Abstract
It is significant to promote reliability testing and assessment research of hydraulic cylinder which is the basis to improve reliability of the cylinder and pertinent machine system. In this study, a new comprehensive testing system for the reliability research of hydraulic cylinder has been developed, reliability testing of a hydraulic cylinder for precision production has been conducted using the test bench. With the obtained test data, parameters of the Weibull distribution function of the cylinder are estimated by means of the least square estimation method, thus, reliability distribution function and lifetime values of the cylinder under normal stress level are ultimately obtained. The developed new test bench and performed testing and analysis in this study would provide an excellent platform and reliability assessment approach for industry hydraulic cylinders.
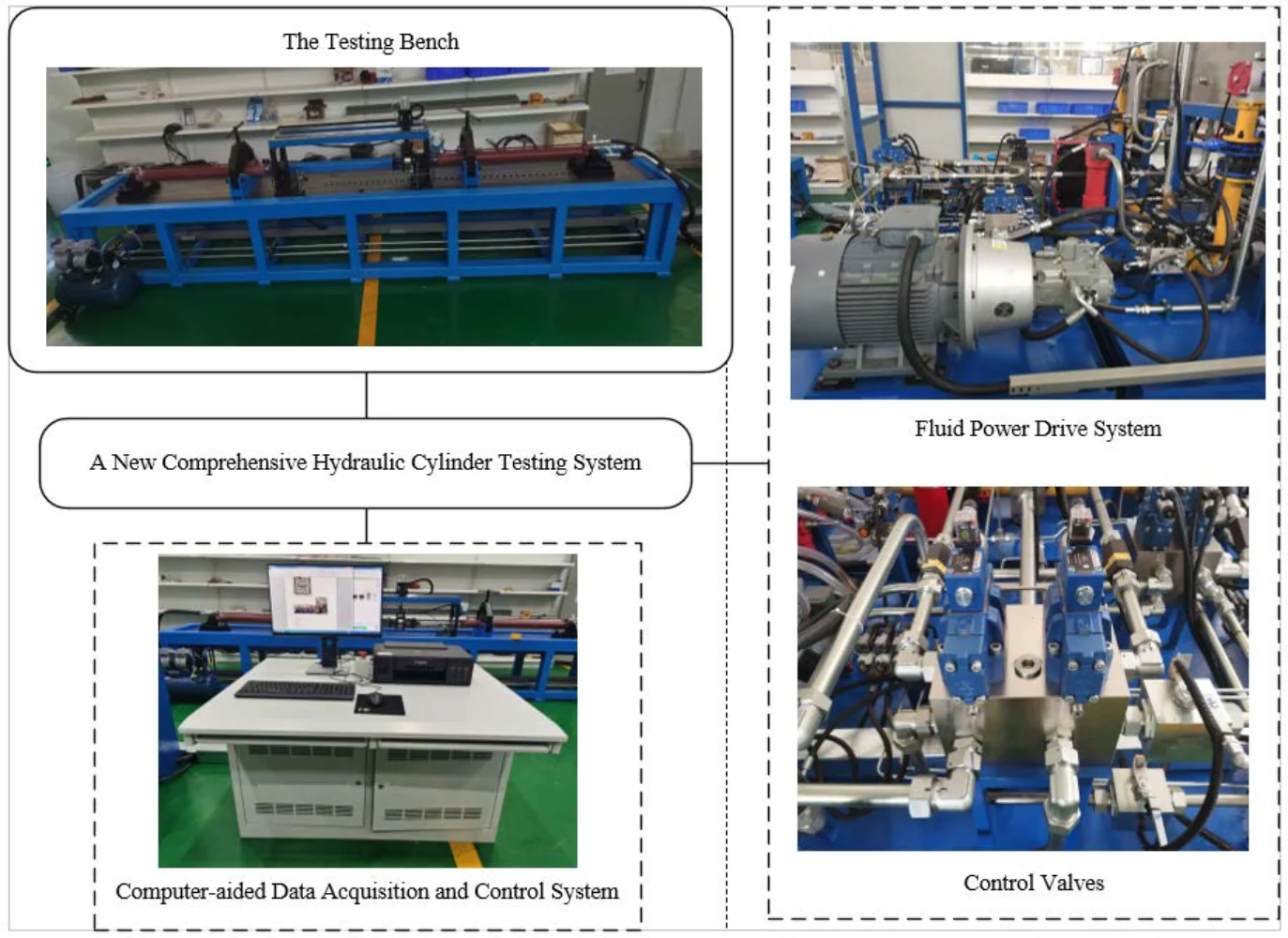
1. Introduction
Hydraulic cylinders are crucial components in modern high-standard equipment systems, so it is meaningful to improve reliability of the cylinders, however, reliability testing and assessment of any cylinder is the basis of reliability engineering in its whole life cycle.
So far, many previous works have studied the ordinary approach and devices [1, 2] for type testing or predelivery testing of hydraulic cylinders, research works addressing reliability testing, analysis and new equipment development for hydraulic cylinder need to be promoted. Li et al. [3] and Han et al. [4] have proposed accelerated life test method and/or calculation model for their cylinders; Altamura et al. [5] have deduced reliability model for tubular component with surface flaws and applied that model for life prediction of construction machinery cylinders; Kobzov et al. [6] have setup a stability criterion for reliability design of hydraulic cylinder under longitudinal-transverse loads; Zeng et al. [7] have made low-cost maintenance plans for excavator cylinders by reliability and failure modes analysis.
In this work, a new comprehensive test bench for the reliability research of hydraulic cylinder has been developed, then reliability testing of a hydraulic cylinder for precision production has been conducted using the test bench. With the obtained test data, parameters of the Weibull distribution function of the cylinder are estimated by means of the least square method, thus, the reliability distribution function and life values of the cylinder are ultimately obtained. The developed new test bench and performed testing and analysis in this study would provide a meaningful platform and reliability assessment approach for hydraulic cylinders.
2. Development of a new comprehensive hydraulic cylinder testing system
A new comprehensive testing system with power recovery for the reliability research of hydraulic cylinder has been developed [8], as shown in Fig. 1. The new testing system consists of a mechanical testing bench on which the hydraulic cylinder is mounted to undertake inspection and characteristics measurement, a fluid power drive system with variable pump control and valve controls, and a computer-aided data acquisition and control system with sensors, PLC and instruments, modularization conception is adopted in design and integration of the whole testing system.
Fig. 1The developed new comprehensive hydraulic cylinder testing system
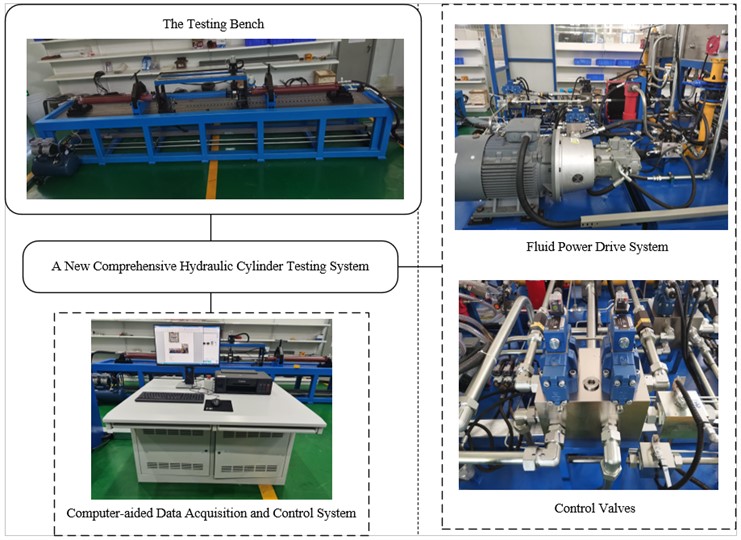
With the new test bench, not only normal [9] type testing or predelivery testing can be performed, but also reliability testing under normal or accelerated stress level can be conducted. In any reliability test, the user could compile and control the loading laws according to the real load spectrum of any cylinder product, the available loading stresses could be loaded in the testing process include working pressure, working velocity, oil temperature and side load of the cylinder. The developed new testing system has advantages in obvious energy saving, high test precision, safety and reliability.
3. Reliability testing of a hydraulic cylinder for precision production
Reliability testing of a hydraulic cylinder for precision production is conducted using the developed new testing bench, as demonstrated in Fig. 2. In the testing process, the cylinder is driven to and fro under desired pressure and velocity, a side load simulating the real situation in application is also applied to the rod by a moving mechanism with pneumatic actuation during reciprocating motion of the cylinder, a load sensor and a displacement sensor are respectively devised to measure dynamic forces and motions of the cylinder.
Fig. 3 illustrates some of the collected real-time curves during reliability testing of the hydraulic cylinder. Fig. 3(a) shows the pressure-drop curves (three tests) of the cylinder due to oil leakage under very high working pressure conditions, it indicates that the pressure would drop by 5 %-6 % in a five- minute-high-pressure holding process. Fig. 3(b) shows dynamic working pressure profiles in the cylinder chambers, and it indicates that the pressure of the non-rod chamber remains constant, while that of the chamber with rod changes to obtain pressure difference between the two chambers, the pressure difference would make the cylinder move, in other words, the hydraulic cylinder being tested is driven by low-pressure oil, thus, the new testing system has the advantage of power recovery and remarkable energy saving effect.
Fig. 2A hydraulic cylinder for precision production is under reliability testing
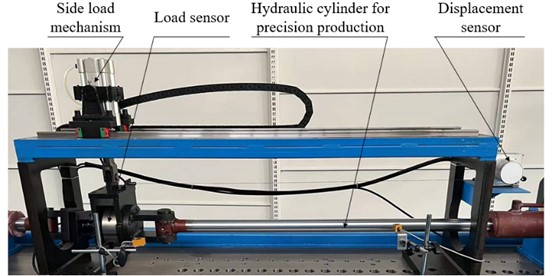
Fig. 3Some of the collected real-time curves during reliability testing of the hydraulic cylinder
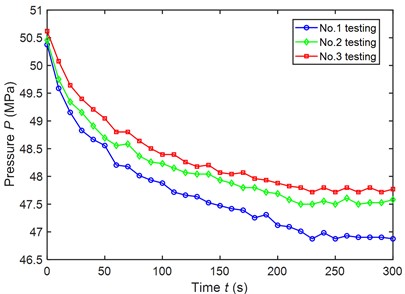
a) Pressure-drop curves of the cylinder due to oil leakage
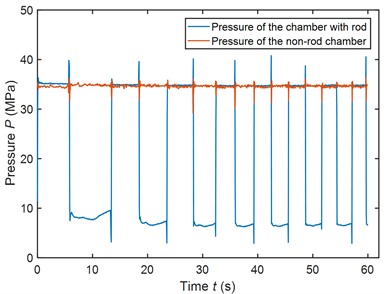
b) Working pressure profiles in the cylinder chambers
Table 1 collects reliability testing data of twenty-two samples of the hydraulic cylinder product, which includes the sample number and pertinent lifetime value of each sample.
Table 1Reliability testing data of the hydraulic cylinder samples
Sample number | Lifetime value (104 Cycles) | Sample number | Lifetime value (104 Cycles) |
1 | 20.67 | 12 | 62.80 |
2 | 22.92 | 13 | 67.34 |
3 | 31.19 | 14 | 69.24 |
4 | 35.43 | 15 | 70.21 |
5 | 42.72 | 16 | 74.39 |
6 | 45.60 | 17 | 79.12 |
7 | 48.99 | 18 | 83.10 |
8 | 51.00 | 19 | 88.94 |
9 | 52.66 | 20 | 93.12 |
10 | 55.12 | 21 | 97.84 |
11 | 57.56 | 22 | 105.92 |
4. Reliability assessment of the hydraulic cylinder
In the first Chinese national standard for basic hydraulic component reliability assessment [10], the law of Weibull distributionis recommended for description of failure mode and reliability distribution of fluid power components, thus, failure density function of the hydraulic cylinder could be expressed as the following two-parameter [10, 11] Weibull function:
where and are respectively shape parameter and scale parameter of the Weibull function, is lifetime of the cylinder.
Therefore, reliability function and failure rate function of the cylinder could be deduced as:
In addition, the average lifetime, the reliability lifetime, the characteristic lifetime and the medium lifetime of the cylinder could also be respectively deduced as:
The least square estimation approach is firstly used to verify if the testing data in Table 1 obeys the law of Weibull distribution or not. As demonstrated by Fig. 4, both of the Weibull probability distribution (Fig. 4(a)) and fitting effect of Weibull function (Fig. 4(b)) show that the testing data in Table 1 approximatively distributes along a straight line, which means that the failure testing data truly obeys the law of Weibull distribution.
Fig. 4Verification of obeying the Weibull distribution of the testing data
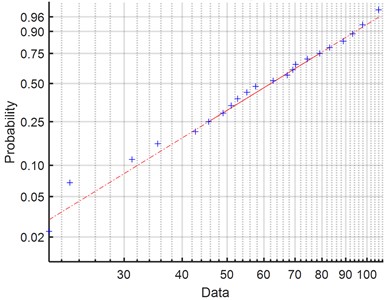
a) Weibull probability distribution of the testing data
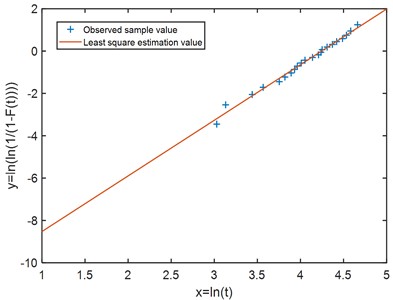
b) Fitting effect of Weibull function of the testing data
Estimation of the parameters and in Eq. (1-7) is performed by using the testing data in Table 1, and the results are: the shape parameter 2.6272, the scale parameter 69.7078.
Thus, the reliability function and the failure rate function of the cylinder could be respectively deduced as:
Thus, curves of the reliability function and the failure rate function can be finally obtained, as demonstrated in Fig. 5. Fig. 5(a) shows that reliability of the cylinder would decline slowly before 25-30×104 cycles and drop sharply between 30-80×104 cycles, however, the reliability would decline slowly again after 80×104 cycles. Fig. 5(b) shows that failure rate of the cylinder would also go up nonlinearly with increasing of working cycles of the cylinder. The assessed lifetimes of the hydraulic cylinder are summarized in Table 2.
Fig. 5Reliability distribution characteristics of the hydraulic cylinder
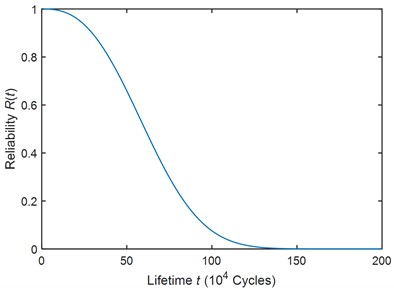
a) The reliability function
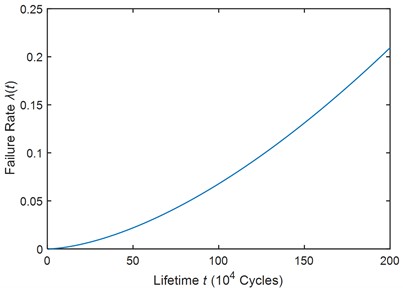
b) The failure rate function
Table 2Predicted lifetimes of the hydraulic cylinder
Lifetime | Lifetime value (104 Cycles) |
The average lifetime | 61.9425 |
The reliability lifetime | 22.0508 |
The characteristic lifetime | 69.7078 |
The medium lifetime | 60.6385 |
5. Conclusions
1) A new comprehensive testing system for the reliability research of hydraulic cylinder has been developed, with the new test bench, not only normal type testing or predelivery testing can be performed, but also reliability testing under normal or accelerated stress level can be conducted.
2) Reliability testing of a hydraulic cylinder for precision production is conducted and valuable failure data is collected. Testing results indicate that working pressure of the cylinder would drop by 5 %-6 % in a five-minute-high-pressure holding process, the dynamic working pressure profiles in the cylinder chambers also verify that the testing system has the advantage of power recovery and remarkable energy saving effect.
3) Reliability analysis of the hydraulic cylinder is performed, the obtained results demonstrate that reliability of the cylinder would decline slowly before 25-30×104 cycles, drop sharply between 30-80×104 cycles and decline slowly again after 80×104 cycles, in addition, failure rate of the cylinder would also go up nonlinearly with increasing of working cycles of the cylinder.
4) The developed new test system and performed testing and analysis in this study would provide an excellent platform and reliability assessment approach for industry hydraulic cylinders.
References
-
Y. Hu, J. K. Hu, Z. P. Wu, Y. Cheng, and F. He, “Design and research on hydraulic cylinder-testing for power-recycling,” (in Chinese), Modern Manufacturing Engineering, Vol. 3, pp. 130–134, 2017, https://doi.org/10.16731/j.cnki.1671-3133.2017.03.023
-
Y. Jin, M. H. Jiang, X. He, Y. M. Xia, and C. L. Luo, “Development and experimental research of measurement and control platform for integrated performance of hydraulic cylinder,” (in Chinese), Journal of Hefei University of Technology, Vol. 39, No. 9, pp. 1163–1168, 2016.
-
Y. Q. Li, C. H. He, W. D. Zhang, and Q. J. Liu, “Research on accelerated test method of hydraulic cylinder,” (in Chinese), Hydraulics Pneumatics and Seals, Vol. 4, pp. 84–88, 2022, https://doi.org/10.3969/j.issn.1008-0813.2022.04.02
-
G. H. Han and Y. L. Fu, “A study on the accelerated life test for hydraulic cylinders,” Advanced Materials Research, Vol. 199-200, pp. 630–637, Feb. 2011, https://doi.org/10.4028/www.scientific.net/amr.199-200.630
-
A. Altamura and S. Beretta, “Reliability assessment of hydraulic cylinders considering service loads and flaw distribution,” International Journal of Pressure Vessels and Piping, Vol. 98, pp. 76–88, Oct. 2012, https://doi.org/10.1016/j.ijpvp.2012.07.006
-
D. Kobzov, S. Repin, and V. Gubanov, “Criterion of stability of hydraulic cylinder and method of increasing its reliability under longitudinal-transverse loads,” E3S Web of Conferences, Vol. 164, p. 08022, 2020, https://doi.org/10.1051/e3sconf/202016408022
-
Q. Zeng, W. Liu, L. Wan, C. Wang, and K. Gao, “Maintenance strategy based on reliability analysis and FMEA: A case study for hydraulic cylinders of traditional excavators with ERRS,” Mathematical Problems in Engineering, Vol. 2020, pp. 1–11, Nov. 2020, https://doi.org/10.1155/2020/2908568
-
W. Wang and K. Yan, “Development of a new testing system for reliability assessment of hydraulic cylinder,” in 2022 5th World Conference on Mechanical Engineering and Intelligent Manufacturing (WCMEIM), Nov. 2022, https://doi.org/10.1109/wcmeim56910.2022.10021522
-
“GB/T15622-2005 Hydraulic fluid power – Test method for the cylinders,” (in Chinese), General Administration of Quality Supervision, Inspection and Quarantine of the People’s Republic of China, Standardization Administration of the People’s Republic of China, 2005.
-
“GB/T 35023-2018 Methods to assess the reliability of hydraulic components,” (in Chinese), State Administration for Market Regulation of the People’s Republic of China, Standardization Administration of the People’s Republic of China, 2018.
-
D. T. O. Patrick and K. Andre, Practical Reliability Engineering. West Sussex, UK: John Wiley & Sons, 2012.
About this article
The authors have not disclosed any funding.
The datasets generated during and/or analyzed during the current study are available from the corresponding author on reasonable request.
The authors declare that they have no conflict of interest.