Abstract
Dual-tube directional drilling technology is an effective method to solve the problem of long directional drilling in soft coal seam. According to the requirements of double pipe directional drilling, this paper introduces the structure of the mainframe of double pipe drilling rig, and develops a kind of double pipe automatic loading and unloading device, which can load and unload of drill pipe and casing at the same time. According to the different working conditions of double pipe drilling, the process flow of double pipe automatic loading and unloading is introduced. The research of double pipe automatic loading and unloading device and its process method lays a foundation for the popularization and application of double pipe directional drilling technology in related fields of coal bed methane exploitation.
1. Introduction
Due to the large gas pressure and soft and broken coal quality in broken soft coal seam, the traditional construction method of gas drainage drilling hole is easy to collapse, the depth of drilling hole is shallow, and the sieve tube is difficult to install after the hole is formed [1-3], seriously restricts the safe and efficient mining of coal. Therefore, the problem of gas pre-drainage and outburst elimination in broken soft coal seam has become a research hotspot in the field of coal safety mining.
Ningping Yao [4] proposed the use of directional drilling technology to construct a directional main hole in the stable roof or floor rocks of the coal seam, and then construct the small curvature comb-shaped branch drill hole from the main hole to the cracked zone of the coal seam or the goaf, forming a set of construction methods. It is suitable for comb-hole gas drainage technology system in Jincheng mining area, and has been successfully applied in Zhaozhuang Mine and Chengzhuang Mine. Xinsheng Yin [5] proposed the method of air drilling to solve the gas outburst problem of broken soft coal seams.
Frank Hungerford [6] described the development of drilling technology in Australia over the past thirty years. He believes that the application of directional drilling technology can improve the speed and accuracy of gas drainage drilling and help to achieve the overall drilling depths.
Yafeng Yao [7] has developed a complete set of technology and equipment for dual-power-head dual-pipe directional drilling in broken soft coal seams in coal mines, which can effectively solve the problem of long directional drilling in broken soft coal seams. Difficulty in hole formation and installation of large-diameter screen after hole formation. Among them, the dual-power-head dual-pipe drilling directional drilling rig is one of the cores of this technology; and the mainframe with automatic drilling function, as well as the automatic loading and unloading device of drill pipe and casing under different working conditions. The rod device is the main research point of the drilling rig. The mainframe of the drilling rig with automatic drilling function, and the rod adding device that can complete the automatic loading and unloading of the drill pipe and casing under different working conditions are also the key points of the drilling rig.
2. The overall structure design of the mainframe of the double-pipe directional drilling rig
In order to adapt to the requirements of dual-pipe drilling technology, the mainframe of dual-pipe directional drilling rig has been developed. Compared with the traditional drilling rig, the directional drilling rig with double power head and double pipe has a big difference [8]. The main characteristic is that the mainframe consists of three grippers and two power heads. As shown in Fig. 1, a casing gripper, a casing shackle, a drill pipe shackle, a casing power head and a drill pipe power head are respectively installed on the left to right of the feeding device. The casing power head is used to drive the casing (outer pipe) to rotate, while the drill pipe power head is used to drive the drill pipe (inner pipe) to rotate. The casing and the drill pipe are driven by an independent hydraulic system, rotating without interference with each other. An oil cylinder is arranged between the casing power head and the drill pipe power head, and the relative position of the thread of the drill pipe and the casing front end can be adjusted through the motion of this oil cylinder. The carrier of the casing power head connected with one end of the feed cylinder, and the feed cylinder drives two power heads to feed synchronously. The casing gripper is located at the front end of the feed device, which is used to clamp the casing in the hole. The casing shackle is used to loosen the casing thread, and cooperate with the drill pipe shackle to complete the disassembly of the drill pipe thread.
The side of the feeding device is also provided with a double-pipe automatic loading and unloading device, which can work with three grippers and two power heads to complete the automatic loading and unloading of casing and drill pipe under different working conditions.
Fig. 1Schematic diagram of mainframe of double-pipe directional drilling rig: 1. Casing gripper, 2. Casing shackle, 3. Drill pipe shackle, 4. Double pipe automatic loading and unloading device, 5. Feeding device, 6. Casing power head, 7. Drill pipe power head
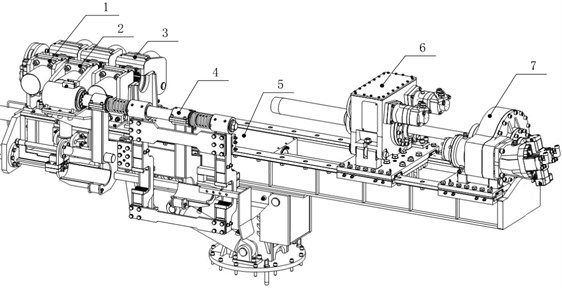
3. Design of double pipe automatic loading and unloading device
In the traditional coal mine drilling, the operation mode of manual loading and unloading drill pipe is generally adopted. For a drill with dual power head structure, it is essential to load drill pipe and casing at the same time during drilling construction, as well as remove drill pipe and casing at the same time after drilling. Due to the heavy weight of drill pipe and casing and different specifications of thread, manual loading and unloading is difficult to achieve. The double-pipe automatic loading and unloading device can automatically load and unload the casing and drill pipe at the same time, which can solve the key problem during double-pipe automatic drilling. The device has been patented in China. The authorization notice number is CN109611040B.
3.1. Structure of double pipe automatic loading and unloading device
The double-pipe automatic loading and unloading device (as shown in Fig. 2) is composed of oscillating oil cylinder, support, reset spring, casing pipe gripper arm, drive shaft, gripper arm stop device, drill pipe gripper arm, flow dividers and combiner, baffle, casing stop plate, push rod device, etc. The oscillating oil cylinder is fixed on one end of the bracket and connected with the drive shaft through a coupling. The drive shaft is provided with a casing pipe gripper arm and a drill pipe gripper arm. The two gripping arms connected with the transmission shaft through the sliding key, and can rotate around the transmission shaft under the drive of the oscillating oil cylinder, while sliding along the transmission shaft axially. The drive shaft is set in the bracket through two groups of axle suspension bushes, and a self-lubricating bearing is arranged between the bracket and the drive shaft to reduce the friction force during rotation. The two arms are fixed together through two sets of beams, and two sets of reset springs are arranged between the arms and the bracket. Two sets of clamping cylinders are arranged at the end of the clamping arm to drive two sets of slips to clamp the drill pipe or casing. One end of the bracket is provided with a push rod device, the other end is provided with a baffle, the bottom of the bracket is provided with a circular arc space for placing casing and drill pipe, and an auxiliary support plate for convenient placement of drilling tools.
Fig. 2Schematic diagram of double pipe automatic loading and unloading device: 1. Oscillating oil cylinder, 2. Support, 3. Reset spring, 4. Casing pipe gripper arm, 5. Drive shaft, 6. Gripper arm stop device, 7. Drill pipe gripper arm, 8. Flow dividers and combiner, 9. Baffle, 10. Casing stop plate, 11. Push rod device
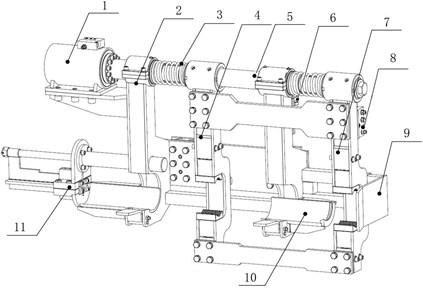
3.2. Working principle of double pipe automatic loading and unloading device
When installing drilling tools for dual-pipe directional drilling, first place the drill pipe inside the casing, keeping the thread facing the same and the ends flat, to form a BHA. Then the BHA is placed between the push rod device and the casing stop plate, the screw buckle is toward the side of the push rod device. With the push rod oil cylinder in the push rod device is withdrawn, the drill pipe and the casing are simultaneously moved to the right; the push rod cylinder stops until the casing moves to the step at the right end of the casing stop plate and the drill pipe contacts the baffle. At this point, the casing is just in the middle of the casing gripping arm slips, and the drill pipe is just inside the drill pipe gripping arm. the casing gripping arm and the drill pipe gripping arm clamp the casing and drill pipe respectively; the push rod of the push rod device retracted to the initial position; the oscillating oil cylinder drives the two gripper arms to rotate simultaneously through the drive shaft, driving the casing and drill pipe to rotate to the front end of casing power head and the drill pipe power head. Then the double pipe automatic loading and unloading device cooperates with the casing gripper, casing shackle, drill pipe shackle, casing power head and drill pipe power head complete the entire process of automatic installation of drill pipe and casing.
4. Design of double pipe automatic loading and unloading process under different working conditions
According to the construction technology of double pipe directional drilling, the drilling rig needs to meet the requirements of automatic rod loading and unloading under different working conditions. Include, double pipe loading requirements; the requirements for simultaneous unloading of dual pipes when dealing with abnormal conditions in the hole and separate unloading of the drill pipe and casing after drilling is also very important.
4.1. Process flow of simultaneous loading of drill pipe and casing
When the casing power head and drill pipe power head both run to the front end of the feeding device and need to add drilling tools, the process flow of loading casing and drill pipe at the same time is as follows:
(1) Casing gripper clamps the front casing of the active casing; the casing power head reverses to remove the Casing thread.
(2) The feeding device is pulled out, the Casing shackle clamps the front drill pipe of the active drill pipe, and the drill pipe power head reverses to remove the drill pipe thread.
(3) The casing power head and the drill pipe power head are pulled out to the end of the feeding device.
(4) The double-pipe automatic loading and unloading device sends the casing and drill pipe to the front of the two power heads active rod, and the drill pipe shackler clamps the casing in the casing gripping arm.
(5) The drill pipe power head rotates and slowly tightens the drill pipe thread in the drill pipe gripper arm.
(6) Drill pipe gripper arm slips open; then the drill pipe power head continues to rotate and feed slowly, tighten the drill pipe thread in the Casing shackle.
(7) The drill pipe power head stops turning and feeding; the slip of casing shackle is opened; the casing power head rotates and slowly feeds to tighten the casing thread in the casing gripper arm.
(8) The casing gripper slips open, the drill pipe shackle slips open, the casing power head rotates and continues to feed slowly to tighten the casing thread in the casing gripper, the gripper slips open, the casing power head stops rotating and feeding, the double pipe automatic loading and unloading device is put back to the initial position, and the entire casing and drill pipe loading process was completed.
4.2. Process flow of simultaneous unloading of drill pipe and casing
In the normal operation state of the drilling rig, when the casing and drill pipe need to be removed at the same time due to an abnormality in the hole. The process flow is as follows:
(1) Adjust the position of the casing power head and the drill pipe power head on the feeding device, so that the thread of the front end of the casing (near the orifice) is located between the casing gripper and the casing shackle, and the casing power head and the drill pipe power head slide to the nearest distance.
(2) Casing gripper clamps the casing in front of the casing to be unloaded; casing shackle clamps the casing to be unloaded; the casing shackler shackle cylinder pushes out and unloads the thread of the casing to be unloaded; the casing power head reverses and slowly pulls out to remove the thread of the casing to be unloaded.
(3) The casing power head continues to be pulled until the front end of the drill pipe to be unloaded is located between the casing shackle and the drill pipe shackle.
(4) The casing shackle clamps the front-end drill pipe to be unloaded; drill pipe unshackle clamp drill pipe to be unloaded; drill pipe shackler shackle cylinder pushes out unshackle drill pipe thread; the drill pipe power head is reversed and slowly pulled out to remove the drill pipe thread buckle.
(5) The drill pipe unloaded clamps the drill pipe in front of the drill pipe to be unloaded, and the drill pipe power head reverses to loosen (not unload) the thread of the back end of the drill pipe to be unloaded (near the power head); the drill pipe shackle releases the drill pipe to be unloaded; the lever of the sliding cylinder is fully extended, and the drill pipe power head is pulled up to the farthest distance from the casing power head.
(6) The casing power head is fed to send the casing to be unloaded between the slips of the drill pipe shackle; The drill pipe shackler clamps the casing to be unloaded, and the power head of the casing reverses and slowly pulls out and removes the thread at the back end of the casing to be unloaded (near the power head).
(7) The drill pipe power head is pulled up to 100 mm away from the last end of the feeding device.
(8) The two clamping arms of the double-pipe automatic loading and unloading device are put to the front of the power head, and the casing gripper arm clamps the casing to be unloaded; Drill pipe gripper arm clamps drill pipe to be unloaded; The drill pipe power head is reversed and slowly pulled out to remove the drill pipe thread to be unloaded, and the two power heads are pulled up to the last end of the feeding device.
(9) The two gripping arms are swung back to the initial position, and the drill pipe and casing are sent to the side of the feeding device and the entire casing and drill pipe unloading process was completed.
5. Conclusions
According to the construction technology requirements of double pipe directional drilling, the structure design of the drilling rig is completed. It has the functions of double pipe automatic loading and unloading, and the process design of double pipe automatic loading and unloading is carried out according to the different working conditions of double pipe drilling. The difficulty of automatically load and unload the drill pipe and casing in double pipe automatic directional drilling has been solved.
References
-
Shi Z. J., Liu J. L., Li Q. X. Development and application of drilling technique and equipment in coal mining area of China. Coal Science and Technology, Vol. 46, Issue 4, 2018, p. 1-6.
-
Lin B. Q., Li Q. Z., Yang W., Wu H. J. Gas control technology and applications for the three-soft coal seam based on VLD-1000 drilling systems. Journal of China Coal Society, Vol. 36, Issue 12, 2011, p. 1968-1973.
-
Li Q. X., Shi Z. J., Tian H. L., Yao K., Liu J. L., Yao Y. F., Xu C., Fang J., Liu F. Progress in the research on drilling technology and equipment in coal mining areas of China. Coal Geology and Exploration, Vol. 47, Issue 2, 2019, p. 1-6.
-
Yao N. P., Zhang J., Zhang G. L., Du L. M., Zhang X. L., Song B., Ren H. H. System of gas drainage technology of comb-like directional drilling in Jincheng Mining Area. Coal Science and Technology, Vol. 43, Issue 2, 2015, p. 88-91.
-
Yin X. S., Fan D., Yao K., Ji Q. H. Medium pressure compression technique and matched equipment of air drilling in soft and outburst seam. Coal Science and Technology, Vol. 37, Issue 9, 2009, p. 72-74.
-
Hungerford F., Ren T., Aziz N. Evolution and application of in-seam drilling for gas drainage. International Journal of Mining Science and Technology, Vol. 23, 2013, p. 543-553.
-
Yao Y. F., Yao N. P., Peng T. Design and analysis on clamping mechanism of soft seam casing drilling rig. Coal Science and Technology, Vol. 41, Issue 6, 2013, p. 73-76.
-
Yao N. P., Wang Y., Yao Y. F., Song H. T., Wang L., Peng T., Sun X. S. Progress of drilling technologies and equipment for complicated geological conditions in underground coal mines in China. Coal Geology and Exploration, Vol. 48, Issue 2, 2020, p. 1-7.
About this article
This research was supported by the National Key Research and Development Program of Xi’an Research Institute of China Coal Technology and Engineering Group No. 2018YFC0808005.