Abstract
The built-in spring reinforced metal C-shaped sealing ring is a high-performance static sealing component. Its metal combination sealing structure is designed to meet the sealing requirements of all metal graded cementing tools. To analyze and study the sealing performance of this combination sealing structure under complex underground application conditions, a three-dimensional simulation analysis model of the metal C-shaped ring combination sealing structure was established using ANSYS finite element analysis software, Simulate and analyze the stress and deformation of the combined sealing structure under different working conditions (room temperature and high temperature), and discuss the influence of external load conditions, including underground working medium pressure, temperature, and pre compression amount, on the sealing performance of the combined sealing structure. Calculate the variation law of contact pressure and equivalent stress under specific external conditions, providing some reference basis for the design and application of sealing rings and combined sealing structures.
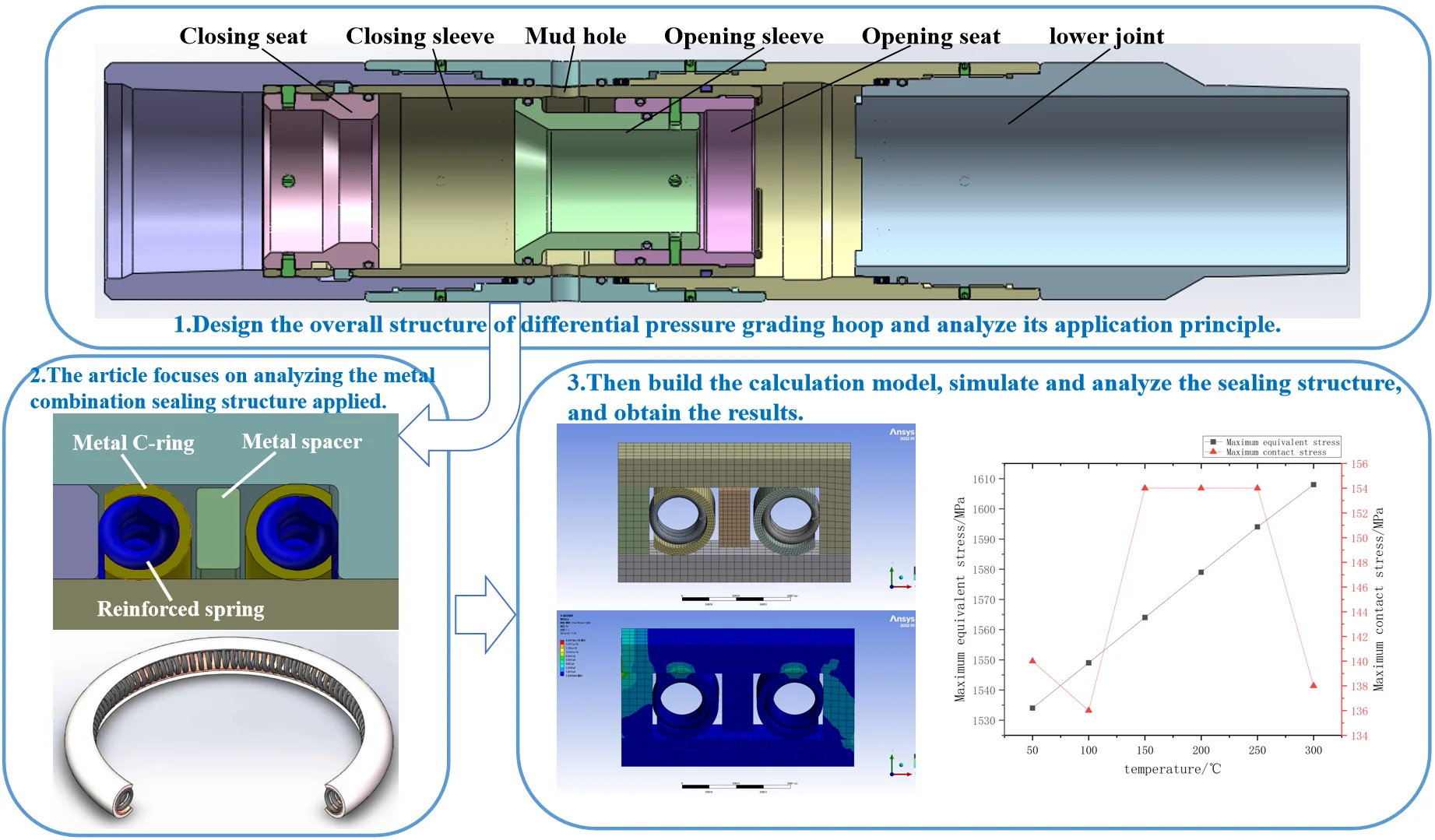
Highlights
- The article applies metal C-shaped sealing ring with better sealing performance to achieve the downhole sealing performance of the grading hoop.
- The combined sealing structure analyzed was designed by individuals, using spring reinforced metal sealing ring, afterwards, collaborated with the company on a project to jointly research.
- Use finite element numerical simulation method to analyze and calculate the calculation model under various conditions.
1. Introduction
With the rapid development of modern nuclear power, petrochemical and other industries and the continuous improvement of technological level, the operating conditions of their equipment have also shown an increasingly stringent trend, such as extreme usage conditions such as high temperature, low temperature, high pressure, strong corrosion, nuclear radiation, etc. Therefore, higher requirements have been put forward for the design of relevant sealing rings used in equipment. The failure of seals not only causes damage to production equipment and a decrease in industrial production output, but also leads to significant safety and environmental issues due to the leakage of working media. Metal seal technology is developed based on the above problems. Its application in Petroleum engineering originated early. In recent years, metal seal technology has been widely used in many industrial fields such as aerospace, chemical industry, nuclear energy, etc., and there are more and more types of metal seal rings, which are mainly divided into O, C, W, U, etc. according to the seal section shape.
C-shaped sealing rings are currently mainly used in aviation and Nuclear reaction fields. There is little research on the application of built-in spring reinforced metal C-shaped rings in the oil industry, and the relevant simulation and analysis are not perfect. Therefore, this paper analyzes the combined sealing structure of this type of sealing ring used in staged cementing tools, establishes a three-dimensional finite element simulation model Simulate and calculate the sealing reliability under external conditions such as temperature, discuss the specific impact of operating conditions on its sealing characteristics, and provide theoretical reference for the selection and optimization design of metal C-rings.
2. Analysis of metal C-ring sealing principle
The built-in spring metal C-ring consists of an exposed metal cladding layer and a cylindrical spiral spring wrapped inside it. The spiral spring is made of metal wire material and serves as the elastic load-bearing body of the combined sealing ring, requiring its material to have good elasticity and load-bearing strength; The external C-shaped coating layer consists of an alloy layer on the inner layer and a soft metal layer on the outer layer. The soft metal layer is usually made of materials such as silver or aluminum, and its good ductility and plastic deformation can fully compensate for the micro unevenness of the flange sealing surface.
Regarding the sealing process of spring reinforced metal C-rings, in the ideal process, the C-ring placed in the flange sealing groove is subjected to a certain amount of pressure during the initial pre compression process. The C-ring undergoes deformation, and the reaction force generated by deformation acts on the contact surface to form a large contact pressure. Excessive contact pressure causes plastic deformation of the C-ring metal coating and the contact surface area, Plastic deformation makes the soft metal outer coating of C-ring fully contact and combine with the micro-Interstitial defect on the contact surface, thus reducing the size of the leakage path and achieving the initial sealing effect. In actual working environments, factors such as medium temperature, pressure fluctuations, and bolt relaxation may cause the separation of the C-ring from the flange or reduce the sealing load. At this time, the good rebound performance of the spring metal C-ring and the contact stress and plastic deformation generated by compression during the pre-tightening process enable the contact surface of the C-ring to still contact and fit with the micro gap on the flange surface, achieving a sealing effect, The synergistic effect of plastic deformation of the silver layer and elastic deformation of the spring effectively improves the sealing performance of the C-shaped sealing ring and compensates for flange deformation and sealing ring relaxation caused by temperature and pressure fluctuations. In addition, because the spring metal C-shaped sealing ring is a self-tightening sealing ring, its opening opens axially due to internal pressure during operation, further increasing the contact stress and contact area on the sealing surface, thereby ensuring the sealing performance of the sealing ring.
3. Finite element analysis of metal C-ring sealing contact
3.1. Establishment of finite element model for contact analysis
The metal C-ring and the built-in spring base material are made of high-temperature alloy Inconel 718. The soft metal coating layer is pure silver, and the yield strength of silver at 20 ℃ and 350 ℃ is 80 MPa and 60 MPa, respectively. The thickness of the coating layer is 20 microns. The intermediate retaining ring material is copper alloy, and the finite element analysis of the metal C-ring combination sealing structure is carried out. Considering the periodicity of the combined sealing ring along the circumference, which means that each turn of spring and the corresponding metal C-shaped ring segment form a cycle, in order to reduce the computational complexity, only the combined sealing structure corresponding to the three turn springs is selected for modeling and calculation, that is, only the calculation results of the middle segment of the model are simulated and analyzed, which can eliminate the influence of some boundary constraint effects.
The finite element model and mesh generation results are shown in Fig. 1. To ensure the accuracy of the calculation results, the springs and C-rings in the combined seal structure are divided by Hexahedron elements (3D). Among them, full constraints are applied to the bottom surface of the upper and lower flanges, and symmetrical constraints are applied at both ends of the C-ring and spring periodic sections. Because the sealing structure has initial bolt interference pre tightening, radial downward displacement compression is applied to the flange, with a value equal to the initial installation interference to simulate the initial pre tightening process of the sealing structure. Temperature thermal load is applied in the analysis, and a certain working pressure is applied at the position with working medium. In addition, during the loading process, there will be partial contact, separation, or sliding between the C-ring and the spiral spring, as well as between the C-ring and the sealing surface, which will generate friction. Therefore, during the simulation, the friction coefficient between the contact surfaces is 0.15.
Fig. 1Finite element model
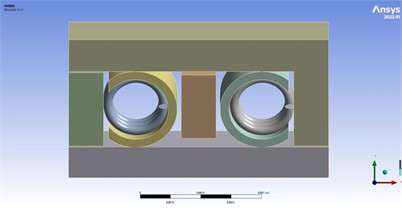
a) Geometric modeling
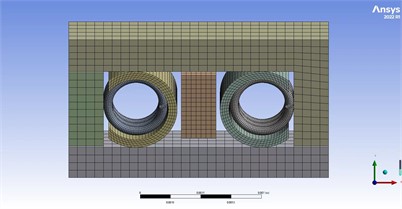
b) Grid model
3.2. Sealing analysis of initial installation and working conditions
When the C-shaped sealing ring is pre installed at room temperature, a certain amount of compression is uniformly applied to the sealing element, causing elastic deformation of the sealing ring and close contact with the surface of the sealing element, completing the initial pre installation. Under high temperature working conditions, the sealing ring bears a certain amount of pressure. Under the pressure, the sealing ring has an axial opening trend, producing an axial self tightening effect to ensure good sealing performance. Below, Ansys simulation analysis is conducted on the stress of the sealing ring under the initial installation condition at room temperature and the high temperature working condition of the combined sealing structure.
Fig. 2Cloud chart of equivalent stress and total deformation distribution of metal composite sealing structure
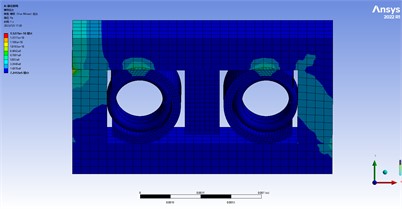
a) Equivalent stress in initial installation state (25 ℃, 0)
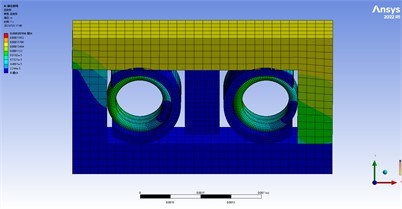
b) Total deformation in initial installation state (25 ℃, 0)
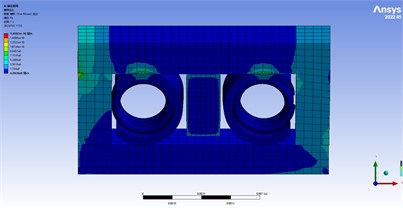
c) Equivalent stress in working state (300 ℃, 20 MPa)
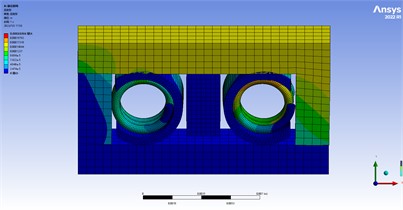
d) Total deformation in working state (300 ℃, 20 MPa)
During the analysis of normal temperature working conditions, no working pressure is applied, and an axial compressive displacement load of 0.15 mm is applied to the sealing element; When analyzing the working state, take the working temperature of 300 ℃ and the working medium pressure of 20 MPa to analyze the stress distribution and deformation of the sealing ring. Fig. 2 shows the stress cloud diagram and total deformation diagram of the metal composite sealing structure under initial installation and working conditions. From the figure, it can be seen that the equivalent stress results of the sealing rings on both sides in the initial installation state are symmetrically distributed, and the maximum equivalent stress value appears at the contact position with the addition of pre tightening displacement, which is 678.9 MPa. The maximum value of total deformation is 0.2 mm, which is within the allowable deformation range. The maximum equivalent stress under working condition is 1073.4 MPa, and the maximum total deformation is 0.22 mm.
4. Analysis of factors influencing the sealing performance of metal C-ring
4.1. The effect of temperature on the sealing performance of metal C-ring
The sealing performance of the sealing ring mainly depends on the degree of pre tightening of the sealing ring under working conditions. When the temperature changes, changes in thermal expansion and elastic modulus can lead to changes in preload, which can affect the sealing performance of the sealing ring. The working temperature range of the C-shaped sealing ring in downhole cementing tools is large, and its maximum working temperature can reach 300 ℃ under working conditions. Therefore, the axial compression amount of the sealing ring is selected as 0.15 mm, and the working medium pressure is 0. Then, the maximum equivalent stress and maximum contact stress changes of the C-shaped sealing ring at different temperatures between 50 and 300 ℃ are compared. The Ansys simulation analysis results are shown in Fig. 3. It can be seen that during the temperature change process, the maximum equivalent stress of the combined sealing structure is 1608 MPa, and the maximum contact stress is 154 MPa. As the temperature increases, the maximum equivalent stress continues to increase. The maximum contact stress increases to a maximum value of 154 MPa after 100 ℃, and then drops to 138 MPa at 300 ℃, indicating that the sealing performance remains basically stable in the range of 150-250 ℃.
Fig. 3Stress variation curve of metal composite sealing structure with temperature
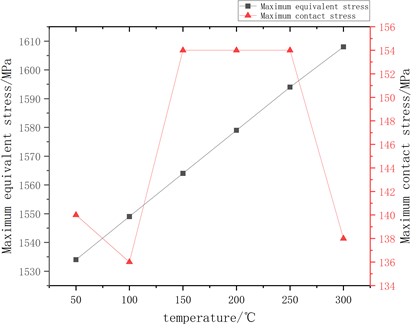
4.2. The effect of working pressure on the sealing performance of metal C-ring
The C-shaped sealing ring is in a high-temperature and pressurized environment during operation, and needs to withstand different working medium pressures. Therefore, it is necessary to study and analyze the impact of working medium pressure on the sealing performance of the sealing ring.
The variation pattern of the maximum stress of the sealing ring under different working pressures (10 MPa, 15 MPa, 20 MPa, 25 MPa, 30 MPa, 35 MPa, 40 MPa) with an initial preload of 0.15 mm and a temperature of 300 ℃ is shown in Fig. 4.
It can be seen that the maximum equivalent stress of the combined sealing structure is 1610 MPa, and the maximum contact pressure is 156 MPa. As the working pressure increases, after 15 MPa, the equivalent stress and contact stress show a trend of first decreasing, then increasing, and then decreasing. At 25 MPa, the equivalent stress and contact stress show their lowest values. Overall, the impact of working pressure on the equivalent stress peak of the combined sealing structure is minimal. Based on the contact stress, it can be inferred that when the working pressure is less than 20 MPa and greater than 30 MPa, the sealing performance basically meets the requirements.
Fig. 4Stress variation curve of metal composite sealing structure with pressure
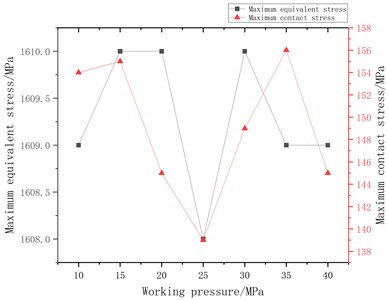
Fig. 5Stress variation curve of metal composite sealing structure with compression amount
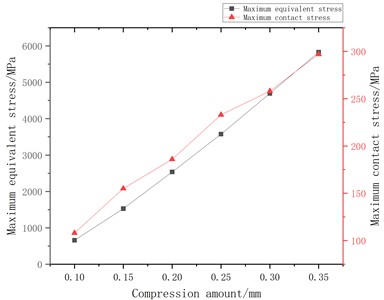
4.3. The effect of compression on the sealing performance of metal C-ring
During the assembly process of the metal sealing ring, sufficient compression is required to ensure contact sealing. During the initial pre tightening compression, the built-in spring metal C-shaped sealing ring is compressed by the bolt acting on the sealing element. The metal C-shaped ring undergoes certain deformation under compression, and the reaction force generated by the deformation causes plastic deformation at the sealing contact surface to compensate for defects such as micro concave convex gaps on the contact surface, thus forming the initial seal. Therefore, the initial pre compression amount of the sealing ring has a significant impact on whether a good seal can be achieved. If the initial pre compression amount is too small, the deformation of the contact surface will not be enough to compensate for the micro unevenness on the contact surface, and micro leakage channels can easily form on the contact surface; On the contrary, if the initial pre compression amount is too large, to a certain extent, the sealing ring will collapse and lose its rebound performance, which is very unfavorable for sealing. Therefore, it is necessary to choose the initial pre compression amount reasonably. To this end, six displacement loads of 0.10 mm, 0.15 mm, 0.20 mm, 0.25 mm, 0.30 mm, and 0.35 mm were applied to the built-in spring metal sealing ring to analyze the impact of compression on sealing performance.
Under different compression amounts (working pressure 0 MPa, temperature 25 ℃), the maximum stress variation of the sealing ring is shown in Fig. 5. It can be seen that the maximum equivalent stress of the sealing ring is 5830 MPa, and the maximum contact stress is 297 MPa. With the increase of the initial compression amount, the equivalent stress and contact stress both show an increasing trend. From the simulation results, it can be seen that the deformation of the structure is more reasonable when the initial compression amount is within the range of 0.15 to 0.25 mm, The sealing performance meets the requirements.
5. Conclusions
1) In this paper, the sealing mechanism and contact characteristics of the metal combined seal structure are described in detail, and a three-dimensional simulation model of the metal combined seal structure is established. The numerical simulation results of the sealing performance of the Geometric modeling under different working conditions are analyzed, and the changing laws of its stress and deformation with external conditions are obtained.
2) As the temperature increases, the maximum equivalent stress of the sealing structure increases linearly. The maximum contact stress remains stable within the temperature range of 150-250 ℃, and the sealing performance meets the requirements. At this point, the sealing performance of the sealing ring improves, while the strength decreases; As the working pressure increases, the maximum equivalent stress of the sealing structure does not change much, and based on the contact stress, it can be inferred that the sealing performance basically meets the requirements when the working pressure is less than 20 MPa and more than 30 MPa; When the initial compression amount is within the range of 0.15-0.25 mm, the maximum contact stress and deformation are more reasonable, and the sealing performance of the sealing ring is the best at this time.
3) The built-in spring metal C-shaped seal ring has good sealing performance. The spiral spring makes the C-shaped seal ring have good resilience, which can better cope with the fluctuations of operating conditions. The silver coating makes the contact interface between the sealing surface and the seal ring well sealed. The alloy layer plays the role of protecting the silver layer and stably transmitting Contact force.
References
-
K. Ma, K. Guan, and R. Cai, “Compression recovery performance of spring energized C-rings,” Proceedings of the Institution of Mechanical Engineers, Part E: Journal of Process Mechanical Engineering, Vol. 230, No. 1, pp. 18–25, 2016.
-
D. Yuanyuan, L. Ying, and Z. Liping, “Numerical simulation of sealing behavior of C-ring for reactor pressure vessel,” Journal of Nuclear Engineering and Radiation Science, Vol. 2, No. 4, Oct. 2016, https://doi.org/10.1115/1.4033551
-
G. M. Jacobsen, J. D. Stone, H. E. Khalifa, C. P. Deck, and C. A. Back, “Investigation of the C-ring test for measuring hoop tensile strength of nuclear grade ceramic composites,” Journal of Nuclear Materials, Vol. 452, No. 1-3, pp. 125–132, Sep. 2014, https://doi.org/10.1016/j.jnucmat.2014.05.002
-
J. Yamabe, A. Koga, and S. Nishimura, “Failure behavior of rubber O-ring under cyclic exposure to high-pressure hydrogen gas,” Engineering Failure Analysis, Vol. 35, pp. 193–205, Dec. 2013, https://doi.org/10.1016/j.engfailanal.2013.01.034
-
H. Sassoulas, L. Morice, P. Caplain, C. Rouaud, L. Mirabel, and F. Beal, “Ageing of metallic gaskets for spent fuel casks: Century-long life forecast from 25,000-h-long experiments,” Nuclear Engineering and Design, Vol. 236, No. 22, pp. 2411–2417, Nov. 2006, https://doi.org/10.1016/j.nucengdes.2006.02.008
-
D. Wolff et al., “Safety aspects of long-term dry interim storage of type-b spent fuel and HLW transport casks,” Packaging, Transport, Storage and Security of Radioactive Material, Vol. 15, No. 3-4, pp. 207–214, 2004.
-
N. Sarawate et al., “Characterization of metallic W-seals for inner to outer shroud sealing in industrial gas turbines,” in ASME Turbo Expo 2012: Turbine Technical Conference and Exposition. American Society of Mechanical Engineers, pp. 1855–1862, 2012.
-
R. Kumar et al., “Effects of pressure gradients on laser beam propagation through an optical window for tokamak plasma diagnostics,” Fusion Science and Technology, Vol. 61, No. 1, pp. 51–56, 2012.
-
X. J. Cui, “Research progress and sealing mechanism analysis of metal sealing technology,” (in Chinese), Petroleum Machinery, pp. 102–105, 2011.
-
Q. Q. Li, “Simulation analysis and optimization of sealing performance of built-in spring metal C-ring,” (in Chinese), Beijing University of Chemical Technology, 2017.
-
X. G. Li, R. L. Cai, and J. W. Hang, “Development of "C" shaped sealing ring for reactor pressure vessel,” (in Chinese), Pressure Vessel, Vol. 30, No. 5, pp. 74–79, 2013.
-
X. H. Jia et al., “Analysis on the mechanical and sealing properties of metallic C-ring,” (in Chinese), Lubrication Engineering, Vol. 39, No. 11, pp. 1–5, 2014.
About this article
The authors have not disclosed any funding.
The datasets generated during and/or analyzed during the current study are available from the corresponding author on reasonable request.
The authors declare that they have no conflict of interest.