Abstract
In view of the difficult construction problem of narrow roadway drilling rig, the design plan and technical requirements of the drilling rig were formulated, and the narrow-body double-turn track crawler was developed. The key technologies of the luffing device, the crawler body and the integrated operating valve were introduced. Research and verification of the reliability of the rig through field tests. The rig moves quickly and easily; The cylindrical column-double hydraulic drive turntable luffing device has compact structure; no rubber chuck have simple structure and convenient use which can save maintenance and cost; integrated operating valve have small size and less rubber tube Pipeline, which can be easy to repair; the open large stroke holder have the small width and large opening, which make it high reliability and good neutrality. Development of narrow double turntable crawn rigs, shorten the auxiliary operation time of the rig in a narrow roadway, improves the safety of on-site workers, providing technical support for improving the construction efficiency of narrow road rigs.
1. Introduction
The coal resources of China are rich in reserves, but coal mining geological conditions are complex. Many mining areas have a lot of problems, such as soft coal seam, low permeability, large gas content and high gas pressure. Therefore, gas extraction is particularly important [1-4]. As an essential equipment for coal mine gas drainage, full hydraulic tunnel drilling rig has the advantages of reasonable structure, advanced technology, strong process adaptability, safe and reliable.
Crawler drilling rig has been recognized by the majority of customers because of its advantages of convenient relocation and rapid stability. However, the size of the integral crawler drilling rig is large [5, 6], which cannot be used in some narrow tunnel. Therefore, it is necessary to develop an integral crawler drilling rig that can adapt to narrow roadways and carry out cross-belt construction.
2. Overall design
The drilling rig is mainly used for drilling construction of double-layer or multi-layer holes in narrow roadways in coal mines, gas drainage holes in adjacent layers, through-layer holes and exploration and drainage holes. The overall design scheme of drilling rig mainly has the following requirements:
1) The drilling rig is integrated, the structure is compact, the mobility is high, the automation degree is high, which can adapt to most roadways;
2) The luffing device is hydraulically driven, the angle range is large, the adjustment is fast and flexible, the process is stable and reliable, the labor intensity of workers is low;
3) Optimize the key components of the drilling machine to upgrade or innovate, in order to better satisfying on-site construction needs.
In view of the above requirements, the ZDY3500L (A) narrow-type double-turn track crawler drilling rig is developed. The main technical parameters of the drilling rig are shown in Table 1.
Table 1Main technical parameters of narrow-type double-turn track crawler drilling rig
Category | Parameter |
Diameter of spindle hole/ mm | 75 |
Rated torque / Nm | 3500~850 |
Rated speed / r/min | 55~200 |
Axis-angle / ° | –90~+90 |
Azimuth angle / ° | –90~+90 |
Drilling height of drilling rig / mm | 1250~1900 |
Rated feed / pullout force / kN | 70/102 |
Cylinder feeding/lift stroke / mm | 600 |
Motor power / kW | 45 |
3. The key technologies research
After determining the overall scheme of the drilling rig, this paper mainly studies the key technologies of the luffing device, tracked body and integrated operation valve.
3.1. Cylindrical column-double hydraulic drive turntable luffing device
A cylindrical column-double hydraulic drive turntable luffing device is developed. The luffing device adopts two cylindrical hydraulic cylinder (as shown in Fig. 1), which are used as both the upper stable cylinder and the sliding rail for adjusting the opening height. The structure is simple, and the space is small. The feed device has small friction and good orientation in the lifting process. The brake pressure block is designed on the angular turntable, and the feed device and the right connecting plate component are pressed by the brake pressure block to reduce the sloshing of the feed device during construction.
Fig. 1Circular column double liquid drive turntable unit: 1 – azimuth rotary reducer; 2 – left connection plate assembly; 3 – left column assembly; 4 – lift cylinder; 5 – right column assembly; 6 – right connection plate assembly; 7 – pressure block; 8 – feed device; 9 – axis-angle rotary reducer
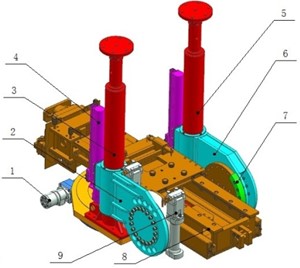
The column cylinder in the luffing device not only bears the axial force, but also bears the bending moment caused by the radial force and the feed force, and the stress is complicated.
Therefore, the finite element software is used to analyze the stress of the column cylinder, simulate the stress of the part under the combined action of the axial force and the radial eccentric load, and judge the stress of the part. First, the three-dimensional model of the column cylinder is established by the three-dimensional design software UG, and the model is simplified under the premise of calculation accuracy, and the model is introduced into finite element analysis software for finite element analysis (as shown in Fig. 2).
According to Fig. 2, the maximum stress of the column cylinder occurs at the contact between the column and the rib plate. The maximum stress is 270 MPa, and the permissible stress is 355 MPa, which satisfy the use requirement. Theoretical analysis, the largest stress of the column cylinder is at the connection between the bottom ribs and the cylinder, which is the most prone to damage of the whole parts, consistent with the finite element analysis.
Fig. 2Pressure cylinder finite element analysis stress map
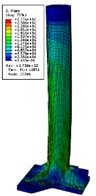
3.2. Narrow-body track
A narrow-body track having a lateral telescopic stabilizing device is developed (as shown in Fig. 3). The track width is 950 mm, which can be adapted to the multi-purpose drilling construction of the narrow roadway; four lateral telescoping stabilizing devices can be completely retracted during walking, which can adjust the width in the range of 950 mm to 1390 mm. This kind of design can adjust the range of high stability and no need for manual auxiliary flipping and fixation; telescopic coats are arranged up and down which welded to the vehicle body platform, and the telescopic cylinder pushes the telescopic laundry along the telescopic coat.
Fig. 3Narrow-body track: 1 – telescopic inner sleeve; 2 – telescopic outer sleeve; 3 – telescopic hydraulic cylinder; 4 – lower stabilizing hydraulic cylinder
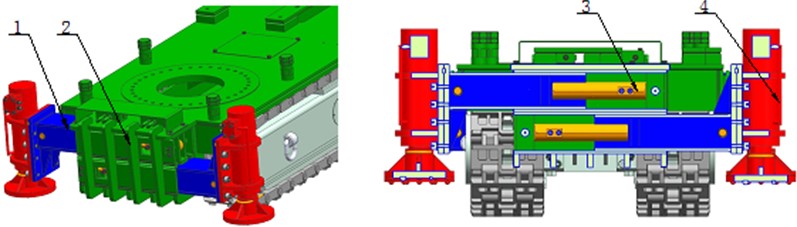
Fig. 4One-piece operating valve
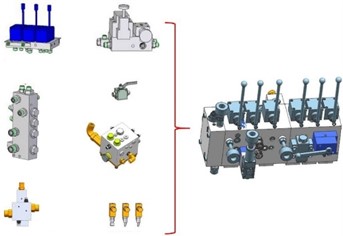
3.3. One-piece operating valve
The integrated operating valve (as shown in Fig. 4) includes the four-way valve oil board assembly, the sub-pump oil board assembly, the assembly of the oil board assembly, the turnover oil board assembly, anti-oil Dynamic head decline module, cut-off valve, seven functional valve groups, etc. There is no pipe connection in the integrated operating valve, compared with traditional consumptions, the number of operating tables is reduced from 48 to 18, which reduce the leak point and enhance the reliability of the drilling machine and convenient for post- maintenance and maintenance. The integrated operating valve share the same operation order and mode with the drilling machine of our hospital, which make the workers are easy to promote. The operation desk is integrated with the anti-power head slip module, preventing the power head in the main angle, and improves the safety of the drilling machine.
3.4. Pump station
The pump station is the power source of the drilling rig, providing matching power for each actuator. The most important aspect in the pump station is the selection of motor power. Based on the different actions of the drilling rig, in order to make the hydraulic system has higher efficiency and lower energy consumption, we make a decision to use double pump. The system pressure and flow rate are determined according to the action requirements of each actuator, from which the hydraulic pump input power can be calculated:
where: – rated pressure of the hydraulic pump, – rated flow rate of the hydraulic pump, – volumetric efficiency of the hydraulic pump.
The drilling rig ultimately determines the main pump pressure as 25 MPa with a displacement of 71 ml/r; the secondary pump pressure as 21 MPa with a displacement of 10 ml/r. Taking the volumetric efficiency of the pump as 0.8, based on Eq. (1), we can calculate:
Total power is 54.36 kW, therefore select 55 kW motor.
During the operation of the pumping station, oil contamination often occurs, such as emulsification or deterioration and so on, which will affect the service life of the key components such as pumps and valves in the drilling rig. Therefore, we require the use of regular replacement in the process of oil filter, oil filter and other accessories, generally require continuous use of more than 3 months to be replaced. At the same time, require the use of 46 or 68 anti-wear hydraulic oil during the use, hydraulic oil needs to be added to the two-thirds of the level meter, and filled the hydraulic oil through the air filter, this can effectively reduce oil pollution.
3.5. The test of drilling rig
The drilling rig was tested in No. 13 coal mine of Shenma Group of Pingdingshan Coal Mine, China. Drill 229 holes and the total depth of drilling is 4797 m, he average footage per shift was 67 m, the maximum amount is 128 m, the average of the rig is 3600 meters / month. The stand-alone catering is 60 % compared to ordinary split rigs, and 1 employment is reduced each class.
The test results prove that the size of drilling rig is small which can be very good to adapt to a variety of laneways; the steady angle is convenient and fast and high mechanization; the spindle inclination angle and the azimuth adjustment are wide, the horizontal opening is high, which can meet the site construction needs.
4. Conclusions
1) The cost of narrow-type double-turn track crawler drilling rig is low, and the rig moves quickly and easily. It can be used in wide range of applications such as gas extraction, exploration of water, geological construction exploration, coal grade water, top floor grout, large diameter pressure relief pressure.
2) The cylindrical column-double hydraulic drive turntable luffing device has compact structure; no rubber chuck have simple structure and convenient use which can save maintenance and cost; integrated operating valve have small size and less rubber tube Pipeline, which can be easy to repaird; the open large stroke holder have the small width and large opening, which make it high reliability and good neutrality.
3) Development of narrow double turntable crawn rigs, shorten the auxiliary operation time of the rig in a narrow roadway, improves the safety of on-site workers, providing technical support for improving the construction efficiency of narrow road rigs.
Narrow tunnels can only be constructed using small volume split drilling rigs, which are difficult to relocate, low on-site construction efficiency, high labor intensity of workers and low safety. The development of narrow-type double-turn track crawler drilling rig has effectively solved the problems. The drilling rig has a small width and compact structure, and has certain advantages in narrow tunnels underground coal mines.
The drilling rig has all-round angle adjustment, strong adaptability to the tunnel, stable and easy displacement, high construction efficiency, and certain advantages in comprehensive outburst prevention of coal seam areas, filling the gap of narrow tunnel crawler drilling rig, thus promoting the improvement of the technical level of crawler tunnel drilling rig in this industry.
References
-
F. Zhang, “Analysis of the ways of modern improvement coal mines in gas effect,” Energy and Energy Saving, Vol. 10, 2018.
-
N. Lu et al., “The current situation and development trend of full hydraulic drilling machine under coal mine,” Coal Mine Machinery, Vol. 32, No. 3, pp. 1–3, 2011, https://doi.org/10.3969/j.issn.1001-1986.2019.01.001
-
H. L. Tian, “Development and application of gas pumping turning tolerel drilling rigs,” Coalfield Geology and Exploration, Vol. 36, No. 5, pp. 77–80, 2008.
-
Y. F. Yao, “Independent walking hydraulic system of gas paddation split track drilling rigs,” Coalfield Geology and Exploration, Vol. 42, No. 3, pp. 105–108, 2014.
-
Z. Liu, “Thertence of ZDY4300LP type track rig,” Coal Mine Safety, Vol. 49, No. 3, pp. 102–108, 2018.
-
Y. F. Yao et al., “Development and application of large torque two-body crawler rig in Song soft coal seam,” Coal Mine Machinery, Vol. 36, No. 10, pp. 215–218, 2015.
About this article
The authors have not disclosed any funding.
The datasets generated during and/or analyzed during the current study are available from the corresponding author on reasonable request.
The authors declare that they have no conflict of interest.