Abstract
Mesh stiffness always is a studying focus of gear dynamics. In the issue, a solution for the calculation of mesh stiffness considering the sliding friction effect is constructed, and the influence of the sliding friction on mesh stiffness is analyzed. Further, the analytical results indicate mesh stiffness is sensitive to the sliding friction in poorly lubricating conditions specially. These contributions would not only simplify the calculation of mesh stiffness associated with the sliding friction but also be good for assessing the dynamic behaviors of spur gear drives in some special operating conditions
1. Introduction
Mesh stiffness always is one of studying focuses of gear dynamics since it is important for inherent properties and dynamic response of gear drives. There are many literatures discussing mesh stiffness over the past several years. In these issues [1-8], the researchers constructed analytical solutions of mesh stiffness such as Ishikawa method. However, how the sliding friction affects mesh stiffness is yet to be resolved or addressed by the gear dynamics researchers. Thus, in this study, an incremental angle of action caused by the sliding friction is included into Ishikawa model for the calculation of mesh stiffness considering the sliding friction effect as well as the impact of the sliding friction on mesh stiffness is analyzed. Furthermore, the analytical results indicate that mesh stiffness of spur gear drives is sensitive to the sliding friction in poor lubrication conditions specially. These contributions would be helpful for assessing mesh stiffness associated with the sliding friction.
2. The incremental angle of action caused by the sliding friction
2.1. The sliding friction direction on the tooth
The relative velocity on the tooth flank, only at the pitch point, is equal to zero during the meshing process of spur gear drives. Therefore, the sliding friction direction on the tooth of the driving gear is apart from the pitch point. In contrast, that on the tooth of the driven gear is pointing to the pitch point. The sliding friction direction on the tooth of a gear pair is given in Fig. 1.
Fig. 1The sliding friction directions on the tooth of a gear pair
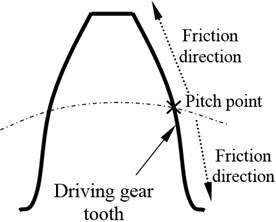
a) On the driving gear tooth
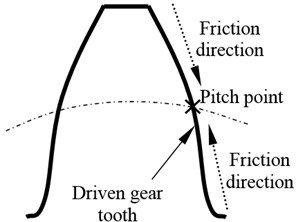
b) On the driven gear tooth
2.2. The pressure distribution on the tooth
The contact ratio is important for describing the pressure distribution on the tooth. The relationship between the contact ratio ε and the deformation of the tooth during the meshing process is shown in Fig. 2.
In Fig. 2, A, B, C, D and E are the mesh points, is the pitch of the base circle, is the flexibility of the tooth at any mesh points, which can be expressed as [8, 9]:
where the subscript 1 and 2 represent the pinion and the gear respectively. Meanwhile, the equations of the variables in Eq. (1) are listed in Table 1.
Table 1The equations of the variables in Eq. (1)
Value name | Equations [8, 9] |
In Table 1, is the elastic modulus, is the Poisson ratio, is the root thickness, , and are the geometric parameters of gears and is the angle of action.
According to the tooth deformation, as shown in Fig. 2, the pressure at the mesh points as A, B, C, D and E, can be derived in a piecewise form as:
where is the power, is the input pinion speed, is the radius of the reference circle of the pinion and is the pressure angle of the reference circle of the driving gear.
2.3. The solution constructed
The solution for the calculation of mesh stiffness associated with sliding friction, namely Ishikawa model considering the sliding friction effect, is constructed and shown in Fig. 3.
Fig. 2The relationship between the contact ratio and the deformation of the tooth
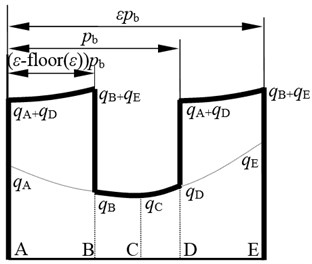
Fig. 3Ishikawa model considering the sliding friction
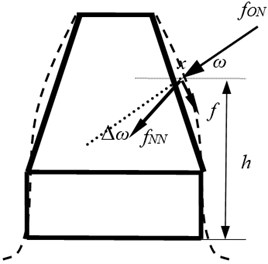
As given in Fig. 3, the change, comparing the proposed model with Ishikawa model [8, 9], is essentially the incremental angle of action caused by the sliding friction. Therefore, considering both the sliding friction direction as shown in Fig. 1 and the pressure distribution on the tooth described as Eq. (2), the incremental angle of action can be deduced as:
3. Simulation and analysis
Several different sliding friction coefficients and the basically geometric parameters of an example case, which are from the reference [1], are listed in Table 2.
Table 2The simulation parameters
Basic geometric parameters | Driving gear | Driven gear | Unit | Description | ||
8 | mm | Module | ||||
20 | deg | Pressure angle | ||||
95 | 22 | – | Number of tooth | |||
Friction coefficient | Condition 1 | Condition 2 | Condition 3 | |||
0.05 | 0.3 | 0.64 |
Table 3The average mesh stiffness
Ref. [1] | Without the friction | Condition 1 | Condition 2 | Condition 3 | Unit | |
Average mesh stiffness | 25 | 23.2099 | 23.2607 | 23.9779 | 26.3876 | N/μm mm |
The incremental angle of action of the pinion and that of the driven gear are simulated and shown in Fig. 4. Moreover, the time-varying mesh stiffness considering the sliding friction effect is given in Fig. 5 and the results of the average mesh stiffness are listed in Table 3.
The calculating error of the average mesh stiffness based on between the proposed model and Ishikawa model, and the difference of the average mesh stiffness between without and with the sliding friction effect can be reduced to one equation, which can be defined as:
where is the average mesh stiffness without the sliding friction based on the proposed model and is the benchmark from the reference [1] or is the average mesh stiffness with the sliding friction and is that without the sliding friction and based on the proposed model. The calculating error of the example case is 7 %, which is acceptable. Moreover, the differences of the average mesh stiffness between without and with the sliding friction effect are listed in Table 4.
Fig. 4The incremental angle of action
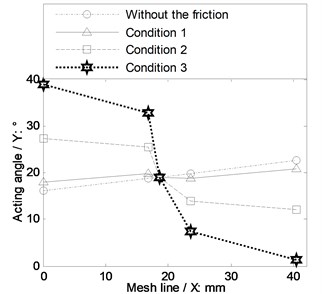
a) On the driving gear
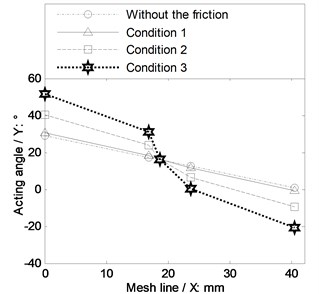
b) On the driven gear
Fig. 5The time-varying mesh stiffness considering the sliding friction effect

The results in Table 4 indicate the average mesh stiffness of spur gear drives is sensitive to the sliding friction in poor lubrication conditions specially. Moreover, in the case of Fig. 4 and Fig. 5, the angle of action would be increased in the engagement, and not be changed at the pitch point and be decreased at the meshing-out point due to the sliding friction. Furthermore, the trend of the time-varying mesh stiffness of spur gear drives would be changed.
Table 4The differences of the average mesh stiffness between without and with the sliding friction effect
Condition 1 | Condition 2 | Condition 3 | |
The difference | 0.2 % | 3.31 % | 13.69 % |
4. Conclusions
In the study, two important works can be extracted as follows:
1) The incremental angle of action caused by the sliding friction is joined into Ishikawa model to construct a solution for the calculation of mesh stiffness considering the sliding friction effect of spur gear drives.
2) The impact of the sliding friction on mesh stiffness of spur gear drives is analyzed and the results indicate mesh stiffness is sensitive to the sliding friction in poorly lubricating conditions specially.
These conclusions would be benefit to assess mesh stiffness associate with the sliding friction and help to analyze the dynamic behaviors of spur gear drives in some special operating conditions.
References
-
Pedersen R., Santos I. F., Hede I. A. Advantages and drawbacks of applying periodic time-variant modal analysis to spur gear dynamics. Mechanical Systems and Signal Processing, Vol. 24, Issue 5, 2010, p. 1495-1508.
-
Xihui Liang, Ming J. Zuo, Tejas H. Patel Evaluating the time-varying mesh stiffness of a planetary gear set using the potential energy method. Journal of Mechanical Engineering Science, 2013, p. 1-13.
-
Li S., KahramanA. A spur gear mesh interface damping model based on elastohydrodynamic contact behavior. International Journal of Powertrains, Vol. 1, Issue 1, 2011, p. 4-21.
-
Li S., Kahraman A. A tribo-d ynamic model of a spur gear pair. Journal of Sound and Vibration, Vol. 332, 2013, p. 4963-4978.
-
Song He, Todd Rook, Rajendra Singh Construction of semianalytical solutions to spur gear dynamics given periodic mesh stiffness and sliding friction functions. Journal of Mechanical Design, Vol. 130, 2008, p. 1-9.
-
Gang Liu, Robert G. Parker Impact of tooth friction and its bending effect on gear dynamics. Journal of Sound and Vibration, Vol. 320, 2009, p. 1039-1063.
-
Lassâad Walha, Tahar Fakhfakh and Mohamed Haddar Nonlinear dynamics of a two-stage gear system with mesh stiffness fluctuation, bearing flexibility and backlash. Mechanism and Machine Theory, Vol. 44, 2009, p. 1058-1069.
-
Shi J. L., Ma X. G., Xu C. L., Zang S. J. Meshing stiffness analysis of gear using the ishikawa method. Applied Mechanics and Materials, Vol. 401, 2013, p. 203-206.
-
Zhu X., et al. Analysis of Load Capacity of Gears. Beijing, Higher Education Press, 1992.
About this article
The authors are grateful for the financial support provided by NSFC under No. 51105194 and No. 51375226 as well as CSC under contract No. 201206835011.
In addition, the authors declare that there is no conflict of interests regarding the publication of this article.