Abstract
This research study is primarily focused on evaluating the fresh properties of industrial-based 3D printable geopolymer concrete by adding glass wool strings and glass fibers activated by sodium silicate solution with a molar ratio of 2.4-2.6 (31 % SiO2 and 13 % Na2O). The glass wool strings, and recycled glass fiber are added to industrial-based geopolymer concrete at a dosage of 1 % to 5 % by volume of the concrete. The fresh concrete properties such as open time, setting time and shape stability of industrial-based geopolymer concrete (GPC) with glass wool and glass fibers were compared with those of industrial-based GPC without glass wool strings and glass fibers. The results show that the addition of glass wool increases the setting time of the concrete mix at room temperature. The deformation of the specimens at room temperature decreased by 39 %. The addition of glass fiber in geopolymers also increases the stiffness by 74 % compared to GPC without glass fiber.
Highlights
- This research study is primarily focused on evaluating the fresh properties of industrial-based 3D printable geopolymer concrete by adding glass wool strings and glass fibers activated by sodium silicate solution with a molar ratio of 2.4-2.6 (31% SiO2 and 13% Na2O).
- The fresh concrete properties such as open time, setting time and shape stability of industrial-based geopolymer concrete (GPC) with glass wool and glass fibers were compared with those of industrial-based GPC without glass wool strings and glass fibers.
- The addition of glass fiber in geopolymers also increases the stiffness by 74% compared to GPC without glass fiber.
1. Introduction
Ordinary Portland cement (OPC), used as a binder in conventional concrete production, accounts for nearly 8 % of global carbon emissions. The high consumption of concrete has led to high production of cement, which amounted to nearly 4.1 billion tons in 2020 and is considered one of the main sources of global warming emissions [1]. In addition to cement, aggregates account for 60 to 80 % of concrete, and water is the main component of concrete. The excessive use of raw materials in the form of aggregates (coarse and fine), water, and cement (calcined limestone, clay, and sand) to produce concrete causes irreversible damage to the atmosphere and is considered a serious threat to environmental sustainability [2, 3]. The adverse effects of concrete on the environment can be reduced by using alternative cementitious materials.
Geopolymers prepared by polymerization of aluminosilicate materials are considered environmentally friendly and are viable substitutes for OPC with various sustainable properties [4]. Numerous aluminosilicate precursors such as ground granulated blast furnace slag (GGBFS), fly ash, slag, volcanic ash, and cement kiln dust are used for the production of geopolymers. Industrial side streams such as screenings residues from construction and demolition wastes (CDW), green liquor sludge, fiber wastes, and mine tailings are also considered as potential raw materials for the synthesis of geopolymer concrete. The use of geopolymer concrete in the construction industry reduces CO2 emissions by almost 80 % compared to OPC [5].
Numerous studies have been conducted to improve the strength properties of geopolymer concrete by using different recycled industrial wastes and fibers [6-10]. Most used fibers to improve the strength properties of concrete are cotton fiber, carbon fiber, glass fiber and basalt fiber. The study conducted by Mehta and Bhandari [11], Blazy et al [12] investigated the effects of adding glass fibers on the mechanical properties of concrete. The study showed that the addition of glass fibers (1 % to 2.5 %) in geopolymer concrete increased the flexural strength of the specimen by 20 % compared to a specimen without glass fibers. In addition, the glass fiber reinforced concrete improved the tensile and splitting strength, permeability, and toughness of the concrete specimens. However, the addition of glass wool and glass fibers to the fresh 3D printable properties of geopolymer concrete received the least attention.
This study investigates the use of glass fiber and glass wool strings on the fresh properties of industrial base geopolymer concrete. The suitability of recycled glass fibers and glass wool strings on the setting time and shape stability of fresh concrete was investigated. The effects of heat and additives on the deformation, shape stability and open time of the concrete were discussed.
2. Materials
The collected glass fiber sample shown in Fig. 1(a) is produced after the sizing is applied to the glass fiber during the installation process. The material produced has a limited end use and is often treated as waste. The residual waste produced during installation has the same properties as the new fiberglass material. The glass fibers are crushed in a mechanical recycling process and used for concrete applications. The crushing in the recycling process is done to make fibers usable as an additive for concrete production. The glass fibers are shredded and crushed to achieve the desired particle size. A magnetic field is used to remove the metallic impurities between the fibers. The glass fiber strings shown in Fig. 1(b) are inserted into concrete specimens in parallel and in a wave form. The average chemical composition of the glass fibers and glass fiber strings is shown in Table 1. The Glass fiber strings and glass fibers have similar chemical composition. The high content of silicon and aluminum in glass fibers makes them suitable for use in concrete.
Fig. 1Recycled materials used for geopolymer concrete formulation: a) glass fiber, b) glass fiber strings
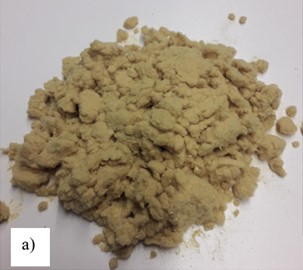
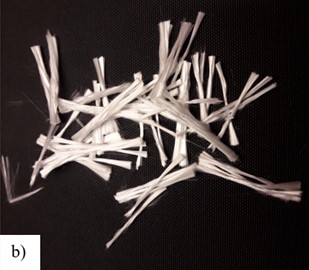
Table 1Chemical composition of glass fiber [13-15]
Component | Glass fiber [%] | Glass wool strings [%] | Bark boiler ash [%] |
Al2O3 | 12 | 4 | 1.54 |
CaO | 18 | 12 | 3.85 |
SiO2 | 55 | 63 | 89.02 |
Na2O | 1 | 11 | 0.18 |
MgO | 4 | 4,5 | 0.58 |
K2O | 1 | 0.5 | 2.07 |
B2O3 | 10 | 5 | 0.02 |
3. Methods
The crushed glass fibers are added to the geopolymer mixture containing bark boiler ash, CDW, fiber waste, mine tailings, metakaolin, and sodium silicate with 13 % Na2O and 31 % SiO2 (as alkali activator). The weight value of the glass fibers was measured with an accuracy of 0.1 gram. The dry mixture of binder and fillers is continuously mixed with the glass fibers for 3 minutes. The mixed amount of water and sodium silicate was added to the dry mixture and further mixed for 1-2 minutes. The mixing process was carried out using a Hobart mixer and a drill (Makita DHP453). During the mixing process, the adherent material on the side of the container was scraped off periodically. Three glass fiber strings with a diameter of 2 mm were used in parallel and in waves pattern in some concrete specimens, as shown in Fig. 2. The fresh concrete properties such as open time and workability of the mixture were measured.
Fig. 2Parallel and wave pattern of glass fiber strings used in industrial based geopolymer concrete
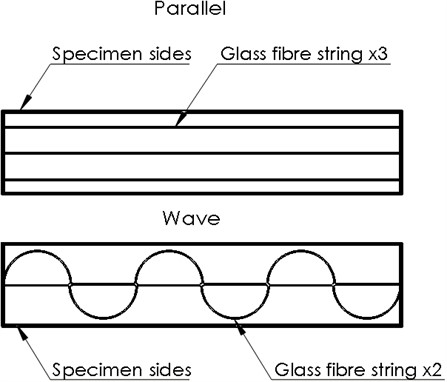
The setting test is performed to measure the potential open time of fresh concrete. ASTM C403/C403M-08 standard was used for the setting time of the mixture [16]. The force gauge with a 5 mm diameter round needle was pressed into the specimen to a depth of 25 mm. Measurements were taken until the penetration resistance exceeded 3.5 MPa at a temperature between 20 °C and 100 °C. The setting time value was calculated with Eqs. (1) and (2). The Gallen Kamp Hot Box with furnace size 2 as shown in Fig. 3 was used for heating purpose:
where Initial penetration of needle in test specimens (min), needle fail to penetrate till the bottom of specimens (min), penetration resistance exceeded 3.5 MPa (min).
Fig. 3Gallen Kamp Hot Box used for heating [17]
![Gallen Kamp Hot Box used for heating [17]](https://static-01.extrica.com/articles/23152/23152-img4.jpg)
The shape stability test of concrete mixtures was performed by pouring the mixture into a test specimen with 54 mm diameter, 50 mm height and 2 mm thickness. The load (equal mass of the specimen) was applied to the top of the mix, and the difference in height was calculated with Eq. (3). The specimens and testing setup used for shape stability testing is presented in Fig. 4. The mixture design of GPC is shown in Table 2:
where initial height of concrete mixture, height of concrete mixture after applying load.
Table 2Mix design of GPC
GPC mix | Bark boiler ash [%] | CDW [%] | Metakaolin [%] | Sodium silicate [%] | Water [%] | Sand [%] | Glass fiber [%] |
GPC 1 | 10 | 30 | 15 | 5 | 30 | 5 | 5 |
GPC 2 | 7 | 10 | 11 | 25 | 6 | 39 | 2 |
GPC 3 | 7 | 9 | 13 | 15 | 16 | 39 | 1 |
Fig. 4a) Test specimen mould, b) setup used for shape stability testing
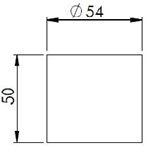
a)
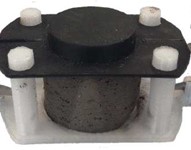
b)
4. Results and discussions
4.1. Glass fiber effect on the setting time of geopolymer concrete
The initial setting time of the concrete specimens was tested with different values of glass fiber. The setting tests were performed by the materials reaching a strength of 3.5 MPa (68.7 N), which is considered the end point of the setting time. The concrete specimen with a glass fiber content of 2 % exhibited the highest setting time, which was compared with that of the specimen without glass fiber (see Table 3). The test was performed by heating the specimens in the temperature range of 20, 60 and 80 °C.
Table 3Setting time of samples at different temperatures
Temperature | Penetration resistance | Glass fiber mixtures Setting time[min] | Concrete without glass fiber Setting time [min] |
20 °C | 60 N | 26 | 42 |
60 °C | 60 N | 20 | 21 |
80 °C | 60 N | 20 | 19 |
The addition of glass fibers to the concrete mix resulted in better setting time and workability, with lower adhesion of the mix to the metal surface and somewhat poorer extrudability. The addition of additives to the concrete mix to achieve better pumpability and lower slump, by adding bentonite, cellulose and Actigel, was investigated in another study [18]. The glass wool strings did not show any effect on the material properties because the strings were not blended but added to the compound during the extrusion phase. The addition of glass fibers in geopolymer concrete helps the mixture to set faster at room temperature.
4.2. Glass fiber effect on the shape stability of geopolymer concrete
The shape stability test was performed for the specimens in a temperature range of 20 and 100 °C. The concrete mix was poured into a 50 mm high steel mold for the shape stability test. The glass fiber specimen remained in the mold for 6 minutes, while the mix without glass fiber specimen remained for 10 minutes. The weight used for the test was 10.3 N. The deformation of the specimens is shown in Table 4. The amount of deformation in the concrete samples with the weight increment is shown in Fig. 5.
Table 4Shape stability test for concrete samples
Temperature | Glass fiber sample (deformation) | Concrete sample (deformation) |
20 °C | 4.8 % | 8 % |
100 °C | 3.4 % | 3 % |
Fig. 5a) concrete sample without glass fiber, b) GPC with glass fiber addition
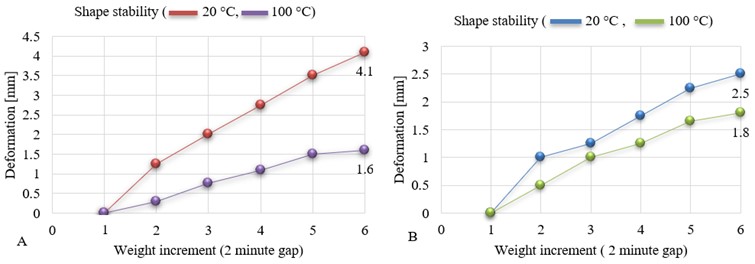
In most cases, the deformation value of geopolymer concrete is 2-6 %, which is measured immediately after mixing the concrete [19, 20]. A similar deformation value was obtained in this study after 10 and 6 minutes of setting time by adding heat. The deformations in the mix were reduced by adding glass fibers and increasing the temperature. The deformation of the glass fiber specimens at room temperature is 39 % lower than the other specimens. Increasing the temperature in the range of 20 to 100 °C reduced the deformation by 28 % for the glass fiber test specimens and by 61 % for the specimens without glass fibers. The stiffness increased by 74 % for the glass fiber specimens.
5. Conclusions
In this research work, the effect of glass fibers on fresh properties such as open time and shape stability of industrial based geopolymer concrete was investigated. The experimental results showed that the addition of glass fibers in GPC samples reduced the room temperature deformation by 39 %. The setting time of the glass fiber sample decreased by 21 % when the temperature range was increased from 20-80 °C. The recycled glass fiber mix showed a faster setting time at room temperature and hardened 28 % faster than the other specimens. Depending on the intended use of the concrete, it may be appropriate to use glass fibers to improve setting time and workability instead of using heat.
References
-
H. Marey, G. Kozma, and G. Szabó, “Effects of using green concrete materials on the CO2 emissions of the residential building sector in Egypt,” Sustainability, Vol. 14, No. 6, p. 3592, Mar. 2022, https://doi.org/10.3390/su14063592
-
Q. Munir, S. Afshariantorghabeh, and T. Kärki, “Industrial waste pretreatment approach for 3D printing of sustainable building materials,” Urban Science, Vol. 6, No. 3, p. 50, Aug. 2022, https://doi.org/10.3390/urbansci6030050
-
QQ. Munir and T. Kärki, “Cost Analysis of Various Factors for Geopolymer 3D Printing of Construction Products in Factories and on Construction Sites,” Recycling, Vol. 6, No. 3, p. 60, 2021.
-
Q. Munir, R. Peltonen, and T. Kärki, “Printing parameter requirements for 3D printable geopolymer materials prepared from industrial side streams,” Materials, Vol. 14, No. 16, p. 4758, Aug. 2021, https://doi.org/10.3390/ma14164758
-
T. Luukkonen, Z. Abdollahnejad, J. Yliniemi, P. Kinnunen, and M. Illikainen, “One-part alkali-activated materials: A review,” Cement and Concrete Research, Vol. 103, pp. 21–34, Jan. 2018, https://doi.org/10.1016/j.cemconres.2017.10.001
-
S. Yan et al., “Effect of fiber content on the microstructure and mechanical properties of carbon fiber felt reinforced geopolymer composites,” Ceramics International, Vol. 42, No. 6, pp. 7837–7843, May 2016, https://doi.org/10.1016/j.ceramint.2016.01.197
-
T. Alomayri, “The microstructural and mechanical properties of geopolymer composites containing glass microfibres,” Ceramics International, Vol. 43, No. 5, pp. 4576–4582, Apr. 2017, https://doi.org/10.1016/j.ceramint.2016.12.118
-
G. H. Ahmed, “A review of “3D concrete printing”: Materials and process characterization, economic considerations and environmental sustainability,” Journal of Building Engineering, Vol. 66, p. 105863, May 2023, https://doi.org/10.1016/j.jobe.2023.105863
-
V. Romanazzi, M. Leone, M. A. Aiello, and M. R. Pecce, “Bond behavior of geopolymer concrete with steel and GFRP Bars,” Composite Structures, Vol. 300, p. 116150, Nov. 2022, https://doi.org/10.1016/j.compstruct.2022.116150
-
H. A. Goaiz, H. A. Shamsaldeen, M. A. Abdulrehman, and T. S. Al-Gasham, “Evaluation of steel fiber reinforced geopolymer concrete made of recycled materials,” International Journal of Engineering, Vol. 35, No. 10, pp. 2018–2026, 2022, https://doi.org/10.5829/ije.2022.35.10a.19
-
S. Mehta and M. Bhandari, “Effect of glass fiber and recycled aggregates on Geopolymer concrete,” in IOP Conference Series: Earth and Environmental Science, Vol. 889, No. 1, p. 012038, Nov. 2021, https://doi.org/10.1088/1755-1315/889/1/012038
-
J. Blazy, R. Blazy, and Drobiec, “Glass fiber reinforced concrete as a durable and enhanced material for structural and architectural elements in smart city-a review,” Materials, Vol. 15, No. 8, p. 2754, Apr. 2022, https://doi.org/10.3390/ma15082754
-
E. Patwary. “Chemical composition of glass fiber production.” Textile Fashion Study, 2022, https://textilefashionstudy.com/chemical-composition-of-glass-fiber/
-
“GLASS WOOL DATA.” Nakagawa Sangyo Co.,Ltd. https://www.nsggmbh.de/wp-content/uploads/2019/05/glass-wool_data-sheet_eng.pdf
-
M. Ulewicz and J. Jura, “Effect of fly and bottom ash mixture from combustion of biomass on strength of cement mortar,” E3S Web of Conferences, Vol. 18, p. 01029, 2017, https://doi.org/10.1051/e3sconf/201712301029
-
“Standard Test Method for Time of Setting of Concrete mixtures by Penetration Resistance,” ASTM C403/C403M-08, American Society of Testing and Materials, 2008.
-
“Gallenkamp hot box oven with fan – size 2 CHF097 XX2.5.” Akribis Scientific Limited. https://www.akribis.co.uk/gallenkamp-hot-box-oven-with-fan-size-2-chf097-xx2-5
-
B. Panda, S. C. Paul, L. J. Hui, Y. W. D. Tay, and M. J. Tan, “Additive manufacturing of geopolymer for sustainable built environment,” Journal of Cleaner Production, Vol. 167, pp. 281–288, Nov. 2017, https://doi.org/10.1016/j.jclepro.2017.08.165
-
S. C. Paul, Y. W. D. Tay, B. Panda, and M. J. Tan, “Fresh and hardened properties of 3D printable cementitious materials for building and construction,” Archives of Civil and Mechanical Engineering, Vol. 18, No. 1, pp. 311–319, Jan. 2018, https://doi.org/10.1016/j.acme.2017.02.008
-
S. Al-Qutaifi, A. Nazari, and A. Bagheri, “Mechanical properties of layered geopolymer structures applicable in concrete 3D-printing,” Construction and Building Materials, Vol. 176, pp. 690–699, Jul. 2018, https://doi.org/10.1016/j.conbuildmat.2018.04.195
About this article
The authors have not disclosed any funding.
The datasets generated during and/or analyzed during the current study are available from the corresponding author on reasonable request.
Qaisar Munir: conceptualization, data curation, formal analysis, validation, methodology, writing – original draft preparation, writing – review and editing. Timo Kärki: conceptualization, formal analysis, validation, project administration, resources, supervision, writing – review and editing.
The authors declare that they have no conflict of interest.