Abstract
For companies to be able not only to survive, but also to differentiate themselves in the current global market scenario, all their functional areas must be in line with short, medium, and long-term management objectives and policies. The performance and competitiveness of companies depend on the behaviour of their production system, so an ambitious and adequate maintenance management is necessary. In this way, companies seek to adopt new methodologies and approaches to maintenance management that allow them to prepare maintenance for the challenges of Lean Philosophy and Industry 4.0. The Lean philosophy aims to do more and more with less and less, that is, using less equipment, less human effort, less space, and time, trying to offer customers exactly what they want, at the right time. On the other hand, Industry 4.0 is based on intelligent factories with production processes with a computer interface between people, machines, and resources, through extensive communication networks that combine the virtual and the real world, to obtain all integrated processes generating thus a real-time information system. Thus, an adequate maintenance management system contributes not only to improve maintenance performance as well as the production system. The maintenance management system, when combined with Lean Philosophy and Industry 4.0 concepts, makes it more efficient and effective. To improve maintenance performance, a system that combines these three concepts is proposed.
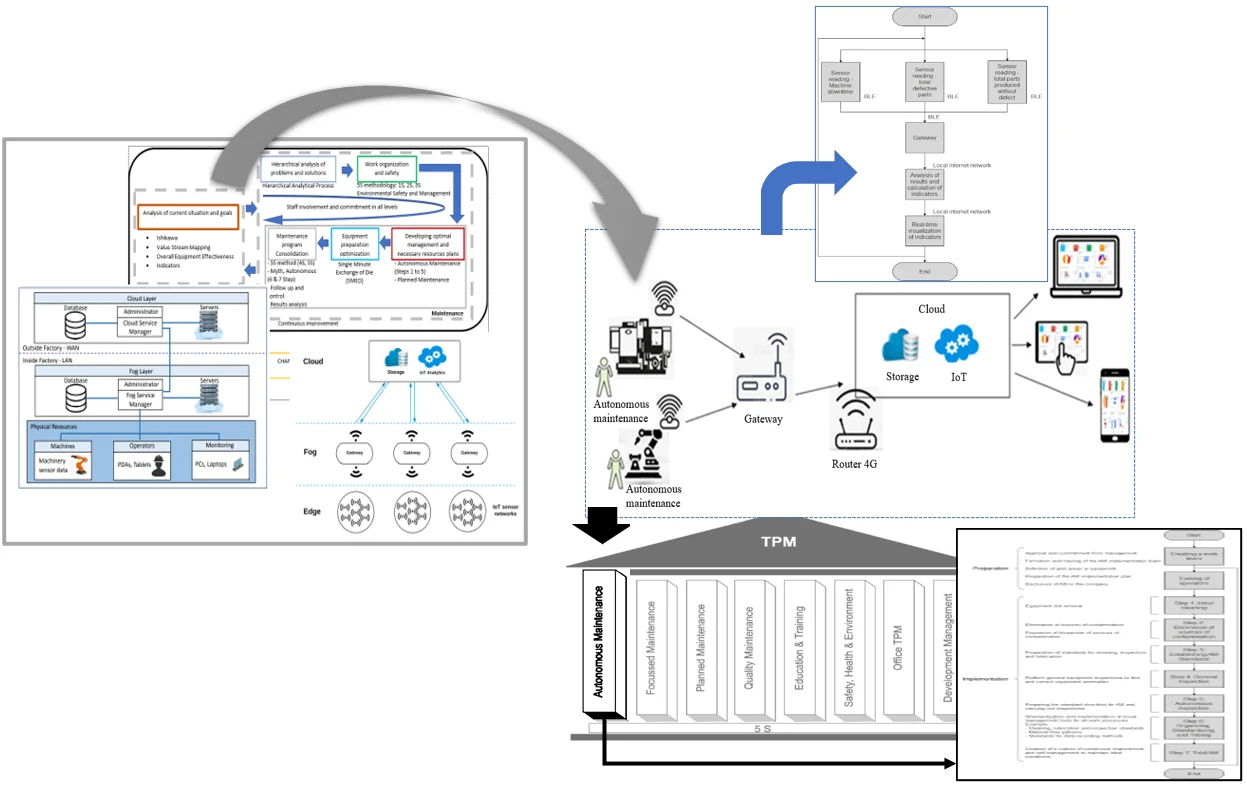
Highlights
- The classification and description of faults, as well as the monitoring of the various indicators contribute to a more accurate and economical maintenance.
- Real-time monitoring of machines and equipment allows maintenance managers to obtain more easily, quickly, and accurately important data that help improve decision-making and response time.
- The involvement of the maintenance and production area provides a better symbiosis and performance of the production system.
- Operators, motivated and with the proper education and training, contribute to an increase in the productivity of the machines and equipment where they operate.
1. Introduction
With globalization, the survival of companies depends on the speed of innovating and making continuous improvements. To remain competitive, companies must adopt new management and organization tools, focusing on issues that are within their control, starting with the factory floor. For these purposes, maintenance stands out due to the obvious cost reduction and increase in reliability it provides. To face the growing complexity of the market and competitiveness between companies, it is necessary that maintenance management is efficient and effective, as well as its processes and strategies [1-6].
In this way, those responsible for maintenance services are looking for new management and organization tools, which direct them to greater competitiveness through quality, reliability, and productivity. Thus, Lean Philosophy plays a crucial role in the pursuit of such goals. This philosophy has led to the improvement of processes to achieve greater productivity in industrial companies, which can represent a competitive advantage and contribute to improving the performance of companies [6-10].
On the other hand, the industry is in constant transformation, leading to a change in the production paradigm, giving rise to the concept of Industry 4.0, which is characterized by the incorporation of new resources, which combines technological transformations, enabling connectivity and interaction of equipment and people, thus allowing the industry to remain competitive in the market based on intelligent and high-tech production at lower costs and offering more innovative products and services [11-15].
As previously mentioned, one of the ways to get to know and explore opportunities to improve the shop floor is through a Gemba Walk, which is one of several tools associated with the Lean Philosophy. This methodology aims to identify existing safety hazards, observe the conditions of machines and equipment and extract as much information as possible, such as downtime, cycle time, among other indicators. However, this methodology has some limitations regarding the accuracy of the collected data [16-18].
As described, the collection of information through the Gemba Walk is not always accurate and does not reliably evidence what is happening on the shop floor. Based on this gap, it is intended to develop a system integrating the tools provided by Industry 4.0 and Lean Philosophy, due to the wide variety of technologies and methodologies they provide.
To show what is happening in real time on the shop floor, there are some important indicators that contribute to decision making, both in the maintenance and production departments, these being monitoring targets in the proposed model.
2. Existing architectures for the integration of continuous improvement and Industry 4.0 in maintenance management
For the construction of the system and after a bibliographic review [19] and a previous analysis of 86 articles, which combine the concepts Maintenance, Lean Philosophy and Industry 4.0, three were chosen, taking into account various criteria such as equipment monitoring , improvement of maintenance intervention, intelligent maintenance and flexibility in the applicability of models, maintenance management, quality of maintenance intervention, increased availability of machines and equipment, among others. The three chosen models are briefly described below: Magadán et al. [8] developed a framework to monitor electric motors in real time, using low-cost hardware components, open-source software, and a free version of an Internet of Things (IoT) analytics service. Fig. 1 shows the architecture of the system, which is composed of three layers. The first layer is composed of the sensors, the next layer by the Gateways, which make the bridge with the last layer, which allows the storage, treatment, and visualization of data through the cloud [20].
Fig. 1System architecture [20]
![System architecture [20]](https://static-01.extrica.com/articles/22472/22472-img1.jpg)
The operation of the system in general is done through sensors coupled to the motors to be monitored. The Gateway in turn sends the data collected by the sensors to the cloud. In the third layer, it will be possible to store, process and visualize data through ThingSpeak, an analysis platform service made available by the IoT for free that allows aggregation, visualization, and analysis of data streams in real time [20].
Ashjaei & Bengtsson [21], developed a platform to improve smart maintenance management. The structure presented is composed of two layers, the first being composed of physical resources: Sensors, machines and equipment, tablets, and operators (Fig. 2). The first layer is also constituted by data storage and processing devices, whose function is to make the connection and filter the data collected in the physical resources for the last layer. The second layer has a data storage and processing unit. After the data is collected and properly processed, it is sent to the monitoring room, among other mobile devices. If the system detects an anomaly, it issues a warning. The factory’s local network makes communication between the system and physical resources possible [21].
Fig. 2Proposed platform for smart maintenance management [21]
![Proposed platform for smart maintenance management [21]](https://static-01.extrica.com/articles/22472/22472-img2.jpg)
In 2020, Arrascue-Hernandez et al. developed a model applying Lean tools through change management to increase equipment availability and useful life (Fig. 3) [22].
For the implementation of the model, it is necessary to consider several points that make up the phases of implementation of the model [22]:
Analysis of the current situation and objectives: to analysed and outline the objectives one must use some tools such as the VSM, Ishikawa Diagram, Takt Time and OEE [22].
Hierarchical analysis of problems and solutions: This phase consists of identifying the root cause of problems and finding more effective solutions to problems associated with maintenance. To carry out this phase, six steps must be considered: decomposing the problem, weighting the criteria matrix, normalizing the criteria matrix, comparing alternatives, deciding on the best alternative, and performing the consistency assessment [22].
Work organization and safety: to achieve the objective of this phase, the implementation of the 5S methodology must be audited to see the current level of the company and the post implementation level. At this stage, the 5S must be implemented partially, that is, only Classification, Organization and Cleaning [22].
Safety pillar: phase related to the safe work of operators, following written work safety procedures through periodic training on hazard identification and risk assessment of the workplace and training in the use and management of personal protective equipment, collectives, among others [20].
Development of optimized management and necessary resource plans: the first five steps of autonomous maintenance should be implemented, starting with cleaning, removal of sources of pollution, inspection standards and general cleaning, autonomous inspection. Improve planned maintenance planning to maximize equipment life [22].
Optimization of equipment preparation through the Single Minute Exchange of Die (SMED) methodology. All activities inherent to the equipment must be analysed, that is, analysing internal and external activities and converting internal activities into external activities and internal activities must be reduced [22].
Maintenance program consolidation focuses on completing the implementation of the 5S methodology, i.e., implementing standardization and discipline along with the sixth and seventh step of autonomous maintenance of equipment in general [22].
Fig. 3Maintenance management model [22]
![Maintenance management model [22]](https://static-01.extrica.com/articles/22472/22472-img3.jpg)
The systems presented by Magadán et al. [20] and Ashjaei & Bengtsson [21] address two of the three concepts that are the subject of study: Maintenance and Industry 4.0 and present some similarities regarding their operation. Although the models contribute to improve maintenance management, they have some limitations, such as the maximum distance between the various devices that make up the system, because as the distance between the devices increases, the smaller the amount of data collected will be. It is also possible to observe that the greater the amount of data to be collected and analysed, the system has problems in its processing. Finally, another limitation has to do with security, privacy, and data preservation within the factory.
The model presented by Arrascue-Hernandez et al. [22] presents a structure that involves the concepts: Maintenance and Lean Philosophy. The authors focus on improving the production process by reducing the time needed to change tools, improving the organization, cleanliness and safety of the workplace and Autonomous Maintenance, these being important tools for a good improvement of the production process. In addition to improving the aforementioned areas, it should be implemented in the remaining areas of the factory. In the phase of identification and analysis of problems and objectives, in addition to the proposed methodologies, others associated with the identification and prioritization of problems could be used with the GUT matrix, Pareto diagram, brainstorming.
3. System proposal for maintenance performance improvement
The proposed system is an adaptation and improvement of the systems presented above, to better adapt to the objectives outlined. For the construction of the system, it was defined that the base of the same would be composed by Industry 4.0, for the capacity that it provides in the real-time monitoring of machines and equipment, thus enabling a collection of information in a precise way, which will contribute to better manage the activities. effectively and efficiently. The system presented was mainly based on the architecture proposed by Magadán et al. [20].
This system is designed so that its implementation takes place only in one part of the company, and in this case, it will be applied to the factory floor as well as in the maintenance department. It is also intended that the proposed model is easily adaptable to allow its use in any business context.
Fig. 4 shows the proposed system, which is composed of an architecture to be implemented to ensure continuous and accurate monitoring of the most relevant indicators of maintenance and production processes, such as intrinsic and operational availability, Average repair time, Mean Between Failures, Cycle Time, and Overall Equipment Efficiency. In addition to the architecture to be implemented, the system lacks the implementation of Autonomous Maintenance.
Fig. 4Proposal of the application model that combines the concepts of Maintenance, Lean Philosophy, and Industry 4.0
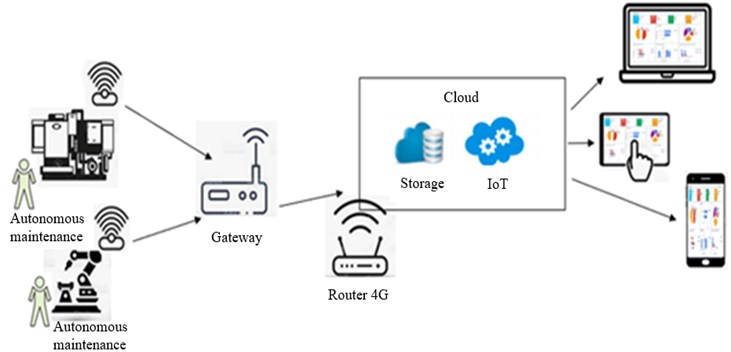
The monitoring system is supported by the local internet network (wireless) and the Bluetooth Low Energy (BLE) communication protocol and various devices that allow data collection, storage, and visualization through mobile or fixed devices. Monitoring is performed through a wireless sensor that collects and transmits data to a gateway, which aims to receive data from all sensors on the factory floor to monitor equipment. The gateway processes the data received and after processing it sends it to the server located in the cloud. This aims to store all the information and be the interface for viewing data in real time, through the various devices. Finally, the cloud layer is implemented using a free version of ThingSpeak, an internet of things platform service that allows aggregation, visualization, and analysis of real-time data streams in the cloud. Fig. 5 describes the operation described above in a schematic and summarized way.
The efficiency of the shop floor depends on several factors, one of the most important being to maintain the machines and equipment so that they work without any kind of problems, unexpected stops or being producing outside the parameters causing production losses compromising the entire production system. Thus, in addition to real-time monitoring that allows for the perception of what is happening at each moment and in each machine and equipment on the factory floor, the maintenance of physical resources becomes fundamental and vital so that they can operate in an uninterrupted and under the best conditions. Autonomous maintenance (AM) contributes to improving the production process, fostering continuous improvement, and directly facilitating the work of maintenance technicians, since daily the operators involved through correct cleaning, inspections can detect small defects, correct them or early warning those responsible for maintenance so that they can have a quick and assertive intervention, avoiding a problem of greater size and complexity.
Fig. 5System operation description flowchart
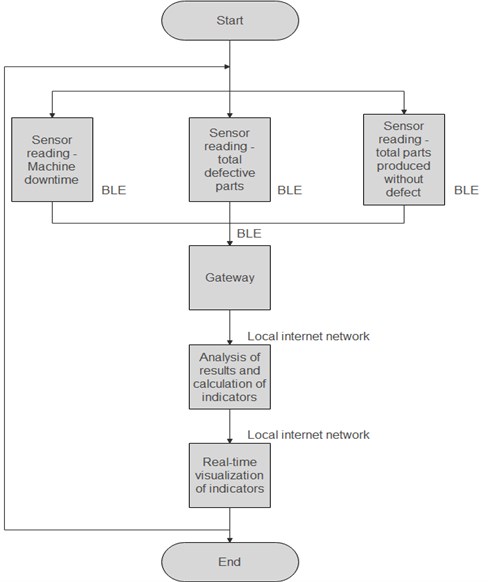
AM is one of the eight pillars of TPM (Fig. 6), being the highest level of this methodology in terms of maintenance [23].
Fig. 6Eight pillars approach for TPM implementation [23]
![Eight pillars approach for TPM implementation [23]](https://static-01.extrica.com/articles/22472/22472-img6.jpg)
Although AM is one of the pillars of TPM, it can be implemented without the need to implement the other pillars that make up the TPM, as it shares some identical points, and the TPM is a more complete methodology. The use of the TPM methodology completely or exclusively of the AM pillar depends on several factors, whether human, financial or temporal [23-24].
Through AM, operators learn to perform important daily tasks that maintenance technicians rarely have time to perform. These tasks include keeping the equipment clean, lubricated and with all components properly secured to reduce deterioration and prevent equipment failures. To achieve the goals of autonomous maintenance, it is necessary to involve production and maintenance personnel in daily activities to maintain the state of equipment, training to improve operator skills, and participation of production personnel in the maintenance process [24-26].
Thus, the fundamental objective of AM is to avoid, in the day-to-day production, the deterioration of equipment by detecting and treating its anomalies at an early stage before they develop and result in more serious failures [24-26].
The machine operator becomes the key element, as he will be responsible for carrying out small maintenance activities (cleaning, tightening screws and lubricating). The operator having this attitude will feel like another important element, which will help in his development and taste for the job, as well as helping to create more time for the maintenance team, leaving more time for more time-consuming and complex tasks, make improvements to the machines contributing to increased productivity [24-26].
This process is intended to reduce the frequency of breakdowns due to small causes that can be identified and resolved by the equipment operators, who are autonomous for the preparation of maintenance on the equipment itself [26-29].
Thus, AM consists of training and qualifying operators to develop a feeling of ownership over the equipment and thus take care of them, carrying out inspections and detecting problems at an early stage, and even making small adjustments and tightening’s to maintain the equipment. in perfect condition for as long as possible [26-29].
A well-maintained equipment, in good cleaning conditions, with repairs with determined frequencies, with trained and qualified operators, will have greater productivity [26-29].
For the implementation of AM, seven steps must be followed: initial cleaning, eliminate sources of problems, establish cleaning and lubrication standards, general inspection, autonomous inspection, organization and tidying and finally total autonomous maintenance. In addition to these steps, a team must be set up to monitor this entire process, in the training and training of operators and evaluation (Fig. 7) [26-29].
Step 1. Initial cleaning: in this first step, operators clean and inspect the machines and equipment to solve possible problems in the short term [26-29].
Step 2. Eliminate sources of problems: this step involves making changes to both the equipment and the workstation, to ensure the prevention of dirt, reducing the time spent on these actions as much as possible. In this step, hard-to-reach places must be eliminated, to facilitate operation and maintenance services [26-29].
Step 3. Establish cleaning and lubrication standards: proceed with the construction of cleaning standards to optimize the operating time of actions such as cleaning and checks. It also has the objective of standardizing these norms, so that this procedure is the same in other companies belonging to the same organization [26-29].
Step 4. General inspection: in this step, operators must be trained in basic maintenance on the machines and equipment they deal with daily. Detect possible failures in machines and equipment, through the application of general inspection technical procedures, according to the equipment inspection manual [26-29].
Step 5. Autonomous inspection: once the general inspection is mastered, the necessary information will now be provided, whether inspection procedures, work manuals, among others, to carry out a periodic inspection and adjustments. In this step, operators should already feel able to distinguish whether the equipment is operating correctly and act if an anomaly occurs [26-29].
Step 6. Organization and storage: operators must now organize their workstation, starting with defining the mandatory inspection points on the equipment, organizing the tools and materials essential to the workstation, in the strictly necessary quantities and finally defining the standards. of work and responsibilities [26-29].
Step 7. Total autonomous maintenance: this is the last step of autonomous maintenance, and therefore in this step the employees involved should already be able to autonomously manage their activities and the TPM program. Thus, in this step, it is intended that all information about the equipment be recorded for later analysis that can help in the definition of new parameters to improve the reliability, maintainability, and operability of the equipment [26-29].
As the AM is prepared and implemented as shown in Fig. 7, the operator begins to acquire knowledge. In the initial preparation phase, he begins to acquire knowledge of AM, its objectives, as well as knowledge about equipment and basic maintenance. In the implementation phase, which includes steps 1 to 7, the operator begins to understand and take root in the concept of continuous improvement (steps 1 and 2). In step 3 and 4, the operator continues to acquire more knowledge about the characteristics and operation of the equipment. In steps 5 and 6, the operator, through training, sharing the knowledge he had over time, starts to have a better perception between equipment accuracy and product quality. Finally, in step 7, the operator begins to have greater control and knowledge of the equipment and starts to carry out small repairs to the equipment, as well as to identify and solve problems that may occur daily. Fig. 7 describes the various phases for a correct implementation of AM in a schematic and summarized way.
Fig. 7Flowchart describing the AM implementation
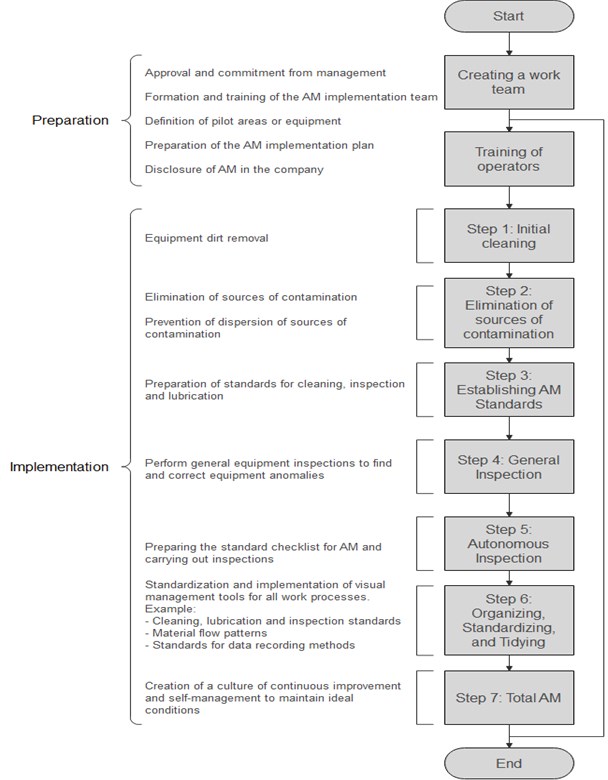
4. Conclusions
Faced with the current market, which is increasingly volatile and competitive, companies need to be in tune with the general objectives and maintenance policies, as this is increasingly essential for the proper functioning of industrial production systems.
The management of maintenance, when effective and efficient, allows to improve not only the performance of the production system and maintenance, which provides a better response to what the market wants, as well as its satisfaction.
This work aimed to develop a real-time monitoring system of important indicators that help to understand what is happening on the shop floor as well as support maintenance decision-making. The designed system allows the monitoring of different parameters of maintenance management at the level of production systems in industries, it can be easily adapted and used in different industrial domains, as it can monitor a wide range of parameters.
The developed model is composed of sensors, gateway, and an Internet of Things service. The sensors collect information, downtime, cycle time, which they in turn send to the gateway. The gateway’s function is to receive the data sent by the sensors and to interface with the cloud. Using a free IoT platform, ThingSpeak, it is possible to view all the information in real time as well as the classification of stops.
The sensors proposed in the system may have some limitation regarding the distance between the various devices that make up the system, but another sensor system can be adapted, however it may increase the cost of the proposed system.
The proposed system aims to implement both an architecture and an AM. AM, being one of the most effective methods for transforming a factory into an operation focused on equipment, will allow to increase the performance of the system, giving these characteristics of reliability, availability, productivity, and operational safety. Such elements can be important for the development of competitive characteristics, such as high quality, reduced lead times, and low production costs.
Although AM is one of the most effective methods to improve production performance, it can present several challenges for companies, such as the preparation and training of maintenance technicians and production operators.
References
-
N. F. Espinoza-Sepulveda and J. K. Sinha, “Robust vibration-based faults diagnosis machine learning model for rotating machines to enhance plant reliability,” Maintenance, Reliability and Condition Monitoring, Vol. 1, No. 1, pp. 1–8, Jun. 2021, https://doi.org/10.21595/mrcm.2021.22110
-
A. Bakri et al., “Addressing the issues of maintenance management in SMEs: towards sustainable and lean maintenance approach,” Emerging Science Journal, Vol. 5, No. 3, pp. 367–379, Jun. 2021, https://doi.org/10.28991/esj-2021-01283
-
O. Bounou, A. El Barkany, and A. El Biyaali, “Performance indicators for spare parts and maintenance management: an analytical study,” Journal of Engineering, Vol. 2020, pp. 1–22, Oct. 2020, https://doi.org/10.1155/2020/2950789
-
J. Bokrantz, A. Skoogh, C. Berlin, and J. Stahre, “Maintenance in digitalised manufacturing: Delphi-based scenarios for 2030,” International Journal of Production Economics, Vol. 191, pp. 154–169, Sep. 2017, https://doi.org/10.1016/j.ijpe.2017.06.010
-
H. Nissoul, T. El Harrouti, D. Serrou, and A. Abouabdellah, “Impact of maintenance 4.0 on the performance of the production function: application to the automotive industry in Morocco,” in 2020 5th International Conference on Logistics Operations Management (GOL), Oct. 2020, https://doi.org/10.1109/gol49479.2020.9314737
-
Coelho et al., “Otimização de processo de manutenção com a modificação do duto de exaustão de uma UTE da cidade de Manaus.,” South American Development Society Journal, Vol. 6, No. 18, pp. 1–19, 2020, https://doi.org/10.24325/issn.2446-5763.v6i18p1-19
-
E. Stefani, J. M. B. Oliveira, P. Montini, J. F. Wanderley, and I. Costa, “Aplicabilidade da filosofia lean na indústria 4.0 / applicability of lean philosophy in industry 4.0,” Brazilian Journal of Development, Vol. 7, No. 3, pp. 21335–21348, 2021, https://doi.org/10.34117/bjdv7n3-036
-
D. Ivina and N. O. E. Olsson, “Lean construction principles and railway maintenance planning,” in 28th Annual Conference of the International Group for Lean Construction (IGLC), pp. 577–588, Jul. 2020, https://doi.org/10.24928/2020/0025
-
W. Shou, J. Wang, P. Wu, and X. Wang, “Lean management framework for improving maintenance operation: development and application in the oil and gas industry,” Production Planning and Control, Vol. 32, No. 7, pp. 585–602, May 2021, https://doi.org/10.1080/09537287.2020.1744762
-
S. Solaimani, J. Veen, D. K. Sobek Ii, E. Gulyaz, and V. Venugopal, “On the application of lean principles and practices to innovation management: A systematic review,” The TQM Journal, Vol. 31, No. 6, pp. 1064–1092, Nov. 2019, https://doi.org/10.1108/tqm-12-2018-0208
-
Tartarotti, L., Sirtori, G., Larentis, and F., “Indústria 4.0: Mudanças e Perspetivas,” in XVIII Mostra de Iniciação Científica, Pós-graduação, Pesquisa e Extensão, 2018.
-
Peter Poór, David Ženíšek, and Josef Basl, “Historical overview of maintenance management strategies: Development from breakdown maintenance to predictive maintenance in accordance with four industrial revolutions,” in EU International Conference on Industrial Engineering and Operations Management (IEOM), Aug. 2019.
-
T. Zonta, C. A. Da Costa, R. Da Rosa Righi, M. J. de Lima, E. S. Da Trindade, and G. P. Li, “Predictive maintenance in the Industry 4.0: A systematic literature review,” Computers and Industrial Engineering, Vol. 150, p. 106889, Dec. 2020, https://doi.org/10.1016/j.cie.2020.106889
-
J. Bokrantz, A. Skoogh, C. Berlin, T. Wuest, and J. Stahre, “Smart Maintenance: a research agenda for industrial maintenance management,” International Journal of Production Economics, Vol. 224, p. 107547, Jun. 2020, https://doi.org/10.1016/j.ijpe.2019.107547
-
J. Dalzochio et al., “Machine learning and reasoning for predictive maintenance in Industry 4.0: Current status and challenges,” Computers in Industry, Vol. 123, p. 103298, Dec. 2020, https://doi.org/10.1016/j.compind.2020.103298
-
Dattaji K. Shinde and Shahikumar Ranjan, “Implementing lean manufacturing technique in fabrication process planning – a case study,” International Journal of Engineering and Technical Research, Vol. 5, No. 7, pp. 2600–2606, Jul. 2018.
-
Mičieta et al., “Increasing work efficiency in a manufacturing setting,” European Research Studies Journal, Vol. 24, No. 4, pp. 601–620, 2021.
-
J. Hanahoe, M. Taggart, and C. Willis, “Not seeing the wood for the trees – a Gemba walk through a timber framed housing development,” in 27th Annual Conference of the International Group for Lean Construction (IGLC), pp. 1209–1218, Jul. 2019, https://doi.org/10.24928/2019/0231
-
D. S. F. T. Mendes, H. V. G. Navas, and F. M. B. Charrua-Santos, “Relationship between maintenance, lean philosophy, and Industry 4.0: Systematic Literature Review,” in European Professors of Industrial Engineering and Management, Vol. 54, pp. 54–59, 2021.
-
L. Magadán, F. J. Suárez, J. C. Granda, and D. F. García, “Low-cost real-time monitoring of electric motors for the Industry 4.0,” in Procedia Manufacturing, Vol. 42, pp. 393–398, 2020, https://doi.org/10.1016/j.promfg.2020.02.057
-
M. Ashjaei and M. Bengtsson, “Enhancing smart maintenance management using fog computing technology,” in 2017 IEEE International Conference on Industrial Engineering and Engineering Management (IEEM), Dec. 2017, https://doi.org/10.1109/ieem.2017.8290155
-
G. Arrascue-Hernandez, J. Cabrera-Brusil, P. Chavez-Soriano, C. Raymundo-Ibañez, and M. Perez, “LEAN maintenance model based on change management allowing the reduction of delays in the production line of textile SMEs in Peru,” in IOP Conference Series: Materials Science and Engineering, Vol. 796, No. 1, p. 012017, Mar. 2020, https://doi.org/10.1088/1757-899x/796/1/012017
-
Parikh, Y., Mahamuni, and P., “Total productive maintenance: need and framework,” International Journal of Innovative Research in Advanced Engineering (IJIRAE), Vol. 2, No. 2, pp. 126–130, 2015.
-
T. K. Agustiady and E. A. Cudney, “Total productive maintenance,” Total Quality Management and Business Excellence, pp. 1–8, Feb. 2018, https://doi.org/10.1080/14783363.2018.1438843
-
Z. Tian Xiang and C. Jeng Feng, “Implementing total productive maintenance in a manufacturing small or medium-sized enterprise,” Journal of Industrial Engineering and Management, Vol. 14, No. 2, pp. 152–175, Feb. 2021, https://doi.org/10.3926/jiem.3286
-
A. Duques Maciel Filho, J. Gomes Da Silva, and M. Sarmanho de Oliveira Lima, “Impact of Autonomous Maintenance on a PIM Production Line,” International Journal for Innovation Education and Research, Vol. 7, No. 12, pp. 385–398, Dec. 2019, https://doi.org/10.31686/ijier.vol7.iss12.2084
-
Maria Antônia Da Silva, Flávia Garrett Azevedo, and Flávia Gonçalves Domingues Ferreira, “TPM E manutenção autonôma: estudo de caso em uma empresa de pintura no ramo automotivo,” Revista Eletrônica da Estácio Recife, Vol. 5, No. 2, 2019.
-
Carvalho et al., “Manutenção Autónoma,” Revista Pesquisa e Ação, Vol. 5, No. 4, pp. 146–156, 2019.
-
O. Joochim and J. Meekaew, “Applying total productive maintenance in aluminium conductor stranding process,” Journal of Industrial Engineering and Management Science, Vol. 2016, No. 1, pp. 1–24, 2016, https://doi.org/10.13052/jiems2446-1822.2016.002
About this article
The author from FCT NOVA acknowledge Fundação para a Ciência e a Tecnologia (FCT-MCTES) for its financial support via the project UIDB/00667/2020 (UNIDEMI).