Abstract
The paper presents results of measurements of radial vibrations of steel friction pair "rotating roller – fixed segment" under starved and amply lubricated boundary lubrication conditions. Experiments were conducted on computerized tribometer, the friction pair was lubricated with mineral motor oil. Vibrations were measured by means of accelerometer attached to the loaded element of friction pair – segment. Results are presented as vertical vibration spectra of segment versus lubrication mode and load
1. Introduction
The past century has seen a considerable improvement in the performance of machine elements. The average pressure, speed, temperature, accuracy and life have increased as the size, weight, and cost have decreased [1]. This has been accomplished through improved design and manufacture, and advances in lubrication. A second factor however is the reduction of safety margins. One consequence of this reduction is that increasingly accurate predictions of all operational parameters are required, including lubricant performance, to prevent component failure [1, 2].
The lubrication of friction pairs has two major functions: reducing friction and wear as well as dissipating heat [3, 4]. It is can be stated that rich lubrication conditions are better for the friction surfaces. However, in some cases the power losses, especially the no-load losses, lessen with decreasing immersion depth using dip lubrication (f. e. in gears) [3]. The load-dependent power losses are nearly unaffected by minimized lubrication. However, the friction pair bulk temperatures rise dramatically by using minimized lubrication due to a lack of heat dissipation. With minimized lubrication, the scuffing load carrying capacity decreased by up to 60 %, compared to rich lubrication conditions [3]. Therefore, the dominating influence of the bulk temperature is very clear. Starved lubrication leads to more frequent metal-to-metal contact and the generation of high, local flash temperatures must be considered.
A reduced oil film thickness as a consequence of increased bulk temperatures results in more frequent metal-to-metal contacts causing a higher surface shear stress. In combination with a decreased material strength due to a possible tempering effect at high bulk temperatures, the failure risk of pitting damage is clearly increased [3, 5].
The gear micropitting risk is increased by low oil levels, especially at high loads and during the endurance test. The micropitting damage is caused by poor lubrication conditions that are characterized by a too low, relative oil film thickness due to high bulk temperatures [3].
However, low oil levels – and, thus, reduced oil quantities – are sometimes used for the reduction of no-load losses in dip lubricated automotive and industrial friction pairs. Specifically, a higher efficiency can be obtained by reducing no-load power losses such as squeezing, splashing and ventilation losses [3]. These losses can be reduced by lowering the oil volume, namely the oil level in dip-lubricated friction pairs and the oil flow rate with oil injection lubrication. In these cases, the oil amount required for lubrication may be sufficient, but there may be a lack of cooling oil. This leads to high gear bulk temperatures resulting in thin separating films with higher friction and wear on the mating surfaces and, therefore, an increased risk of surface failures such as scuffing, pitting, micropitting and low-speed wear. Therefore, it is very important to establish the limits concerning possible reduction of lubricant quantity that could be tolerated without detrimental effects on friction pair load carrying capacity [3].
Lubricant starvation can occur for a number of reasons. Some examples of these reasons are: low temperature of lubricant (lubricant viscosity is too high to permit flow to the wear surfaces), high temperature of lubricant (lubricant viscosity is too low, causing lubricant to drain off of wear surfaces), start-up process (lubricant pump cannot deliver full lubrication to all surfaces simultaneously) and small or blocked flow path (inadequate lubricant delivered to wear area) [6].
Consequently, a variety of techniques for detection of incipient friction pair (f. e. rolling-element bearings, gears) faults have been developed in the past decades [4]. They rely mainly on vibration analysis and focus on detecting surface damages, such as bearing inner and outer race, and rolling elements faults. Conversely, very few works examine the possibility of employing vibration analysis for detecting improper lubrication or lubrication starved friction pairs [7].
2. Experimental set-up
Vibrational behavior of friction pair was investigated using a computerized tribometer [8] presented in Fig. 1. Steel friction pair “rotating roller – fixed segment” (Fig. 1a) was used under the different lubrication conditions (amply and starved). The height of the roller was 12 mm and the diameter was 50 mm. The height of the segment was 10 mm. The segment was vertically loaded. Radial load was applied to the segment through a lever 4 of the load unit 6 with a screw-spring system (not shown in Fig. 1).
Fig. 1Scheme of friction pair (a) and top view of tribometer (b): 1 – roller, 2 – segment, 3 – accelerometer, 4 – load lever, 5 – lubricant bath, 6 – load unit, 7 – computer, Nl – load force, Ffr – friction force
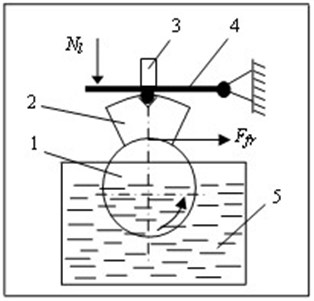
a)
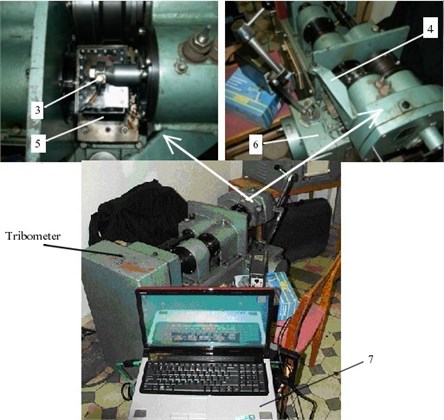
b)
Roller was lubricated by dipping into lubricant bath 5 (Fig. 1) in case of amply lubrication conditions. Semi-synthetic mineral motor oil (SAE 10W/30) was used to lubricate friction pair. In case of lubrication starved friction pair, the following procedure was applied before each experiment. Roller was dipped into the oil and rotated by hand to complete some revolutions. Then oil level in the bath was reduced below the roller. However, some oil remained on the surface of the roller. This amount of oil was used as lubricant under starved lubrication conditions.
Initially, friction surfaces of roller and segment were finished to the roughness 2.5 µm. Then the run-in process under amply lubrication conditions was applied to allow surfaces to become well aligned. After that specimens were used in experiments.
Other conditions of the experiments were following: rotational speed of the roller was constant – 320 rpm (frequency 5.3 Hz), sliding velocity – 0.84 m/s. The load force was varied from 0 (no-load conditions) to 1000 N (maximum contact pressure is equal to 5 MPa).
A piezoelectric accelerometer 3 (Brüel & Kjær mod. 4375, 0.1 – 16500 Hz useful range, 55 kHz resonance frequency) attached to the segment measured radial vibration of the segment (Fig. 1). Brüel & Kjær LAN-XI Type 3660-D data acquisition hardware was used. The measured signal is amplified and filtered with low band pass filter at a 2 Hz cutoff frequency. Measured acceleration signal was integrated using computer. Data analysis was performed with the aid of Brüel & Kjær Pulse Reflex software.
3. Results and discussion
Fig. 2 shows amplitude spectrum of vibration velocity of the segment under amply lubricated boundary lubrication conditions. Amplitude spectrum of vibration velocity of the segment under starved lubricated boundary lubrication conditions is presented in Fig. 3.
Fig. 2Segment vibration velocity spectrum obtained when friction pair was lubricated with motor oil under amply boundary lubrication conditions
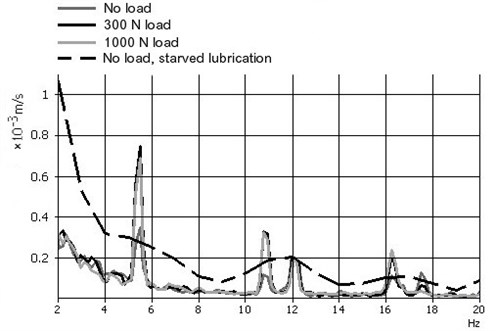
Fig. 3Segment vibration velocity amplitude obtained when friction pair was lubricated with motor oil under starved boundary lubrication conditions
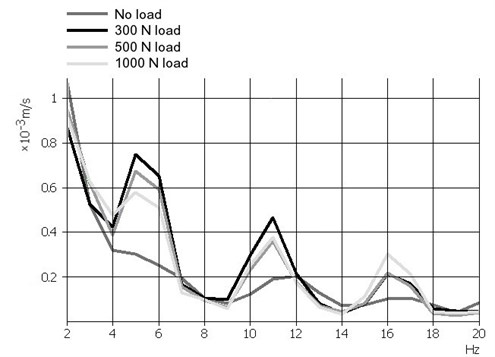
It can be seen from Fig. 2 that segment vibration intensity doesn’t depend on load under amply lubricated boundary lubrication conditions. If the load is removed velocity amplitude decreases about 2.5 times (Fig. 2). In case of starved lubrication (Fig. 3) vibration amplitude at frequency 2 × rpm is about 1.3 times bigger as compared to the value, obtained in rich lubrication case. The velocity amplitude at frequency 1 × rpm becomes load dependent in case of starved lubrication and decreases with increase of the load. No sufficient changes in velocity are obtained at frequency 3 × rpm. When the load is removed, vibration intensity decreased (Fig. 3), but remains bigger as compared with rich lubrication case in almost whole investigated frequency range between 2 and 20 Hz.
4. Conclusions
1. The influence of the improper lubrication of friction pair was detected as an increase in the vibration velocity amplitude spectral components at frequency 2 × rpm.
2. The results raise the question of the possibility of using vibration analysis for detecting other processes in lubricant quality, like external contamination or aging process.
References
-
Damiens B., Venner C. H., Cann P. M. E., Lubrecht A. A. Starved lubrication of elliptical EHD contact. Journal of Tribology, Vol. 126, Issue 1, 2004, p. 105-111.
-
Padgurskas J., Rukuiža R., Bubulis A. Analysis of tribological properties of precise contact pairs. Journal of Vibroengineering, Vol. 13, Issue 2, 2011, p. 327-333.
-
Hohn B.-R., Michaelis K., Otto H.-P. Flank load carrying capacity and power loss reduction by minimized lubrication. Gear Technology, 2011, p. 53-62.
-
Padgurskas J., Kreivaitis R., Kupčinskas A., Žunda A. Modification of rapeseed oils with free fatty acids. Mechanika, Vol. 17, Issue 2, 2011, p. 203-207.
-
Zurovski W. Structural determinants maximizing wear resistance of friction joints. Journal of Vibroengineering, Vol. 14, Issue 2, 2012, p. 538-545.
-
DeCamillo S., He M., Cloud C. H., Byrne J. M. Journal bearing vibration and SSV hash. Proceedings of the Thirty-Seventh Turbomachinery Symposium, III Houston, Texas, 2008, p. 13-23.
-
Boškoski P., Petrovčič J., Musizza B., Juričic D. Detection of lubrication starved bearings in electrical motors by means of vibration analysis. Tribology International, Vol. 43, Issue 9, 2010, p. 1683-1692.
-
Mokšin V., Vekteris V., Kilikevičius A. Computerized tribometer for experimental research of tribological properties of lubricants and materials. Proceedings of First International Summer School on Mechatronic Systems “UPTRONIC 2009”, Wisla, Poland, 2009, p. 291-308.