Abstract
Many driving schools adopt existing vehicle platform for integration with electric powertrains to reduce fuel consumptions. The special car consists of a conventional manual transmission but a driving motor for driving instruction. This modification can create unique challenges for noise, vibration and harshness (NVH) refinement. This paper presents an experimental NVH evaluation of the special electric vehicle, which lays more emphasis on transient operations. The powertrain mounting system, the driving motor and the transmission are tested and their NVH performances are analyzed at different transient modes. The results indicate that the transmission and the final drive contribute to the medium frequency range of interior noise due to the missing masking of the internal combustion engine. In addition, the vibration isolation performance of electric powertrain mounting system is assessed by calculating transmissibility characteristics of the powertrain mounts. It is pointed out that the transmissibility of 20 dB, which means ninety percent of the vibration energy has been reduced, may no longer be suitable for an electric powertrain mounting system. Furthermore, interior vibration behaviors such as the acceleration amplitude of seat track should be subordinated to the assessment of the powertrain mounting system.
1. Introduction
The severe traffic emission regulations and depleting supply of fossil fuels have spurred automotive manufactures to search alternative solutions. Electric powertrain is getting widely concerned as an efficient and clear power. An electric motor which is coupled to the driveline through an appropriate transmission is integrated into the conventional vehicle platform.
Noise, vibration and harshness (NVH) behaviors become the principal consideration for potential consumers due to the public’s high reputation. However, wind, road and accessory noise become more prominent without engine-noise masking. That the lighter electric powertrain cut down the powertrain rigid body modes can motivate the resonance vibration easily. Fig. 1 gives a specific conception of electric vehicle’s noise distribution at different speeds. Engine is always the dominant noise source in a conventional powertrain. With regard to electric vehicle (EV), road noise becomes audible at low speed, and noise motivated by the motor has obvious effect at wide speed range. High frequency wind noise gets noticeable at high speed.
Fig. 1Nosie level description at different vehicle speed
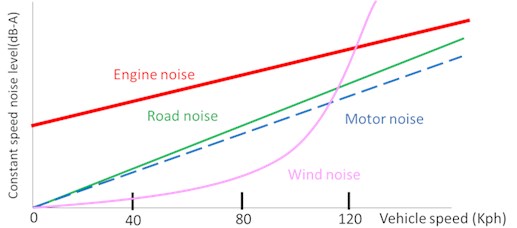
A considerable amount of published studies has discussed and analyzed the noise and vibration phenomena of an electric car. It is widely accepted that the electric powertrain can be significantly quieter than the internal combustion engine (ICE) power unit composed of the air intake and exhaust system [1]. Several studies have revealed that EV related special NVH issues need more attention when adapting conventional vehicle platforms for integration with electric powertrain [2]. Auxiliary systems such as transmissions and battery cooling could generate high-pitched noise at low speeds [3]. Magnetic noise radiated by stator was evaluated according to the Maxwell pressure [4].
This paper seeks to address NVH problems of a special electric vehicle from the experimental point of view, and lays more emphasis on behaviors of transient operation modes. The study focuses on the interior noise and the electric powertrain mounting system of a special electric car. Some unique NVH problems will be discussed for drawing researchers’ attention when adopting existing vehicle platform for integration with electric powertrains.
2. NVH tests on the EV
Fig. 2 shows the schematic diagram of the test EV. The vehicle’s electric powertrain located in the front of the vehicle consists of a driving motor, a manual transmission, a final drive and a drive axle. Six triaxial accelerometers are attached at active and passive sides of three powertrain mounts. Another two accelerometers are attached at the steering wheel and seat track of the driver.
Fig. 2Schematic diagram of the transducer set-up
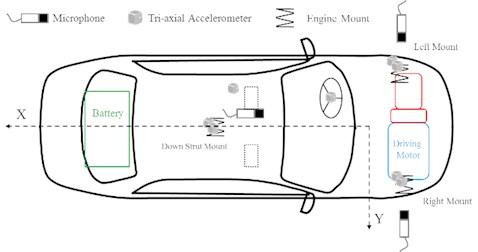
One microphone is installed in the driver’s right ear (DRE) side. Another two near the left and right wheel are 0.5 m away from the car body and the ground. The tests are performed in the semi-anechoic room with a low-noise chassis dynamometer. An LMS SCADAS III data acquisition system and LMS Test. lab 11b software is used for data acquisition and post-processing. Several representative transient testing conditions are selected as follows with reference to Table 1.
Table 1Test conditions and description
Test condition | Description |
Run up in neutral | The vehicle is powered on and stopped; the engine runs up |
2nd gear POT | Part-load acceleration of vehicle in the 2nd gear |
2nd gear WOT | Full-load acceleration of vehicle in the 2nd gear |
3rd gear WOT | Full-load acceleration of vehicle in the 3rd gear |
3. Electric powertrain noise description
Interior noise at various frequencies is shown below in the context of various testing conditions. Fig. 3 shows the Spectral map of drivers’ right ear under the condition of part-load acceleration of vehicle in the 2nd gear. The figure focuses on the low frequency range below 500 Hz. The interior noise in the 7.84th order is much higher in a range between 1100 rpm and 1250 rpm. And the 153 Hz component of the noise is dominant in the case. Obviously, the driving motor’s electro-magnetic orders are the main source at the low frequency range.
Fig. 3The color map of the interior noise
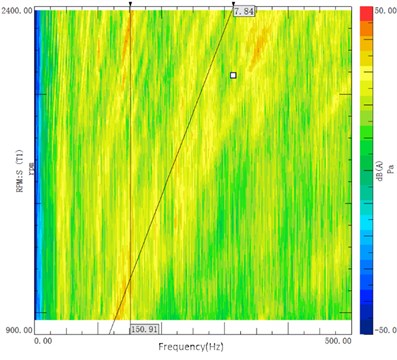
Due to the missing masking of the internal combustion engine, the transmission noise becomes more prominent. The transmission and the final drive contributes to the medium frequency noise range. Fig. 4 gives an explicit comparison between the 2nd gear wide open throttle (WOT) condition and the 3rd gear WOT condition. To be noted that the 146.9 Hz components of the noise which are evoked by the driving motor are remarkable in both conditions. The 3rd gear transmission induced interior noise is significantly higher than that of the 2nd gear condition, resulting in up to 5 dB of difference testing modes under same full load conditions. Fig. 5 shows the sound pressure levels of all the testing conditions and the transmission’s influence to the interior noise can be observed as below.
Fig. 4The color map of the interior noise at the 2nd and 3rd gear WOT
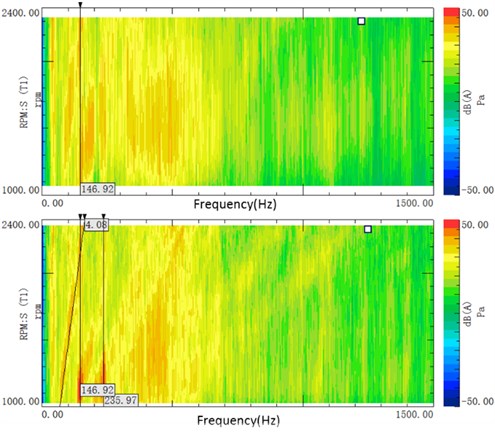
4. Powertrain mount performance evaluation
In order to evaluate the vibration isolation performance of electric powertrain mounting system, accelerometers have been attached in the engine side and the body side. Fig. 6 shows the motor and transmission side mounts’ acceleration signal of the vertical direction at the 3rd gear WOT testing mode.
Fig. 5Comparison of Sound pressure level at different transient modes
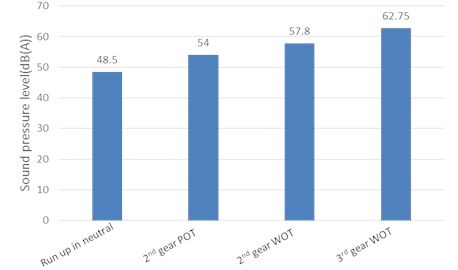
Fig. 6The motor and transmission side mounts’ acceleration signal
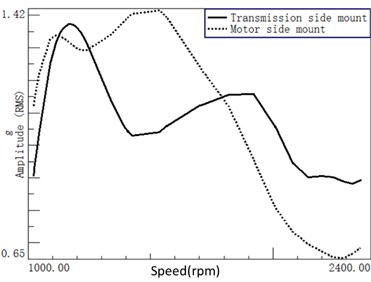
Fig. 7The transmissibility of the three mounts
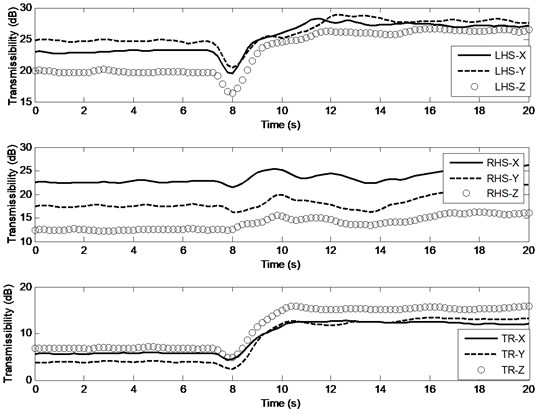
It’s denoted that the vibration of the motor side mount is lower than that of the transmission side in some speed ranges which is quite different from the combustion engine powertrain system. And in the high speed range, the acceleration of transmission side mount becomes prominent.
In assessing a new powertrain mounting system, the traditional way is to calculate transmissibility characteristics of the powertrain mounts. Fig. 7 gives the transmissibility of the three mounts at the run up in neutral testing mode.
When evaluating a traditional engine powertrain mounting system, the transmissibility of 20 dB, which means ninety percent of the vibration energy has been isolated, is regarded as a benchmark index of a satisfactory mounting system. However, it should be pointed out that the vibration of the electric powertrain is sufficient small than conventional engine powertrain system. So, it is unreasonable to assess the electric powertrain mounting system with the old standard. Furthermore, inside vibration level of the car such as the seat track and steering wheel should be incorporated into the evaluation process. Fig. 8 give the time domain vibration of the driver seat track and the steering wheel respectively at the same run up in neutral testing mode.
Fig. 8(a) and Fig. 8(b) illustrate the inside vibration level is quite small despite the fact that the transmissibility of the powertrain mounting system reveals not so good isolation performance.
Fig. 8The time domain vibration of a) the driver seat track and b) the steering wheel
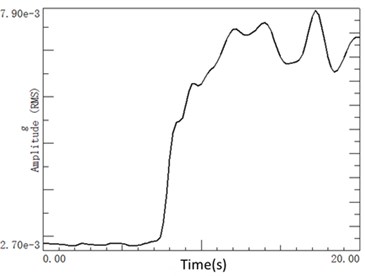
a)
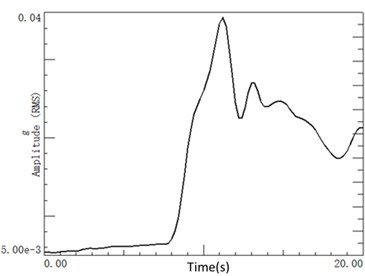
b)
5. Conclusions
The study investigates a special electric car to evaluate the NVH behaviors of a driving motor coupled with a conventional powertrain system. An experimental NVH assessment has been conducted at different transient testing modes. The results indicate that the transmission and the final drive contribute to the medium frequency interior noise range due to the missing masking of the internal combustion engine. Further, the vibration isolation performance of electric powertrain mount system is assessed by calculating transmissibility characteristics of the powertrain mounts. It is pointed out that the transmissibility of 20 dB, which means ninety percent of the vibration energy has been reduced, may no longer be suitable for an electric powertrain mounting system.
References
-
Shin E., Ahlswede M., Muenzberg C., Suh I., et al. Noise and vibration phenomena of on-line electric vehicle. SAE Technical Paper 2011-01-1726, https://www.doi.org/10.4271/2011-01-1726, 2011.
-
Freeman T., Thom B., Smith S. Noise and vibration development for adapting a conventional vehicle platform for an electric powertrain. SAE Technical Paper 2013-01-2003, https://www.doi.org/10.4271/2013-01-2003, 2013.
-
van der Auweraer H., Janssens K. A source-transfer-receiver approach to NVH engineering of hybrid/electric vehicles. SAE Technical Paper 2012-36-0646, https://www.doi.org/10.4271/2012-36-0646, 2012.
-
Slavic J., Javorski M., Luznar J., Cepon G., et al. Magnetostrictive and magnetic sources of noise in the electric motors. SAE Technical Paper 2016-01-1838, https://www.doi.org/10.4271/2016-01-1838, 2016.