Abstract
Indoor simulated mixing building storage bin unloading, forming conical piles. The effects of falling distance, mixing time and water content on rolling segregation of cement-stabilized macadam were analyzed by three indexes, including repose Angle of pile, key sieve passing rate and cement dosage. The results show that the segregation of mixture can be increased significantly with the increase of drop distance. The separation degree of the mixture can be effectively controlled by controlling the unloading distance within 70 cm. Mixing time has little effect on the Angle of rest and gradation segregation of the mixture, but has significant effect on the distribution uniformity of cement. Indoor mixing time should reach more than 45 s. When the mixing water content is less than the optimal water content, the segregation of the mixture is serious. When the moisture content increased to 1.5 %, the mixture showed obvious bleeding phenomenon. The mixture shall not be lower than the optimal moisture content before the crushing is completed, and the moisture content increase shall not exceed 1.5 % of the optimal moisture content as far as possible.
1. Introduction
Cement stabilized crushed stone mixture is composed of heterogeneous aggregates and cement with different particle sizes. There are obvious differences in volume and density between the components of the mixture. In mixing, paving and other construction links, the movement of each component is different [1]. This results in uneven distribution of the mixture in the solid engineering, namely segregation. The segregation of the mixture results in the deviation of local pavement performance from the design objective. Segregation results in the increase of partial voidage of semi-rigid base, the decrease of cement dosage, and the damage of overall bearing capacity of pavement [2-3]. This is an important factor affecting the service quality of pavement. Mastering the segregation law of cement stabilized macadam mixture and putting forward the control measures according to the influencing factors are the important guarantee to improve the uniformity of pavement construction and ensure that the service life surface of pavement reaches the design goal.
Cement stabilized crushed stone is a mixture of different particles in composition. The movement in the construction process satisfies the basic law of friction and collision between particles [4]. Qin Wen from Chang’an University proposed a test method for simulating construction segregation. Based on the movement characteristics of different particles, the mechanism of segregation in different stages of production was analyzed [5]. Ketterhagen et al. simulated the motion state of particles in a wedge funnel and analyzed the rolling segregation rule of particles [6]. Carr et al. used viscoelastic model to analyze the influence of cement on the segregation of mixture [7]. Lin Chao used a homemade funnel in the laboratory to conduct simulation tests to study the influence of the pile Angle of the mixture on segregation [8]. Han Leng put forward an evaluation method of mixture segregation based on voidage ratio [9]. Based on the topic of “Research on Lean Construction Technology of semi-rigid base asphalt Pavement”, this paper analyzes the important factors affecting the segregation of cement stabilized gravel mixture in the construction process through laboratory simulation test, and provides support for the uniformity control scheme of semi-rigid base.
2. Mixture design
Limestone aggregate was used in the test, and the grading curve of the mixture was determined by sifting each grade, as shown in Fig. 1. The benchmark test used 4.5 % cement dosage. The optimal water content of 4.7 % and the maximum dry density of 2.483 were determined by vibration compaction method.
Fig. 1Mixture grading curve
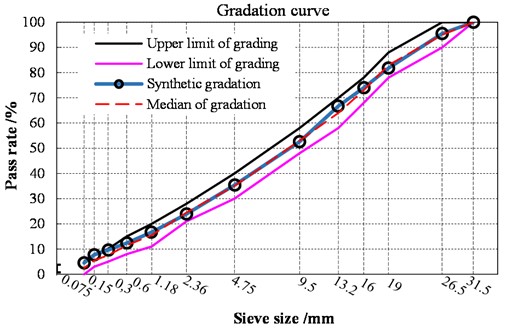
3. Test method for segregation of mixtures
The segregation of the mixture mainly occurs in the process of mixing, loading, unloading and laying. The root cause is caused by the asynchronous movement between different materials [10]. Conical piles are formed when granular materials are loaded and unloaded. The conical Angle of the piles is the Angle between the free surface and the horizontal plane when the free surface of the accumulation body is in the limit state of equilibrium. Conical piles will be formed when granular materials are loaded and unloaded. The conical Angle of the piles is the Angle between the free surface of the accumulation body and the horizontal plane, which is called the Angle of repose, as shown in Fig. 2. It is an important parameter to characterize the flow characteristics of mixed particles. Segregation of the mixture is caused by mobility. The relationship between mobility of granular material and Angle of repose is shown in Table 1. The cohesiveness of the mixture reduces rolling segregation. In this paper, the free flow in the unloading process is simulated and the factors affecting the segregation of mixture are evaluated by the Angle of repose.
Table 1Relationship between flow characteristics of granular mixture and Angle of repose
Angle of repose (°) | Characteristics of granular mixture |
25-35 | Free flow |
35-45 | Medium fluidity, slightly sticky |
45-55 | Can not flow freely, good cohesiveness |
Fig. 2Mix pile shape
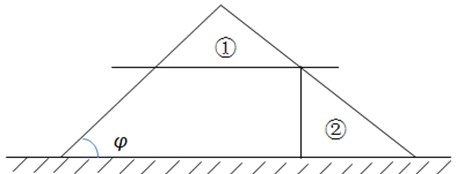
The segregation of the mixture directly affects the distribution of gradation and cement dosage, and finally affects the strength of the mixture. The influence of segregation on the performance of the mixture was evaluated by the variability of the key sieve pass rate of the mixture and the dosage of cement by extracting the mixture from different locations ((1) and (2) in Fig. 1).
4. Segregation test analysis of mixture
4.1. Effect of falling distance on Angle of rerest of mixture
In order to analyze the influence of unloading distance on mixture segregation, a funnel-shaped device was used to simulate the storage bin for indoor mixture unloading test. Mix according to the mixing ratio determined by the benchmark test to produce the mixture. 6 groups of mixture unloading tests were carried out according to different drop distances, and 5 parts of cement stabilized gravel mixture were mixed in each group, each of which was 4 kg. In each group of tests, each mixture is loaded into the storage hopper for free unloading. After each mixture is unloaded, the height and diameter of the accumulated pile are measured and the Angle of reactivity is calculated. The test results are shown in Table 2.
It can be seen from the test results that the Angle of rest of the pile is related to the blanking mass and falling distance, and the falling distance has a greater influence on the Angle of rest. When the discharge mass is large, the pile is stable, and the Angle of repose is representative. When the landing distance is less than 70 cm, the Angle of rest has little change, while when the landing distance is more than 90 cm, the Angle of rest decreases significantly with the increase of the landing distance. Under the condition of the same drop distance, the repose Angle of the pile increases with the increase of the discharge mass. This is because the interaction between the mixture and the ground increases the rolling dispersion during the initial discharge. After the formation of the pile, the buffer effect is generated on the discharged mixture, and the repose Angle gradually becomes stable. When the falling distance is less than 90 cm, the mass of the mixture reaches more than 12 kg and the Angle of rest tends to be stable; when the falling distance is more than 110 cm, the mass of the mixture reaches more than 16 kg and the Angle of rest tends to be stable.
Table 2Unloading test results of cement stabilized gravel at different falling distances
Angle of repose weight | Drop distance | |||||
50 cm | 70 cm | 90 cm | 110 cm | 130 cm | 150 cm | |
4 kg | 38.7 | 38.4 | 37.5 | 35.2 | 31.1 | 30.6 |
8 kg | 39.6 | 38.9 | 38.1 | 36.1 | 33.1 | 32.6 |
12 kg | 39.5 | 39.2 | 38.6 | 36.7 | 33.7 | 33.2 |
16 kg | 39.5 | 39.3 | 38.9 | 37.4 | 34.2 | 33.9 |
20 kg | 39.7 | 39.5 | 38.8 | 37.9 | 34.5 | 34.1 |
4.2. Effect of drop distance on segregation of mixture
The 4.75 mm sieve pass rate of the mixture is an important index to characterize the gradation thickness. After the mixture segregation, the ratio of coarse and fine aggregate changes, and the dosage of cement in different positions of the mixture also varies. In order to analyze the impact of mixture unloading on segregation, the mixture is taken from two locations of the pile ((1) and (2) in Fig. 2). The mixture at the two locations was divided into two parts. One part was used to measure the cement dosage and the other part was screened to determine the 4.75 mm pass rate. The key sieve pass rate test of the mixture is shown in Table 3, and the cement dose test results are shown in Table 4.
Table 3Test results of key sieve passing rate of mixture
Drop distance (cm) | 50 | 70 | 90 | 110 | 130 | 150 |
(1) 4.75 mm Pass rate | 36.2 | 36.1 | 36.8 | 37.4 | 39.1 | 39.5 |
(2) 4.75 mm Pass rate | 32.5 | 32.1 | 31.3 | 29.5 | 29.1 | 28.3 |
Table 4Dosage test results of mixed cement
Drop distance (cm) | 50 | 70 | 90 | 110 | 130 | 150 |
(1) Cement dosage (%) | 4.7 | 4.9 | 4.7 | 5 | 4.8 | 4.9 |
(2) Cement dosage (%) | 4.1 | 4.2 | 4 | 3.8 | 3.6 | 3.7 |
As can be seen from Table 3, there is a significant difference in the gradation of mixtures at the top and bottom of the pile. Compared with the design grading, the pass rate of 4.75 cm at the top of the pile increases, while the pass rate of 4.75 cm at the bottom decreases. The top gradation is thinner and the bottom gradation is thicker. With the increase of drop distance, the top gradation changes little, and the bottom becomes more obvious. When the drop distance is less than 70 cm, the pass rate difference of 4.75 cm sieve reaches 4 %. When the drop distance is 150 cm, the pass rate difference of 4.75 cm sieve increases nearly twice, reaching more than 11 %. Due to the particle property of the mixture itself, segregation of the mixture is inevitable during loading and unloading, but the separation degree of the mixture can be effectively limited by controlling the fall distance within 70 cm.
As can be seen from Table 4, the cement dose at the top of the pile is higher than the reference cement dose, while the tested cement dose at the bottom is lower due to segregation of the mixture gradation at different locations. Therefore, the detection of mixture gradation and cement dose on the construction site is greatly affected by the uniformity of taking material, so it is necessary to take material evenly on the drive belt as far as possible.
The segregation of the mixture gradation directly leads to the uneven density of the structural layer after forming, and the difference of the dosage of cement leads to the difference of the strength of different parts. The result is the uneven bearing capacity and cracking performance of the whole semi-rigid base, which makes the pavement structure performance far from the design expectation.
4.3. Effect of mixing time on segregation
Mixing time is an important factor affecting the performance of the mixture. The mixing state of the mixture was distinguished by adjusting mixing time in an indoor mixing pot, and the influence of mixing adequacy on segregation of the mixture was analyzed. In order to ensure the differentiation of test results, 90 cm unloading height was adopted, and each group of mixed materials was no less than 16 kg. The test results are shown in Table 5-Table 7.
The results show that mixing time has little effect on the Angle of rest and segregation of cement stabilized gravel. When the indoor mixing time is less than 30 s, the dispersion of cement dose is larger, and the cement cannot be fully dispersed in the mixture for a short mixing time, resulting in the cement gathering in the fine aggregate, and the coarse aggregate cannot be fully wrapped by the cement. The dosage distribution of cement was stable when the mixing time was greater than 45 s. The mixing effect can be improved by increasing the mixing strength or extending the mixing time in engineering. It is recommended to use double mixing tank or vibrating mixing tank to mix the mixture.
Table 5Angle of repose of cement stabilized gravel at different mixing time
Mixing time (s) | 15 | 30 | 45 | 60 | 75 | 90 |
Angle of repose (°) | 38.4 | 38.3 | 38.2 | 38.5 | 38.8 | 38.7 |
Table 6Key sieve passing rate of mixtures at different mixing times
Mixing time (s) | 15 | 30 | 45 | 60 | 75 | 90 |
(1) 4.75 mm Pass rate | 36.5 | 36.7 | 36.3 | 36.1 | 36.5 | 36.4 |
(2) 4.75 mm Pass rate | 30.8 | 31.7 | 31.5 | 31.9 | 31.7 | 32.3 |
Table 7Test results of cement dosage of mixtures at different mixing times
Mixing time (s) | 15 | 30 | 45 | 60 | 75 | 90 |
(1) Cement dosage (%) | 5.1 | 4.9 | 4.7 | 4.7 | 4.8 | 4.6 |
(2) Cement dosage (%) | 3.6 | 3.8 | 4.0 | 3.9 | 4.1 | 4.0 |
4.4. Effect of water content on segregation
There is a certain time interval between the production of the mixture and the completion of spreading and rolling. In order to ensure that the mixture at the spreading and rolling stage is close to the optimal water content, the water content is generally increased by 0.5 %-1.0 % during the mixing production. The change of water content has a direct effect on the cohesiveness of the mixture. Based on the best moisture content, the water content was adjusted at intervals of 0.5 %. The unloading height of 90 cm was adopted, and the mixing time of 90 s was no less than 16 kg for each group. The influence of water content on segregation of mixture was analyzed experimentally, and the experimental results were shown in Table 8- Table 10.
Table 8Repose angle of gravel stabilized by mud with different moisture content
Water content (%) | 3.7 | 4.2 | 4.7 | 5.2 | 5.7 | 6.2 |
Angle of repose (°) | 35.5 | 37.1 | 38.7 | 39.2 | 39.1 | 38.6 |
Table 9Key sieve pass rate of mixtures with different water content
Water content (%) | 3.7 | 4.2 | 4.7 | 5.2 | 5.7 | 6.2 |
(1) 4.75 mm Pass rate | 37.5 | 37.2 | 36.4 | 36.1 | 36.3 | 36.6 |
(2) 4.75 mm Pass rate | 25.7 | 28.3 | 32.3 | 33.2 | 33.1 | 32.9 |
Table 10Dosage of cement mixed with different water content
Water content (%) | 3.7 | 4.2 | 4.7 | 5.2 | 5.7 | 6.2 |
(1) Cement dosage (%) | 5.1 | 4.8 | 4.6 | 4.7 | 4.7 | 5.0 |
(2) Cement dosage (%) | 3.5 | 3.9 | 4 | 4.1 | 3.9 | 3.9 |
According to the test results, under the condition of sufficient mixing, when the water content of mixing is less than the optimal water content, the Angle of rerest decreases significantly, and the bottom of the pile is dominated by coarse aggregate and segregation details. Inadequate water content will increase the segregation of the mixture, resulting in a decrease in cement slurry adhesion. The uneven cement coating has a serious effect on the properties of the mixture. At the same time, the lack of moisture content will affect the field compaction degree. When the mixing water content is higher than the optimal water content, the adhesion of cement and fine aggregate on the surface of coarse aggregate is enhanced, the cohesiveness of the mixture is increased, and the rolling segregation of the mixture is obviously reduced. When the moisture content increases to 1.5 %, there is obvious bleeding phenomenon in the mixture, which affects the distribution of powder and cement in the mixture, and the spring phenomenon appears in the field rolling. Therefore, cement stabilized crushed stone mixing production should ensure sufficient moisture content, so that the mixture is not less than the optimal moisture content before the completion of rolling. The moisture content of the mix should not exceed 1.5 % of the optimal moisture content. The construction in high temperature season should achieve effective water retention, and cannot blindly increase the mixing moisture content, otherwise the uneven distribution of the moisture content of the mixture will also cause the compaction segregation of the base. When necessary, water can be properly replenished in the rolling process through the roller to ensure even compaction effect.
5. Conclusions
The effects of unloading distance, mixing time and water content on the rolling segregation of the mixture were analyzed by using the Angle of rerest, key sieve pass rate and cement dose. The following conclusions are drawn:
1) Unloading distance has significant effect on segregation of mixture. With the increase of fall distance, the rerest Angle of the pile decreases, the fine aggregate at the top of the pile increases, the coarse aggregate at the bottom increases, and the segregation distribution of cement with gradation is uneven. In order to reduce the segregation of the mixture during unloading, it is advisable to control the unloading distance within 70 cm.
2) Mixing time has little effect on the segregation of cement stable fragmentation gradation. Mixing time affects the dispersion of cement in the mixture and the binding of aggregate. In order to ensure the mixing effect, indoor mixing should reach more than 45 s. In practical engineering, the mixing quality can be guaranteed by increasing the length of mixing tank, increasing mixing times and improving mixing strength.
3) When the mixing water content is less than the optimal water content, the cement paste adhesion decreases, the cement coating is uneven, resulting in the separation of the mixture intensified. In order to control bleeding of the mixture, the increase in moisture content should not exceed 1.5 % of the optimal moisture content.
References
-
Y. Peng and L. J. Sun, “Summary of research methods for uniformity (segregation) of asphalt mixture,” Journal of Chinese and Foreign Highway, Vol. 27, No. 1, pp. 147–150, 2007.
-
L. Z. Dan, F. Chen, and W. Chen, “Study on pavement performance of cement stabilized crushed stone mixture based on vibration mixing technology,” Journal of Highway Traffic Technology, Vol. 34, No. 5, pp. 21–26, 2018.
-
P. Qu, Quantitative Analysis of Asphalt Mixture Segregation. Xi’an: Chang’an University, 2017.
-
Li Pei-Long, Su Jin-Fei, Sun Sheng-Fei, Wang Xiao, and Ma Yun-Fei, “Research advances of aggregate characteristics, interface effect, and migration behaviors of multi-level aggregate-asphalt system,” China Journal of Highway and Transport, Vol. 36, No. 1, Jan. 2023, https://doi.org/10.19721/j.cnki.1001-7372.2023.01.001
-
W. Qin, Study on Segregation of Pavement Materials Based on Granular Characteristics. Xi’an: Chang’an University, 2011.
-
W. R. Ketterhagen, J. S. Curtis, C. R. Wassgren, and B. C. Hancock, “Modeling granular segregation in flow from quasi-three-dimensional, wedge-shaped hoppers,” Powder Technology, Vol. 179, No. 3, pp. 126–143, Jan. 2008, https://doi.org/10.1016/j.powtec.2007.06.023
-
M. J. Carr, W. Chen, K. W. Williams, and A. Katterfeld, “Comparative investigation on modelling wet and sticky material behaviours with a simplified JKR cohesion model and liquid bridging cohesion model in DEM,” in Proceedings of the 12th International Conference on Bulk Materials Storage, Handling and Transportation, pp. 11–14, 2016.
-
C. Lin, Study on Pavement Mixture Segregation Under Nature Falling Accumulation Condition. Xi’an: Chang'an University, 2014.
-
L. Han, Analysis of the Cause of Segregation of Asphalt Mixture and Its Influence on Road Performance. Chongqing: Chongqing Jiaotong University.
-
S. L. Li, N. X. Liang, and S. Zeng, “Influence of acquisition methods on segregation evaluation of digital image of asphalt mixture,” Journal of Chongqing Jiaotong University, Vol. 40, No. 3, pp. 103–107, 2021.
About this article
The authors have not disclosed any funding.
The datasets generated during and/or analyzed during the current study are available from the corresponding author on reasonable request.
The authors declare that they have no conflict of interest.