Abstract
A hybrid soft computing approach is developed with the aim of identifying multiple damage in beam-type structures. This approach is formulated based on integration of two renowned soft computing methods: a wavelet transform and a singular value decomposition. The integration features the creation of a sophisticated damage indicator: mode shape’ continuous wavelet transform-singular value decomposition component (MWSC).The MWSC has inherent capabilities of immunity to noise and sensitivity to multiple damage of beam-like structures. The effectiveness of the MWSC is numerically verified by identifying multiple cracks in cantilever beams, with particular emphasis on its ability of locating multiple damages in noisy environments.
1. Introduction
Structural damage detection has gained increasing attention throughout civil, mechanical, and aerospace engineering communities [1-3]. In recent years, various damage identification methods have been developed, typically vibration-based methods, wave propagation-based methods, and the methods stemming from the interaction of multiple disciplines [4-6]. Especially, soft computing approaches have been increasingly used to detection structural damage and on this basis, soft computing-based damage identification is becoming an active research focus. The prevailing soft computing methods present in structural damage detection studies include neural networks [7, 8], wavelet transforms (WT) [9, 10], genetic algorithms [11, 12], singular value decomposition (SVD) [13-19], fuzzy logic [20-21] etc. Among the existing soft computing methods mentioned above, SVD and WT are two interesting soft computing methods. In general they are individually employed to identify structural damage, while taking on dissimilar functions of damage characterization due to the different properties of their own. However, there is literature in computer science which shows that hybridizing two or more soft computing methods can result in improved damage detection systems [22-24].
In this paper, an approach is formulated based on integration of two renowned soft computing methods: a wavelet transform and a singular value decomposition. The integration features the creation of a sophisticated damage indicator: Mode shape’ continuous Wavelet transform-Singular value decomposition Component (MWSC).
2. Damage indicator: MWSC
Let be a 1D displacement mode shape of a structural beam component. The continuous wavelet transform (CWT) of is expressed as:
where is the CWT coefficient of in space-scale domain with respect to wavelet ; and are the scale (or dilation) and space (or translation) parameters, respectively. Unlike the 1D mode shape is a 2D matrix of continuous wavelet coefficients (CWC) with the dimensions of the matrix are measured by the numbers of the discretized and in the and directions, respectively. can be analyzed by the SVD, giving as:
where , jointly indicate the data originating from the CWC field. The columns of are the left singular vectors , and the columns of are the right singular vectors . of give the singular values of . can also be expressed as the summation of its singular components:
where is the th singular component of . , defines a new damage indicator: Mode shape’ continuous Wavelet transform-Singular value decomposition Component.
3. Numerical verification
The use of the damage indicator, MWSC, to identify damage is numerically verified by an Euler-Bernoulli cantilever beam with multiple single-sided through-width transverse cracks. The finite element of a cantilever beam with double cracks is created, shown in Fig. 1. The beam has dimensions: length 500 mm, width 50 mm, height 10 mm. Elastic modulus, Poisson’s ratio, and material density are taken as 206 GPa, 0.3, and 7860 kg/m3, respectively. The depth ratio is noted as , being the crack depth and is the height of the beam cross-section. Two cracks are located at 125 mm (0.25) and 325 mm (0.65), with depths 2 mm and 3 mm, respectively.
The finite element equation of a beam segment based on the Euler-Bernoulli theory of length can be defined as [25]:
where matrices and are the elemental mass and stiffness matrices defined as:
and is the generalized element load vector. , , and are Young’s modulus, moment of inertia, cross-section area and material density, respectively. The crack is modeled as a linear rotational spring [26-29]. After application of the boundary conditions, the characteristic equation for the free vibration of the beam can be described as:
where and are the global stiffness and mass matrices. Solving Eq. (6) yields the natural frequency and denoting the obtained th-order mode shape.
Fig. 1A cantilever Euler-Bernoulli beam with double cracks
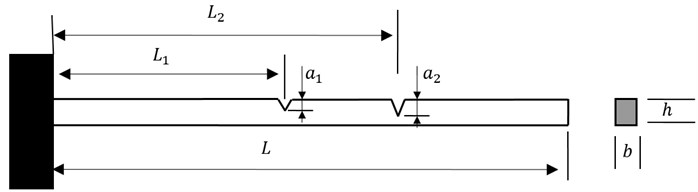
4. Damage identification
The mode shape, , (Fig. 2(a)) is arbitrarily chosen to demonstrate the capability of the MWSC to detect damage. The mode shape looks fairly smooth, from which no any damage signature can be discerned. The mode shape is processed by the CWT in terms of Eq. (1) to produce , with the result shown in Fig. 2(b). In Fig. 2(b), for appears an regular and flowing surface of the global trend of with the possible damage feature entirely overshadowed by the trend. The instance indicates that the use of CWT for damage detection may undergo a particular problem of the global fluctuating trend usually concealing the damage feature.
Fig. 2a) W, b) Wu,s, c) Wu,ssc and d) planform of Wu,ssc for the 4th mode shape
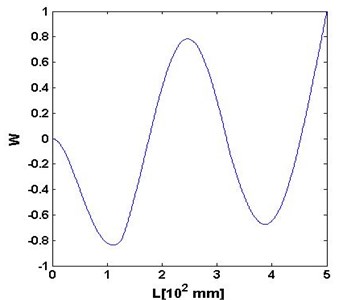
a)
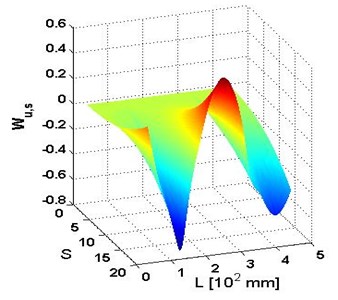
b)
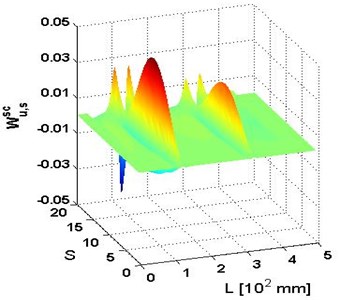
c)
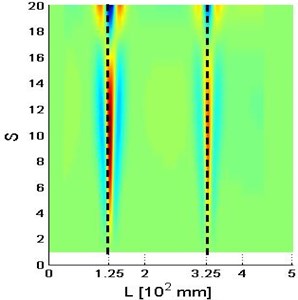
d)
Among singular components, the combination of the 2nd and 3rd singular component, , are selected to form the damage indicator, MWSC. The resulting MWSC is shown in Fig. 2(c)-(d) corresponding to the 4th mode shape. Dramatically, in the figure, bears two pronounced peaks that sharply stand out of the rest area of . These peaks purely characterize the damage information by getting rid of the global trend influence, undoubtedly designating the occurrence and location of cracks. The two vertical lines in the planform of distinctly delineate the location of the cracks at 125 mm (0.25) and 325 mm (0.65) distances, respectively. The superiorities of over to reflect damage indicates that the integration of CWT and SVD provides a valid regime of damage identification; in particular, the SVD plays a critical role of extracting damage feature.
5. Robustness against noise
The capability of damage indicator, MWSC, to identify damage in noisy environment is investigated using with added noise at various signal-to-noise ratios (SNRs). The white Gaussian noise is incorporated into the modal data by the Matlab function , where and denote noise-free and noisy data, respectively. Noises of various SNRs ranging from 60 dB to 40 dB with a step of 2.5 dB are individually added to to simulate the 4th mode shape obtained by actual measurement. Following the procedure provided in Eq. (1) and Eq. (3), the representative outcomes of are presented in Figs. 3-5 for SNRs equal to 60 dB, 50 dB, and 40 dB, respectively.
Fig. 3a) Wu,ssc and b) planform of Wu,ssc for the 4th mode shape with SNRs = 60 dB
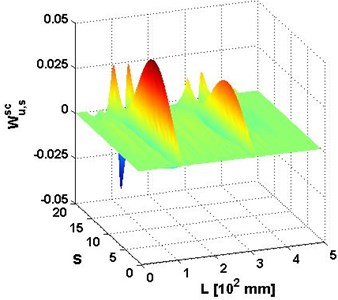
a)
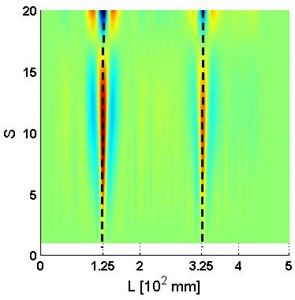
b)
Fig. 4a) Wu,ssc and b) planform of Wu,ssc for the 4th mode shape with SNRs = 50 dB
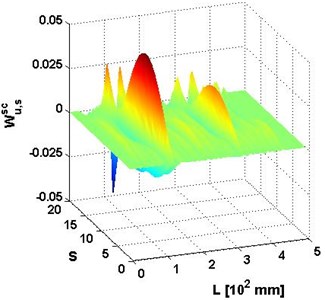
a)
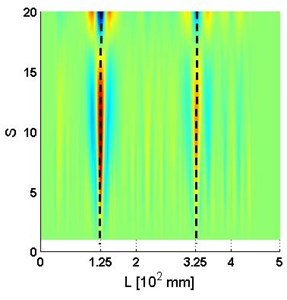
b)
In general, for the cases where the SNRs is not less than 50 dB, the identification results are similar to the result of the case without noise (Figs. 2(c)-(d)), with two sharp peaks distinctly indicating double cracks. For the case with the SNRs equal to 40 dB, the peak for the crack at 125 mm is still noticeable; however the peak for the crack at 325 mm is obscured by the noise.
Fig. 5a) Wu,ssc and b) planform of Wu,ssc for the 4th mode shape with SNRs = 40 dB
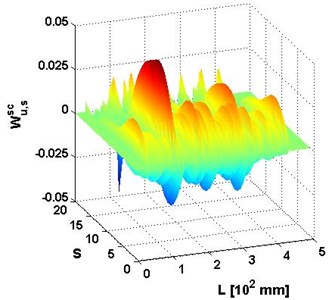
a)
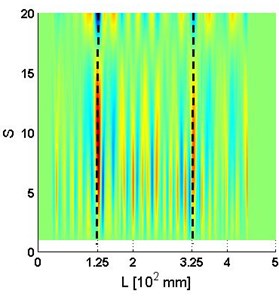
b)
6. Conclusions
In the field of structural health monitoring, identification of multiple damages is an issue of wider significance and of greater challenge compared to single damage identification. As an exploration for multiple-damage identification in beams, this study using a hybrid soft computing approach develops MWSC, assimilating the complementary merits of the SVD and WT in portraying damages in beams. The effectiveness of the MWSC is numerically verified by identifying multiple cracks in cantilever beams. Numerical results show that the MWSC features stronger immunity to noise and greater sensitivity to damage in comparison to the individually employed CWT technique.
References
-
Kopsaftopoulos F. P., Fassois S. D. Vibration based health monitoring for a lightweight truss structure: experimental assessment of several statistical time series methods. Mechanical Systems and Signal Processing, Vol. 24, Issue 7, 2010, p. 1977-1997.
-
Kulisiewicz M., Iwankiewicz R., Piesiak S. An identification technique for non-linear dynamical systems under stochastic excitations. Journal of Sound and Vibration, Vol. 200, Issue 1, 1997, p. 31-40.
-
Wang S. S., Ren Q. W., Qiao P. Z. Structural damage detection using local damage factor. Journal of Vibration and Control, Vol. 12, Issue 9, 2006, p. 955-973.
-
Semperlotti F., Wang K. W., Smith E. C. Localization of a breathing crack using nonlinear subharmonic response signals. Applied Physics Letter, Vol. 95, Issue 25, 2009, p. 254101.
-
Cheng L., Tian G. Y. Surface crack detection for carbon fiber reinforced plastic (CFRP) materials using pulsed eddy current thermography. IEEE Sensors Journal, Vol. 11, Issue 12, 2011, p. 3261-3268.
-
An Y. H., Ou J. P. Experimental and numerical studies on model updating method of damage severity identification utilizing four cost functions. Structural Control and Health Monitoring, Vol. 20, Issue 1, 2013, p. 107-120.
-
Cedric Yiu K. F. Neural network analysis for the detection of glaucomatous damage. Applied Soft Computing, Vol. 20, 2014, p. 66-69.
-
Ding Z. C., Cao M. S., Jia H. L., et al. Structural dynamics-guided hierarchical neural-networks scheme for locating and quantifying damage in beam-type structures. Journal of Vibroengineering, Vol. 16, Issue 7, 2014, p. 3595-3608.
-
Kim Hansang, Melhem Hani Damage detection of structures by wavelet analysis. Engineering Structures, Vol. 26, Issue 3, 2004, p. 347-362.
-
Hakan Gökdağ, Osman Kopmaz A new damage detection approach for beam-type structures based on the combination of continuous and discrete wavelet transforms. Journal of Sound and Vibration, Vol. 324, Issue 3, 2009, p. 1158-1180.
-
Mohsen Mehrjoo, Naser Khaji, Mohsen Ghafory-Ashtiany Application of genetic algorithm in crack detection of beam-like structures using. Applied Soft Computing, Vol. 13, Issue 2, 2013, p. 66-69.
-
Mohammad-T. V.-B., Mansour P., Morteza H. S., et al. Crack detection in beam-like structures using genetic algorithms. Applied Soft Computing, Vol. 8, Issue 2, 2008, p. 1150-1160.
-
Jiang Y., Tang B., Qin Y., et al. Feature extraction method of wind turbine based on adaptive Morlet wavelet and SVD. Renewable Energy, Vol. 36, Issue 8, 2011, p. 2146-2153.
-
Vanlanduit S., Parloo E., Cauberghe B., et al. A robust singular value decomposition for damage detection under changing operating conditions and structural uncertainties. Journal of Sound and Vibration, Vol. 284, Issue 3, 2005, p. 1033-1050.
-
Vanlanduit S., Cauberghe B., Guillaume P., et al. Reduction of large frequency response function data sets using a robust singular value decomposition. Computers and Structures, Vol. 84, Issue 12, 2006, p. 808-822.
-
Duarte H. V., Donadon L. V., Ribeiro R. P. Damage detection using robust singular value decomposition method applied to FRFs at high frequency. 22nd International Congress of Mechanical Engineering, 2013.
-
Liu C., Harley J. B., Bergés M., et al. Robust ultrasonic damage detection under complex environmental conditions using singular value decomposition. Ultrasonics, Vol. 58, 2015, p. 75-86.
-
Ruotolo R., Surace C. Using SVD to detect damage in structures with different operational conditions. Journal of Sound and Vibration, Vol. 226, Issue 3, 1999, p. 425-439.
-
Araújo I. G., Laier J. E. Operational modal analysis using SVD of power spectral density transmissibility matrices. Mechanical Systems and Signal Processing, Vol. 46 Issue 1, 2014, p. 129-145.
-
Chandrashekhar M., Ranjan Ganguli Structural damage detection using modal curvature and fuzzy logic. Structural Health Monitoring, Vol. 8, Issue 4, 2009, p. 267-282.
-
Rabinarayan Sethi, Senapati S. K., Dayal R. Parhi Structural damage detection by fuzzy logic technique. Applied Mechanics and Materials, Vol. 592, 2014, p. 1175-1179.
-
Futao Zhu, Yunjie Wu A rapid structural damage detection method using integrated ANFIS and interval modeling technique. Applied Soft Computing, Vol.25, 2014, p. 473-484.
-
Bishweswar Sahooa, Damodar Maity Damage assessment of structures using hybrid neuro-genetic algorithm. Applied Soft Computing, Vol. 7, Issue 1, 2007, p. 89-104.
-
Beena P., Ranjan Ganguli Structural damage detection using fuzzy cognitive maps and Hebbian learning. Applied Soft Computing, Vol. 11, Issue 1, 2011, p. 1014-1020.
-
Jinhee Lee Identification of multiple cracks in a beam using natural frequencies. Journal of Sound and Vibration, Vol. 320, Issue 3, 2009, p. 482-490.
-
Ostachowicz W. M., Krawczuk M. Analysis of the effect of cracks on the natural frequencies of a cantilever beam. Journal of Sound and Vibration, Vol. 150, Issue 2, 1991, p. 191-201.
-
Behzad M., Ebrahimi A., Meghdari A. A new continuous model for flexural vibration analysis of a cracked beam. Polish Maritime Research, Vol. 15, Issue 2, 2008, p. 32-39.
-
Cao M. S., Ye L., Zhou L. M., Su Z. Q. Sensitivity of fundamental mode shape and static deflection for damage identification in cantilever beams. Mechanical Systems and Signal Processing, Vol. 25, Issue 2, 2011, p. 630-643.
-
Paipetis S. A., Dimarogonas A. D. Identification of crack location and magnitude in cantilever beam from the vibration modes. Journal of Sound and Vibration, Vol. 138, Issue 3, 1990, p. 381-388.
About this article
The authors are grateful for the partial support provided by the Natural Science Foundations of China (No. 11172091), Qing Lan Project, and the Fundamental Research Funds for the Central Universities (Grant Nos. 2014B03914 and 2012B05814).