Abstract
Graphene possesses not only excellent optical, electrical and thermal properties but also outstanding thermoelectric and photothermal conversion capabilities. The application of graphene with functional responses plays a vital role in the development of intelligent materials intended for flexible actuators and intelligent robots. Cellulose paper is foldable and is a hydrophilic network comprised of porous cellulose fibres. In this paper, graphene composites as well as cellulose paper were taken as basic materials, which were further combined with other polymer materials (biaxially oriented polypropylene film (BOPP) and poly (3, 4-ethylenedioxythiophene/polystyrene sulfonate) (PEDOT: PSS). PEDOT: PSS solution can penetrate into the porous network of the paper to form a high-strength nanocomposite structure. A flexible thin film driver capable of multiple stimuli under light, heat and humidity was produced. Through characterization, it was found that the bending ability of the composite film was significantly improved in response to stimulation.

Highlights
- In this paper, graphene composites as well as cellulose paper were taken as basic materials, which were further combined with other polymer materials (biaxially oriented polypropylene film (BOPP) and poly (3, 4-ethylenedioxythiophene/polystyrene sulfonate) (PEDOT: PSS).
- In fact, graphene demonstrates excellent optical, thermal and electrical properties along with high efficiency in photothermal, electrothermal and photoelectric conversion. Composite materials hold massive potential for application in energy conversion.
- In addition, the composite materials can be flexibly driven without electricity and synergy due to the environmental responsiveness of these actuators. By adjusting the porosity and fiber orientation of the paper, it is possible to further improve the relative thickness of the layers, and even the coupling of different stimuli, the actuation of the paper-based actuator.
1. Introduction
In recent years, the development of carbon materials has been occurring at a rapid pace, and they have been met with widespread applications. The combination of lightweight and inexpensive carbon nanomaterials with intelligent materials capable of responding to stimuli has also drawn much research attention in recent years [1].
Graphene is a variety of monoatomic two-dimensional crystalline materials comprised of sp2 hybrid carbon atoms. It possesses superior mechanical properties. Currently, graphene has been commonly applied in light sensors and electrical sensors due to advantages such as unique photoelectric properties [2, 3], photothermal properties [4, 5], high specific surface area, high flexibility and biocompatibility. Cellulose paper shows a fairly high coefficient of wet expansion (CHE) and an extremely low coefficient of thermal expansion (CTE), which allows it to be foldable. In structure, the paper is a hydrophilic network made up of porous cellulose fibres. Porosity endows the actuator with the capability of large actuation and fast response [6]. The multifunctional response material is bendable under the stimulation of external conditions such as heat, light, humidity and electricity.
In the past, many flexible actuators related to stimulus response have been reported. Due to the limitations of the bulk film, however, it is common for actuators to achieve only bending actuation with a single stimulus source, and the response performance is unsatisfactory. Upon continuous exploration and innovation, this paper proposes to use graphene and cellulose to prepare composite film drivers capable of responding to a variety of different stimuli, including thermal stimuli, humidity stimuli, and light stimuli. It shows desirable advantages such as inexpensive affordability, fast response, no pollution, and a high degree of bending.
2. Material and research method
2.1. Materials
Biaxially oriented polypropylene film was obtained from Deli Group Co., Ltd., poly (3, 4-ethylenedioxythiophene) -poly (styrene sulfonate) was provided by Suzhou Gree Company, cellulose fibre, lithium bromide solution (9.3 mol/L). Graphite was purchased from Suzhou Greite Pharmaceutical Technology Co., Ltd. Concentrated sulfuric acid, potassium permanganate, and deionized water were provided by Sinopharm Chemical Reagent Co., Ltd., while hydrochloric acid, polyethylene glycol, stannous chloride, and SnCl2/EtOH solution were all provided by Suzhou Beinuo Biotechnology Co., Ltd.
2.2. Preparation of graphene oxide powder
Since the Hummers method is characterized by relative simplicity, high yield, and limited pollution, this method was adopted in this study to prepare GO experimentally. There are three steps in preparing GO.
In step 1, 1 g of graphite powder, 23 ml of concentrated sulfuric acid, and 0.5 g of sodium nitrate were added into a 250 ml three-necked flask. Then, the flask was placed in an ice-water bath before stirring at below 4 °C for half an hour. With 3 g of potassium acid added, the reaction continued for 2 hours to complete the low-temperature reaction. In step 2, the temperature of the system was raised to 35 °C, and the reaction continued for another 3 hours to complete the intermediate temperature reaction. In step 3, the temperature of the system was further increased to 98 ℃, and 46 ml of distilled water was added dropwise using a constant pressure funnel. Then, the reaction continued for another 1 hour to complete the high-temperature reaction. After the reaction, 70 ml of distilled water and 10 ml of hydrogen peroxide were also added for continuous stirring for 15 minutes. Then, suction filtration was performed at high temperatures, while the product was washed using a large amount of dilute hydrochloric acid (5% by volume) and distilled water until the pH value approached 7. Finally, the obtained product was centrifuged, placed in a drying oven, and dried at 60 °C for 24 hours.
2.3. Preparation of graphene oxide film
After being added to deionized water, the GO powder was stirred for 1 hour and then sonicated for half an hour. The process was repeated 5 times, and after sufficient stirring, the liquid was centrifuged for 15 minutes (5000 rpm) using a centrifuge machine to filter out the unoxidized graphite and various impurities. Then, it was configured as a 10 mg/ml graphene oxide aqueous solution. The film-forming substrate was made of ordinary glass. The glass substrate was immersed in ultrapure water with detergent for 24 hours prior to being washed using a cotton swab for 10 minutes. Finally, it was blow dried for later use. The film was prepared using the drop coating method. A certain amount of the prepared graphene oxide solution was added dropwise to a glass substrate, and the graphene oxide film was left at a constant temperature of 60 °C for 1 hour to obtain a dried graphene oxide film.
2.4. Preparation of graphene conductive film
There are various reducing agents that can be used for graphene conductive films. In this experiment stannous chloride was used because it is more eco-friendly.
In step 1, a certain amount of SnCl2 was first weighed and dissolved into absolute ethanol (EtOH), with a certain concentration of SnCl2 solution arranged. The ultrasonic wave was sonicated for half an hour in an ultrasonic machine to achieve uniform dispersion as a reducing agent. In step 2, 0.5 ml of the reducing agent was added dropwise to the dried GO film using the drop coating method and was dried in a drying oven at 60 °C for 30 minutes. The entire reduction process was kept in contact with the air, which was accompanied by the reducing agent solvent. It took approximately 20 minutes to complete the rapid volatilization of ethanol and reduction of GO. In step 3, after the solvent was evaporated and dried, the byproducts were removed using ethanol prior to drying in an oven at 60 °C for 30 minutes. Finally, a graphene transparent conductive film was obtained.
2.5. Preparation of BOPP/paper/RGO/PEDOT: PSS composite film
The self-adhesive BOPP film was cut into a size of 75×12 mm. Then, the paper cut into the same size was affixed to the BOPP film. A 10 mg/ml graphene oxide aqueous solution was dropped onto the composite BOPP/A4 by drip coating after the graphene oxide was reduced with SnCl2/EtOH solution on the paper composite film, dried in a 30 °C blast drying oven for 3 hours, and removed. Then, PEDOT was applied to the BOPP/paper/RGO composite film. The PSS solution was then dried in a blast drying oven for 3 hours and removed to obtain a BOPP/paper/RGO/PEDOT: PSS composite film. Fig. 1(a) shows the process of preparing the BOPP/paper/RGO/PEDOT: PSS composite film.
Sample characterization: (1) Characterization of the surface micromorphology of the sample: A Japanese Hitachi S-4800 cold field emission scanning electron microscope (SEM) was used. For the test conditions, the voltage was 3 kV, and the current was 8 mA. It was observed after being sprayed with gold. (2) Characterization of mechanical performance test: The American INSTRON universal experimental material machine was used to perform the test at a constant temperature of 20 °C and a relative humidity of 60 %. The sample was 0.25-0.28 mm in thickness, 70 mm in length and 12 mm in width. The tensile speed was 100 mm/min, and there were 5 sets of data tested for each sample, with the average taken.
Fig. 1a) Schematic illustration of the fabrication process of the BOPP/paper/RGO/PEDOT: PSS films; b) SEM of the cross section of BOPP/paper/RGO/PEDOT: PSS film
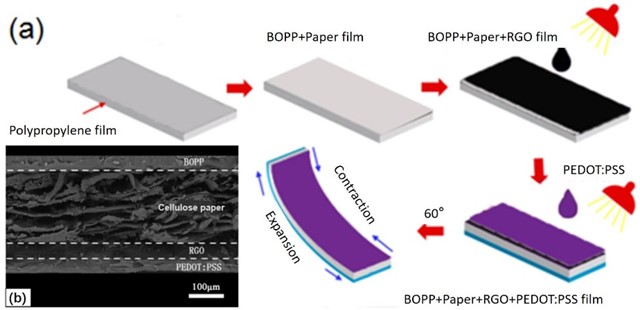
3. Conclusion and analysis
3.1. Morphology characterization
It is worth noting that the four-layer film structure can be clearly observed from the cross-sectional view of the BOPP/paper/RGO/PEDOT: PSS composite film in Fig. 1(b), with an overall thickness of approximately 0.258 mm.
3.2. BOPP/paper/RGO/PEDOT: PSS composite film thermal response performance test
In the experiment, the prepared BOPP/paper/RGO/PEDOT:PSS composite film was placed in a blast drying oven with a preset temperature of 50 °C and horizontally placed on copy paper before being photographed and recorded every three seconds. The following pictures of bending deformation over time were obtained, as shown in Fig. 2(a-c). It can be seen from the figure that the BOPP/paper/RGO/PEDOT: PSS composite film is deformed upwards to overcome gravity over time. Through research, it was found that the bending deformation of this high-performance multiresponsive film was reversible.
Fig. 2a)-c) Schematic illustration of the thermal response bending deformation of the BOPP/paper/RGO/PEDOT: PSS composite film; d)-f) schematic illustration of the photoresponse bending deformation of the BOPP/paper/RGO/PEDOT:PSS composite film; g) Corresponding bending angle–time curve during the heating process; h) corresponding curvature-time curve during the heating process. Jiayi Cheng and Yuting Wang took the photos at the Experimental Building of the college of Textile and Clothing Engineering, located in the Dushu Lake Campus of Soochow University on March 12th 2022
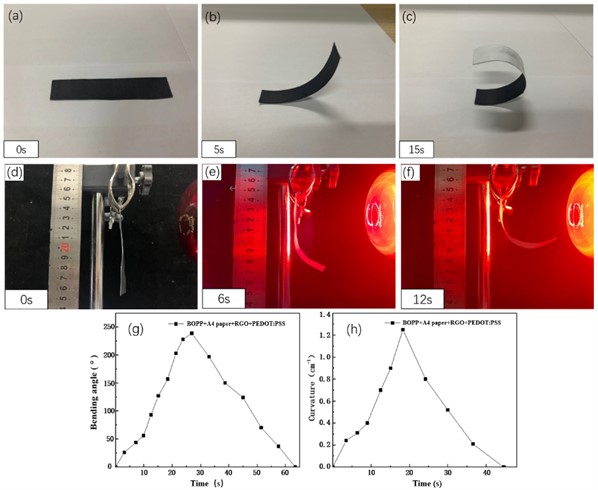
3.3. BOPP/paper/RGO/PEDOT: PSS composite film light response performance test
In the experiment, the prepared BOPP/paper/RGO/PEDOT: PSS composite film was cut into a size of 75 mm×12 mm before being placed under a digital display infrared baking lamp. The lamp has a rated power of 100 W, a rated voltage of 110 V/220 V, and a rated frequency of 50 Hz. The emitted near-infrared light wavelength ranges from 780 to 3000 nm, the distance between the control film and the lamp is approximately 6 cm, and the photo is recorded every 6 s. The schematic diagram shown in Fig. 2(d-f) is obtained to explore the performance of the BOPP/paper/RGO/PEDOT: PSS composite film in near-infrared light photoresponse deformation. It can be seen from the figure that with the continuous irradiation of near-infrared light, the film bends toward the PEDOT: PSS layer, and the bending becomes more significant.
The BOPP/paper/RGO/PEDOT: PSS composite film is tested for bending deformation. As shown in Fig. 2(g), the curve of the bending angle of the composite film over time is shown at a temperature controlled at 50 °C. It can be seen from the figure that when the response time is approximately 32 s, the maximum bending angle can be approximately 250°. The bending angle increases almost linearly with time. After removing the composite film from the baking box after 32 s, the composite film gradually returns to the initial state with increasing time, indicating that the bending deformation of the composite film is reversible. Fig. 2(h) shows the curve of the curvature of the composite film over time when the temperature is controlled at 50 °C.
3.4. BOPP/paper/RGO/PEDOT: PSS composite film humidity response performance test
In the experiment, the prepared BOPP/paper/RGO/PEDOT: PSS composite film was cut into a size of 75 mm×12 mm and then placed near a humidity meter. The humidity was controlled at approximately 60 %, with a photo taken and recorded every 8 s, as shown in Fig. 3(a-c). From the figure, it can be seen that the BOPP/paper/RGO/PEDOT: PSS composite film bends toward the BOPP film side due to humidity.
Fig. 3a)-c) Schematic illustration of the humidity response bending deformation of the BOPP/paper/RGO/PEDOT: PSS composite film; d)-f) schematic illustration of the electrical response bending deformation of the BOPP/paper/RGO/PEDOT: PSS composite film; g) corresponding curvature–temperature curve during the heating process; insets: optical images at different temperatures; h) Stability test of a 6.5 cm long film under 250 cycles; insets: optical images of the actuator at different loading cycles. Danye Han and Run Liu took the photos at the Experimental Building of the college of Textile and Clothing Engineering, located in the Dushu Lake Campus of Soochow University on March 19th 2022
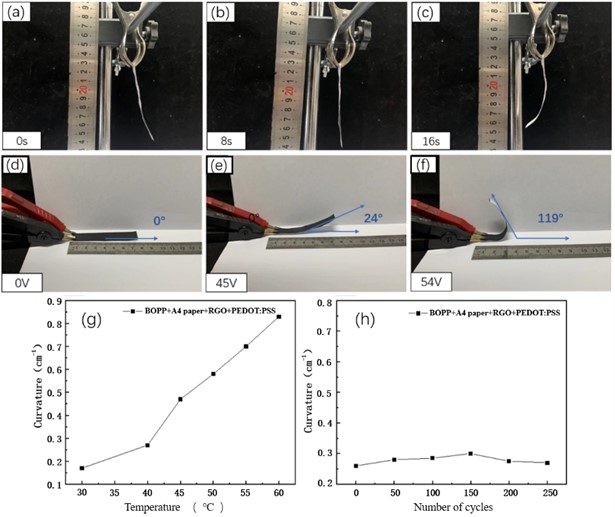
3.5. BOPP/paper/RGO/PEDOT: PSS composite film electrical response performance test
In the experiment, the prepared BOPP/paper/RGO/PEDOT:PSS composite film was cut into a film with a size of 70 mm×12 mm and a groove size of 10 mm×6 mm for the formation of a closed circuit, based on which an investigation was conducted into the electrical response performance of the composite film. Among them, the starting voltage was 45 V. It can be clearly seen from Fig. 3(d-f) that the film bends toward the PEDOT: PSS layer with increasing voltage, and the bending becomes more significant. When the voltage increases to 54 V, the maximum bending angle can reach 119°, which is attributed to the excellent electrical conductivity of the graphene-based composite film. After the system is energized, electrical energy is converted into thermal energy. Due to the significant difference in the thermal expansion coefficients of the thin film layers, bending deformation results. The BOPP/paper/RGO/PEDOT: PSS composite film is tested for bending deformation. Fig. 3(g) shows the change curve of the temperature and curvature of the BOP/paper/RGO/PEDOT: PSS composite film. Fig. 3(h) shows the stability test of a 6.5 cm long actuator at 250 °C under temperature control at 40 °C. The inset is an optical image of the actuator under different loading cycles. It can be seen from the figure that under frequent cycle loading, the maximum curvature of the actuator is almost constant. The slight increase in curvature may be due to thermal stress at the interlayer interface.
We develop high-performance multilayer drivers in a simple, scalable, maskless, and low-cost way. Graphene coating can effectively improve the electrical and mechanical properties of the film. The high moisture absorption of PEDOT: PSS greatly promotes the wet expansion coefficient (CHE) of PEDOT: PSS-coated paper. The foldability and anisotropy of cellulose paper allow specific shape changes to be achieved at a variety of programmable locations. A series of tests showed that the bending angle of the film driver induced by different stimulus sources is different, and the maximum can reach approximately 250°. The environmental responsiveness of these actuators enables composite materials to be flexibly driven without electricity and synergy. By changing the porosity and fibre orientation of the paper, the relative thickness of the layers, and even the coupling of different stimuli, the actuation of the paper-based actuator can be further improved and adjusted.
4. Conclusions
Over the past few decades, there have been many reports on graphene, its composite materials and stimulus-responsive flexible actuators. However, few people have paid attention to combining the two to develop new graphene-based flexible actuators. In fact, graphene demonstrates excellent optical, thermal and electrical properties along with high efficiency in photothermal, electrothermal and photoelectric conversion. Composite materials hold massive potential for application in energy conversion. The high molecular polymer poly (3, 4-ethylenedioxythiophene/polystyrene sulfonate) (PEDOT: PPS) was coated on a paper substrate to exhibit stable mechanical properties. In addition, the PEDOT: PSS solution can penetrate into the porous network of paper, thus forming a strong nanocomposite structure. As revealed by a series of tests, the bending angle of the film driver induced by different stimulus sources varies, and it reaches a maximum of approximately 250°. In addition, the composite materials can be flexibly driven without electricity and synergy due to the environmental responsiveness of these actuators. By adjusting the porosity and fiber orientation of the paper, it is possible to further improve the relative thickness of the layers, and even the coupling of different stimuli, the actuation of the paper-based actuator. The material methods designed in this subject can be applied to develop high-performance foldable electronic circuits and wearable systems.
References
-
P. Zhou, L. Chen, L. Yao, M. Weng, and W. Zhang, “Humidity – and light-driven actuators based on carbon nanotube-coated paper and polymer composite,” Nanoscale, Vol. 10, No. 18, pp. 8422–8427, 2018, https://doi.org/10.1039/c7nr09580e
-
D. Balle, C. Schedel, T. Chassé, and H. Peisert, “Interface properties of CoPc and CoPcF16 on graphene/nickel: influence of germanium intercalation,” Journal of Physics: Condensed Matter, Vol. 31, No. 17, p. 174004, May 2019, https://doi.org/10.1088/1361-648x/ab028f
-
R. Belchi et al., “One-step synthesis of TiO2/Graphene nanocomposites by laser pyrolysis with well-controlled properties and application in perovskite solar cells,” ACS Omega, Vol. 4, No. 7, pp. 11906–11913, Jul. 2019, https://doi.org/10.1021/acsomega.9b01352
-
P. C. Bandara, F. Ibañez de Santi Ferrara, H. Nguyen, G. Santos, W.-C. Shih, and D. F. Rodrigues, “Investigation of thermal properties of graphene-coated membranes by laser irradiation to remove biofoulants,” Environmental Science and Technology, Vol. 53, No. 2, pp. 903–911, Jan. 2019, https://doi.org/10.1021/acs.est.8b05149
-
M. Caminero, J. Chacón, E. García-Plaza, P. Núñez, J. Reverte, and J. Becar, “Additive manufacturing of PLA-based composites using fused filament fabrication: effect of graphene nanoplatelet reinforcement on mechanical properties, dimensional accuracy and texture,” Polymers, Vol. 11, No. 5, p. 799, May 2019, https://doi.org/10.3390/polym11050799
-
Q. Jin et al., “Cellulose fiber-based hierarchical porous bismuth telluride for high-performance flexible and tailorable thermoelectrics,” ACS Applied Materials and Interfaces, Vol. 10, No. 2, pp. 1743–1751, Jan. 2018, https://doi.org/10.1021/acsami.7b16356
About this article
The authors have not disclosed any funding.
The datasets generated during and/or analyzed during the current study are available from the corresponding author on reasonable request.
The authors declare that they have no conflict of interest.