Abstract
The main goal of this paper is to show dynamic behavior of carbon fiber drive shaft. In the paper, authors showed the effect of passing shaft resonance (1st critical speed). The effect of a shaft passage through critical state under conditions of acceleration and deceleration was shown. The main conclusion of the research is the necessity of taking into account an influence of changes rate on the characteristics of the composite structure elasticity. Taking into account the static elasticity characteristic only, even if it is obtained from empirical investigations of a real object, does not allow for the proper draw conclusions, so we can’t predict critical state of such shaft properly.
1. Introduction
Composite materials find their application as elements of plating and finned structures (in aircrafts, gliders or yachts) as well as in rotating systems (e.g. turbine blades). However, since products of carbon composites are characterized by a high strength at small mass, their natural application seems to be production of elements used for power transmission, it means for drive shafts. Currently applied structure solutions of this type of drive transmissions are kept strictly secret (e.g. for Formula 1 drives). This means, that there are no publications concerning even preliminary calculations of composite structures, or tests results, not to mention investigations on complex dynamic effects, which occur in such structures in a natural way.
As it is well known, products of carbon composites are characterised by a high elasticity, are strongly non-linear and anisotropic. These features cause that traditional calculation methods applied e.g. at designing steel structures are not suitable in this case. Products designed in such way usually are multiply oversized (which is not without meaning when considering prices of the material), and very often do not meet the basic structural and strength requirements.
According to the available knowledge, a carbon fiber shaft in a form of a cylindrical profile („tube”) is characterised by a high torsional rigidity and strength at a small specific weight. This is especially important at forming long shafting (e.g. aircraft and ship power transmission systems) due to a small static deflection under a dead weight. In addition they can be designed in such a way that they will prevent effects of self-exciting vibrations. However, there are no references explaining this problem. A small weight is especially important for long shafts operating at a certain angle to the horizontal, since static deflections under a dead weight are also small.
Due to the lack of the dynamic calculations methodology, it seems necessary to perform experimental investigations of dynamics of carbon fiber drive. The results obtained in this work should make it possible to develop the accurate description of influences within such structure, to prepare recommendations for choosing calculation models and finally for proposing the rational designing method and optimization of carbon fiber shafts.
Structural calculations of steel (or more generally: metal) machine shafts constitute the topic of the classical lecture of Machine Design Basics [1-3] and it could have appeared that all problems related to this topic were solved. Dynamic problems are usually limited to determination of critical states (rotational speed) [1, 3-5].
Quite different is the situation in case of shafts made of carbon composites or carbon-aramide ones. First of all, such composite is anisotropic structure not satisfying at a deformation in whichever direction the Hook’s law, and secondly it is not a material in the current understanding, since it obtains a material feature only after being shaped (!). Thus, it is not possible to transfer experimental results performed on an ideal sample (usually in a form of flat beam), on a drive shaft operating under complex load conditions. Presently it can be stated, that several published theoretical papers concerning the mechanics of composites and empirical investigations leading to propositions of certain mathematical models [6-9], are still within laboratory tests. When investigating the dynamics of fast-rotating systems with composite elements one is finding, all the time, new effects requiring complex examinations [8, 10-15].
2. Experimental research
We will start building our research stand by considering that the future mathematical model of such system has to be as simplest as possible, so our future model will assume the shaft as the massless beam and the mass concentrated in the centre of its length (as a disc). The previous works of author indicated that is the simplest dynamic model of the drive shaft that should take proper conclusions. Other benefit of defined in such way shaft model is possibility to manipulate the disc mass to obtain experimentally the expected critical speeds (this is related to the possibilities of our research stand).
Since in engineering applications the main emphasis – at the analysis of the rotating shaft dynamic behaviour – is placed on looking for critical states, we will limit the model to the one, which takes into account only transverse vibrations. This also allows to reduce the problem to the forced damped vibrations of the system with one degree of freedom.
Fig. 1Experimental stand for testing the shaft transverse vibrations
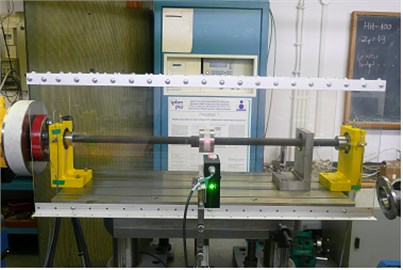
Having such assumptions the experiment was performed in the research stand, shown in Fig. 1. The shaft bearing was realised with using self-aligning bearings. In addition, the possibility of the shaft necks free shifting in the axial direction was assured. The displacement measurement was carried out by means of the laser displacement sensor.
Fig. 2Comparison of the results of acceleration and deceleration, with a velocity of 100 RPM/sec
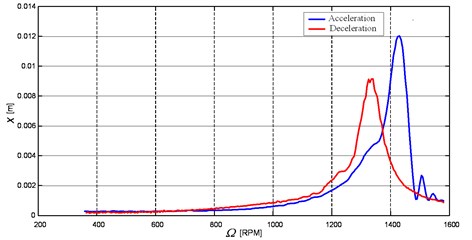
The described experiment allowed for the qualitative recognition of the effect. The amplitude-frequency characteristic at increasing and decreasing the rotational speed are presented in Figs. 2-5. Shifting of the characteristics at acceleration and deceleration indicates non-linearity of the system, while the amplitude value change as a function of the acceleration velocity, different than for the linear system, confirms the dependence of elasticity on a deformation velocity (Fig. 6).
Fig. 3Comparison of the results of acceleration and deceleration, with a velocity of 50 RPM/sec
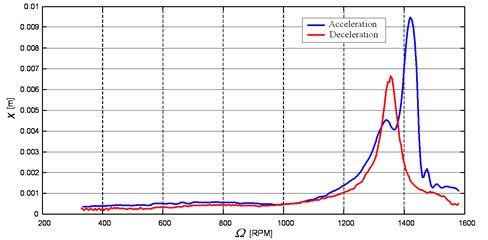
Fig. 4Comparison of the results of acceleration and deceleration, with a velocity of 25 RPM/sec
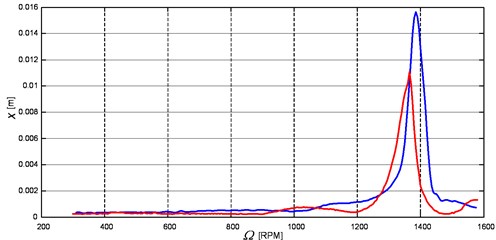
Fig. 5Comparison of the results of acceleration and deceleration, with a velocity of 10 RPM/sec
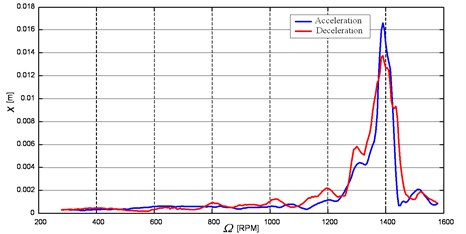
Fig. 6Interpretation of various amplitude-frequency characteristics at accelerations and decelerations
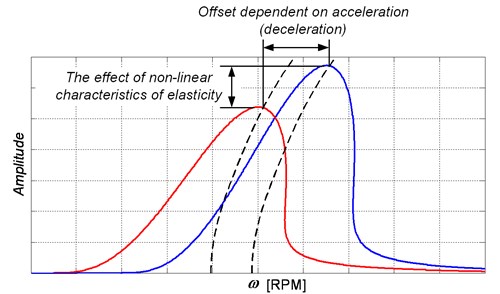
3. Conclusions
In case of thin-walled carbon fiber drive shafts loaded with discs of a high mass (the discrete model) experiment allows to show the strong dependence of critical states on the velocity of acceleration (deceleration). Such results suggest that exist the dependence between velocity of shaft deflection and its elasticity characteristic.
The performed experiment lead to the following final conclusion: at designing carbon fiber drive shafts the main factor influencing on construction should be the dynamic criterion, since application of only static criteria could lead to serious errors. To be able to fully assess the state and properties as well as to undertake an attempt of the proper designing of the carbon fiber shaft it is necessary to apply the dynamic criteria.
References
-
Dąbrowski Z. Machine Shafts. Warsaw, 1999, (in Polish).
-
Dietrich M. Machine Design Basics. Warsaw, 1995, (in Polish).
-
Osiński Z., Bajon W., Szucki T. Machine Design Basics. Warsaw, 1980, (in Polish).
-
Dąbrowski Z., Deuszkiewicz P. Designing of high-speed machine shafts of carbon composites with highly nonlinear characteristics. Key Engineering Materials, Fundamentals of Machine Design, Vol. 490, 2011, p. 76-82.
-
Łączkowski R. Balancing of Rotating Elements. Warsaw, 1979, (in Polish).
-
Boczkowska A., Kapuściński J., Lindemann Z., Witemberg-Perzyk D., Wojciechowski S. Composites. Warsaw, 2003, (in Polish).
-
Głowacki H. Technical Mechanics – Dynamics. Warsaw, 2001, (in Polish).
-
Kurnik W., Tylikowski A. Mechanics of Laminated Elements. Warsaw, 1997, (in Polish).
-
Osiński Z. Theory of Vibration. Warsaw, 1980, (in Polish).
-
Batko W., Dąbrowski Z., Engel Z., Kiciński J., Weyna S. Modern Research Methods of Vibroacoustic Processes Vol. 1. WN ITE–PIB, Radom, 2005, (in Polish).
-
Batko W., Dąbrowski Z., Kiciński J. Nonlinear Effects in Technical Diagnostics. Warsaw, 2008.
-
Batko W., Dąbrowski Z. Modern Research Methods of Vibroacoustic Processes (Technical Applications) Vol. 2. WN ITE–PIB, Radom, 2006, (in Polish).
-
Deuszkiewicz P. Analysis of dynamic properties of machine shafts made from carbon-epoxy composites. XXXVIII Symposium Diagnostics Machine, Katowice, 2011, (in Polish).
-
Deuszkiewicz P., Grządziela A. Dynamic testing machine shaft made of carbon composite. XXIII Machine Design Symposium, 2007, (in Polish).
-
Kurnik W., Tylikowski A., Starczewski Z., Przybyłowicz P. Unconventional Materials in the Diagnosis and Active Vibration Reduction. Diadyn, WN ITE-PIB, Radom, 2008, (in Polish).