Abstract
During work or long-term storage, grease is susceptible to thermal oxygen or mechanical aging, which affects the performance of grease or even leads to the destruction of the structural surface of grease lubricated products. As the main mechanism of grease lubrication, grease partitioning can explore the aging law of grease and effectively identify whether the grease fails. In this paper, 7014 aerospace grease was selected as the research object and accelerated test was conducted by high temperature thermal oxygen. The combination of grease separation degree and mass change rate was selected for comprehensive characterization of grease separation performance. The results show that the grease partitioning degree has a significant decreasing trend; the quality change has also decreased and the degradation trajectory is similar to the partitioning degree; it is inferred that the main reason for the decrease of grease partitioning performance may be the loss of base oil and the change of thickener fiber structure.
1. Introduction
During product operation, the grease releases base oil to the frictional contact through the oil penetration process as a way to ensure the separation between the rolling body and raceway to ensure the lubricating properties, resulting in low friction and high service life [1]. Aviation grease, which has higher environmental bearing capacity and service life compared to the common grease, is still subject to a series of complex physicochemical processes such as volatilization, oxidation, and oil separation due to thermal oxygen and mechanical stress, resulting in permanent changes in grease performance [2]. The aging of grease will further lead to the destruction of the surface structure of grease lubrication products, such as wear, water damage, etc. and may affect the whole electromechanical equipment. Among them, the grease separation performance is the main mechanism to ensure the lubrication of grease lubrication products, and also can directly judge the life of grease. When the grease is subjected to long-term or extreme high temperature or mechanical aging, the thickener structure suffers damage, which can significantly change the grease partitioning performance [3].
In grease aging tests, a few aging data can be obtained from the products that have been working for a long time, thus most grease aging studies are performed using accelerated testing methods. There are accelerated grease degradation tests simulated under thermal oxygen aging conditions, constant temperature tests [4], step temperature tests [5] and other accelerated test aging methods. In addition, there are also greases accelerated under mechanical aging conditions [6]. The testing of grease separation performance can be done in various ways currently there are high pressure conditions (ASTM D1742), high temperature conditions (ASTM D6184) method, centrifugal method (ASTM D4425), etc. For some costly greases with small sample size of grease, an SKF MaPro test method was developed by Alain et al [7]. In addition, the long-term working environment also affects the oxidation and evaporation of the base oil [8], and the grease parting performance can be more accurately identified by combining the mass change rate of the grease. At present, the aging degree of aviation grease has not been studied. The SKF MaPro test method is a new method for oil separation that can effectively determine the aging degree of grease.
Therefore, in this paper, 7014 aviation grease was selected as the research object, and high-temperature thermal oxygen was used as the stress for accelerated degradation test of the grease. The combination of grease parting performance and mass change rate was selected for the comprehensive characterization of the aging grease parting performance testing method. Finally, the mechanism of grease parting after thermal oxygen aging is described.
2. Methodology
2.1. Grease aging test method
In order to be able to simulate the different accumulations of grease in the product, the grease will be made into 2.5mm, 5mm, 10mm three different thicknesses of the sample evenly coated to the tooling, each thickness of a total of 5 samples designed. The temperature stress is selected as 130℃ for the thermal oxygen test of grease, and the total aging time is set as 28 days, of which the grease is sampled and tested regularly. Among them, the oil separation degree adopts the non-release sampling test method, and each thickness type sample is sampled 5 times in a turn. The mass change rate sampling method was used to select one sample of each thickness for the sample measurement with the release, and one sample was sampled 25 times. The aviation grease selected in this paper is 7014 wide temperature aviation grease, which is formed by thickening synthetic oil with sodium alkyl terephthalate amide, and the specific parameters are shown in the Table 1.
Table 1Performance indicators of lubricating grease
No. | Performance index | Method | Parameters |
1 | Appearance | Visual test | Milky white uniform oil paste |
2 | Density (g/cm3) | Weight test | 0.9 |
3 | 1/4 working cone penetration (mm) | ASTM D1403 | 67 |
4 | Pressure oil bleed (%) | GB/T 392 | 6.41 |
5 | Oil separation area (mm2) | SKF MaPro test | 493 |
6 | Evaporation degree (%) | ASTM D972 | 2.66 |
7 | Similar viscosity (Pa.s) | ASTM D1092 | 653 |
8 | Applicable temperature range (℃) | — | -60-200 |
2.2. Test method
The sampling of oil separation degree is tested by taking samples and then not putting them back, and the test method is mainly chosen from SKF MaPro test method [7]. The method consists of placing a certain amount of grease (10 mm in diameter and 1.1 mm in height) in a circle specified by a sheet of blotting paper, and after continuous heating for 2 h in a constant-temperature flatbed heater at 55 °C, the grease diffuses through oil penetration into the area , as shown in Fig. 1. Where the grease penetration rate is quantified by the area , the larger represents the greater the penetration rate.
The measurement of grease quality is faster than oil bleed, and a set of test samples can be taken several times for testing, which has lower cost and time. Therefore, three test specimens were selected in turn for periodic sampling and testing. The mass of each platform was measured as M0, the mass of the greased platform was measured as M1, and the mass of the regularly sampled greased platform was measured as Mi in turn.
Fig. 1SKF MaPro kit based bleed experiment
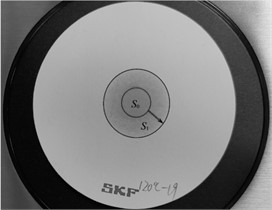
3. Results and discussion
3.1. Grease oil separation
Based on the SKF MaPro test method, grease fractionation measurements were performed for different aging levels, and a set of grease fractionation test results for 0, 3, 9, and 28 day aging times are listed, as shown in the Fig. 2. It was observed that the appearance of the grease deepened significantly with aging time, from milky white to yellowish brown. In addition, it was observed that the oil separation area formed by grease diffusion on the paper gradually became smaller with the increase of aging time.
Fig. 2Appearance and oil separation of grease at different aging time
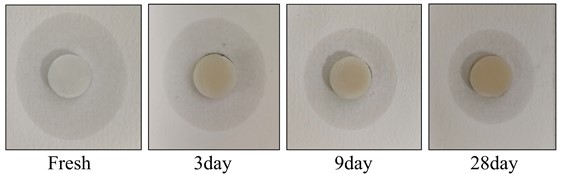
Fig. 3. shows the degradation values of oil separation area for each thickness of grease sample sampled three times for measurement. The results obtained that the difference of oil separation rate of grease with different aging degree is obvious, and the oil separation area decreases with the aging time. The law of decline in which is basically consistent with the quality loss of grease, the degradation rate of grease partitioning is faster in the early stage, and the oil partitioning rate becomes slower as the aging time is extended. In addition, it was observed that the measurement of grease partitioning degree was more discrete and there was no significant variability between different thicknesses.
Fig. 3Oil bleed area of grease at different aging levels
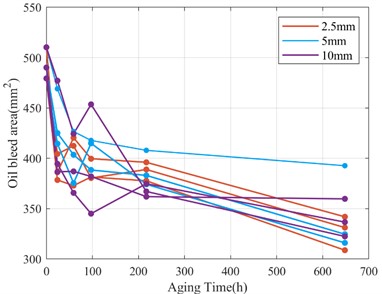
In order to further investigate the degradation law, the mean values were taken for three groups of grease of the same thickness, and the rate of change of oil separation was calculated, as shown in the following equation:
where, represents the rate of change of grease partition degree; is the partition area of grease after aging; is the partition area of fresh grease; is the area of grease itself.
Meanwhile, the double exponential method was selected to fit the rate of change of oil separation for different aging degrees, as shown in Fig. 4. The results obtained that a rapid decrease in oil separation occurred during 0-100 h of grease aging. After 100 h, the change of oil separation slows down and is basically linear. Comparing the rate of change between different thicknesses, 2.5 mm showed a faster rate of decline in grease partitioning compared to 5 mm and 10 mm thicknesses. The specific fitting equations and the goodness of fit are shown in Table 2.
Table 2Fitted equation for oil bleed rate and aging time of grease
Type | Fitted Equation | RMSE | R2 |
2.5 mm | 1.3829 | 0.9806 | |
5 mm | 0.80067 | 0.99248 | |
10 mm | 0.84208 | 0.99252 |
Fig. 4Fitted curve for oil separation and aging time of lubricating grease
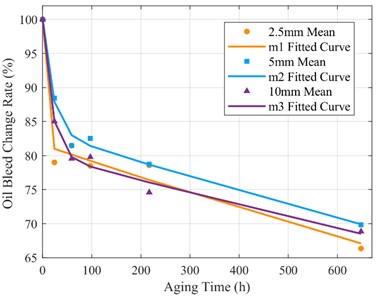
a)Fitted Curve
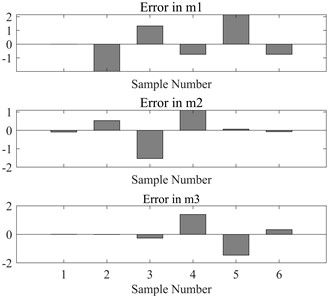
b) Fitting error
3.2. Grease mass loss
Fig. 5 shows the change of grease quality for three different thicknesses. It can be observed that the quality change trend of aviation grease of different thicknesses all decreases significantly and consistently with the aging time. The loss of base oil will affect the grease separation.
In order to be able to compare the mass loss of different thicknesses of grease more closely, the rate of mass change of the grease was calculated as shown in the following equation:
where represents the rate of change of grease mass; is the mass of aged grease and tooling; is the mass of fresh grease and tooling; and is the mass of tooling.
A double exponential function was used to fit the degradation trajectory, as shown in Fig. 6. In the first 100 hours of aging, the degradation degree of the three types of grease was basically the same. When the aging time exceeds 100 hours, the degradation speed of 2.5 mm thickness grease is slightly faster than 5 mm and 10 mm. The change rate of grease quality and the change rate of grease separation degree are similar, and the degradation trajectory basically forms a trend of fast and then slow. The specific fitting equation and the goodness of fit are shown in Table 3.
Fig. 5Mass of grease at different aging levels
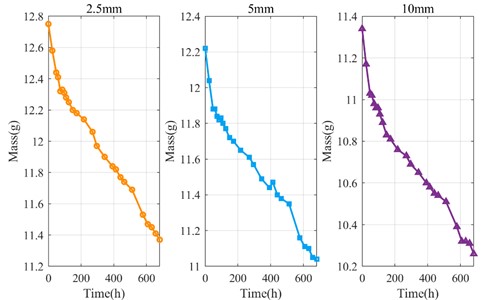
Table 3Fitted equation for mass change rate and aging time of grease
Type | Fitted equation | RMSE | R2 |
2.5 mm | 0.16483 | 0.99696 | |
5 mm | 0.25405 | 0.99027 | |
10 mm | 0.12921 | 0.99538 |
Fig. 6Fitted curve for mass change rate and aging time of grease
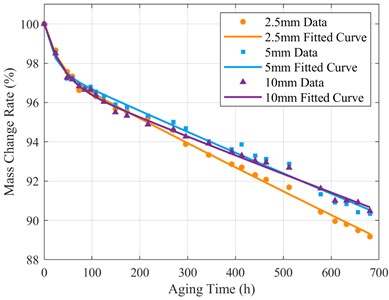
a) Fitted curve
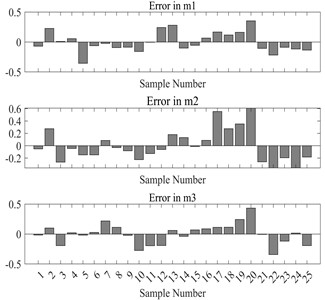
b) Fitting error
3.3. Aging of grease oil bleed mechanism
The grease partitioning occurs a significant decrease with aging time, and this trend is caused by the increase in the concentration of grease thickener and microstructural changes. A significant decrease in grease quality occurred through section 3.2, with values exceeding 10 %. The main mechanism is accelerated by high temperature for a long time leading to evaporation of grease causing loss of base oil and oxidation, while no significant quality loss of thickener occurs. The decrease in the proportion of base oil will lead to the increase in the concentration of thickening agent, which further causes the internal structure of thickening agent to be more compact and the permeability to be reduced, thus reducing the oil separation degree.
In addition, in the tests where the oil separation degree was studied, the oil separation process of grease mainly followed Darcy's law due to the porous medium [9]:
where represents the local speed of oil splitting; is the layout pressure gradient; is the penetration rate, representing the ease of grease penetration in the paper, can be expressed as the size of the grease splitting area in the measurement; is the viscosity of the base oil.
Therefore, analyzing the results of section 3.1 where the oil separation rate decreased by more than 30 %, the more critical point obtained is the change in the microscopic fiber structure of the thickener. The oil bleed rate depends internally on the interplay between the oil affinity and permeability of the thickener matrix [10]. These two properties are mainly determined by the fiber diameter and the volume fraction of the fiber. After the grease is subjected to high temperature thermal oxygen aging, it increases the amount of thermal degradation, the fiber structure may become shorter and smaller in diameter from the previous fiber structure, and the elasticity of the thickener network may also decrease. This makes the aged fiber structure have lower oil affinity and lower permeability, which reduces the grease partitioning degree.
4. Conclusions
In this study, high temperature thermal and oxygen aging tests were conducted on 7014 grease. The effect of thermal oxygen aging on the grease partitioning performance was analyzed. 1) The color of the aged grease was significantly deepened from milky white to yellowish brown; 2) Comparing the grease with different aging degree, the oil separation degree decreases significantly with the aging time, and the degradation law is a rapid decline in the early stage, and the trend of gradual slowing down in the later stage; 3) The quality of grease also decreases significantly with the aging time, the degradation law is similar to the oil separation degree, showing a trend of fast and then slow; 4) Comparing the aging of different thicknesses of grease, the overall aging degree is basically the same. Among them, the quality change rate of 2.5 mm grease in the late aging period is slightly faster than 5 mm and 10 mm; 5) The main reasons for the degradation of grease partitioning performance may be the loss of base oil and the change of thickener fiber structure.
In the future, the microscopic fiber structure of grease can be observed by microscopic performance AFM, SEM, FTIR and other inspection methods to further analyze the oil separation mechanism of aging aviation grease in combination with the degradation law of oil separation.
References
-
P. M. Lugt, “A review on grease lubrication in rolling bearings,” Tribology Transactions, Vol. 52, No. 4, pp. 470–480, Jun. 2009, https://doi.org/10.1080/10402000802687940
-
D. Gonçalves, B. Graça, A. V. Campos, J. Seabra, J. Leckner, and R. Westbroek, “Formulation, rheology and thermal ageing of polymer greases-Part I: Influence of the thickener content,” Tribology International, Vol. 87, pp. 160–170, Jul. 2015, https://doi.org/10.1016/j.triboint.2015.02.018
-
Q. Zhang, F. Mugele, P. M. Lugt, and D. van den Ende, “Characterizing the fluid-matrix affinity in an organogel from the growth dynamics of oil stains on blotting paper,” Soft Matter, Vol. 16, No. 17, pp. 4200–4209, May 2020, https://doi.org/10.1039/c9sm01965k
-
D. Gonçalves, B. Graça, A. V. Campos, and J. Seabra, “Film thickness and friction behaviour of thermally aged lubricating greases,” Tribology International, Vol. 100, pp. 231–241, Aug. 2016, https://doi.org/10.1016/j.triboint.2016.01.044
-
J. Zheng, Y. Li, J. Wang, E. Shiju, and X. Li, “Accelerated thermal aging of grease-based magnetorheological fluids and their lifetime prediction,” Materials Research Express, Vol. 5, No. 8, p. 085702, Jul. 2018, https://doi.org/10.1088/2053-1591/aad31a
-
A. Rezasoltani and M. M. Khonsari, “On the correlation between mechanical degradation of lubricating grease and entropy,” Tribology Letters, Vol. 56, No. 2, pp. 197–204, Nov. 2014, https://doi.org/10.1007/s11249-014-0399-8
-
A. Noordover, S. David, F. Fiddelaers, and A. van den Kommer, “Grease test kit and methods of testing grease,” Google Patents, 2010.
-
V. Wikström and B. Jacobson, “Loss of lubricant from oil-lubricated near-starved spherical roller bearings,” Proceedings of the Institution of Mechanical Engineers, Part J: Journal of Engineering Tribology, Vol. 211, No. 1, pp. 51–66, Jan. 1997, https://doi.org/10.1243/1350650971542318
-
A. Akchurin, D. Ende, and P. M. Lugt, “Modeling impact of grease mechanical ageing on bleed and permeability in rolling bearings,” Tribology International, Vol. 170, p. 107507, Jun. 2022, https://doi.org/10.1016/j.triboint.2022.107507
-
F. Hogenberk, J. A. Osara, D. van den Ende, and P. M. Lugt, “On the evolution of oil-separation properties of lubricating greases under shear degradation,” Tribology International, Vol. 179, p. 108154, Jan. 2023, https://doi.org/10.1016/j.triboint.2022.108154
About this article
The authors have not disclosed any funding.
The datasets generated during and/or analyzed during the current study are available from the corresponding author on reasonable request.
The authors declare that they have no conflict of interest.