Abstract
In the current research, modes of frequency of isotropic tapered triangular plate having 1-D (one dimensional) circular thickness and 1-D (one dimensional) linear temperature profile for clamped boundary conditions are discussed. Authors implemented Rayleigh Ritz technique to solve the frequency equation of isotropic triangular plate and computed the first four modes with a distinct combination of plate parameters. Authors have performed the convergence study of modes of frequency of the isotropic triangular plate. Also, conducted comparative analysis of modes of frequency of the current study with available published papers and the results presented in tabular form. The aim of the present study is to show the impact of a one dimensional circular thickness and one dimensional linear temperature on modes of frequency of vibration of an isotropic tapered triangular plate.
1. Introduction
Now a days, study of vibration of nonuniform plates is very essential because vibration plays significantly role in many engineering applications i.e., nuclear reactor, aeronautical field, submarine etc. Study of vibration of triangular plates with variable thickness and temperature has been carried out by many researchers/scientists and has been reported in literature. but till date to the best of the knowledge of the authors, vibration of triangular plate with one dimensional circular thickness has not been considered yet.
Free vibration of cantilevered and completely free isosceles triangular plates based on exact three-dimensional elasticity theory has been investigated in [1] and derived the eigen frequency equation by using Rayleigh Ritz method. Chebyshevs Ritz method is applied in [2] to the free in plane vibration of arbitrary shaped laminated triangular plates with elastic boundary conditions. Time period analysis of isotropic and orthotropic visco skew plate having circular variation in thickness and density at different edge conditions is discussed in [3] and [4]. Two dimensional temperature effect on the vibration is computed in [5] for the first time for a clamped triangular plate with two dimensional thickness by using the Rayleigh Ritz method. A unified formulation was proposed in [6] for the free in-plane vibration of arbitrarily shaped straight-sided quadrilateral and triangular plates with arbitrary boundary conditions by improved Fourier series method (IFSM). Fourier series method is used in [7] for free vibration of arbitrary shaped laminated triangular thin plates. A computationally efficient and accurate numerical model is presented in [8] for the study of free vibration behavior of anisotropic triangular plates with edges elastically restrained against rotation and translation. Free vibration of thick equilateral triangular plates with classical boundary conditions has been investigated in [9] based on a new shear deformation theory. Free vibration of circular and annular three-dimensional graphene foam (3D-GrF) plates under various boundary conditions is discussed in [10].
From the above literature, it is evident that till date to the best of the knowledge of the authors, none of the researchers have worked on triangular plate with one dimensional circular thickness and one dimensional linear temperature environment for clamped boundary conditions. Therefore, in this present study we aim to study the above mentioned problem and investigate the impact on frequency modes of the plate The main purpose of the present study to provide a mathematical model for analyzing the effect of 1-D circular variation in thickness on frequency modes of triangular plate under 1-D linear temperature variation, which had not been investigated earlier. All the numerical results in the form of modes of frequency are presented in tabular form.
2. Problem geometry and analysis
Consider a viscoelastic triangle plate having aspect ratio and and one dimensional thickness as shown in Fig. 1. Now transform the given triangle into right-angled triangle using the transformation and as shown in Fig. 2.
Fig. 1Triangle plate
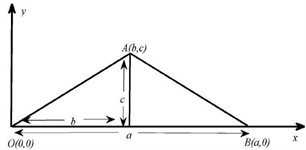
Fig. 2Transformed triangle plate
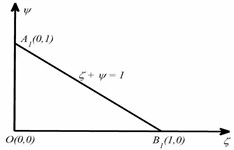
The kinetic energy and strain energy for vibration of a triangle plate are taken as in [11]:
where is the deflection function and is flexural rigidity.
The Rayleigh Ritz method requires:
Using Eqs. (1) and (2), we have:
Introducing one dimensional circular thickness as:
where are the thickness at origin. Also is tapering parameter.
One dimensional temperature on the plate is assumed to be linear as:
where and denote the temperature on and at the origin respectively.
The modulus of elasticity is given by:
where is the Young’s modulus at , and is called the slope of variation. Using Eq. (6) and Eq. (7) becomes:
where , is called thermal gradient. Using Eqs. (5) and (8), the functional in Eq. (4) becomes:
where and .
The deflection function is taken as:
where , are unknowns and the value of , , can be 0, 1 and 2 corresponding to a given edge condition.
To minimize Eq. (9), we have:
Solving Eq. (11), we have frequency equation:
where and are the square matrix of order .
3. Numerical results and discussion
In the current study, authors evaluated numerical data in the form of modes of frequency (first four modes) for right angled isosceles scalene triangular plate, right angled scalene triangular plate and scalene triangular plate on clamped edge condition for the different value of plate parameters. Throughout the calculation the value of aspect ratio 1.5, Poisson’s ratio 0.345, 2.80·103 N/M2 and 2.80·103kg/M3 is taken into consideration. All the results are presented in tabular form (refer Tables 1-3). Table 1 presents the modes of frequency for right angled isosceles triangular plate corresponding to tapering parameter for fixed value of 0, 1.0 and the variable value of thermal gradient i.e., 0.2, 0.6. From the Table 1, it can be seen that the modes of frequency decreases with the increasing value of tapering parameter for all the above mentioned value of thermal gradient . It is also observed that the value modes of frequency decreases with the increasing value of thermal gradient , while the rate of decrement in modes of frequency increases with the increasing value of thermal gradient .
Table 2 incorporates the modes of frequency for right angled scalene triangular plate corresponding to tapering parameter for fixed value of 0, 1.5 and the variable value of thermal gradient i.e., 0.2, 0.6. In table 2 also, modes of frequency decreases with the increasing value of tapering parameter for all the above mentioned value of thermal gradient as shown in Table 1. Like in Table 1, it is also observed in Table 2 that the value modes of frequency decreases with the increasing value of thermal gradient , while the rate of decrement in modes of frequency increases with the increasing value of thermal gradient .
Table 1Modes of frequency of right angle isosceles triangle plate corresponding to tapering parameter
, | ||||||||
0.0 | 100.130 | 366.937 | 831.845 | 2127.902 | 84.6067 | 309.174 | 702.733 | 1815.61 |
0.2 | 97.9199 | 360.068 | 816.224 | 2063.28 | 82.5137 | 302.794 | 687.724 | 1753.50 |
0.4 | 95.7800 | 353.380 | 799.694 | 2024.049 | 80.4804 | 296.555 | 672.161 | 1712.71 |
0.6 | 93.7147 | 346.888 | 785.481 | 1958.46 | 78.5112 | 290.473 | 658.629 | 1649.75 |
0.8 | 91.7283 | 340.614 | 770.259 | 1916.75 | 76.6108 | 284.567 | 644.601 | 1606.46 |
1.0 | 89.8245 | 334.544 | 755.453 | 1883.44 | 74.7835 | 278.878 | 630.245 | 1571.98 |
Table 2Modes of frequency of right angle scalene triangle plate corresponding to tapering parameter
0, | ||||||||
0.0 | 90.3135 | 330.939 | 750.081 | 1917.22 | 76.1245 | 278.106 | 631.328 | 1626.59 |
0.2 | 88.3716 | 324.966 | 736.576 | 1861.97 | 74.2734 | 272.520 | 618.272 | 1573.02 |
0.4 | 86.4950 | 319.165 | 722.302 | 1829.51 | 72.4780 | 267.054 | 604.933 | 1538.14 |
0.6 | 84.6875 | 313.532 | 710.242 | 1773.00 | 70.7424 | 261.745 | 593.284 | 1483.65 |
0.8 | 82.9526 | 308.0911 | 697.482 | 1737.62 | 69.0705 | 256.601 | 581.116 | 1447.01 |
1.0 | 81.2937 | 302.856 | 684.760 | 1710.59 | 67.4662 | 251.626 | 569.113 | 1417.35 |
Table 3Modes of frequency of scalene triangle plate corresponding to tapering parameter
, | ||||||||
0.0 | 78.6772 | 289.064 | 654.766 | 1661.231 | 64.3411 | 237.763 | 538.269 | 1352.55 |
0.2 | 77.5677 | 285.1960 | 645.948 | 1632.17 | 63.2087 | 233.907 | 529.352 | 1321.08 |
0.4 | 76.5167 | 281.485 | 636.874 | 1618.99 | 62.1304 | 230.217 | 519.905 | 1303.43 |
0.6 | 75.5254 | 277.949 | 629.700 | 1584.65 | 61.1079 | 226.664 | 512.370 | 1268.33 |
0.8 | 74.5946 | 274.599 | 621.852 | 1569.17 | 60.1430 | 223.287 | 504.310 | 1248.69 |
1.0 | 73.7247 | 271.443 | 614.434 | 1554.99 | 59.2370 | 220.074 | 496.777 | 1230.15 |
Table 3 provides the modes of frequency for scalene triangular plate corresponding to tapering parameter for fixed value of , and the variable value of thermal gradient i.e., 0.2, 0.6. In table 3 also, modes of frequency decreases with the increasing value of tapering parameter for all the above mentioned value of thermal gradient as shown in Tables 1, 2. Like in Tables 1, 2, it is also reported in Table 3 that the value modes of frequency decreases with the increasing value of thermal gradient , while the rate of decrement in modes of frequency increases with the increasing value of thermal gradient .
4. Convergence study
In this section, authors shows the convergence study done on modes of frequency (first two modes) of right angled isosceles scalene triangular plate, right angled scalene triangular plate and scalene triangular plate at clamped edge condition for the plate parameters specified as , 0.345 and 1.5. The results are displayed in tabular form (refer Table 4). From the Table 4, one can concluded that modes of frequency for the above mentioned triangular plates converges up to three decimal place in fifth approximation.
Table 4Modes of frequency of scalene triangle plate corresponding to tapering parameter
, | , | , | ||||
2 | 107.077 | 436.191 | 107.077 | 436.191 | 92.7314 | 377.753 |
3 | 107.046 | 394.917 | 96.6275 | 356.480 | 92.7048 | 342.008 |
4 | 107.045 | 392.630 | 96.6272 | 354.406 | 92.7045 | 340.018 |
5 | 107.045 | 392.630 | 96.6272 | 354.406 | 92.7045 | 340.018 |
Table 5Comparison of modes of frequency with [12] for right angled isosceles, right angled scalene and scalene triangular plate corresponding to tapering parameter
, | , | , | ||||
0.0 | 107.077 | 436.192 | 96.665 | 393.737 | 84.965 | 346.119 |
107.077 | 436.192 | 79.2171 | 322.7010 | 70.8248 | 288.5140 | |
0.2 | 104.798 | 426.334 | 94.658 | 385.287 | 83.849 | 341.319 |
98.813 | 401.130 | 74.1212 | 301.2510 | 66.7330 | 271.5330 | |
0.4 | 102.595 | 416.894 | 92.731 | 377.213 | 82.792 | 336.839 |
91.069 | 368.577 | 69.4564 | 281.9920 | 63.0304 | 256.6090 | |
0.6 | 100.472 | 407.884 | 90.877 | 369.526 | 81.798 | 332.682 |
83.983 | 339.162 | 65.3054 | 265.3940 | 59.7782 | 244.1390 | |
0.8 | 98.432 | 284.632 | 89.099 | 362.233 | 80.865 | 328.853 |
77.713 | 313.628 | 61.7481 | 251.9720 | 57.0324 | 234.5460 | |
Bold values are obtained from [12] |
5. Results comparison
In this section, authors performed a comparative analysis of modes of frequency (first two modes) obtained in present study (right angled isosceles scalene triangular plate, right angled scalene triangular plate and scalene triangular plate) and modes of frequency obtained in [12] at clamped edge condition and presented in tabular form (refer Table 5). In [12], authors assumed the thickness variations in both the direction but in the present study authors taken the thickness in one direction so authors compared the modes of frequency of present study with modes of frequency obtained in [12] when the value of second tapering parameter is 0.0 in [12]. Table 5 shows the comparison of modes of frequency obtained in present study (right angled isosceles scalene triangular plate, right angled scalene triangular plate and scalene triangular plate) and modes of frequency obtained in [12] at clamped edge condition corresponding to tapering parameter for fixed value of thermal gradient i.e., . From the Table 5, authors conclude that:
1) Modes of frequency obtained in present study (right angled isosceles scalene triangular plate, right angled scalene triangular plate and scalene triangular plate) are higher in comparison to modes of frequency obtained in [12].
2) The rate of change in (decrement) in modes of frequency obtained in present study (right angled isosceles scalene triangular plate, right angled scalene triangular plate and scalene triangular plate) are smaller in comparison to modes of frequency obtained in [12], at clamped edge condition for all the three above mentioned values of thermal gradient .
6. Conclusions
The effect of circular thickness on modes of frequency of right angled isosceles scalene triangular plate, right angled scalene triangular plate and scalene triangular plate under temperature environment at clamped edge condition is computed. Based on numerical discussions and results comparisons, authors would like to records the following facts:
1) The modes of frequency obtained in present study in case of circular thickness is higher than the modes of frequency obtained in [12] in case of linear thickness. The modes of frequency obtained in present study and modes of frequency obtained in [12] exactly match at (refer Table 5).
2) The variation in modes of frequency obtained in present study in case of circular thickness is less in comparison to modes of frequency obtained in [12] in case of linear variation in thickness (refer Table 5).
3) The modes of frequency obtained for the present study decreases (less rate of decrements) with the increasing value of tapering parameter and thermal gradient. (refer Tables 1-3).
4) As temperature increases on the plate, the modes of frequency decreases but the rate of change (decrement) in modes of frequency increases (refer Tables 1-3).
References
-
Y. K. Cheung and D. Zhou, “Three-dimensional vibration analysis of cantilevered and completely free isosceles triangular plates,” International Journal of Solids and Structures, Vol. 39, No. 3, pp. 673–687, Feb. 2002, https://doi.org/10.1016/s0020-7683(01)00196-2
-
D. He, T. Liu, B. Qin, Q. Wang, Z. Zhai, and D. Shi, “In-plane modal studies of arbitrary laminated triangular plates with elastic boundary constraints by the chebyshev-ritz approach,” Composite Structures, Vol. 271, p. 114138, Sep. 2021, https://doi.org/10.1016/j.compstruct.2021.114138
-
A. Sharma, R. Bhardwaj, N. Lather, S. Ghosh, N. Mani, and K. Kumar, “Time period of thermal-induced vibration of skew plate with two-dimensional circular thickness,” Mathematical Problems in Engineering, Vol. 2022, pp. 1–12, Mar. 2022, https://doi.org/10.1155/2022/8368194
-
N. Lather, R. Bhardwaj, A. Sharma, and K. Kumar, “Time period analysis of orthotropic skew plate with 2-d circular thickness and 1-d circular density,” Mathematical Problems in Engineering, Vol. 2022, pp. 1–15, Oct. 2022, https://doi.org/10.1155/2022/7880806
-
A. Khodiya and A. Sharma, “Temperature effect on frequencies of a tapered triangular plate,” Journal of Applied Mathematics and Computational Mechanics, Vol. 20, No. 1, pp. 37–48, 2021.
-
T. Liu, G. Hu, A. Wang, and Q. Wang, “A unified formulation for free in-plane vibrations of arbitrarily-shaped straight-sided quadrilateral and triangular thin plates,” Applied Acoustics, Vol. 155, pp. 407–422, Dec. 2019, https://doi.org/10.1016/j.apacoust.2019.06.014
-
X. Lv and D. Shi, “Free vibration of arbitrary-shaped laminated triangular thin plates with elastic boundary conditions,” Results in Physics, Vol. 11, pp. 523–533, Dec. 2018, https://doi.org/10.1016/j.rinp.2018.09.003
-
L. G. Nallim, B. M. Luccioni, and R. O. Grossi, “Vibration of general triangular composite plates with elastically restrained edges,” Thin-Walled Structures, Vol. 43, No. 11, pp. 1711–1745, Nov. 2005, https://doi.org/10.1016/j.tws.2005.07.002
-
K. Pradhan and S. Chakraverty, “Natural frequencies of equilateral triangular plates under classical edge supports,” in Symposium on Statistical and Computational Modelling with Applications, 2016.
-
Y. Q. Wang and M. W. Teng, “Vibration analysis of circular and annular plates made of 3d graphene foams via Chebyshev-Ritz method,” Aerospace Science and Technology, Vol. 95, p. 105440, Dec. 2019, https://doi.org/10.1016/j.ast.2019.105440
-
S. Chakraverty, Vibration of plates. CRC Press, 2008, https://doi.org/10.1201/9781420053968
-
N. Kaur, “Vibrational behavior of tapered triangular plate with clamped ends under thermal condition,” Journal of The Institution of Engineers (India): Series C, Vol. 101, No. 2, pp. 391–399, Apr. 2020, https://doi.org/10.1007/s40032-019-00551-9
About this article
The authors have not disclosed any funding.
The datasets generated during and/or analyzed during the current study are available from the corresponding author on reasonable request.
The authors declare that they have no conflict of interest.