Abstract
This paper is dedicated to the damping identification problem. Short outlook of damping identification methods is given in the first part of the paper. All these methods can successfully identify internal damping of free-moving structures but it becomes problematically to correctly estimate damping forces when the structure is fixed and there are some joints. The recent methods of structural damping identification don’t give a full understanding of dissipation problem too. An explanation of damping-frequency relation features based on the existence of another damping nature, external damping for example, is proposed in this paper. These assumptions are demonstrated by the modal parameters identification of a turbine blade.
1. Introduction
It can be said without any doubts that the problem of structure damping identification is the one of the most vital topics in structural dynamics. Structure stiffness and inertia properties can be modelled for almost any type of structure using the finite-element method, whereas it’s really complicated problem to simulate an energy dissipation in the structure. This situation is explained by the fact that the stiffness and inertia properties of the structure are simulated with the help of continuum mechanics. It’s well-known that finite-element method based on the theory of elasticity describes mechanical systems quite well especially in case of linear formulation. In contrast to the completeness and uniqueness of the theory of elasticity, there are lot of theories that try to build a model of dissipation in the mechanical systems. There is a great variability of these models because no one among them doesn’t permit to obtain believable results for all the cases. There are linear and non-linear, viscous and non-viscous, scientific and engineering models of damping. The best models represent a compromise between the physical essential of energy dissipation and the engineering convenience of using the model. The difficulty of damping identification is that it’s always some superposition of different damping. A lot of researches are dedicated to the damping identification problem. There are plenty of damping estimation techniques which allow to obtain the coefficients of corresponding damping model from the test data. The coarse classifications of these methods are the following: time-domain and frequency domain, modal and matrix-based, stochastic and deterministic, SDOF and MDOF-based [1]. So an engineer faces a very important problem of the damping identification method appropriate choice. A great work was done in the field of damping estimation methods comparison. Although, there is a need to choose the best damping model and estimation method in each particular case. The main aim of the paper is to try to explain some features of the mechanical structure dynamic behavior with the help of structural, external damping assumption.
2. Viscous damping models outlook
The viscous linear damping models are considered in this paper. These models are the most common in the practical implementation. The motion equations of a viscously damped system vibrations may be written as:
Starting with Rayleigh [2] proportional damping, this theory has undergone many changes. Rayleigh (1877) damping is the most simple and mathematically convenient model. By Rayleigh, damping matrix should be proportional to mass or stiffness matrices, so that:
where and are real scalars. However, this theory appeared not from physical point of view but from the mathematical simplicity. It is shown in many cases that using Rayleigh damping may lead to significant errors in simulation results. Caughey and O’Kelly (1965) have shown that a damped linear system of the Eq. (1) can be described by classical eigenmodes superposition if and only if the system matrices satisfy the relationship:
Caughey [2] made very important generalization of Rayleigh damping by showing that proportional damping may be obtained by ‘Caughey series’:
Damping coefficients may be obtained as follows:
The most widespread approach would be to use a number of terms equal to the number of measured normal modes in the system. The indices are usually taken as in this case, so the problem becomes completely defined. The disadvantage of this method is in significant increasing analysis cost for evaluating matrix in case of big .
Adhikari and Woodhouse (2000) have done the recent researches in the field of proportional damping estimation [3]. They proved that if Eq. (3) is satisfied than the damping matrix in physical coordinates may be represented as follows:
Adhikari [4] has shown that function is the same function that approximately represents the modal damping in respect to the squared frequency:
Furthermore, damping matrix may be obtained with the help of fitted function ) which represents the modal damping variation with respect to the frequency as follows:
This method was proved [5, 6] on the base of some numerical simulations and laboratory case studies. The particularity of these cases was in free boundary conditions of the parts.
3. External damping identification
There is a well-known fact that the theory often fails to simulate difficult transient dynamics of real structures with some joints. The common example is a simple beam clamped by one side under the impulse loading. Otherwise, one can easily simulate the free-free beam dynamics especially using the recent Adhikari and Woodhouse method for damping estimation [6]. These observations tends to suggest the idea of external damping presence – the potential reason of the poorly simulated dynamics of fixed structures.
The external damping is usually called as boundary or structural damping. The main idea of boundary damping is that the energy loss occurs because of the friction in the joints and connections. Kundra (2009) and V. Arora (2013) have proposed a structural damping identification method and verified it on the cantilever beam case study [7, 8]. Nevertheless, some other experimental results point to the fact that structural damping is invoked not only because of joint features.
The assumption of non-boundary caused energy loss is proposed in this paper. The suggestion is that external damping in the particular part can be caused not only by the joints but also by the entire structure, to which considered part is fixed. It can be explained in such a way that mechanical energy can pass through any fixation of any part. Therefore, the energy spread in whole structure and thereby the percentage of energy, which causes the vibration in our part, is decreased. Actually, one should consider the wave propagation process to simulate this effect correctly. However, it is impossible in practical case. One of the alternative ways is to solve this problem is to fix the part through the lumped dampers, which will simulate the joint energy loss.
4. A turbine blade analysis
This situation is illustrated by the example of turbine blade modal analysis. Firstly, a free-free blade was tested (Fig. 1). Laser vibrometer was used to measure the response and the impact hammer was used to produce an impulse load. The great sample rate was used in digitization process to obtain accurate results. An experimental setup is shown in Fig. 1.
Fig. 1An experimental setup scheme
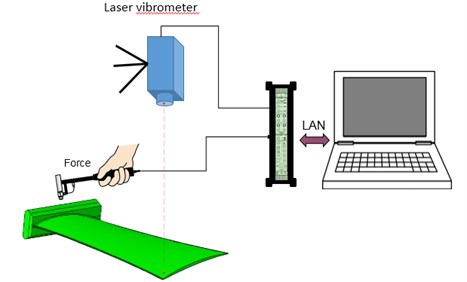
The main aim of the test was to obtain frequency-response functions during sufficient amount of impacts. Then the averaging with respect to all experiments was conducted. The modal parameters such as natural frequencies, modal damping ratios and residues were estimated with the help of well-known least-square approach in frequency domain. Firstly, a free-free blade was tested. Then the blade was fixed in special rig with very high natural frequencies and great stiffness. Then the rig itself was put on the foam rubber – a very soft material. We suppose that the rig is in free condition in this case. The fixed blade is shown in Fig. 2.
Finally, the blade fixed in the rig was mounted on the shaker table and the experience was repeated (Fig. 3). It’s worth noting that the blade fixation haven’t been changed in this process.
The FRFs obtained from all the tests were quite clear so there were no difficulties in modal parameters estimation (Fig. 3). The system has well separated poles and comparably low damping. These facts allow to assume that damping matrix is close to proportional and the eigenvectors are almost real.
Fig. 2The blade clamped in the rig
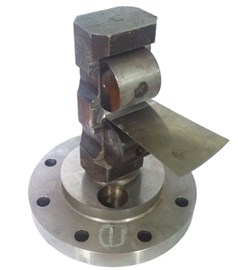
Fig. 3The test structure mounted in the shaker table
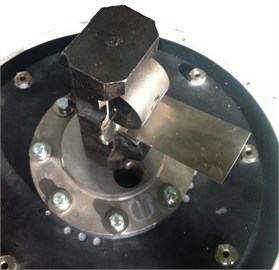
The damping-frequency dependence was built for all the tests and type of fixation. These results are shown in Fig. 5.
Fig. 4One of the FRF’s in medium frequency range
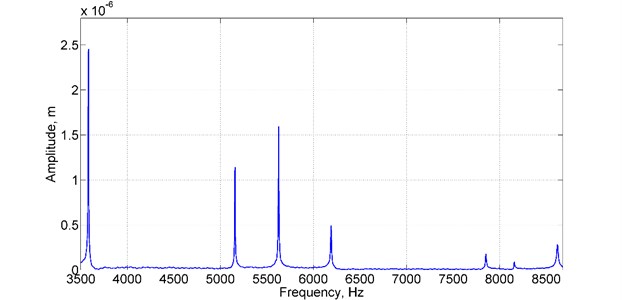
Fig. 5Damping-frequency dependence for different types of fixation
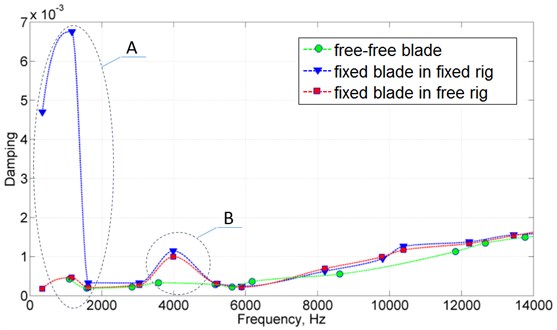
It is clearly seen from Fig. 5 that damping for fixed blade is higher than for free blade in some particular frequencies (area B). It means that at these frequencies energy can pass through the fixation easier than for other frequencies. The most important observation is that damping for the blade, fixed in rig, which is in turn mounted on the shaker table is significantly higher for low frequencies (area A) whereas it is absolutely the same for upper frequencies. This fact is an obvious evidence of external dissipation nature mentioned earlier.
5. Conclusions
In spite of many good researches in damping identification, there are still a lot of questions in this knowledge area. The main problems appear in case of fixed structures and structures with joints, the most common types of structures. The proper dissipation identification is the key to realistic simulation of complicated dynamics. The external or structural damping assumption is made in this paper. The existence of joint and material independent dissipation is proposed. The features of mechanical energy propagation can explain this assumption. These suggestions are illustrated by the example of turbine blade modal analysis. Summarizing the results one can note that damping depends not only on the part configuration and its fixation but also on the whole structure configuration. The simplest way to solve this problem is to add some lumped dampers to the FE model at the fixation area. Then these damper’s characteristics might be configured with the help of iterative updating procedure based on the experimental results [9].
References
-
Nashif A. D., Jones D. I. G., Henderson J. P. Vibration Damping. John Wiley & Sons, New York, 1985.
-
Lord Rayleigh Theory of Sound. Dover Publications, New York, 1897.
-
Caughey T. K. Classical normal modes in damped linear systems. Journal of Applied Mechanics, Vol. 27, 1960, p. 269-271.
-
Adhikari S. Damping models for structural vibration. Ph.D. thesis, University of Cambridge, 2000.
-
Phani S., Woodhouse J. Viscous damping identification in linear vibration. Journal of Sound Vibration, Vol. 303, 2007, p. 475-500.
-
Adhikari S., Woodhouse J. Identification of damping, Part 1: Viscous Damping. Journal of Sound Vibration, Vol. 243, 2000, p. 43-61.
-
Arora V., Singh S. P., Kundra T. K. Damped model updating using complex updating parameters. Journal of Sound Vibration, Vol. 320, 2009, p. 438-451.
-
Arora V. Structural damping identification method using normal FRFs. International Journal of Solids and Structures, Vol. 51, Issue 1, 2014, p. 133-143.
-
Nikolaev S., Kiselev I., Voronov S. Mechanical system finite element model refinement using experimental modal analysis. International Operational Modal Analysis Conference, Vol. 5, Guimaraes, Portugal, 2013.