Abstract
In this paper, lithium slag was used as raw material to prepare zeolite framework with porous structure by alkali activation and hydrothermal synthesis. The alkali activation of raw materials and the phase analysis of zeolite products were carried out by XRD characterization methods, and the effects of different alkali fusion conditions and hydrothermal conditions on zeolite synthesis were investigated. At the same time, the effects of different temperatures on the adsorption capacity and adsorption heat of carbon dioxide adsorbed by zeolite skeleton model under normal pressure were studied by using Materials studio software. The results showed that the optimum alkali fusion conditions were: 500 °C, 6 h; the best hydrothermal condition is 220 °C, 6 h. The average adsorption capacity of cristobalite for carbon dioxide is 2 mmol/g, and the adsorption heat is 11.98 kJ/mol.
1. Introduction
At present, spodumene is the most important source of lithium extraction industrialization, but 8-10 tons of lithium slag will be produced per ton of lithium after lithium extraction. By 2018, the annual output of lithium slag has reached about 1.25 million tons [1]. With accumulation over the years, the stock of lithium slag in China could reach tens of millions of tons. These lithium slags will be released into the environment in large quantities, which will harm the natural environment and people. Therefore, recycling lithium slag can not only reduce the environmental impact of lithium slag, but also increase the added value of the lithium mining industry. Although many researchers have studied the preparation of zeolite from lithium slag, the types of zeolite synthesized from lithium slag are limited. Lin et al. [2]. successfully prepared zeolites using a microwave to stimulate the hydrothermal activity of lithium slag, and used the mother liquor for subsequent preparation to obtain FAU/LTA eutectic zeolite. FAU/LTA has better adsorption capacity than commercial zeolite 4A. Wang et al. [3]. proposed a mild activation method and synthesized a highly crystalline zeolite A, which has excellent selectivity for the radioactive isotope 90Sr in aqueous solution. In addition, molecular dynamics simulation can be used to calculate the interaction forces between molecules from a microscopic point of view to simulate the adsorption performance of zeolite materials. He et al. [4]. measured the adsorption performance of SO2 in HZSM-5 zeolite by experiments and built the corresponding adsorption model using the Grand Canonical Monte Carlo method to simulate the corresponding adsorption behavior.
Therefore, in this work, highly crystalline analcime (ANA) was successfully prepared by alkali fusion and hydrothermal method using lithium slag as raw material, and the optimum synthesis conditions including alkali fusion conditions and hydrothermal conditions were determined. Based on the molecular dynamics simulation method, Materials Studio software was used to simulate the adsorption performance of zeolite for carbon dioxide, and the effects of temperature on the adsorption performance of analcime at atmospheric pressure were studied. The results of this study fill the research on the optimal synthesis conditions and adsorption properties of ANA synthesized from lithium slag, and provide a richer theoretical basis for the study of high-value waste utilization of lithium slag.
Fig. 1Flow chart of lithium slag synthesis of zeolite and carbon dioxide adsorption performance simulation
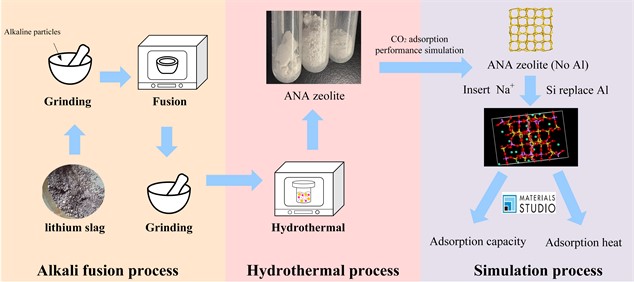
2. Materials and methods
2.1. Raw materials and reagents
The lithium slag (LS) is provided by Guoqiang Mining Co., Ltd. Both sodium hydroxide particles and anhydrous ethanol from Tianjin Kmart Chemical Technology Co., Ltd. were determined to be analytically pure. Table 1 is the chemical composition of the lithium slag and Fig. 2 is the XRD pattern of the lithium slag. It can be seen that the lithium slag is mainly composed of quartz (SiO2) and albite (Na2O·Al2O3·6SiO2), and the main elements in the lithium slag are silica and alumina, accounting for about 85 %.
Table 1Chemical composition of lithium slag
Name | Formula | Content (wt%) |
Silicon dioxide | SiO2 | 80.10 |
Alumina | Al2O3 | 12.70 |
Ferric oxide | Fe2O3 | 0.08 |
Calcium oxide | CaO | 0.07 |
Magnesium oxide | MgO | 0.09 |
Titanium oxide | TiO2 | 0.01 |
Potassium oxide | K2O | 2.60 |
Sodium oxide | Na2O | 3.60 |
Lithia | Li2O | 0.10 |
2.2. Preparation of zeolite from lithium slag
The lithium slag was pretreated by the alkali fusion. The main steps are as follows: (1) First, lithium slag and sodium hydroxide particles with different weight ratios (0.5, 0.8, 1.5) were mixed by grinding. (2) Then the alkali-slag mixture was transferred to the crucible and alkali activation was carried out at fusion temperatures (200 °C, 350 °C, 500 °C) and fusion time (1 h, 2 h, 6 h). The experimental steps for hydrothermal synthesis reaction are as follows: (1) Transfer 3 g of the above alkali-activated product to a beaker containing 30 mL of deionized water and stir to obtain a mixture. (2) The mixture was transferred to an autoclave with Para-polyphenylene lining and heated at hydrothermal temperatures (150 °C, 180 °C, 220 °C) and hydrothermal time (2 h, 6 h, 8 h). (3) After the reaction, it was cooled to room temperature, filtered and dried, and finally the zeolite product was obtained. The synthesis conditions in Table 2.
Fig. 2XRD patterns of lithium slag
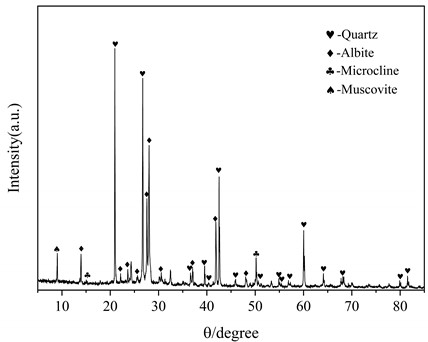
Table 2Conditions for synthesis of zeolite from lithium slag
Alkali: LS | Alkali fusion temperature (℃) | Alkali fusion time (h) | Hydrothermal temperature (℃) | Hydrothermal time (h) |
1.5 | 500 | 1 | 150, 180, 220 | 2, 6, 8 |
1.5 | 200 | 1 | ||
1.5 | 350 | 1 | ||
1.5 | 500 | 2 | ||
1.5 | 500 | 6 | ||
0.8 | 500 | 1 | ||
0.5 | 500 | 1 |
2.3. Simulation of zeolite adsorption performance based on GCMC method
In this paper, the Materials Studio of mainstream material simulation modeling software is used to study the adsorption performance of zeolite. The simulation steps are mainly divided into two steps: First, a zeolite simulation skeleton consistent with the XRD pattern of the experimental sample is constructed. Due to the silica-alumina ratio of ANA zeolite is between 1.82 and 2.2 [5], 1/3 of the Si atoms in the ANA all-silica zeolite framework are replaced by Al atoms and follows the Lowenstein rule [4]. Then the Na+ is introduced to balance the charge in the framework system. The Dmol3 module and the Reflex module are used to optimize the zeolite framework structure and simulate the XRD patterns, respectively.
Fig. 3Optimized ANA zeolite structure model and XRD
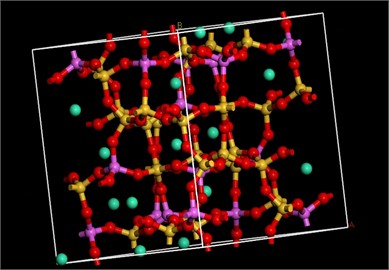
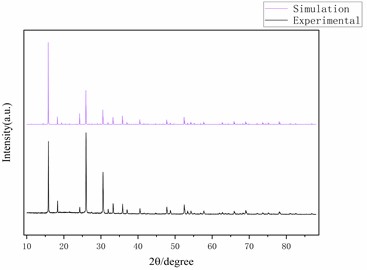
The results are shown in Fig. 3, and the positions of the peaks are basically consistent, indicating that the skeleton model is highly consistent with the structure of ANA zeolite. Second, the Sorption module is used to simulate the adsorption capacity and heat of ANA zeolite for carbon dioxide at different temperatures (10 °C, 20 °C, 30 °C) and atmospheric pressure (101.3 kPa). Ewald summation method was used with the accuracy of 0.01 kcal·mol-1 to calculate the long-range electrostatic interactions. Additionally, using atom-based summation method with the cut off distance of 6.5 (Å)×10-10m, van der Waals potential energy was calculated. The number of calculations for achieving the equilibrium was considered 1×106 steps for equilibrium and 1×106 steps for production. The duration of each timestep was 1 fs.
3. Effect of synthesis conditions on zeolite
3.1. Effect of alkali fusion conditions on lithium slag
Three important conditions for alkali fusion: (1) alkali fusion temperature, (2) alkali fusion time, and (3) the weight ratio of NaOH to lithium slag (alkali-slag ratio) have some influence on Al2O3 and SiO2 in the raw material lithium slag. Fig. 4(a) shows that at alkali-slag ratio of 1.5, alkali fusion time of 1h and alkali fusion temperature of 200 °C, 350 °C and 500 °C, respectively, a phase change occurs in the lithium slag of the raw material. As can be seen in the figure, most of the silicon dioxide in the lithium slag melts with sodium hydroxide and reacts to form NaAlSiO2 at 200 °C. When the temperature rises to 350°C, the lithium slag reacts with sodium hydroxide to give sodium silicate and sodium aluminate under the conditions of alkali-slag ratio and alkali fusion time of 1.5 and 1 h, respectively. When the temperature reaches 500°C, the SiO2 has completely dissolved into sodium aluminate and sodium silicate. Fig. 4(b) shows the lithium slag at an alkali-slag ratio of 1.5, alkali fusion temperature of 500 °C and an alkali fusion time of 1 h, 2 h and 6 h, respectively. When the alkali fusion time gradually increases, the characteristic crystallization peaks at 28° and 39° are enhanced, and the lithium slag is gradually activated to soluble aluminosilicate with increasing alkali fusion time at high temperature. Fig. 4(c) shows alkali fusion temperature of 500 °C, alkali fusion time of 1 h, and alkali-slag ratio of 0.5, 0.8 and 1.5, respectively. When the alkali-slag ratio is 0.5, sharp characteristic crystallization peaks are found at 27° and 33°, indicating that the SiO2 in the lithium slag is not completely melted. At an alkali slag ratio of 1.5, the SiO2 is completely melted and a large amount of soluble aluminosilicate is formed. From the above alkali fusion experiments, it is clear that the optimum alkali fusion conditions are alkali-slag ratio of 1.5, alkali fusion temperature of 500 °C, and alkali fusion time of 6 h.
3.2. Effect of hydrothermal conditions on zeolite
Fig. 5(a) is the X-ray diffraction pattern of the zeolite prepared under the optimum alkali fusion conditions at a hydrothermal time of 6 h and hydrothermal temperature of 150 °C, 180 °C and 220 °C, respectively. The black line represents the characteristic peak of the analcime (Na2[AlSi2O6]2-2H2O, No: 41-1478) in the standard PDF. As can be seen in Fig. 5(a), at hydrothermal temperature of 150 °C, the intensity of the characteristic peak of ANA zeolite is greater, but at the same time there are impurity peaks near 15°, 43° and 30°. When the hydrothermal temperature is 220 °C, the characteristic peak of ANA zeolite is clearly visible, and there is no other impurity peak in the diagram. Fig. 5(b) shows the hydrothermal temperature is 150 °C and the hydrothermal time is 2 h, 6 h and 8 h, respectively. When the hydrothermal time is 2 h and 6 h, there are obvious characteristic peaks of ANA zeolite, but at the same time there are also different peaks near 15°, 43° and 30°. With the increase of hydrothermal time to 8 h, the characteristic peak of ANA zeolite crystallization in the product is obvious, and there is no other impurity peak in the graph.
XRD analysis shows that the product of this experiment is consistent with that of ANA zeolite. Table 3 shows the crystallinity of ANA zeolite prepared under different hydrothermal conditions. Under the optimum alkali fusion conditions, the alkali-activated lithium slag product was hydrothermally heated at 220 °C for 8 hours to obtain a cristobalite with crystallinity up to 96.3 %. Moreover, the crystallinity of the zeolite synthesized by the long-term hydrothermal reaction is about 85 % for 8 hours. However, too high hydrothermal temperature or too long hydrothermal time leads to energy waste. Therefore, the optimum hydrothermal temperature is 220 °C and the hydrothermal time is 6 h.
Fig. 4XRD patterns of the products at different alkali fusion condition
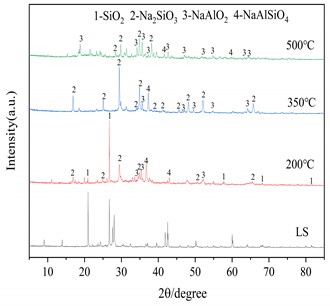
a) Influence of alkali fusion temperature
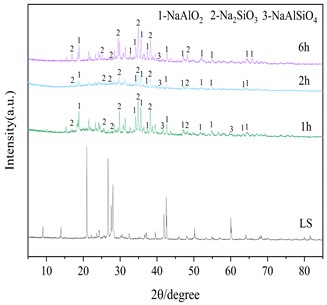
b) Influence of alkali fusion time
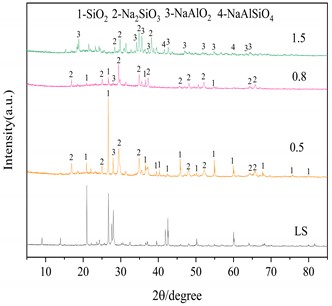
c) Influence of alkali slag ratio
Fig. 5XRD patterns of the products at different hydrothermal condition
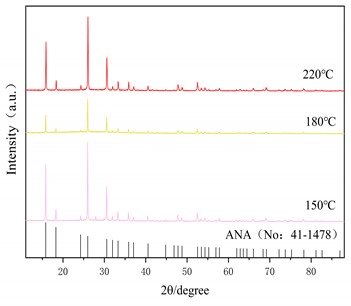
a) Influence of hydrothermal temperature
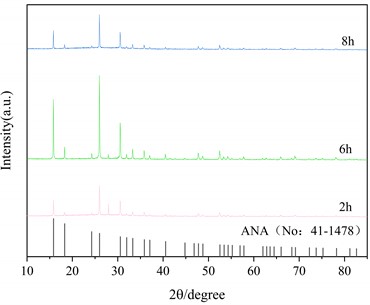
b) Influence of hydrothermal time
3.3. Simulation results of carbon dioxide adsorption performance of ANA zeolite
The adsorption quantity in Table 4 indicates the instantaneous values at which the amount of adsorbed carbon dioxide reaches the maximum and minimum at a certain time of the simulation process. The average value of adsorption quantity can represent the strength of adsorption capacity, and the average value of isosteric adsorption heat is a standard to measure the strength of adsorption capacity between the adsorbent and adsorbate. The larger the value, the stronger the adsorption capacity and vice versa. From the table, it can be seen that as the temperature increases, the average adsorption amount of CO2 on the zeolite skeleton gradually decreases. The reason is that the adsorption of carbon dioxide on the zeolite occurs by a physical adsorption mechanism. This adsorption is caused by the van der Waals force between the molecules and the interaction between the surfaces of the adsorbent, so it decreases with increasing temperature [6]. Moreover, the isosteric adsorption heat of CO2 on ANA zeolite increases slightly with increasing temperature, which is also consistent with the trend of numerical change in the literature [7].
Table 3The Influence of hydrothermal conditions on the crystallinity of zeolites
Alkali fusion temperature (℃) | Alkali fusion time (h) | Alkali: LS | Hydrothermal temperature (℃) | Hydrothermal time (h) | Crystallinity |
500 | 6 | 1.5 | 220 | 8 | 96.3 % |
180 | 2 | 82.2 % | |||
180 | 6 | 84.6 % | |||
180 | 8 | 85.5 % | |||
150 | 6 | 78.1 % | |||
150 | 8 | 86.4 % | |||
120 | 6 | 76.3 % |
Table 4Adsorption performance index of carbon dioxide at different temperatures
Adsorb ability | Temperature (℃) | |||
10 | 20 | 30 | ||
Adsorption quantity (, mmol/g) | Min | 1.86 | 1.55 | 1.24 |
Mean | 2.30 | 1.96 | 1.77 | |
Max | 2.78 | 2.48 | 2.48 | |
Adsorption heat (, kJ/mol) | Min | 2.76 | 1.58 | 2.70 |
Mean | 11.69 | 12.05 | 12.20 | |
Max | 15.36 | 15.38 | 15.50 |
4. Conclusions
In this study, ANA zeolite was successfully prepared by a two-step process using lithium slag as raw material. At the same time, the performance of adsorption of carbon dioxide by ANA zeolite was simulated based on the Grand Canonical Monte Carlo method. The results are as follows:
1) Alkali fusion conditions can better convert lithium slag into water-soluble aluminosilicate. According to the XRD results, the best alkali fusion temperature is 500 °C and the alkali fusion time is 6h.
2) ANA zeolite with a crystallinity of 96.3 % was successfully synthesized by adjusting the hydrothermal time and temperature, where the optimum hydrothermal temperature was 220 °C and the hydrothermal time was 6 h.
3) The average adsorption quantity of carbon dioxide on the simulated ANA zeolite is about 2 mmol/g and the adsorption heat is 11.98 kJ/mol.
References
-
X. Wang, H. Wang, Q. Wang, “Research progress on resource utilization of lithium slag in China,” Materials Reports, Vol. 36, No. 24, pp. 22040195–22040111, 2023.
-
G. Lin, Q. Zhuang, Q. Cui, H. Wang, and H. Yao, “Synthesis and adsorption property of zeolite FAU/LTA from lithium slag with utilization of mother liquid,” Chinese Journal of Chemical Engineering, Vol. 23, No. 11, pp. 1768–1773, Nov. 2015, https://doi.org/10.1016/j.cjche.2015.10.001
-
B. Wang et al., “Facile activation of lithium slag for the hydrothermal synthesis of zeolite A with commercial quality and high removal efficiency for the isotope of radioactive 90Sr,” Inorganic Chemistry Frontiers, Royal Society of Chemistry (RSC), 2022.
-
S. He et al., “Molecular Simulation of Sulfur Dioxide Adsorbed on HZSM-5,” (in Chinese), Journal of The Chinese Ceramic Society, Vol. 38, No. 9, pp. 1832–1836, 2010.
-
C. Baerlocher, L. B. Mccusker, and D. H. Olson, Atlas of Zeolite Framework Types. Netherlands: Elsevier, 2007, https://doi.org/10.1016/b978-0-444-53064-6.x5186-x
-
Y. Zhang, “Molecular simulation of crystal configuration of kaolinite minerals and its adsorption for Cd2+,” (in Chinese), Taiyuan University of Technology, ShanXi, 2018.
-
K. N. Son, G. E. Cmarik, J. C. Knox, J. A. Weibel, and S. V. Garimella, “Correction to “Measurement and prediction of the heat of adsorption and equilibrium concentration of CO2 on zeolite 13X”,” Journal of Chemical and Engineering Data, Vol. 65, No. 8, pp. 4172–4172, Aug. 2020, https://doi.org/10.1021/acs.jced.0c00546
About this article
The authors have not disclosed any funding.
The datasets generated during and/or analyzed during the current study are available from the corresponding author on reasonable request.
The authors declare that they have no conflict of interest.