing the front axle suspension system as well as that of the twin rear axles ensure a reasonable compromise between mobility capabilities of a vehicle carrying load in difficult terrain and costs as well as possibilities to repair the suspension system in the field. Solutions based on elastic components, such as parabolic leaf springs, are not optimum solutions when considering the driving comfort criterion, but their legitimacy stems from the fact that it is the off-road mobility which constitutes the most significant criterion applicable to this platform.
References
-
Burdzik R., Konieczny Ł. Research on structure, propagation and exposure to general vibration in passenger car for different damping parameters. Journal of Vibroengineering, Vol. 15, Issue 4, 2013, p. 1680-1688.
-
Dąbrowski Z., Dziurdź J., Klekot G. Studies on propagation of vibroacoustic energy and its influence on structure vibration in a large-size object. Archives of Acoustics, Vol. 32, Issue 2, 2007, p. 231-240.
-
Konieczny Ł., Burdzik R., Figlus T. The possibility to control and adjust the suspensions of vehicles. Communications in Computer and Information Science, Vol. 395, 2013, p. 378-383.
-
Konieczny Ł., Burdzik R. Comparison of characteristics of the components used in mechanical and non-conventional automotive suspensions. Solid State Phenomena, Vol. 210, 2014, p. 26-31.
-
Konieczny Ł., Burdzik R., Węgrzyn T. Analysis of structural and material aspects of selected elements of a hydropneumatic suspension system in a passenger car. Archives of Metallurgy and Materials, Vol. 61, Issue 1, 2016, p. 79-84.
-
Prochowski L., Żuchowski A. Automotive Vehicles. Heavy Truck and Buses. WKŁ, Warsaw, 2004.
-
Rill G. Road Vehicle Dynamics: Fundamentals and Modeling. CRC Press, 2012.
-
Burdzik R., Konieczny Ł., Adamczyk B. Automatic control systems and control of vibrations in vehicles car. Communications in Computer and Information Science, Vol. 471, 2014, p. 1865-929.
-
Burdzik R., Konieczny Ł. Application of vibroacoustic methods for monitoring and control of comfort and safety of passenger cars. Solid State Phenomena, Vol. 210, 2014, p. 20-25.
-
Giliomee C. L. Analysis of a Four State Switchable Hydro-Pnumatic Spring and Damper System. University of Pretoria, 2005.
-
Szczęśniak G., Nogowczyk P., Burdzik R. Some basic tips in vehicle chassis and frame design. Journal of Measurements in Engineering, Vol. 2, Issue 4, 2014, p. 208-214.
-
Materials provided by Szczesniak Pojazdy Specjalne.
-
Ostrowski T., Nogowczyk P., Burdzik R. The constructional solutions for absorption of vibration in special vehicles operated in terrain. Vibroengineering Procedia, Vol. 3, 2014, p. 249-253.
-
Szczęśniak G., Nogowczyk P., Burdzik R., Konieczny Ł. Requirements for construction of the bodies of special vehicles. Scientific Journal of Silesian University of Technology, Series Transport, Vol. 87, 2015, p. 73-79.
-
Szczęśniak G., Nogowczyk P., Burdzik R., Konieczny Ł. Application of mounting frames in special vehicles. Scientific Journal of Silesian University of Technology, Series Transport, Vol. 87, p. 81-86.
-
http://dziennikzbrojny.pl/artykuly/art,5,20,8,wojska-ladowe,wozy-opancerzone,kolowy-transporter-opancerzony-rosomak
About this article
This article is the result of Research Programme DEMONSTRATOR + Supporting Scientific Research and Development Works in Demonstration Scale, the title of the Project is Develop High Mobility Wheeled Platform for Special Applications (No. WND-DEM-1-325/00 KoPlatWysMob).