Abstract
In the past decades, virtual maintenance has been a vital tool to assist product maintainability design. However, these is few report about the vibration effects on maintenance which has been proved significantly to enhance worker fatigue. In this study, we develop a platform, Semi-physical Simulation Platform (SSP), to analyze vibration effects on maintenance where an advanced Rapid Upper Limb Assessment (A-RULA) is also proposed to realize both static and dynamic assessment of worker postures and fatigue. Furthermore, a series experiments with a specified maintenance task are taken into SSP to investigate the vibration effects on maintenance. The results demonstrate reasonable conclusions about the effects of various frequency vibration and fatigue on maintenance time, maintenance errors, and A-RULA obtained from SSP.
1. Introduction
As a vital index of complex product, the maintainability is always focused by users [1]. Successively, virtual maintenance acts as an effective tool to assist the maintainability design while engine designing [2]. With the developing of technique, high maintainability with less repair time and little errors is required considering most of the possible factors in future working environments.
One of the factors that presumably influences so called “human performance” is the vibration that the maintenance worker undergoes which is an issue that has long been of concern and brings the occupational hazard in vibration environment. Both the references recognize the difficulty in predicting the effect of a vibration level on human performance [3, 4]. In particular, the possible relationship between vibration and psycho physical fatigue is even more uncertain.
In the past decades, references [5, 6] carried out by reference indicated that 20-30 % of all fatal errors on the busiest airport were connected to human errors in maintenance process. NASA has begun work on involvement of human factors assessment of vibration effects on visual performance during launch since 2009 [7]. The primary objective of Short Duration Bioastronautics Investigation (SDBI) 1904 is to determine visual performance limits during operation vibration and g-loads. G. E. Conway quantifies whole-body vibration effects on human performance by identifying those moderating variables that influence the degree to which performance is affected [3]. A. Messina describes an experimental study aimed at determining the existence and the correlation between physiological human performance within the field of heavy goods vehicles and absorbed whole-body vibrations [8]. Some other researches show a possible link between a constant low frequency vibration and fatigue. However, reference [9] explicitly concludes that an extensive study on a possible relationship between vibration and fatigue could be considered, however it is likely that such research would be costly to conduct. In references [10-12], the authors were not able to identify a clear trend which conclusively showed the influence of whole-body vibrations on human performance (in the guise of simple or choice reaction time) especially when human subjects undergo vibration dose values within shoes limits recommended as maximum in working environments.
The existing research succinctly described above demonstrated that the authors planned experimental work aiming at investigating the “existence of a relationship between vibration and maintenance”. In this respect, simple and complex reaction time tests were chosen to be representative of human performance. This choice was not only dictated by previous studies but also and mainly by the fact that such a parameter can decisively influence human performance when making a decision aimed at avoiding repair errors. However, few researcher concerns the influence of vibration effects on maintenance tasks especially for helicopter engine that is working nonstop.
In this paper, we develop a program mainly consisting of systematic architecture, color-based hierarchies of vibration, and advanced RULA (A-RULA) all of which are proposed to deal with the problems aforementioned. The corresponding and reasonable conclusions about the effects of high frequency vibration and fatigue on repair time, maintenance errors, and RULA are derived in the established visual environment.
2. Vibration modeling and simulation in virtual environment
2.1. The developed semi-physical simulation platform (SSP)
To analyze vibration effects on maintenance, a platform named Semi-physical Simulation Platform for Analysis of Vibration Effects on Maintenance is designed and developed. SSP consists of three main parts of Virtual Environment (VE) containing Virtual Vibration Environment Simulation System (VVESS) and Avatar, I/O-interface, and Physical Environment (PE), as shown in Fig. 1.
1) Functionalities of each part.
VE: VVESS, object-oriented system, is used to simulate virtual vibration of the established 3D models of components and system of engine which will be driven and generate animation by calling library functions of OpenGL when real vibration data is acquired. Avatar is a virtual man interacting with both VVESS and I/O-interface. Moreover, the A-RULA model discussing in the following section is applied to avatar to assess the maintenance errors, working posture, and fatigue.
I/O-interface: This part is employed as the interface of VRP and physical system.
PE: A real man tested stands on a vibration table with random vibration signal to reproduce the vibration environment of engine.
Fig. 1The systematic architecture of SSP
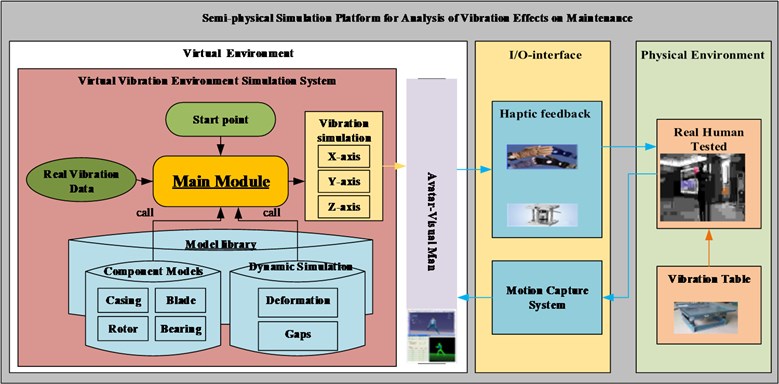
2) Two main processes within SSP.
One is the process of virtual vibration simulation. The Main Module of VVESS is executing and checking the state value of real vibration data during all simulating process. The Main Module will call the corresponding 3D models of engine that pre-established once the state value of real vibration data is true. And then the virtual vibration of engine can be simulated with the results of three dimensional values. The other is called cycle process of Act-Touch-Sense (CP-ATS). When tested and the first process accomplished, the real human tested on the vibration table first ‘Act’ with the purpose of touching and maintaining the engine. The motion capture system acquires the ‘Actions’ of real human and send them to Avatar who will ‘Touch’ the 3D models of engine that vibrating. All the information generated during the ‘Touch’ period can be felt by haptic feedback which will be sensed by real human tested.
2.2. Human factors assessment of vibration effects on maintenance based on A-RULA
The existing whole-body assessment methods are concerning the effects of various levels of vibration on human body, such as ISO 2631-1:1997 [13] and BS 6841-1987 [14]. In this study, we proposed a new and succinctly assessment model called A-RULA to assess human factors of vibration effects on maintenance.
The A-RULA, as Fig. 2 shown, is aiming to investigating the differences of working postures and state of fatigue under vibration conditions. Note that the differences of repair times and numbers of repair errors can be acquired directly by timers and counters during corresponding experiments.
The A-RULA combines the traditional RULA method for static working postures and an advanced part to assess effects on human dynamically. First, three important factors, endurance time, external load, and Maximum Voluntary Contraction (MVC), are introduced to the dynamic advanced part which was first used in Ergonomics field by Ma L. [15]. Focuses on the effects of muscle fatigue, distinguishes whether muscle fatigue or body posture causing uncomfortableness of body, optimizing the recommendations of evaluation, and thereby making evaluation much more precise. Meanwhile, they make the evaluation changes with endurance time dynamically instead of static evaluation coherence instead of intermittency. Second, in accordance with BS 6841-1987, we define the comfort value based on the weight RMS value of vibration. Finally, the total score of body comfort would be obtained based on all of these factors.
Fig. 2The topology of A-RULA
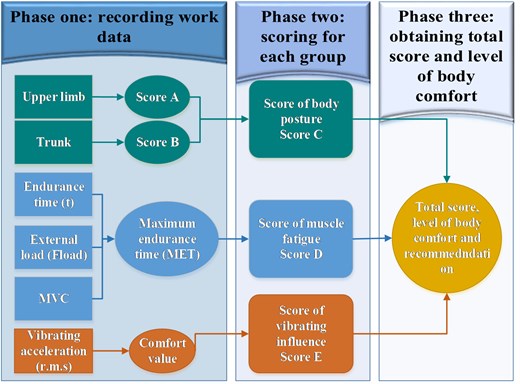
3. Experiment
In this study, a series of experiments are carried out to figure out vibration effects on maintenance in virtual environment. Fifteen crewmembers tested are targeted for this study as well as all the systems aforementioned in section 2.1 (Fig. 1). The real vibration data was collected from real-world maintenance processes of helicopter engine with vibration. Each person tested undergoes experiments of three different vibration conditions with frequencies of 0 Hz, 100 Hz, and 60 Hz, respectively.
3.1. The procedure of each experiment
In this section, the main procedure of an individual experiment is described in details. An individual experiment is one person tested under one of the three different vibration conditions.
1) 3D models establishing of helicopter engine.
The static models (component models and system model of engine) and dynamic behavior models are pre-established based on geometrical models of engine. This model is built from a certain type of real helicopter engine as the prototype, which define as a member variable and function model. Finally, we use the DELMIA virtual environment to realize the modeling and animation engine simulation, and use C++ to develop the dynamic vibration display system, which is called Helicopter-Engine Vibration Visible Modeling and Dynamic show system (HEVADS). Fig. 3 shows the established and assembled 3D model of the tested helicopter engine.
Fig. 33D model of engine system
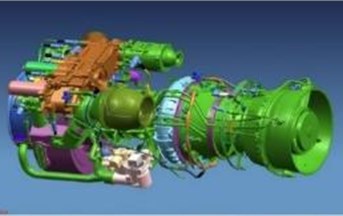
a)
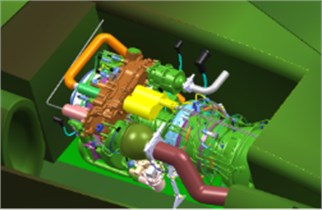
b)
2) Mounting and calibration.
This step is to connect and calibrate the three main aspects as a whole. Fig. 4 shows the control, including various postures and behaviors, calibration process of a real human to the Avatar.
Fig. 4Postures and behaviors calibration process
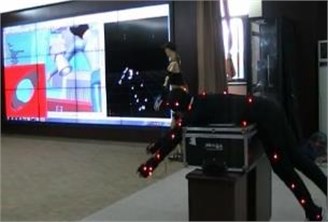
3) 3D model of engine with virtual vibration simulation: the first main process within SSP.
Start the Main Module and input the real vibration data to the Main Module which will call models in library and simulate virtual vibration.
4) CP-ATS start-up.
With the virtual vibration simulating, one crewmember tested acts to start the maintenance process according to the pre-determined maintenance schedule. Each action of the crewmember is end up with the “sense”. Fig. 5 shows postures and behaviors series of the Avatar during CP-ATS.
Fig. 5Postures and behaviors series of the Avatar during CP-ATS
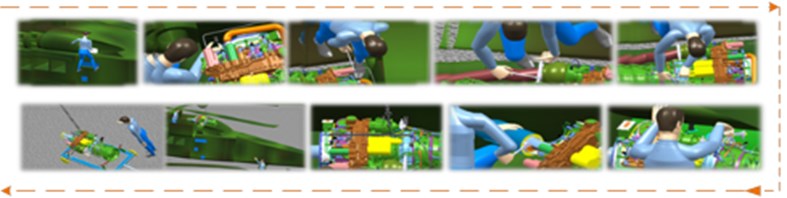
3.2. Results and discussions
In this study, three important indexes, maintenance time, maintenance errors, and A-RULA, with respect to maintenance are obtained and discussed to analyze the vibration effects on maintenance. As aforementioned, the values of maintenance time and maintenance error for each experiment can be acquired directly by timer and counter. Additionally, the corresponding A-RULA value can be calculated based on A-RULA model and data from the Avatar. Table 1 records all the experimental results of 15 crewmembers under three different conditions.
Some statistic results can be achieved according to these records listed in Table 1, shown in Fig. 6.
Table 1Experimental results
No. | 0 Hz | 60 Hz | 100 Hz | ||||||
MT/min | ME | A-RULA | MT/min | ME | A-RULA | MT/min | ME | A-RULA | |
1 | 21 | 0 | 2 | 23 | 0 | 6 | 23 | 1 | 5 |
2 | 23 | 0 | 6 | 24 | 1 | 4 | 22 | 0 | 7 |
3 | 19.5 | 0 | 4 | 26 | 1 | 7 | 27 | 0 | 6 |
… | … | … | … | … | … | … | … | … | … |
13 | 23 | 1 | 6 | 25 | 1 | 7 | 29 | 0 | 6 |
14 | 21 | 0 | 4 | 26 | 0 | 4 | 27 | 1 | 7 |
15 | 22 | 0 | 6 | 23 | 0 | 6 | 26 | 2 | 6 |
Sum | 331 | 7 | 68 | 371.5 | 12 | 86 | 397.5 | 15 | 93 |
Ave | 22.17 | 0.47 | 4.53 | 24.77 | 0.8 | 5.73 | 26.5 | 1 | 6.2 |
The results of AVERAGE carried out on the data collected showed that the effect of vibration on Maintenance time and A-RULA was statistically significant. Fig. 6 shows the relationship between maintenance time, maintenance errors and A-RULA at different vibration frequencies. An approximate linear relationship can be seen in the figure, all these three values increase in proportion to frequency of vibration.
Fig. 6Relationship between MMT, MME, MRULA and vibration frequency
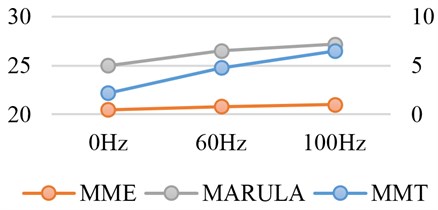
4. Conclusions
Considering the importance of vibration effects on maintenance, in this study, the SSP for analysis of vibration effects on maintenance is established. A series experiments with a specified maintenance task of a helicopter engine are applied to SSP to investigate the vibration effects on maintenance. The results demonstrates that the vibration environment with higher frequency results in worse maintenance experience. Additionally, the sequential maintenance decision making based on the worse experience would lead to an inaccuracy direction. In the near future, on the one hand, some measures will be taken, such as staff training with various maintenance tasks under different vibration levels, to reduce vibration effects on maintenance. On the other hand, further researches on maintenance decisions would be made based on the vibration effects.
References
-
Siegel D., Ly C., Lee J. Methodology and framework for predicting helicopter rolling element bearing failure. IEEE Transactions on Reliability, Vol. 61, 2012, p. 846-857.
-
Liu X.-H., Song G.-M., Cui X.-L., Xu B.-H., Wang K., Wang Z.-B. Development of a virtual maintenance system for complex mechanical product. Advances in Mechanical Engineering, 2013.
-
Conway G. E., Szalma J. L., Hancock P. A. A quantitative meta-analytic examination of whole-body vibration effects on human performance. Ergonomics, Vol. 50, 2007, p. 228-245.
-
Paddan G. S., Holmes S. R., Mansfield N. J., et al. The influence of seat backrest angle on human performance during whole-body vibration. Ergonomics, Vol. 55, 2012, p. 114-128.
-
Liang G. F., Lin J. T., Hwang S. L., Wang E. M. Y., Patterson P. Preventing human errors in aviation maintenance using an on-line maintenance assistance platform. International Journal of Industrial Ergonomics, Vol. 40, 2010.
-
Latorella K. A., Prabhu P. V. A review of human error in aviation maintenance and inspection. International Journal of Industrial Ergonomics, Vol. 26, 2000, p. 133-161.
-
Thompson S. G., Holden K., Ebert D., Root P., Adelstein B., Jones J. Human factors assessment of vibration effects on visual performance during launch, http://www.nasa.gov/mission_pages /station/research/experiments/703.html.
-
Messina A., Schiraldi C., Sheldon A. M. Influence of vibrations on mental human performance for driving safety in heavy vehicles. Conference on Human System Interactions, 2009, p. 580-587.
-
Bajric R., Zuber N., Sostakov R. Relations between pulverizing process parameters and beater wheel mill vibration for predictive maintenance program setup. Maintenance and Reliability, Vol. 16, 2014, p. 158-163.
-
Siefert A., Pankoke S., Eckard C. Continuous virtual process chain for the optimisation of car passenger seats taking into account whole-body-vibrations. Human Vibration: Effects on Health – Performance – Comfort, 2007, p. 435-466.
-
Pennestri E., Stefanelli R., Valentini P. P., Vita L. Using a virtual dummy to simulate vibration dose value for different car occupants. International Design Engineering Technical Conferences and Computers and Information in Engineering Conference, 2005.
-
Martens W. L., Woszczyk W. Psychophysical calibration of whole-body vibration in the display of impact events in auditory and haptic virtual environments. The 3rd IEEE International Workshop on Audio and Visual Environments and Their Applications, 2004.
-
International Standard Organization ISO 2631-1-1997. Evaluation of human exposure to whole-body vibration – Part 1: General requirements.
-
British Standards Institution BS 6841-1987. Measurement and evaluation of human exposure to wholebody mechanical vibration and repeated shock.
-
Ma L., Chablat D., Bennis F., Zhang W. A new simple dynamic muscle fatigue model and its validation. International Journal of Industrial Ergonomics, Vol. 39, 2009, p. 211-220.