Abstract
Internal combustion engines are made of many moving components that are subjected to high inertia and combustion loads. Crankshaft bearing and piston-cylinder walls work under hydrodynamic lubrication conditions. Any failure at those bearing may cause severe damage on the engine. Acceleration measurement on the cylinder block and cylinder was effectively used for early detection of failure in hydrodynamic lubrication. Inspection of the crankshaft and piston components after the test clearly shows that metal-to-metal contact occurred during the test and real-time acceleration signal analysis can help to early detection of the problem.
1. Introduction
Internal combustion engine operating conditions monitoring is an important topic especially when developing a new engine and conducting performance development tests with prototype. There are many moving parts at high speed and accelerations and the limits of bearings and joints should stand the inertia and combustion forces. There is always a pressure to maximize the performance of the engines and designers use the limits of the components. Hence, many components are at the limit of overheating, and many bearings and joints are used at the limit of their loading capacity. Cooling and lubricating systems are also used at their limits while transferring the heat energy and satisfying required oil pressure.
Prototypes built for engine development tests have many temperature, pressure, flow sensors placed at the critical locations to control the performance and operating limits of the components. Many strain and acceleration measurements are also performed during durability and vibration tests to check if the design satisfy the limits. Acceleration and acoustic emission measured during the durability tests are also used to understand the damage and/or wear of components. This approach is a topic of structural health monitoring (SHM) and it is widely used because of its ease of application and benefits of early detection of damage to understand the root causes and damage mechanism.
SHM is a multi-disciplinary approach utilizing the methods presented in structural dynamics, non-destructive evaluation, signal processing, detection theory, machine learning, probability and statistics, and sensor networks courses [1]. Its application is common for high performance mechanical systems like in aerospace industry where lightweight and damage tolerant designs have to be applied to achieve the targets. It is also important to apply it to highly invested and long lasting structures like bridges, offshore oil platforms, buildings and power generation systems to be able to prevent catastrophic failures by early fault or damage detecting.
There have been many fault detection studies for internal combustion engines in literature. Kimmich and Isermann [2] presented a model based fault detection study for the injection, combustion and engine transmission of diesel engines. They stated that most of the available on-board diagnosis systems are mainly based on simple threshold supervision or plausibility checks of measured signals as well as on signal based methods like the frequency analysis of the engine speed signal. This approach is not adequate for complex machinery systems like internal combustion engines. In order to improve the fault detection mythology, they proposed a model based fault detection method where analytical process information in form of mathematical process models is used to evaluate information of different sensors. This allows more specific information on the fault characteristics. Kimmich et al. [3] further developed their modal based fault detection approach for intake system, injection system with the combustion and exhaust system. They used semi physical models, identification with local linear neural networks, signal models and filters to estimate the difference between normal and faulty states of operation. They tested that their approach is successful in the real time operation suing test benches. Clever and Isermann [4] developed a method to locate faults in multivariable systems using such input excitation and its application to the intake air system of a modern common rail diesel engine. They have applied successfully to differentiate air mass sensor faults from other process faults.
Khelil et al. [5] proposed a methodology using neural network to monitor the engine health and to diagnose the faults. The neural network learning step is enhanced by a selection of its inputs using a correlation study and heuristic information. They validated their model upon real data corresponding to real faulty situations. They successfully developed the residual and threshold generation steps and they showed that their results show a good compromise between sensitivity to faults and robustness to false alarms.
Oskoueian and Nuawi [6] proposed a method to detect the wear of engine block using strain gage measurement and processing it by applying statistical analysis techniques. They analyzed kurtosis of the strain signal for different frequency ranges separately.
Jena and Panigrahi [7] presented an approach to detect the motor bike piston-bore fault identification from engine noise signature analysis. They developed a robust filtering algorithm and a statistical learning based decision making system using engine noise signature of healthy and defective vehicles. They found that PSD spectrum of the acoustic signal does not point out presence of the defect precisely. The continuous wavelet transform using bi-orthogonal wavelet is shown to be working satisfactorily, but not up to the expectation, for identifying piston-bore defect in two wheelers. Complex Morlet wavelet is found to be the most appropriate wavelet for characterizing acoustic signal burst due to piston-bore defect and frequencies associated with it. The acoustic signal burst due to such defects carry frequency components from about 100 to 300 Hz. Statistical learning mechanisms such as artificial neural network and support vector machine are designed for defect classification. The feed-forward back-propagation neural network is shown to be able to classify the healthy and defective vehicles with an average of 99.98 % and 98.11 % success rates, respectively.
Wu et al. [8] presented a signal processing technique to normalize and separate the source of non-linear acoustic emission signals of a multi-cylinder diesel engine for condition monitoring applications and fault detection. They showed that the source separation algorithm is able to separate the signal interference of adjacent cylinders from the monitored cylinder once the wave attenuation constant and the arrival time delay along the propagation path are known. They used four resonant type acoustic emission sensors mounted on the cylinder head. They are pre-amplified before being recorded by data acquisition system with 1 MHz sampling frequency. They found that their approach is especially useful in the application of technique for condition monitoring of small-size diesel engines where signal interference from the neighboring cylinders is strong.
Chen et al. [9] developed a diagnostic system to detect piston slap faults in internal combustion engines. They employed artificial neural networks by training of the network by a large amount of data in various engine conditions (different speed/load conditions in normal condition, and with different locations/levels of faults). They proposed three-stage network systems to identify piston faults, fault localization and fault severity. Multi-layer perceptron networks were used in the detection stage and severity/prognosis stage. Probabilistic neural network was used to identify the cylinder where fault occurred. They validated their approach by real tests.
Dayong et al. [10] performed a study to extract fault components from abnormal acoustic signals and automatically diagnosing diesel engine fault. They proposed a new dislocation superimposed method to improve the random decrement technique and searching for the starting point method to extract the fault component from abnormal acoustic signals. They found that their approach is better than the traditional signal analysis method on vibration and acoustic signal.
Flett and Bone [11] developed a fault detection and diagnosis system for detecting deformed valve spring faults and abnormal valve clearance faults using accelerometer signal. Among various classification methods implemented, the Naïve-Bayes classification method produced the best overall performance, with a lowest detection accuracy of 99.95 %.
Moosavian et al. [12] proposed a method to identify piston scuffing fault by acceleration measurements. They analyzed the vibration signal in time-domain, frequency-domain and time-frequency domain. They used continuous wavelet transform to obtain time-frequency representations. They showed that piston scuffing fault excited the frequency band of 2.4-4.7 kHz in which the frequency of 3.7 kHz was affected more. Seven different features were extracted from the engine vibration signals related to the frequency band of 2.4-4.7 kHz. The results indicated that maximum, mean, RMS, skewness, kurtosis and impulse factor of the engine vibration related to the found frequency band increased significantly due to piston scuffing fault. The obtained results showed that the proposed method identified piston scuffing fault and discovered the vibration characteristics of this fault like frequency band.
The aim of the study is to present the bearing and piston faults occurring in an internal combustion engine by processing the acceleration signal. For this purpose, an internal combustion engine was instrumented and was tested under controlled conditions. Then the acceleration signal was processed in time and frequency domains. Inspection of faulty parts revealed that the vibration signal can be used successfully to detect bearing and piston faults in an internal combustion engine.
2. Fault detection
In order to test the efficiency of acceleration measurement from cylinder block and cylinder head to detect early fault of bearings, an I4 diesel was instrumented by 3 accelerometers. A data acquisition system (Reilhofer Delta Analyser v2) was utilized to record and to process the signal (Fig. 1). The locations of sensors are shown in Fig. 2.
Fig. 1Test setup scheme
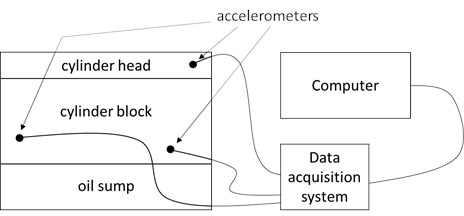
Fig. 2Accelerometers placed on the engine block
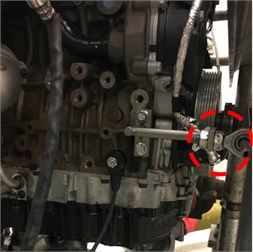
a)
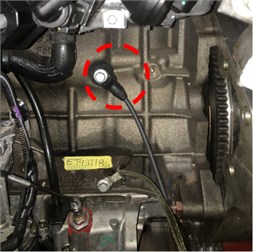
b)
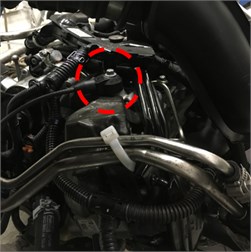
c)
Failure of crankshaft and piston bearings may cause severe damage on the engine. Typical causes of failure in hydrodynamic bearing of crankshaft journals are as follows
• problem in supplying oil pressure,
• problem in oil quality,
• overheating of oil,
• high inertia and combustion forces,
• foreign particles.
Internal combustion engines have temperature and pressure sensors to control the proper functioning of lubrication system. However, those sensors are usually placed far from the crankshaft and piston, and a local failure in one of the bearings may not be detected immediately. Bearing surfaces may start to damage before any temperature change detected. A damaged bearing may not function properly once it is slightly damaged even though the conditions that caused its failure does not exist anymore.
In order to trigger bearing damage, the following test scenario was applied. First, acceleration measurements were taken to specify the limits of the normal operation. Then the oil quantity decreased by one third so that there will not be enough oil pressure on the hydrodynamic bearings and metal-to-metal contact will occur. Engine speed, torque, oil temperature and oil pressure curves are plotted in Fig. 3. The oil temperature rises from 800 °C to 1550 °C at around 300 seconds.
Fig. 3Engine operation parameters in time domain
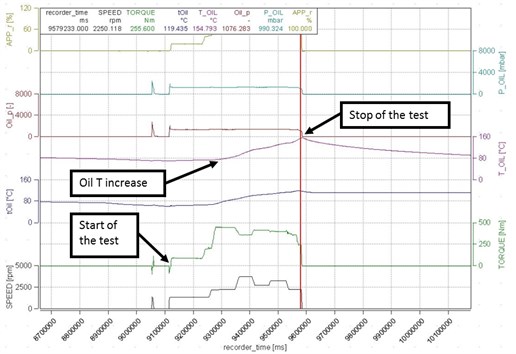
Fig. 4Normal operation acceleration (green) and faulty operation acceleration (red) in frequency domain
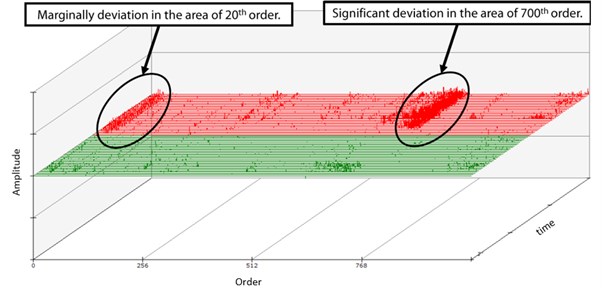
When the acceleration signal was processed to obtain the vibration amplitude change with respect to engine order, as it is seen in Fig. 4, there is a significant change between the normal conditions (green curves) and faulty condition (red condition) for vibration amplitude around 20th and 700th engine orders. This variation in acceleration amplitude at high frequency is a sign for metal-to-metal contact in bearings and/or piston-cylinder wall.
3. Inspection of damaged parts
After the completion of the test where damage on the bearing and piton-cylinder walls have occurred, the engine was disassembled for inspecting the damage on the components. As seen in Figs. 5-8, there are evidences of metal-to-metal contact on the crankshaft bearings and piston-cylinder walls.
Fig. 5Bearing scuff on the Conrod journal
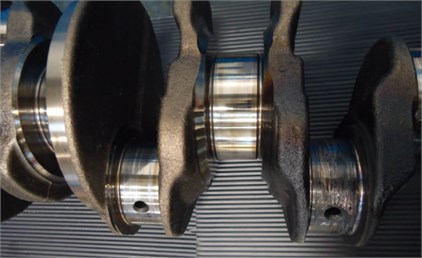
Fig. 6Scratch on the main bearing
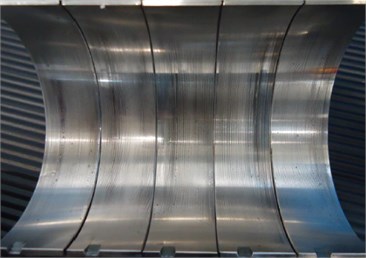
Fig. 7Piston scuff
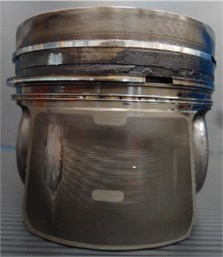
Fig. 8Cylinder bore scuff
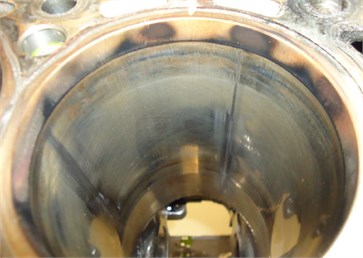
4. Conclusions
I4 diesel engine was tested to investigate the metal-to-metal contact in crankshaft bearings and piston-cylinder wall contact. Under normal operating conditions, hydrodynamic lubrication enables smooth operation of moving components subjected to inertia and combustion loads. The oil in the lubrication system was decreased by one third to simulate oil supply problem on the bearings. Acceleration measurement and analysis of the signal with respect to the engine order clearly detects the problem on the bearings and piston-cylinder walls. It is shown that vibration measurement can effectively be use for early detection of faults on the bearings.
References
-
Farrar Charles R., Worden Keith Structural Health Monitoring. John Wiley and Sons, Ltd., 2013.
-
Kimmich Frank, Isermann Rolf Model based fault detectıon for the injection, combustion and engine-transmission. 15th Triennial World Congress, Barcelona, 2002.
-
Kimmich Frank, Schwarte Anselm, Isermann Rolf Fault detection for modern Diesel engines using signal- and process model-based methods. Control Engineering Practice, Vol. 13, 2005, p. 189-203.
-
Clever Sebastian, Isermann Rolf Model-based fault detection and diagnosis with special input excitation applied to a modern diesel engine. 17th World Congress the International Federation of Automatic Control Seoul, Korea, 2008.
-
Khelil Y., Graton G., Djeziri M., Ouladsine M., Outbib R. Fault detection and isolation in marine diesel engines: a generic methodology. 8th IFAC Symposium on Fault Detection, Supervision and Safety of Technical Processes, Mexico City, 2012.
-
Oskoueian Arshin, Nuawi Mohd Zaki Internal combustion engine monitoring using strain gauge and analyzing with I-Kaz. 2nd International Conference on Mechanical, Industrial, and Manufacturing Engineering, IERI Procedia, Vol. 1, 2012, p. 192-198.
-
Jena D. P., Panigrahi S. N. Motor bike piston-bore fault identification from engine noise signature analysis. Applied Acoustics, Vol. 76, 2014, p. 35-47.
-
Wu Weiliang, Lin Tian Ran, Tan Andy C. C. Normalization and source separation of acoustic emission signals for condition monitoring and fault detection of multi-cylinder diesel engines. Mechanical Systems and Signal Processing, Vols. 64-65, 2015, p. 479-497.
-
Chen Jian, Randall Robert Bond, Peeters Bart Advanced diagnostic system for piston slap faults in IC engines, based on the non-stationary characteristics of the vibration signals. Mechanical Systems and Signal Processing, Vol. 75, 2016, p. 434-454.
-
Ning Dayong, Sun Changle, Gong Yongjun, Zhang Zengmeng, Hou Jiaoyi Extraction of fault component from abnormal sound in diesel engines using acoustic signals. Mechanical Systems and Signal Processing, Vol. 75, 2016, p. 544-555.
-
Flett Justin, Bone Gary M. Fault detection and diagnosis of diesel engine valve trains. Mechanical Systems and Signal Processing, Vols. 72-73, 2016, p. 316-327.
-
Moosavian Ashkan, Najafi G., Ghobadian Barat, Mirsalim Mostafa, Jafari Seyed Mohammad, Sharghi Peyman Piston scuffing fault and its identification in an IC engine by vibration analysis. Applied Acoustics, Vol. 102, 2016, p. 40-48.
-
Reilhofer Delta Analyzer Specifications. www.rhf.de
About this article
Authors would like to thank Ford Otomotiv Sanayi A.S. Powertrain Engineering Design Validation Team for their helps in conducting the bench tests and Çınar Kurra from dBKES Mühendislik Ltd. Şti. for his helps in providing the data acquisition equipment.