Abstract
The current trend, with regards to the cost and energy savings, is to combine properties of basic materials and try to obtain so called synergic effect with that we could get significant amplification of their individual properties. The aim of this article is to assess whether this required improvement of the physical properties occurs also for fiber-reinforced construction materials, whose study has been the author work devoted for a long time. This work is focused on assessment of changes in the acoustic attenuation of the basic plaster composites with addition of some high strength fiber reinforcement. The chosen plasters materials are commonly used in building constructions (gypsum, lime-cement, cement). Into those materials that in our case has become the matrix, some basalt and glass fiber dispersion of length 8.5 and 12 mm have been added. An impedance tube was used to the test of materials acoustic absorption. The results show the very good acoustic absorption for all of the tested samples regardless on the ratio of used reinforcement.
1. Introduction
Many medical researches prove that a long term or a high level of noise has a considerably negative impact on the human body. The consequences of long-term and frequent exposure to noise affect not only the mental state (like e.g. tiredness or ability to concentrate) but also the overall health of the human being and could cause some irreversible harm. For this reason, it is necessary to protect the human organism by minimisation of the noise level [1, 2]. In recent years, people's interest in solving the situation has increased, especially in cities where noise concentrations are higher because of extremely high traffic and industry development. Problems associated with noise in such environment are constantly increasing and therefore people require somehow protect their homes or working places [3]. For this reason, it is necessary to take care about the selection of materials with improved sound insulation just during the construction of building. The ability of building materials to absorb sound waves usually depends on their stiffness, density and porosity [4-6].
The commonly used construction materials (fired and silicate bricks, bricks, concrete, aerated concrete, steel reinforced concrete, glass wool, polystyrene) have known and already explored generally mechanical and thermal insulation properties. However, production of these materials has a negative impact on the environment [7, 8]. For this reason, in last years has been observed the increased efforts to use materials that could reduce the negative impact on environment. Such materials include often some classic natural materials like len, hemp, wood, straw, reeds and some others. The flax and hemp fibers are often used to insulating the buildings. Wood can be used on walls and wood sawdust can be used as a filler for concrete. The combination of straw with clay can be found as a wall paneling and reeds are used as a roof covers [9].
Mostly often are the fibers added to materials in order to improve mechanical properties such as the bending, tensile, compressive and impact strength. Although using of the reinforcing fibers for fragile building materials has been known since the ancient times, this concept came to the fore again in the 1940’s. Plant and viscose fibers have been tested as a potential replacement for asbestos fibers [10]. In the previous studies [11] has been found that with using the correct mass of fibers (1 % to 2 % of reinforcement) there is a significant improvement in the main mechanical properties of plaster composites. As a reinforcing element, the glass and basalt fibers were used in the most commonly applied types of plasters. In the cement composites the same effect could be reached with reinforcing by cellulose fibers [12, 13]. Lately some of works started to mention suitability of these composites also for the anti-noise purposes [14]. Neithalath and Weiss examined the influence of some morphological changes in cellulosic fibers in the point of view on the acoustic and mechanical properties of cello-cement composites. From their results, it is obvious that the increasing volume of fibers proportionally increases also the acoustic absorption [15].
As has been already mentioned, the ability to absorb sound depends mainly on porosity. Pores occur in different scales (micropores, interparticular pores, mesopores). The cannabis-lime composites are characterised by a really high porosity ranging from 70 % to 80 % [16]. Gle, Gourdan and Arnaud [17] have conducted an extensive research of the acoustic benefits obtained by using cannabis composites. This work shows that the level of sound absorption in the hemp reinforced concrete could be controlled and significantly increased by using of suitable components and the specified manufacturing processes.
This work is focused on the sound attenuation characteristics in plaster composites. Three commonly used plasters (gypsum, lime-cement, cement) were reinforced with glass and basalt fibers and measured in the impedance tube.
2. Material and methods
Three commonly used plasters (gypsum, lime-cement, cement) were reinforced with glass and basalt fibers. The plasters were chosen purposefully due to their generally declared properties. The assumption was that the best acoustic results will be achieved by the Thermo UM Xtra thermos-insulating plaster and the least suitable would be the cement plaster. The gypsum plaster has been chosen just as a complementary sample.
Into the thermal insulation plaster the basalt fibers with length of 7.7 mm and a diameter of 13 μm were added. With the gypsum plaster the akaline-resistant 12 mm long glass fibers with a diameter 14 μm were mixed. The cement plaster was for the first study tested without an additional fiber mixture.
2.1. Plaster
The plaster is formed after hardening of the mortar mixture, which is composed of filler, binder and some special additives. The type of used binder is the main criterion, according to which the plasters are divided. The binder ensures good adhesion to the masonry, the strength of the plaster itself and durability to withstand arising impacts from the environment.
The heat insulation plaster ThermoUM Xtra has a low modulus of elasticity and low density. Thanks to these properties, the plaster can eliminate some volumetric changes in the main building material and thus way prevent creatiation of visible cracks in the top ply. This type of plaster is approximately 4 times lighter than another commonly used, it has a high value of thermal conductivity and is hydrophobic (it means protects the facade against long-term influences of rain) [18].
The gypsum plaster is vapor-permeable and unlike the application of glue with perlin, does not close water in structure and allows the natural drying of residual water which positively affects the microclimate in a room. At a high temperatures, the gypsum releases water vapor that could increase the fire resistance [19].
The cement plaster is designed for higher load areas, has increased strength, water resistance, adhesion on the substrate is frost and weather-resistant [20].
2.2. Used fibers
Basalt is a designation for group of rock materials that consist of a number of oxides (Table 1). This rock is made up of different species like pyroxene, magnetite, olivine and plagioclase [21]. The basic technological condition for the selection of basalt that is suitable for fiber production is the acidity factor , which is defined by the relation Eq. (1):
The value of the acidity factor must be in the range of 1.1 to 3. When the most appropriate technological conditions for fiber production are for 1.65. The choice of basalt rocks for fiber production is affected not only by the chemical and mineralogical composition but also by the rock texture [22]. The resulting quality of fibers is influenced by the level of technological equipment and the whole technological process of production.
Compared to the glass, the basal fibers are more stable in a strongly alkaline environment, but on the contrary in a strongly acidic environment is their stability lower [24]. The basalt is non-flammable, has strong damping capabilities against penetrating of flames [3] and is a very good thermal insulator.
The base of glass fibers is made of tetrahedrons (SiO4)4- and contains different types of oxides. The individual types of glass fibers could be distributed by their content of oxides – according to Table 2. For the production of fibers could be used not only the glass stones but also various processed glass metaproducts like glass beads, rods, frits or waste glass shards). The composition of the base glass significantly affects the resulting fiber properties [25]. Just after spinning, the glass fibers are most sensitive to moisture absorption. In some surface defects of the fiber, this moisture acts as a surfactant which results in their reduced fracture energy. The advantage of glass fibers is their high tensile strength and quite low costs, which allows their application in modern composite materials [26].
Nowadays, there are various products like chopped fibers, grids, steel truss, rovings for pipes, veils, etc., that could improve the properties of building materials (Fig. 1) [27, 28].
Table 1Composition of basalt fibers [23]
Constituent | Content [%] |
SiO2 | 42-56 |
Al3O3 | 11-18 |
Fe2O3 | 5-12 |
CaO | 7,5-13 |
MgO | 4-11 |
Na2O | Méně než 5 |
TiO2 | Méně než 5 |
K2O | Méně než 5 |
Table 2The content of oxides for individual types of fibers
Oxides | A-glass [%] | C-glass [%] | E-glass [%] | D-glass [%] | R-glass [%] | ECR-glass [%] |
SiO2 | 63-72 | 64-68 | 52-56 | 72-75 | 55-65 | 54-62 |
Al2O3 | 0-6 | 3-5 | 12-16 | 0-1 | 15-30 | 9-15 |
B2O3 | 0-6 | 4-6 | 5-10 | 21-24 | 0 | 0 |
CaO | 6-10 | 11-15 | 16-25 | 0-1 | 9-25 | 17-25 |
MgO | 0-4 | 2-4 | 0-5 | 0 | 3-8 | 0-4 |
Na2O + K2O | 14-16 | 7-10 | 0-2 | 0-4 | 0-1 | 0-2 |
Another oxides | 0-1 | 0-1 | 0-1 | 0-1 | 0-1 | 0-1 |
2.3. Preparation of samples and testing
The content of the fibrous reinforcement in concrete materials is usually 6 %. Blending the plaster and fibers with thus high content could cause some problems in their bonding. The content of fibrous reinforcement for this experiment was 1 % (Fig. 2). The reason is the optimal improvement of mechanical properties as has been demonstrated in the previous study where the glass and the basalt filaments with a weight ratio of 1 %, 2 % and 3 % were used as the reinforcing elements [11]. The calculation of the mixing ratio Eq. (2) is based on the percentage of the components in the composite [31] and their densities:
where: [%] is the mass fraction of the th component, [%] the volume fraction of the th component and [kg/m3] is the density of the th component.
Fig. 1Some of fibrous materials commercially used to improve the mechanical and acoustic properties of building materials [29, 23]
![Some of fibrous materials commercially used to improve the mechanical and acoustic properties of building materials [29, 23]](https://static-01.extrica.com/articles/18567/18567-img1.jpg)
![Some of fibrous materials commercially used to improve the mechanical and acoustic properties of building materials [29, 23]](https://static-01.extrica.com/articles/18567/18567-img2.jpg)
![Some of fibrous materials commercially used to improve the mechanical and acoustic properties of building materials [29, 23]](https://static-01.extrica.com/articles/18567/18567-img3.jpg)
Fig. 2The tested plaster a) without b) with the fiber reinforcement
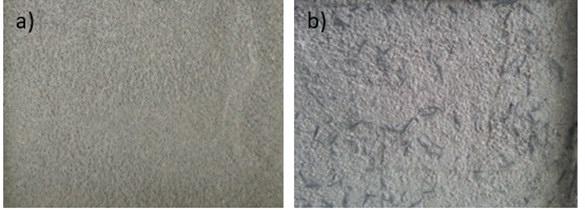
2.4. Acoustic properties
Sound is characterized as any mechanical waves in the environment that are capable of producing the hearing sensation in the human ears. It is spread in the form of sound waves through gases (air), liquids and solids. In each of different medium, the sound waves spreads in a different way. The greater the particles vibrate within the medium, the more energy passes through it. The sound is the vibration of the elastic medium particles in the range of audible frequencies (20 Hz-20 kHz). A specific form of sound is noise. Physically it can be described as very loud, irregular or random oscillation.
Table 3Typical values of coefficient for the commonly used materials [32]
Material | Sound absorption co-efficient |
Concrete | 0,02-0,06 |
Unpainted blockwork | 0,02-0,05 |
Hardwood | 0,03 |
The subjective perception of the noise is influenced by a number of factors such as age, duration, health or attitude of the listener or the pertinental content of information. When considering noise in a structure the subjective noise perception must be taken into account, particularly in an urban environment [32]. The level of air absorption can be expressed by the absorption coefficient. Extremely dense material that reflects 100 % of sound has an absorption coefficient equal to 0 [33]. The values of the absorption coefficients for building materials are given in Table 3. The acoustic absorption of plasters at frequency 1 000 Hz is 0.02-0.05. Basalt fiber layers move around 0.2 and the glass layer around 0.1.
3. Experiment
For testing the acoustic absorption it is necessary to create the samples with a precise cylindrical profile in a way to fit them accurately into the clamping part of the impedance tube (Fig. 3). Samples with a thickness of 10 mm and a diameter of 99.8 mm were made for the experiment. If there is a gap between the specimen and the inner wall of the tube, the measurement results show an overestimation of the results caused by the undiluted waves and occurrence of vibrations of the imperfectly touching parts as could be seen in Fig. 4 for the non-ideally circular sample nr. 3 (green line).
Three sets of samples were tested. Thermo-insulating plaster with basalt fibers, gypsum plaster with glass fibers and cement plaster. Every set contained three samples. The first set (thermos-insulation plaster + basalt fiber) was a sample that supposed to have the best acoustic absorption and the last set (cement plaster) should have the worst results. The testing was carried on the Brüel & Kjaer impedance tube type 4206. This device allows to measure the factor for the perpendicularly impacting waves. The impedance tube consists of a loudspeaker and two measuring microphones that are connected to the evaluation unit.
Fig. 3The samples of plaster prepared for testing
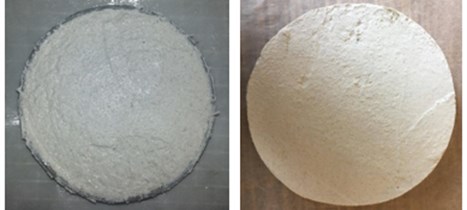
4. Result and discussion
The acoustic absorption of the samples was measured on the three various, usually available plasters. The aim of the test was to assess whether the samples have good acoustic absorption and to determine the difference between the selected materials. For all of the samples the frequency dependence of the sound absorption factor was monitored.
Fig. 4Experimental comparison of the cement plaster samples
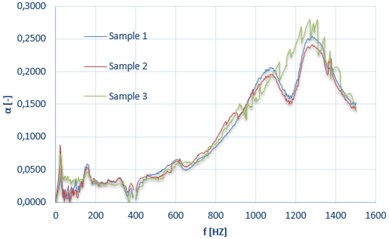
Fig. 5The founded frequency dependence of the measured sound absorption coefficient
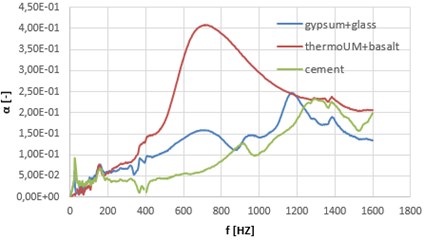
It can be seen in the Fig. 5, that the best results were obtained from a samples of the thermos-insulating plaster with the basalt fibers.
At the same time, it could be seen that the results of the two another material do not significantly differ from each other, even if the one of the sample groups containing fiber reinforcement. Each of the tested set contained 3 samples. In the Fig. 4 are results of the test with one group of plaster samples, when one of them does not have the ideal circular profile. As could be seen this cause some vibration and lot of small steps in the value of the acoustic attenuation.
5. Conclusions
The three usually used plaster materials were used for creation of testing samples. The plasters have been chosen with an assumption that the best acoustic results will have the thermal-insulation plaster Thermo UM Xtra, which was reinforcement with the basalt fibres. The measurement was carried according to standard ČSN ISO 10534-2. From the results is clear to see, as has been supposed, that the thermo-insulation plaster reinforcement basalt fibres has significantly better properties than the other test samples. The reason could be the grainy structure of the plaster which causes the larger content of pores in the plaster. For the cement and gypsum plaster reinforced with the glass fibers we obtained an almost similar results. The results showed that the addition of short fibre reinforcement to plaster does not have significant impact on the value of acoustic absorption. Another possible target of our future work is to test the possibility of using some other forms of reinforcement, such as leno wave with a various fibrous ratio.
References
-
Baltrénas P., Butkus D., Grubliauskas R., Kučiaukaité J. Noise studies and reduction possibilities in a residential area located by a highway. Ecology, Vol. 55, Issue 1, 2009, p. 48-57.
-
Francis C. D., Paritsis J., Ortega C. P., Cruz A. Landscape patterns of avian habitat use and nest success are affected by chronic gas well compressor noise. Landscape Ecology, Vol. 26, Issue 9, 2011, p. 1269-1280.
-
Chahrour A. H., Soudki K. A. RBS polymer encased concrete wall. Part II: experimental study and theoretical provisions for combined axial compression and flexure. Construction and Building Materials, Vol. 20, Issue 10, 2006, p. 1016-1027.
-
Diaz C., Diaz A., Navacerrada M. A. An experimental study on the effect of rollong shutters on the field measurements of airborne sound insulation of facades. Applied Acoustics, Vol. 1, Issue 174, 2013, p. 134-140.
-
Frontczak M., Wargocki P. Literature survey on how different factors influence human comfort in indoor environments. Building and Environment, Vol. 46, Issue 4, 2011, p. 922-937.
-
Cuiyun D., Guang C., Xinbang X., Peisheng L. Sound absorption characteristics of a high-temperature sintering porous ceramic material. Applied Acoustics, Vol. 73, Issue 9, 2012, p. 865-871.
-
Dixit M. K., Fernández-Solís J. L., Lavy S., Culp C. H. Identification of parameters for embodied energy measurement. Energy and Buildings, Vol. 42, Issue 8, 2010, p. 1238-1247.
-
Faustino J., Pereira L., Soares S., Cruz D., Paiva A., Varum H., et al. Impact sound insulation technique using corn cob particleboard. Construction and Building Materials, Vol. 37, 2012, p. 153-159.
-
Januševičius T., Mažuolis J., Butkus D. Sound reduction in samples of environmentally friendly building materials and their compositions. Applied Acoustic, Vol. 113, Issue 1, 2016, p. 132-136.
-
Tonoli G. H. D., Santos S. F., Savastano H., Delvasto S., Mejía de Gutiérrez R., Lopez de Murphy M. D. M. Effects of natural wearhering on microstructure and mineral composition roofing tiles reinforced with fique fibre. Cement and Concrete Composites, Vol. 33, 2011, p. 225-232.
-
Samková A., Kulhavý P., Pechočiaková M. M. Fibre reinforcement effect on plaster composite properties. NART Conference Proceeding, 2015, p. 189-195.
-
Blankenhorn P. R., Silsbee M. R., Blankenhorn B. D., DiCola M., Kessler K. Temperature and moisture effects on selected properties of wood fiber-cement composites. Cement and Concrete Research, Vol. 29, 1999, p. 737-741.
-
Soroushian P., Marikunte S., Won J. P. Statistical evaluation of mechanical and physical properties of cellulose fiber reinforced cement composites. ACI Materials Journal, Vol. 92, Issue 2, 1995, p. 172-180.
-
Wolfe R. W., Gjinolli A. Durability and strength of cement bonded wood particle composites made from construction wase. Forest Products Journal, Vol. 49, Issue 2, 1999, p. 24-31.
-
Neithalath N., Weiss J., Olek J. Acoustic performance and dampling behavior of cellulose-cement composites. Cement and Concrete Composites, Vol. 26, 2002, p. 359-370.
-
Arnaud L., Gourlay E. Experimental study of parameters influencing mechanical properties of hemp concretes. Construction and Building Materials, Vol. 28, Issue 1, 2012, p. 50-56.
-
Glé P., Gourdon L., Arnaud L. Acoustical properties of material made of vegetable particles with several scales of porosity. Applied Acoustics, Vol. 72, Issue 5, 2011, p. 249-259.
-
http://www.izolace-sanace.cz/thermoum-extra, 2017.
-
http://www.levnestavebniny.cz/sadrova-omitka-rigips-rimat-100-dlp-.7666/, 2017.
-
https://www.weber-terranova.cz, 2017.
-
Best Myron G. Magmatic and Metamorphic Petrology. 2nd Edition, Willey-Blackwell, 2002.
-
Singha K. A short review of basalt fiber. International Journal of Textile Science, Vol. 1, Issue 4, 2012, p. 19-28.
-
Fiore V., Scalici T., Di Bella G., Valenza A. A review on basalt fibre and its composites. Composites Part B: Engineering, Vol. 74, 2015, p. 74-94.
-
Wei B., Cao H., Song S. Enviromental resistance and mechanical performance of basalt and glass fiber. Material Science and Engineering, 2010.
-
Lehner J. Skleněná Horninová a Strukturová Vlákna. STNL, Praha, 1960.
-
Chen J., Lee Y. E., Ueda M., Taniguchi K. A simple optical method for the measurement of glass wool fiber diameter. Optics and Lasers in Engineering, Vol. 29, 1998, p. 67-71.
-
http://www.okorder.com/p/basalt-fiber-continous-roving-chopped-fiberneedle-felt_898695.html#prev, 2016.
-
http://kirknielsen.com/project/metal/, 2016.
-
http://www.vlaknadobetonu.cz/, 2017.
-
http://agostinanotherm.com, 2017.
-
Methods of Test for Mortar for Masonry – Part 11. Standard ČSN EN 1015-11. Český Normalizační Institut, Praha, 2000.
-
Bies D. A., Hansen C. H. Engineering Noise Control-Theory and Practice. Spon Press, 2009.
-
Holmes N., Browne A., Montague Ch. Acoustic properties of concrete panels with crumb rubber as a fine aggregate replacement. Construction and Building Materials, Vol. 73, 2014, p. 195-204.
About this article
This publication was written at the Technical University of Liberec as part of the Project Options Reinforcement Plaster Using Fibrous Materials, 21195 with the support of the Specific University Research Grant, as provided by the Ministry of Education and the results of this Project LO1201 were obtained with co-funding from the Ministry of Education, Youth and Sports as part of targeted support from the “Národní program udržitelnosti I” Program.