Abstract
In this study, measures were taken to eliminate the negative effects of mechanical vibrations of a multicylinder internal combustion engine by reducing the amplitude of selected components of the frequency spectrum of momentary velocity of the engine crankshaft. For this purpose, experimental tests were carried out combustion piston engine, which was not originally equipped with a torsional vibration damper. On the basis of theoretical calculations were prepared three versions of hyper viscous torsional vibration dampers. Then were conducted experimental studies of engine built into the vehicle in which the engine had to be operated. For the measurement of momentary angular velocity of the crankshaft uses a laser vibrometer Polytec RLV-5500. The studies confirmed the usefulness prepared torsional vibration dampers to reduce selected components of the frequency spectrum of the signal instantaneous changes in the angular velocity of the crankshaft.
1. Introduction
Drive systems for vehicles and machines are made from internal combustion engines, transmissions, clutches, cardan shafts etc. are a source of mechanical vibrations. Causes of vibration may be generally divided into:
• caused by processes and phenomena associated with the work piece driveline: fuel combustion in the cylinder [1], parametric meshing stiffness transition occurring during meshing pairs of teeth [2], matched coupling stiffness without the required dynamic analysis [3], etc.
• due to out of tolerance of execution propulsion components and improper cooperation kinematic pairs [4-6].
The first reason is tried to be reduced by the use of various types of dampers [7-9] and wheels dual mass [10]. Other reason for trying to limit by narrowing of the tolerance of components and the use of modern methods of numerical analysis in order to obtain the most advantageous cooperation kinematic pairs [4-6]. The vibrations generated by the drive systems in addition to being a negative phenomenon can also be used as a utilitarian status information causing them to the object [11]. This paper attempts to eliminate the negative aspects of mechanical vibrations of a multi-cylinder internal combustion engine by reducing the amplitude of selected components of the frequency spectrum of momentary velocity of the engine crankshaft. This was achieved through the use of hyper viscous torsional vibration dampers.
2. Experimental research
Multi-cylinder piston internal combustion engine with complete accessories being the object of reducing vibration during testing was built in one of the vehicles, which ultimately had to be operated. In the original version the motor is not equipped with a torsional vibration damper of the crankshaft. On the basis of theoretical calculations [12] chosen three viscous dampers, which was mounted at the end of the crankshaft opposite to that on which is mounted the clutch.
Fig. 1Frequency spectrum of signal momentary changes of speed of vibration of the crankshaft received when operation of the test engine crankshaft rotational speed of 2000 rpm: original type of engine with: a) torsional vibration damper, b) engine mounted with a torsional vibration damper A, c) engine mounted with a torsional vibration damper B, d) engine mounted with a torsional vibration damper C
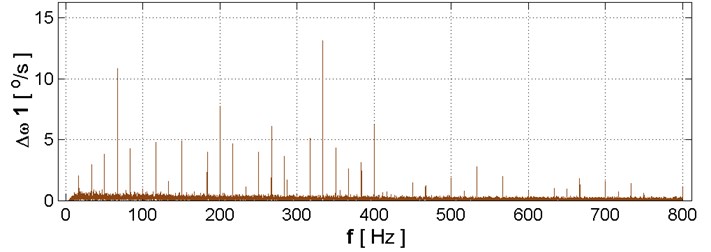
a)

b)
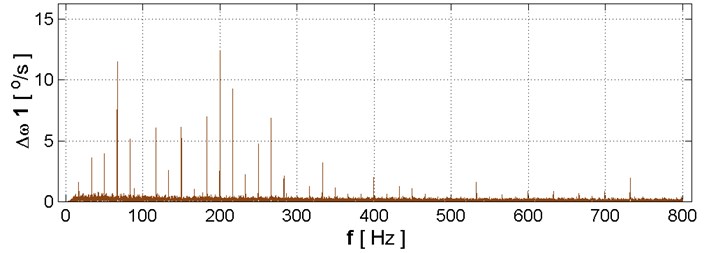
c)
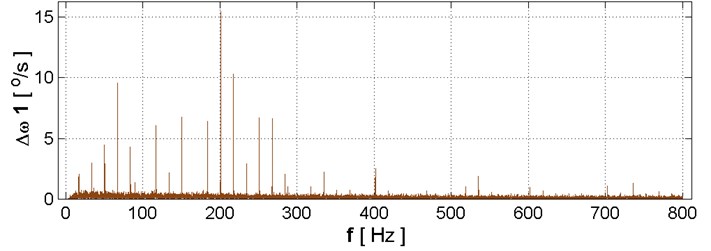
d)
Using a laser vibrometer RLV-5500, the company Polytec was measured angular velocity of the crankshaft of engine, even at the end where a selected torsional damper was fastened. The research was conducted with the engine roperation with different speeds and therefore also recorded signal coming from the crankshaft position sensor which original is an equipment of engine. Recorded signals sampled at a frequency of 51.2 kHz. In the case of engine tests equipped with a selected torsional vibration dampers temperature was taken. Since vibration signals is Carried out only after reaching the saturation temperature of the silencer. During the study also maintained the coolant temperature at a constant level.
3. Results
Fig. 1 shows the frequency spectrum of momentary velocity of the crankshaft of the internal combustion engine piston tested when operating with the rotational speed of 2,000 rpm. When the engine operates without torsional vibration damper have a dominant amplitude spectrum components corresponding crankshaft rotational frequency of 33.33 Hz and its harmonics and subharmonic. The range to 400 Hz and they have a significantly higher amplitude than the above-mentioned frequency (Fig. 1(a)). When operating the engine with dampers viscous designed according to and mounted on the end of the crankshaft opposite to that on which is fixed the coupling also the dominant amplitude from a spectrum components corresponding to a given rotational frequency of the crankshaft and its harmonic and subharmonic but ranging up to 300 Hz. By use of viscous dampers, therefore, caused a significant reduction of harmonic amplitudes rotational frequency of a signal instantaneous changes in the angular velocity of the crankshaft in the range of 300 to 400 Hz (Fig. 1(b)-(d)).
4. Conclusions
This study, measures were taken to eliminate the negative effects of mechanical vibrations of a multicylinder internal combustion engine by reducing the amplitude of selected components of the frequency spectrum of instantaneous changes in the angular velocity of the crankshaft. For this purpose, experimental tests were carried out combustion piston engine, which was not originally equipped with a torsional vibration damper. The studies confirmed the usefulness prepared on the basis of theoretical calculations torsional vibration dampers to reduce selected components of the frequency spectrum for instantaneous changes in the angular velocity of the crankshaft. Use the viscous dampers resulted in a significant reduction of harmonic amplitudes rotational frequency of a signal instantaneous changes in the angular velocity of the crankshaft in the range of 300 to 400 Hz.
References
-
Brun R. High-Speed Diesel Engines. WKiŁ, 1973.
-
Wilk A., Madej H., Łazarz B. Vibration Activity of Gear Transmissions. Biblioteka Problemów Eksploatacji, WNTITE – PIB, 2009.
-
Homišin J., Urbanský M. Partial results of extremal control of mobile mechanical system. Diagnostyka, Vol. 16, Issue 1, 2015, p. 35-39.
-
Dziubek T. The determination of accuracy of testing gear wheel for aeronautical dual-power path gear after heat treatment. Diagnostyka, Vol. 16, Issue 2, 2015, p. 61-66.
-
Marciniec A., Budzik G., Dziubek T., Sobolewski B., Zaborniak M. Determine the precision of aviation bevel gear, made by the selected incremental techniques and using an optical scanner Atos II Triple scan. Diagnostyka, Vol. 16, Issue 1, 2015, p. 63-67.
-
Pisula J. A mathematical model for designing tooth surfaces in spiral bevel gears and gear meshing analysis. Diagnostyka, Vol. 16, Issue 1, 2015, p. 57-62.
-
Homik W. Torsional vibrations of the crankshaft of the engine without the damper and with viscous torsional damper. Przegląd Mechanicznym, Vol. 9, 2008, p. 43-46.
-
Homik W. Damping of torsional vibrations oh ship engine crankshafts – general selection methods of viscous vibration damper. Polish Maritime Research, Vol. 3, 2011, p. 43-47.
-
Homik W., Zygmuntowicz J. Rules for selection of the viscous torsional vibration damper in a stationary diesel engine generator set AC. Symposium PKM Gdańsk, Fundamentals of Machine Design – Trends in Research and Development, Vol. 1, 2011, p. 154-162.
-
Baran P., Grega R. Comparison of dynamic properties of dual mass flywheel. Diagnostyka, Vol. 16, Issue 1, 2015, p. 29-33.
-
Grządziela A. Diagnosing of naval gas turbine rotors with use of vibroacoustic parameters. Polish Maritime Research, Vol. 3, 2000, p. 14-17.
-
Homik W. Broadbands torsional vibration dampers. Biblioteka Problemów Eksploatacji, WNTITE-PIB, 2012.