Abstract
In order to analyze the impact of the new pier bearing platform construction on the bridge section adjacent to the high-speed railway line, a new pier bearing platform project adjacent to the high-speed railway line in the soft soil area of the Yangtze River Delta is taken as the background of the project, and the finite element software Plaxis 3D is used to study the impact of the pier bearing platform construction on the bridge section adjacent to the high-speed railway line, and to analyze the effect of distance on the horizontal displacement and settlement of the bridge foundation soil body. The neighboring high-speed rail line bridge is displaced horizontally toward the foundation, with the maximum horizontal displacement of 1.5 mm and the maximum settlement of 5.5 mm; the existing pier bearing platforms are also displaced in the same direction, with the maximum horizontal displacement of 2.7 mm and the maximum settlement of 5.4 mm, and the pier bearing platforms in the middle are affected the most.
1. Introduction
High-speed rails have been built quickly and implemented one after another in tandem with the growth of urbanization. Building an intercity railroad next to a high-speed railroad becomes essential in order to reduce the transportation strain on already-existing high-speed railway lines, as well as to further boost the network’s density and operating efficiency [1-3]. In the construction process of intercity railroad adjacent to the existing high-speed rail line, a large number of pier and bearing platform projects will be generated [4]. The construction of piers and platforms will lead to the displacement of foundation soil, which in turn will produce additional displacement to the adjacent existing high-speed rail line [5-6]. As a result, there has been an increasing focus on both the regular functioning of the current high-speed rail line and the building safety of new intercity railroad pier bearing platforms.
A new line crossing an old line will cause the previous soil layer to be unloaded during construction of the new line beneath, which will cause the surrounding soil to shift and have a major effect on the higher buildings (structures). Interaction in crossing construction research has always drawn a lot of interest [7-8]. Yang et al. [9] used a metro tunnel excavation simulation to study the deformation and stress distribution in an existing pedestrian underpass caused by a new line that undercuts it in order to examine the effects of a new metro tunnel on an existing pedestrian underpass. To provide realistic guidelines for the building of a shield underpass as a method of guaranteeing the safety of the current tunnel, Huang et al. [10] put up a test section of a shield tunnel beneath an existing high-speed railway tunnel. A shield tunnel model undercrossing a high-speed railway tunnel was built by Zhao et al. [11] in order to assess the force and deformation impacts of the underpass construction on the current tunnel structures. Lee [12] assessed the displacement effect of underpass construction on the nearby pier structures by analyzing the underpasses beneath the nearby bridge using 3D finite element software.
Since the building of new lines will unavoidably have an impact on the current high-speed rail network, the new lines must guarantee the stability and safety of the current high-speed rail network throughout the construction process. The effect of the pit distance during the pier bearing platform's pre-construction phase on the pier bearing platform next to the high-speed rail line, however, is still not well studied. This paper uses Plaxis 3D finite element numerical computation to examine the effects of a new pier bearing project on the nearby bridge section of the high-speed rail line in order to address the shortcomings of the previous studies.
2. Finite element modeling
2.1. Engineering overview
A new intercity railroad is located in the plain area of the Yangtze River Delta, and the construction area is characterized by large variations in stratigraphic lithology and poor engineering geological conditions. The upper part of the clayey soil, the lower part of the sand layer containing multiple layers of fine sand, shallow groundwater is pore diving, diving level depth ranging from 0 to 3.0 m, groundwater with micro-pressure, groundwater is rich, water level changes are not large. The whole line is parallel to the existing Hutong High-speed Railway, with a design speed of 350 km/h, and the total length of the line is 278.53 km. The location of the steel sheet pile cofferdam of part of the bearing platforms is less than 30 m away from the Hutong High-speed Railway line, which belongs to the neighboring existing line, and the 305 pier bearings of bridges are facing the construction of neighboring high-speed railway line. The construction site of the new pier bearing platform is shown in Fig. 1. The pier bearing platform in the area with poor soil quality, located in the reservoir and adjacent to the high-speed rail line adopts the steel sheet pile cofferdam construction.
2.2. Soil parameters
The basic physical and mechanical properties of each soil layer are derived from the proposed design parameters of the pier bearing platform in the engineering ground investigation report, with a total of five soil layers. The parameters of each soil layer are shown in Table 1.
Table 1Basic parameters of the soil body
Soil name | Unsaturated density (kN/m3) | Cohesive force (kPa) | Angle of internal friction (°) | Poisson’s ratio | Compression modulus (kPa) | Depth (m) |
Silty powdery clay | 18.0 | 10.27 | 10.49 | 0.36 | 2.0×103 | 15 |
Silty clay | 18.6 | 9.83 | 17.97 | 0.34 | 2.79×103 | 16 |
Silt | 19.4 | 5.0 | 31.0 | 0.28 | 11.73×103 | 8 |
Clay | 19.7 | 21.51 | 22.72 | 0.35 | 3.45×103 | 10 |
Medium sand | 18.8 | 1.0 | 29.0 | 0.31 | 10.82×103 | 31 |
Miscellaneous fill | 19.5 | 24.5 | 21.5 | 0.30 | 31.0×103 | – |
Reinforced concrete | 24.5 | – | – | 0.20 | 3.0×107 | – |
2.3. Structural material modeling
Plaxis 3D finite element software can use plate unit, beam unit, Embedded pile unit to simulate the structure of the actual project, and interface unit to simulate the mutual contact of the structure. The cofferdam adopts Larsen SP-VIL steel sheet piles and the concrete bedding under the pier abutment is simulated by plate unit; the pier abutment supporting structure is simulated by beam unit, the inner support adopts circular steel pipe, and the bored pile is simulated by Embedded pile unit. The size of the abutment adjacent to the high-speed railway line is 9.3 m×6.6 m×2.5 m, the size of the bottom of the pier is 5.8 m×2.4 m, and the height of the pier is 14.5 m, and the bottom of the abutment is drilled piles with the diameter of 1.0 m and the length of the piles is 70 m, the nearest distance between the abutment of the pier adjacent to the high-speed railway line and the new pier abutment pit is 12.45 m, and the excavation depth of the pit of the new pier abutment is 11.35 m at most, and the weir is used as the support structure of the pier abutment, the inner support is made of circular steel pipe. The construction is driven into 24 m deep steel sheet piles, and the support structure is set up at the depth of 1, 4 and 7 m in the excavation of the foundation pit, including walings, inner supports and corner supports. The bottom sealing was done using 0.3 m thick C30 concrete and a 0.2 m thick gravel bedding. The bearing platforms and piers adjacent to the high-speed railway line are made of C30 concrete, and the main reinforcement material is HRB400 steel bar.
2.4. Finite element model
This study exclusively analyzes the impact of new pier bearing platform construction on adjacent high-speed railway line bridge sections, omitting consideration of dynamic loading from railway traffic. The neighboring high-speed rail line is in the form of bridge pier bearing platform, and the pit area of the new pier bearing platform is larger, the excavation depth is deeper, and the hydraulic conditions at the location are more complicated. Considering the spatial stress-strain effect of the new pier bearing platform construction, Plaxis 3D finite element software will be used to simulate the finite element model mesh as shown in Fig. 2. In order to ensure the accuracy of the calculation, the soil is simulated by 15-node triangular cells [13]. According to the actual situation to determine the location of the water table, the water table line is set at 0 m, the model boundary to limit the seepage, a total of 22,395 cells generated, 53,916 nodes.
Fig. 1Construction site plan of the new pier bearing platform adjacent to the high-speed rail line
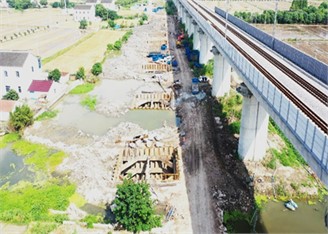
Fig. 2Mesh division of the finite element model
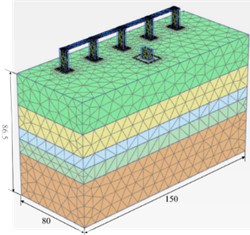
3. Results and analysis
3.1. Displacement analysis of pier bearing platforms adjacent to high-speed rail line
The magnitude of displacement difference of adjacent pier bearing platforms plays a key role in the safe and stable operation of the neighboring high-speed rail line. The displacement map of the new pier bearing platforms in its final stage and the displacement map of the pier bearing platforms of the neighboring high-speed rail line are shown in Figs. 3 and 4. As can be seen in Figs. 3 and 4, the pier bearing displacement is mainly from settlement, and the horizontal displacement is too small compared to the settlement value. As the distance to the pit increases, the displacement decreases, pier bearing platform 3 (middle bearing platform) displacement is the largest. Taking the vertical diagonal as the dividing line, the pier and bearing on the side close to the foundation pit are larger than on the other side, and the total displacement trend of each bearing is different. The pier body of pier bearing 3 is displaced towards the foundation pit, while the rest of the pier body is displaced towards the x-negative direction, and the bearing platform part is dominated by settlement. Take the pier body and bearing platform settlement maximum position, the rest of the pier bearing platform also choose the same position node, draw the vertical displacement curve.
Fig. 3Displacement cloud of new pier bearing (m)
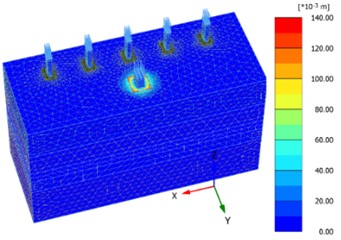
Fig. 4Displacement maps of pier bearing platforms adjacent to the high-speed rail line
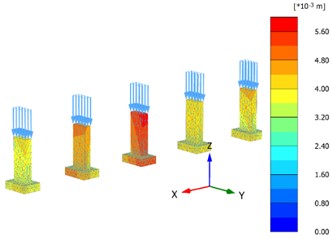
In order to avoid the pier bearing platform to produce too large a difference in the uneven settlement, and then the various neighboring high-speed rail line pier and bearing platform final settlement is plotted as a curve, as shown in Fig. 5.
Fig. 5Vertical displacement curves of pier bearing platforms adjacent to the high-speed rail line
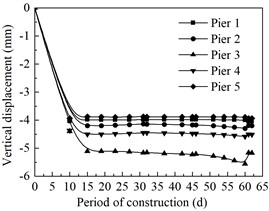
a) Pier
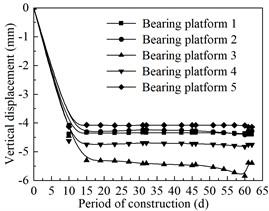
b) Bearing platform
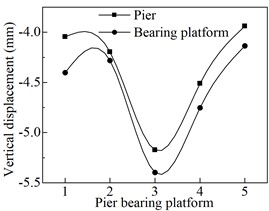
c) Pier bearing platform
From Fig. 5, it can be concluded that: (1) the settlement trend of pier body and bearing platform adjacent to the high-speed rail line is similar, the maximum settlement is within 6mm, and a large settlement is generated in the construction of bored piles, followed by the construction of steel sheet piles, which also has a relatively large impact on the settlement, and the closer the pit, the greater the impact. The final settlement of the platform of the existing high-speed rail line is slightly larger than that of the pier body, and at the location of pier bearing platform 3, the settlement of the pier body and the bearing platform have reached the peak. (2) At present, the limit value of total settlement of pier bearing platform of high-speed railroad in China [14] is ∆1=20L1/2; the limit value of uniform total settlement of adjacent pier bearing platform is ∆2=10L1/2, where L is the length of the minimum span between adjacent pier bearing platforms, m. Calculation can be obtained as ∆1=100 mm, ∆2=50 mm, and the total settlement and the difference settlement of adjacent pier bearing platforms in the model are smaller than ∆1 and ∆2, which satisfy the requirements.
3.2. Impact of new pier bearing distance on neighboring high-speed rail lines
The distance from the newly constructed pier bearing to the neighboring high-speed rail line pier bearing is the key factor affecting the soil displacement of the high-speed rail line. By varying the distance between the two lines (2, 4, 8, 12, 16, 32 and 64 m), the maximum values of the displacement of the high-speed rail line pier bearings in the horizontal and vertical directions at different distances were obtained, as shown in Fig. 6.
Fig. 6Soil displacement-distance relationships for pier bearing platform adjacent to the high-speed rail line
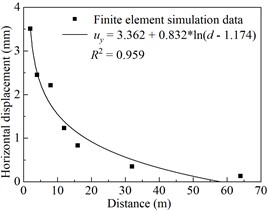
a) Horizontal displacement
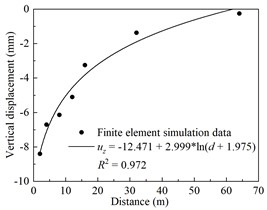
b) Vertical displacement
From Fig. 6, it can be seen that both horizontal and vertical displacements tend to decrease as the distance from the newly constructed pier bearing to the soil body where the pier bearing of the high-speed rail line is located increases, and a curve-fitting relationship for the displacement (uy/z) of the bridge section with distance (d) is derived.
The equation of the fitted curve for horizontal displacement and vertical displacement are shown in Eq. (1) and Eq. (2):
where uy/z is the displacement in the y or z direction, respectively, mm; d is the distance from the new pier cap project to the pier cap of the high-speed railway line, m; R2 is the correlation coefficient.
In the Technical Specification for Observation and Evaluation of Settlement and Displacement in Railway Engineering [15] and High-speed Railway Design Specification [16], the post-work settlement of ballasted track bridge pier bearing platforms should be less than 30 mm for a design speed of 250-350 km/h, and that of ballasted track should be less than 20 mm, but this is the alarm value for post-work observation, and the limit value should be controlled in a lower range in the neighboring construction stage. Numerical calculation of horizontal displacement and vertical displacement is numerically located in the same order of magnitude, so the limit value of horizontal displacement can also refer to the value of vertical displacement, and when the limit value of displacement is stipulated, the safety range of pier and bearing platform construction can be inverted through the fitted displacement curve. Given that there is a 60 % difference between the numerical calculation results for the horizontal displacement and vertical displacement quantities of the bridge section of the current high-speed railway line, let uy=2 mm, dy=6.31 m; let uy=1 mm, dy=18.28 m; and let uy=0 mm, dy=58.11 m. Assume uz= –5 mm, dz= 10.10 m, uz= –2.5 mm, dz= 25.83 m, and uz= 0 mm, dz= 62.02 m in separate equations. Results show that the adjacent high-speed railway bridge section is significantly impacted by distances of 6 meters or less.
4. Conclusions
In this paper, with the background of the pier bearing platform project in a soft soil area adjacent to the bridge section of the high-speed rail line, with the help of Plaxis 3D finite element to establish the field model, the impact of the new pier bearing platform construction on the adjacent high-speed rail line is studied, and the following conclusions are drawn:
1) The bridge of the neighboring high-speed rail line is displaced horizontally to the pit direction, the maximum horizontal displacement is 1.5 mm, and the vertical direction settlement, the maximum settlement is 5.5 mm. the existing pier bearing platforms are also displaced in the same direction, the maximum horizontal displacement is 2.7 mm, and the maximum settlement is 5.4 mm, and the middle pier bearing platforms are affected the most.
2) In the construction condition, the greater influence on the horizontal displacement is the activation of the bored piles, excavation of the foundation pit, insertion and extraction of the steel sheet piles and backfilling of the foundation pit. The greater influence on settlement is activation of bored piles, pit descending excavation, casting and loading of new piers.
3) When the construction distance of the bridge section adjacent to the high-speed rail line is above 62 m, there is almost no impact on the high-speed rail line. When the distance is 18-62 m, the impact is small; when the distance is 6-18 m, the impact is large; and when the distance is less than 6 m, it will have a great impact.
References
-
T. Yang, S. L. Liu, H. Zhao, and X. R. Li, “Study on the restraint control of an isolation pile on an existing high-speed railway during the close passing of a shield machine,” Frontiers in Earth Science, Vol. 11, p. 11428, 2023, https://doi.org/10.3389/feart.2023.1142864/full
-
R. Hu, S. Hu, X. Zhang, M. Yang, and N. Zheng, “Innovative simulation method of the spherical steel bearing applied to high-speed railway bridges,” Structural Engineering and Mechanics, Vol. 85, No. 2, pp. 265–274, Jan. 2023, https://doi.org/10.12989/sem.2023.85.2.265
-
H. Zheng and W. Yan, “Study on dynamic response and permanent deformation of the pier and its surrounding sites induced by high-speed train loads in seasonally frozen regions,” Construction and Building Materials, Vol. 331, p. 127264, May 2022, https://doi.org/10.1016/j.conbuildmat.2022.127264
-
P. Pan, W. Chen, and P. Wu, “Safety and stability analysis of demolition and reconstruction of existing railway bridge piers and caps,” Applied Sciences, Vol. 13, No. 12, p. 7213, 2023, https://doi.org/doi.org/10.3390/app13127213
-
Y. Cao, H. Xia, W. Lu, K. Wang, and R. Calçada, “A numerical method to predict the riding comfort induced by foundation construction close to a high-speed-line bridge,” Proceedings of the Institution of Mechanical Engineers, Part F: Journal of Rail and Rapid Transit, Vol. 229, No. 5, pp. 553–564, Jan. 2014, https://doi.org/10.1177/0954409713519087
-
C. Liu, Z. Jiang, and H. Yu, “Safety analysis for bridge pier under nearby road construction and operation,” Measurement, Vol. 151, p. 107169, Feb. 2020, https://doi.org/10.1016/j.measurement.2019.107169
-
Y. Wang, S. Liang, C. Huang, and R. Wang, “Foundation settlement response of existing high-speed railway bridge induced by construction of undercrossing roads,” Sustainability, Vol. 14, No. 14, p. 8700, Jul. 2022, https://doi.org/10.3390/su14148700
-
B. Liu, Z. Yu, R. Zhang, Y. Han, Z. Wang, and S. Wang, “Effects of undercrossing tunneling on existing shield tunnels,” International Journal of Geomechanics, Vol. 21, No. 8, p. 04021, Aug. 2021, https://doi.org/10.1061/(asce)gm.1943-5622.0002102
-
Z. Yang and X. Wang, “Influence of Metro tunnel excavation on deformation of existing pedestrian underpass in Changzhou railway station platform,” IEEE Access, Vol. 8, pp. 55860–55871, Jan. 2020, https://doi.org/10.1109/access.2020.2981343
-
Z. Huang, H. Zhang, Z. Long, W. Qiu, G. Meng, and L. Zhu, “Field test optimization of shield tunnelling parameters undercrossing an existing high-speed railway tunnel: a case study,” Geotechnical and Geological Engineering, Vol. 39, No. 2, pp. 1381–1398, Sep. 2020, https://doi.org/10.1007/s10706-020-01564-3
-
M. Zhao et al., “Stability analysis of TBM tunnel undercrossing existing high-speed railway tunnel: a case study from Yangtaishan tunnel of Shenzhen metro line 6,” Advances in Civil Engineering, Vol. 2021, pp. 1–18, 2021.
-
D. Lee, “Analysis on the influence and reinforcement effect of adjacent pier structures according to the underpass construction,” Journal of the Korean GEO-environmental Society, Vol. 23, No. 4, pp. 29–39, 2022.
-
Y. Yao, B. Hong, X. Liu, G. Wang, Z. Shao, and D. Sun, “Field and numerical study of the bearing capacity of pre-stressed high-strength concrete (PHC)-pipe-pile-reinforced soft soil foundations with tie beams,” Applied Sciences, Vol. 13, No. 21, p. 11786, 2023.
-
N. Ma, “Excavation Construction’s Influence on existing bridge based on Abaqus,” Master’s Thesis, Tianjin University, Tianjin, China, 2014.
-
“Observation and evaluation specification for settlement deformation of railway engineering: Q/CR 9230-2016,” Beijing: China Railway Publishing House, China Railway, 2016.
-
“Code for design of high-speed railway: TB 10621-2014,” Bingjing: China Railway Publishing House, National Railway Administration of People’s Republic of China, 2014.
About this article
The authors have not disclosed any funding.
The datasets generated during and/or analyzed during the current study are available from the corresponding author on reasonable request.
The authors declare that they have no conflict of interest.