Abstract
In order to effectively improve the friction and wear performance of the brake disc without changing the raw materials and process flow, ultrasonic vibration was proposed and verified in this paper. During the casting process, ultrasonic waves with excitation frequency of 20 kHz and 25 kHz were applied to prepare the sample of the brake disc. Based on the Link3900 NVH test bench, the pressure, speed and temperature sensors were installed to obtain the variation rules of the average friction coefficient and friction stability coefficient under different working conditions. The friction samples were processed by ultrasonic cleaner and measured by high-precision electronic balance, the wear quality change rule at different times was obtained. The hardness study was carried out synchronously with the metallographic test by using the sample test method, thus the influence of ultrasonic vibration on the microstructure and surface hardness was obtained. Combining with the element distribution test results, the influence mechanism of ultrasonic vibration on wear resistance was explained by analyzing the micro wear morphology with electron probe microscope. The results show that applying ultrasonic vibration to the brake disc casting process can significantly improve the hardness, wear resistance and friction stability of the product, especially when the excitation frequency is 20 kHz, better effect can be achieved.
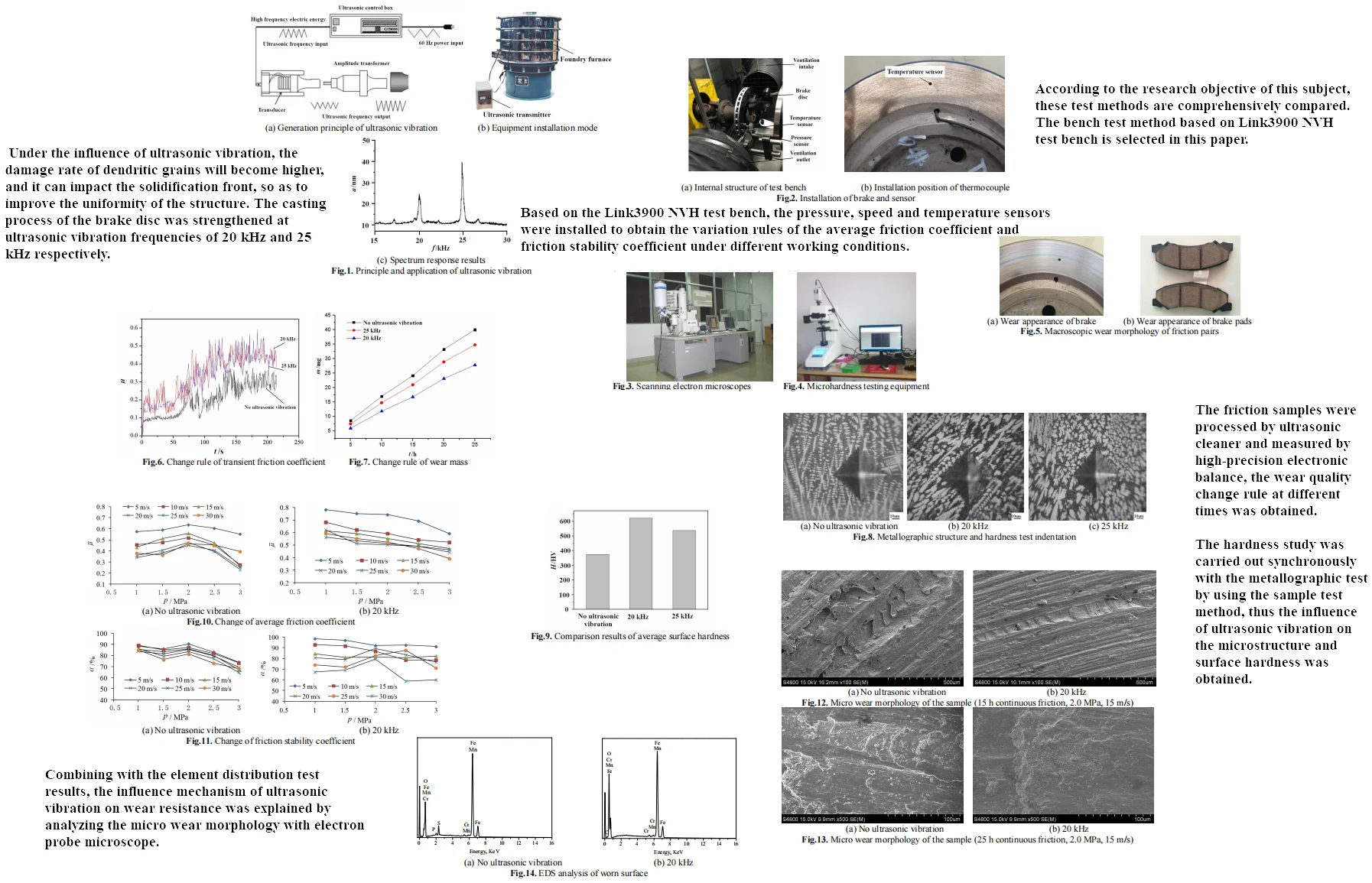
Highlights
- In order to effectively improve the friction and wear performance of the brake disc without changing the raw materials and process flow, ultrasonic vibration was proposed and verified.
- Based on the Link3900 NVH test bench, the pressure, speed and temperature sensors were installed to obtain the variation rules of the average friction coefficient and friction stability coefficient under different working conditions.
- The hardness study was carried out synchronously with the metallographic test by using the sample test method, thus the influence of ultrasonic vibration on the microstructure and surface hardness was obtained.
1. Introduction
The wear resistance of automobile brake disc has a key influence on the driving safety, stability and working life. When the wear value of the brake disc reaches a certain level, the vibration and noise during braking process will increase significantly. If the wear resistance of the brake disc is insufficient, it will further aggravate the eccentric wear of the contact surface, resulting in a large fluctuation of the friction coefficient [1]. Therefore, the wear characteristic is one of the key indicators to measure the brake performance. At present, the research on the improvement of brake wear resistance mainly focuses on the optimization of material elements or the application of new materials, such as: Yang [2] applied a low carbon martensite to the brake disc steel, analyzed the microstructure evolution and mechanical properties from the wear surface to the matrix, established the relationship between shear strain and surface depth, and verified the improvement effect of hardness and wear resistance; Darmawan [3] developed a plant fiber reinforced composite, added it to the brake disc, and tested the hardness and wear resistance of the brake disc in different environments; Kindrachuk [4] proposed to increase the content of hydrogen element in the brake disc, study the influence of this element on the overall hardness and wear resistance, and provide an important basis for material optimization. However, these research methods need a lot of time and resources to verify the feasibility of new materials. Even if the improved materials are feasible, it is necessary to reformulate the process plan, or even change the production line, so the cost performance is relatively low. According to Ref [5], it can be known that ultrasonic vibration has a good effect on grain refinement and can significantly improve the mechanical properties of alloy steel materials. Therefore, ultrasonic vibration is applied to the casting process of brake disc in this paper, and its influence of friction parameters and wear resistance is tested and verified. As the manufacturing process of existing brake disc materials has been relatively mature, this research scheme can realize part processing and performance enhancement conveniently, which has higher economic benefits.
2. Design of testing scheme
2.1. Principle of ultrasonic vibration strengthening
The initial material of the brake disc is 42CrMo, which belongs to a medium carbon low alloy steel [6]. This type of steel is easy to smelt, cast and formed, and can obtain a series of mechanical properties through quenching and tempering treatment. It is widely used to manufacture parts that can withstand large cyclic load and impact load, or work under composite stress. However, in the casting process, the grains are prone to local oversize or imbalance, which is also one of the reasons for the decline of wear resistance under extreme conditions [7]. The principle and application of ultrasonic vibration in brake disc casting are shown in Fig. 1(a) and Fig. 1(b). The photo of equipment installation mode in Fig. 1(b) was taken in foundry and smelting laboratory by author. In order to obtain the influence of ultrasonic excitation frequency on the vibration characteristics of casting process, the vibration amplitude was collected by laser vibration tester, and the amplitude accuracy was 0.1 nm. Set the ultrasonic wave as the continuous frequency conversion mode, and the range is 15 kHz-30 kHz. According to the test, when the frequency is not in this range, the impact on the molten metal is very small. Through signal amplification, filtering and other processing, spectrum response results can be obtained as shown in Fig. 1(c).
Fig. 1Principle and application of ultrasonic vibration
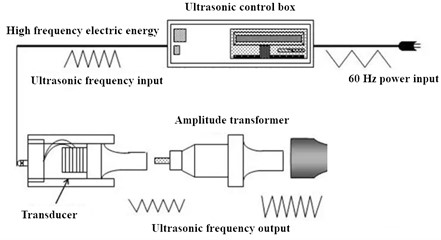
a) Generation principle of ultrasonic vibration
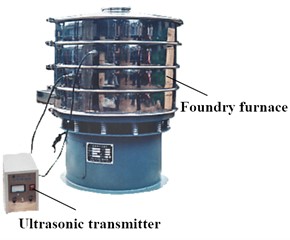
b) Equipment installation mode
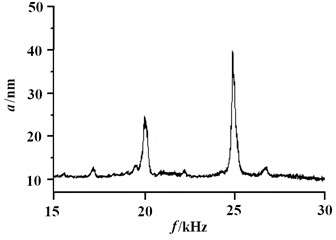
c) Spectrum response results
It can be seen that when the excitation frequency is around 20 kHz and 25 kHz, the amplitude has remarkable peak value. The amplitude and intensity of ultrasonic wave are amplified, and its vibration can promote the cavitation effect of liquid metal and reduce the bubble rate. Under the influence of ultrasonic vibration, the damage rate of dendritic grains will become higher, and it can impact the solidification front, so as to improve the uniformity of the structure. The casting process of the brake disc was strengthened at ultrasonic vibration frequencies of 20 kHz and 25 kHz respectively. Therefore, this frequency is used for sample preparation and friction performance test. The research conclusion can be verified by comparing with the sample without ultrasonic vibration.
2.2. Testing of tribological properties
There are three recognized friction and wear test methods for disc brakes in the field of tribology, including sample test method, bench test method [8] and road test method. The sample test method requires the initial brake disc to be cut according to specific test standards. The difference between test conditions and load conditions is large, leading to the general practicability of test results. Therefore, the purpose of the sample test method is to examine or test the friction properties of a certain friction material under specific conditions, which is more used in the formulation research, optimization screening and quality monitoring before the development of new disc brake products. Bench test method refers to the performance test and analysis of the disc brake on a special test platform. Compared with the sample test method, the bench test method retains the original structure size of the friction pair, which can simulate the load conditions very close to the real working conditions, so the reliability and practicability of the test data are stronger. Road test method is also called vehicle test, that is to test the friction performance on the road. Compared with the first two test methods, the road test method has the best data authenticity and availability, but the test cycle is very long, the sensor installation is difficult, the test cost is high, and the periodic single variable test cannot be realized, which is generally used for the final vehicle sampling inspection.
According to the research objective of this subject, these test methods are comprehensively compared. The bench test method based on Link3900 NVH test bench is selected in this paper. The overall structure and test scheme are shown in Fig. 2. The photo of installation of brake and sensor in Fig. 2 was taken in Noise and Vibration Workshop by author after the manufacturing process of brake was completed. The brake disc is installed on the main shaft and rotates synchronously with the reducer output shaft. In order to more accurately simulate the driving state of the vehicle and consider the influence of air flow on temperature, ventilation inlet and ventilation outlet are set as shown in Fig. 2(a). The sensors mainly include temperature sensor, torque and speed sensor, pressure sensor, etc. The temperature sensor adopts high-precision micro armored thermocouple, and its thermal response time is less than 0.01 s. The installation diagram of the temperature sensor is shown in Fig. 2(b). The micro armored thermocouple is embedded into the brake disc through drilling, and the wire can be directly connected to the information acquisition system of the testing machine.
Fig. 2Installation of brake and sensor
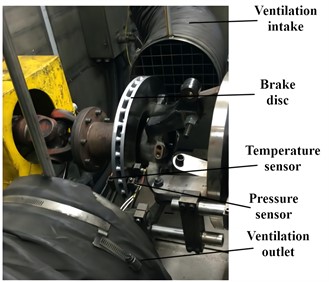
a) Internal structure of test bench

b) Installation position of thermocouple
Friction coefficient is one of the most critical parameters to measure the braking and wear resistance performance. It is an unsteady physical parameter and has a direct relationship with material itself and working condition. It shows different characteristics under different load conditions. In order to study the influence of working conditions on the friction performance, the concept of friction stability coefficient is introduced in the paper. In general, the friction coefficient that measured in the bench test can be calculated as:
where is the friction force between friction pairs, in N; is the brake pad pressure, in MPa; is the nominal contact area between friction pairs, in m2.
Friction stability coefficient in single braking test cycle can be expressed as:
where, is the average friction coefficient; is the maximum friction coefficient.
3. Testing of wear performance
Before and after wear, the brake disc sample shall be cleaned in ultrasonic wave with acetone for 15 min, and then weighed by an electronic balance with an accuracy of 0.1 mg after drying, so as to obtain accurate wear amount. After the friction and wear test of brake disc is completed, S-4800 field emission scanning electron microscope with EDS (Energy Dispersive Spectroscopy) function [9] is used to observe and analyze the worn surface morphology and chemical composition of the specimen, as shown in Fig. 3. The photo of scanning electron microscopes in Fig. 3 was taken by author in metallographic laboratory. In addition, hardness is one of the basic mechanical performance indicators of materials, which plays a key role in the wear resistance of materials. Therefore, it is regarded as an important indicator of brake disc performance strengthening. The microhardness testing equipment is shown in Fig. 4, which can set the loading force and output accurate Vickers hardness. The photo of microhardness testing equipment in Fig. 4 was also taken by author in metallographic laboratory. The measurement of hardness is not only related to the elastic modulus, yield strength, tensile strength and other mechanical properties of materials, but also closely related to the measurement conditions of the measuring instrument itself. Hardness itself is not a physical quantity, but the overall performance of mechanical properties of local areas of materials under specific conditions. It reflects the degree of aggregation or combination of grains in solid materials. Therefore, the effect of ultrasonic vibration on wear resistance can be effectively verified.
Fig. 3Scanning electron microscopes
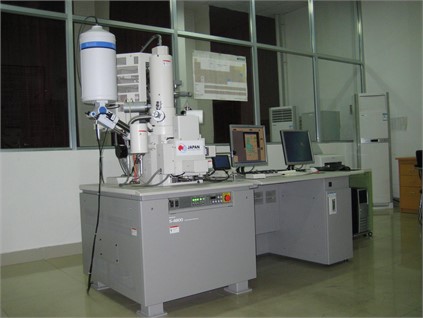
Fig. 4Microhardness testing equipment
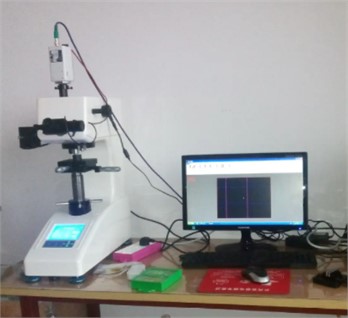
4. Test and analysis of friction and wear properties
4.1. Influence of ultrasonic excitation frequency
In order to ensure the reliability of the friction test, local eccentric wear caused by external impurities or particles should be eliminated. As the cycle friction test takes a long time, the surface morphology of the brake disc and brake pad shows a circular wear state, as shown in Fig. 5. The photo of macroscopic wear morphology of friction pairs in Fig. 5 was taken by author after periodic friction test in Noise and Vibration Workshop. It can be seen that the wear ring is clear, and there is no radial wear, micro cracks or local damage on brake pads, which can indicate that the test environment has no impact on the sample, and the test results have good reliability.
Fig. 5Macroscopic wear morphology of friction pairs
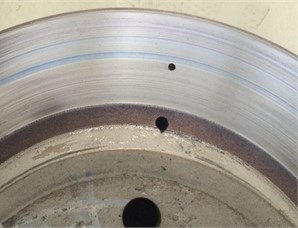
a) Wear appearance of brake
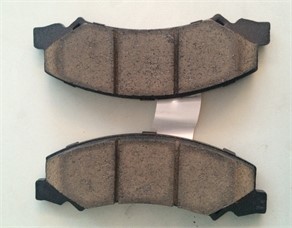
b) Wear appearance of brake pads
Fig. 6Change rule of transient friction coefficient
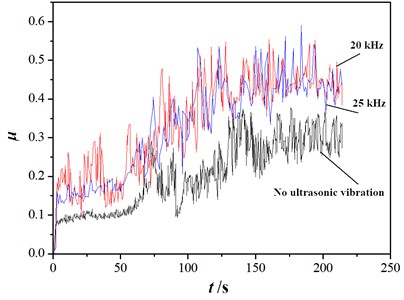
Fig. 7Change rule of wear mass
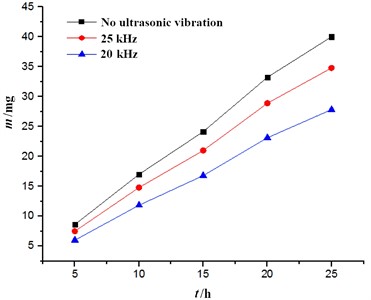
There are three kinds of brake disc samples prepared according to different ultrasonic excitation frequencies, including 20 kHZ, 25 kHz and no ultrasonic vibration. Set the brake pressure to 2.0 MPa and the brake disc speed to 560 rpm. Through the continuous braking test, the transient friction coefficient variation law of different brake disc samples can be obtained, as shown in Fig. 6. It can be seen that ultrasonic vibration can significantly improve the value and stability of the friction coefficient, but there is no significant difference between the effects of the two ultrasonic excitation frequencies on the improvement of the friction coefficient. Clean and weigh the brake disc every 5 hours under the condition of continuous braking for 25 hours. In order to avoid data failure due to excessive temperature caused by continuous braking for a long time. Set temperature control in the test bench. When the brake disc temperature exceeds 600 ℃, it will actively cool down through the circulation of cold air. Thus, the change rule of wear mass can be obtained, as shown in Fig. 7. It can be seen that the wear of the brake disc increases approximately linearly with time. This also shows that the longer the braking time is, the more significant the effect of ultrasonic targeting on the improvement of wear resistance is. Compared with two different ultrasonic excitation frequencies, the ultrasonic frequency at 20 kHz can achieve better wear resistance. Compared with two different ultrasonic excitation frequencies, the ultrasonic frequency at 20 kHz can achieve better wear resistance. At 25 hours, the excitation frequency can reduce the wear mass of the brake disc by about 37 % under initial conditions, and the friction performance is improved significantly.
The hardness test and research are conducted before the friction test, and the sample test method is adopted, which can be conducted simultaneously with the metallographic test. The surfaces of the three samples were polished with metallographic abrasive paper until there was no obvious scratch, then polished with Al2O3, and finally corroded with 5 % nitric acid solution. Thus, clearer indentation and microstructure can be obtained, as shown in Fig. 8. It can be seen that ultrasonic vibration has a significant damage effect on dendritic grains, and 25 kHz excitation frequency has a better effect on grain refinement [10]. The distribution of cementite in pearlite is more balanced. It also known that the indentation produced by the hardness tester has no cracks or notches, which indicates that ultrasonic vibration will not reduce the toughness and plasticity [11] of the material. According to the metallographic morphology, it can be predicted that increasing the ultrasonic vibration frequency can improve the grain crushing efficiency. It has a good effect on the improvement of material strength, but grain refinement does not necessarily have a positive effect on the improvement of hardness.
Fig. 8Metallographic structure and hardness test indentation
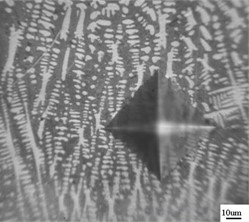
a) No ultrasonic vibration
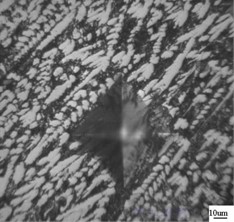
b) 20 kHz
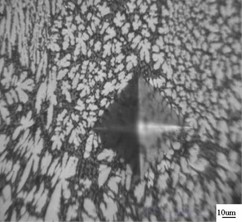
c) 25 kHz
Fig. 9Comparison results of average surface hardness
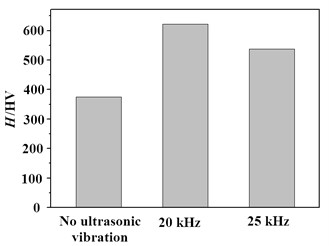
As 50 μm is the interval, set the position of hardness measuring points, and take the average value of 20 hardness as the evaluation value to obtain the comparison results, as shown in Fig. 9. It can be seen that ultrasonic vibration can significantly improve the hardness of the brake disc surface. When the excitation frequency is 20 kHz, the hardness improvement effect is the best, and the average hardness is 1.7 times of the original material. According to the above research results, under the condition of ultrasonic excitation frequency of 20 kHz, a very ideal material strengthening effect can be obtained. Therefore, in the study of the relationship between working conditions and wear, the ultrasonic excitation frequency is set as 20 kHz, and compared with no ultrasonic vibration condition. The sampling period of the data acquisition module is 0.01 s. The total cycle braking times under each working condition is 100. The average value of the detection results is taken. In order to ensure that the initial conditions of each braking are consistent, a certain time interval is required for two adjacent braking cycles.
4.2. Effect of brake condition on friction and wear resistance
When the micro convex body on the brake friction pair surface is subjected to certain extrusion or shearing, the real contact area will be changed. The whole process is greatly affected by pressure and friction velocity, which are the main reasons for the change of friction coefficient. However, the generation rate of micro convex contact spots does not always increase with the increase of the pressure. When the brake pressure is above a certain range, the effective yield pressure of the micro convex will be significantly reduced. According to the working principle of disc brake and the relevant regulations of friction parameter test, the brake pressure p and brake speed v are taken as the data acquisition objects. Among them, the vehicle braking speed can be directly defined in the upper computer, and it is set as a constant value in any test cycle to simulate the constant braking condition of long downhill. The test and comparison results of average friction coefficient are shown in Fig.10. It can be seen that ultrasonic vibration can ensure that the brake disc maintains a high friction coefficient under different brake pressures and speeds. The change of friction stability coefficient is shown in Fig. 11. It can be seen that ultrasonic vibration can significantly improve the fluctuation of friction coefficient under different working conditions and improve the stability of braking. Under low speed driving conditions, the average friction coefficient remains at a high value. Under different driving speeds of 10 m/s-30 m/s, the difference of average friction coefficient under specific braking pressure load is very small. Although the brake pressure increases and the adhesion increases, the brake condition will reduce the effective generation rate of the real friction area and weaken the meshing effect.
Fig. 10Change of average friction coefficient
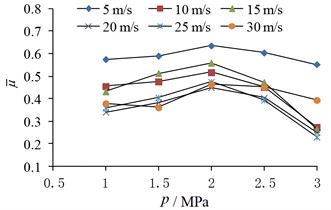
a) No ultrasonic vibration
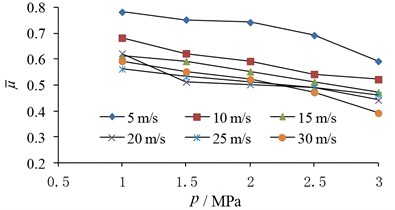
b) 20 kHz
Fig. 11Change of friction stability coefficient
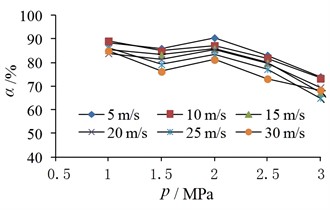
a) No ultrasonic vibration
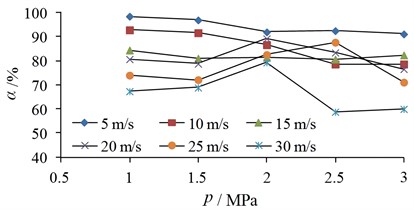
b) 20 kHz
The wear of the brake disc is the combined result of the meshing, adhesion and furrow effect of the surface asperities of the friction pair. With the change of the transient friction, the brake disc surface will dynamically appear in three forms: elastic, plastic and intermediate. According to the change rule of friction coefficient, the wear state of the sample can be divided into three stages. At the initial stage of braking, the friction coefficient first increases rapidly and then slowly with the contact of friction pair, which is in accordance with the change of braking pressure. At this time, the braking force mainly comes from the meshing effect of the asperities on the friction pair surface, and the adhesion effect is not significant. In the friction adjustment stage, the friction coefficient shows a certain decreasing trend, and the influence of the micro convex meshing on the braking force is weakened. With the extension of a short time, the adhesion in the real contact area increases, but the resulting resistance effect is not as good as the meshing effect. In the stable friction stage, the friction coefficient keeps a small fluctuation within a specific amplitude range. The meshing, adhesion and furrowing of friction pairs are stable, which is also the key stage to determine the wear resistance. The micro wear morphology under 15 h and 20 h continuous friction conditions is shown in Fig. 12 and Fig. 13 respectively. It can be seen that ultrasonic vibration can effectively enhance the surface wear resistance, with lower wear groove depth and less obvious adhesion. For the specimens without ultrasonic vibration, there are many delamination areas on the worn material surface. With the increase of friction time, more flake structures and coarse metal particles are produced in these delamination areas. These metal particles are attached to the friction surface and locked between the friction pair surfaces during the wear process, thus increasing the degree of wear, which is also the reason why the friction coefficient and wear rate of materials increase rapidly with the initial increase. As the grain characteristics in the casting process are improved by ultrasonic vibration, the flaky layer and abrasive particles on the material surface will be rolled and oxidized repeatedly to become fine metal particles. These particles adhere to the surface of the specimen, reducing the degree of abrasive wear and improving the wear resistance of the material.
Fig. 12Micro wear morphology of the sample (15 h continuous friction, 2.0 MPa, 15 m/s)
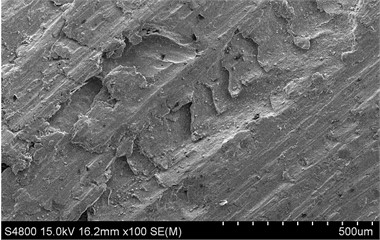
a) No ultrasonic vibration
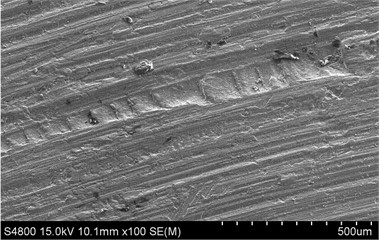
b) 20 kHz
Fig. 13Micro wear morphology of the sample (25 h continuous friction, 2.0 MPa, 15 m/s)

a) No ultrasonic vibration
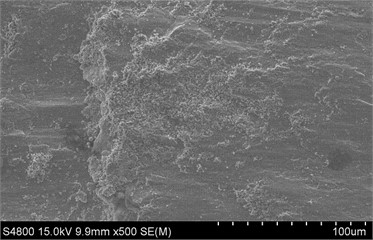
b) 20 kHz
According to the difference of braking conditions, in addition to high braking pressure and braking speed, the friction stability coefficient maintains good stability without obvious fluctuation. When the brake pressure is 2.0 MPa, the friction stability coefficient of the brake under different driving speeds has a very small difference. With the increase of brake pressure, the average friction coefficient of disc brake decreases nearly linearly. It can be seen that it is not reliable to improve the braking efficiency of vehicles only by increasing the braking pressure, especially when the anti-lock system is not installed. Higher driving speed and higher braking pressure are easy to cause sharp decline of braking performance.
4.3. Influence of ultrasonic vibration on element distribution
In order to study the influence of ultrasonic vibration on element distribution, EDS analysis was carried out on two samples, and the results are shown in Fig. 14. It can be seen that under the influence of ultrasonic vibration, the content of metal oxides will increase significantly. Ultrasonic vibration can significantly affect the crystallization process of molten metal, especially the real contact area of various elements in the metal. At the same time, the activity of alloy elements increases obviously at high temperature. Under the promotion of ultrasonic vibration, it is easier to form a dense oxide film. These oxide films exist in the form of coatings, which can improve the wear resistance of the material surface. The metal oxide film formed on the material surface is harder than the substrate. With the increase of braking temperature, the formation rate of oxide film accelerates. When it reaches a certain level, it will protect the material surface, thus effectively reducing the wear degree of the test piece. Under the ultrasonic vibration, the brake disc wear rate decreases significantly for this reason. In addition, after the formation of the oxide film, the wear degree of the abrasive particles becomes lighter. At this time, the wear mechanism of the material is mainly fatigue delamination wear and oxidation wear. In general, the influence of ultrasonic vibration on the structure of the material itself can have a significant impact on the degree and mode of wear. The increase of pressure will reduce the friction coefficient, but will significantly increase the degree of wear, and make the wear mechanism change from abrasive wear to delamination wear. During braking, the temperature rises seriously. After uneven deformation caused by thermal expansion, high concentrated stress will be generated at local position to increase the wear degree of parts, and after the formation of oxide film, the wear resistance of materials will be improved, and the wear degree will be reduced. In contrast, the wear increase effect is more significant. In addition, according to the wear results of the test pieces under low pressure, the wear degree is relatively light, which will not be the main cause of their wear failure.
Fig. 14EDS analysis of worn surface
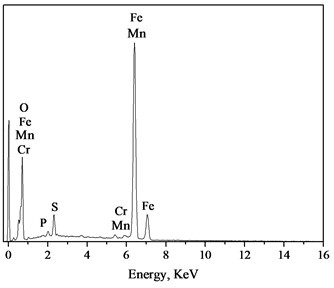
a) No ultrasonic vibration
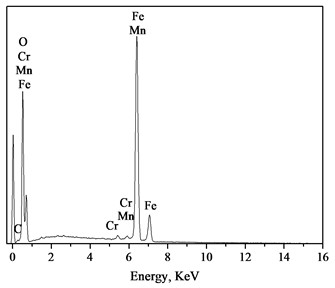
b) 20 kHz
5. Conclusions
The friction and wear characteristics of the brake are the key factors affecting driving safety. For conventional automobile production, how to improve the braking efficiency performance through effective and low-cost technical means is an important problem that needs to be solved properly. On the premise of not changing the original materials and processing methods, the application of ultrasonic vibration to the casting stage of brake discs is proposed in this paper. In order to verify the mechanism of ultrasonic vibration on various properties, friction and wear tests, hardness tests, microstructure observation and other technical means have been comprehensively applied, and the main conclusions are obtained as follows:
1) Ultrasonic vibration has a good positive effect on the friction and wear characteristics of the brake disc, and when the excitation frequency is 20 kHz, it can effectively optimize the comprehensive mechanical properties and significantly improve the cost performance of the product. It can be seen from the comparative analysis of the variation law of average friction coefficient and friction stability coefficient that the brake disc after ultrasonic vibration treatment can show better braking stability under various working conditions, and the probability of braking failure will be significantly reduced.
2) Ultrasonic vibration can change the metallographic structure of the brake disc material in the casting process, and reduce the number of dendritic grains, so that the hardness is higher, and the wear resistance is better. The element distribution analysis shows that more oxidation particles are formed under the influence of ultrasonic vibration, which can further strengthen the friction surface. At the same time, it is also one of the main reasons for the improvement of wear resistance. According to the tribological characteristics test of the brake disc, the performance of light braking and emergency braking can be improved under low, medium and high-speed driving conditions.
References
-
W. Sawczuk, A. M. R. Cañás, D. Ulbrich, and J. Kowalczyk, “Modeling the average and instantaneous friction coefficient of a disc brake on the basis of bench tests,” Materials, Vol. 14, No. 16, p. 4766, Aug. 2021, https://doi.org/10.3390/ma14164766
-
L. Yang, T. Zhou, Z. Xu, Y. He, X. Hu, and H. Zhao, “Excellent wear resistance of a high-speed train brake disc steel with high hardening ratcheting strain zone,” Metals, Vol. 11, No. 9, p. 1478, Sep. 2021, https://doi.org/10.3390/met11091478
-
A. S. Darmawan, P. I. Purboputro, and B. W. Febriantoko, “The effect of composition on hardness and wear resistance of rice plant fiber reinforced composite as a material of brake lining,” in IOP Conference Series: Materials Science and Engineering, Vol. 771, No. 1, p. 012069, Mar. 2020, https://doi.org/10.1088/1757-899x/771/1/012069
-
M. V. Kindrachuk, D. A. Vol’Chenko, N. A. Vol’Chenko, N. M. Stebeletskaya, and A. V. Voznyi, “Influence of hydrogen on the wear resistance of materials in the friction couples of braking units,” Materials Science, Vol. 53, No. 2, pp. 282–288, Sep. 2017, https://doi.org/10.1007/s11003-017-0073-z
-
Z. Hu, X. Li, H. Yan, X. Wu, H. Qun, and J. Lin, “Effects of ultrasonic vibration on microstructure evolution and elevated-temperature mechanical properties of hot-extruded Mg-6Al-0.8Zn-2.0Sm wrought magnesium alloys,” Journal of Alloys and Compounds, Vol. 685, No. 5, pp. 58–64, Nov. 2016, https://doi.org/10.1016/j.jallcom.2016.05.210
-
B. Yang et al., “Effect of temperature on microstructures and mechanical properties of medium‐carbon low‐alloy steel by caliber rolling,” Materialwissenschaft und Werkstofftechnik, Vol. 53, No. 9, pp. 1106–1120, Sep. 2022, https://doi.org/10.1002/mawe.202200017
-
X. C. Wang, “Analysis and verification of equivalent ultimate load test of anti rolling torsion bar system,” (in Chinese), Rolling Stock Technology, Vol. 6, No. 1, pp. 33–35, 2021, https://doi.org/10.14032/j.issn.1007-6034.20211.06.012
-
J. J. Zhang, “Economic performance test of hybrid power system based on test bench,” (in Chinese), Vehicle and Power Technology, Vol. 2, No. 1, pp. 34–39, 2022, https://doi.org/10.16599/j.cnki.1009-4687.2022.02.012
-
M. Moorthy, J. Palraj, L. Kannan, S. Katlakunta, and S. Perumal, “Structural, microstructural, magnetic, and thermoelectric properties of bulk and nanostructured n-type CuFeS2 Chalcopyrite,” Ceramics International, Vol. 48, No. 19, pp. 29039–29048, Oct. 2022, https://doi.org/10.1016/j.ceramint.2022.04.287
-
Q. Luo et al., “Achieving grain refinement of α-Al and Si modification simultaneously by La-B-Sr addition in Al-10Si alloys,” Journal of Materials Science and Technology, Vol. 135, No. 1, pp. 97–110, Feb. 2023, https://doi.org/10.1016/j.jmst.2022.07.009
-
Y. H. Zhang, “Elastoplastic contact and accuracy loss analysis of planetary roller lead screw pair considering radial load,” (in Chinese), Mechanical Transmission, Vol. 46, No. 8, pp. 124–130, 2022, https://doi.org/10.16578/j.issn.1004.2539.2022.08.020
-
H. P. Zhao, “Friction and wear properties of laser remanufactured cobalt based alloy cladding layer on the excessively worn surface of brake disc,” (in Chinese), Mechanical Engineering Materials, Vol. 46, No. 6, pp. 78–83, 2022.
About this article
The paper is supported by University President Fund of Qingdao West Coast New Area: development and application of large ship steel wall permanent magnet adsorption derusting robot and provincial key research and development research projects (SC898744).
The datasets generated during and/or analyzed during the current study are available from the corresponding author on reasonable request.
The authors declare that they have no conflict of interest.