Abstract
As the industrial sector develops, the performance requirements for aluminum alloys are also constantly improving. The study explores how aging and rolling treatment affect aluminum alloys' precipitates and mechanical properties by controlling the parameters of aging process and rolling deformation variables. 7N01 aluminum alloy was selected as the experimental object, and the samples were treated with non-aging, natural aging, artificial aging, and rolling deformation. How aging processes and rolling deforming affected alloys’ mechanical properties was evaluated through performance testing (mechanical and tensile testing) and material fiber characterization methods (advanced electronic instruments). These results confirmed that the combination of three aging pre-treatments + R20 % + 120 °C re-aging could significantly improve the hardness of aluminum alloys and maintain high ductility. As the deformation decreased, the time for the sample to reach the hardness peak was shorter and the hardness was higher. The 20 % deformation sample’s strength was better than the 80 % deformation sample’s. This confirmed that appropriate aging process and deformation combinations could improve the strength and hardness of aluminum alloys. These results have certain guiding significance for optimizing the aging process of mechanical extruded aluminum alloys and provide reference for the study of related alloy properties.
1. Introduction
Aluminum alloy has advantages such as light weight, high strength, and good corrosion resistance. Therefore, it is widely used in aerospace, automobiles, ships, and other fields [1, 2]. Rolling deformation is a commonly used metal processing method that can improve the mechanical properties and microstructure of aluminum alloys through high strain rate plastic deformation. However, defects such as dislocations and grain boundaries introduced during rolling deformation can have a certain negative impact on the properties of the alloy [3]. To further optimize the performance of aluminum alloys, it is necessary to control the microstructure and mechanical properties of the alloy through appropriate heat treatment. Among them, the aging process is a commonly used method that regulates the properties of alloys through solid solution and precipitation phase formation [4]. Aging treatment involves various factors, such as aging time, temperature, solid solution treatment, etc. Different treatment conditions may have different effects on the microstructure and mechanical properties of aluminum alloys. Therefore, studying how the aging process affects the formation of precipitates and mechanical properties of mechanically extruded aluminum alloys has important scientific significance and engineering application value. However, there are still some shortcomings in the research on the effect of aging process on the precipitates and mechanical properties of mechanically extruded aluminum alloys. Firstly, the aging response mechanism of mechanically extruded aluminum alloys is not fully understood, and further research is needed to investigate the effects of different aging processing parameters on type, quantity, and distribution of precipitates in the alloy [5]. Secondly, there is a complex interrelationship between the heat treatment and microstructure of aluminum alloys. Therefore, the mechanical properties of alloys exhibit different characteristics under different aging process conditions, and further exploration of their laws is needed. In response to the above issues, the research aims to explore the relationship between the precipitates and mechanical properties of mechanically extruded samples after different aging processes. The article compares and analyzes the differences in microstructure, precipitate morphology, and mechanical properties of alloys in some processes. This can reveal how aging processes affect the microstructure evolution and performance changes caused by mechanical extrusion of aluminum alloys. The study consists of four sections. Firstly, it mainly discusses the research on aging technology and aluminum alloy properties by domestic and foreign scholars. Secondly, it mainly explains the processing of experimental materials and the analysis of detection methods. The third section mainly discusses the effects of different aging processes and rolling deformation variables on samples’ precipitates and mechanical properties. Finally, the main focus is on summarizing and analyzing the results of the third section of the experiment and pointing out the shortcomings.
2. Related works
Aluminum alloy has the advantages of light weight, high strength, and good thermal conductivity, which is widely used in aerospace, automobiles, sports equipment, and so on. Therefore, the study of its performance is particularly important. To explore the general properties of aluminum alloys, domestic and foreign experts have conducted research on 7xxx aluminum alloy. Ying et al. conducted an experimental study on the interfacial heat transfer coefficient of 7XXX series aluminum alloys at HFQ temperature. They designed a specialized experimental setup. The interface heat transferring coefficient of 7XXX series sample was studied by measuring the temperature field and testing the mechanical properties on the HFQ hot forming testing machine. These results confirm that the interfacial heat transfer coefficient of the 7XXX series aluminum alloy increases with increasing temperature at HFQ temperature [6]. Lee et al. conducted a study on the stress corrosion cracking resistance of high-strength 7xxx series aluminum alloys in a 3.5 % sodium chloride solution. The corrosion behavior and corrosion resistance of 7xxx series aluminum alloys under different conditions were evaluated in a 3.5 % sodium chloride solution using Stress Corrosion Cracking (SCC) method. These results confirm that high-strength 7xxx series aluminum alloys exhibit certain SCC resistance in a 3.5 % sodium chloride solution [7]. Wei et al. conducted research on three-dimensional modeling of grain structure evolution in aluminum alloy welding. A detailed modeling and analysis of the evolution of grain structure in aluminum alloy welding was conducted using numerical simulation methods. By considering multiple physical processes such as heat conduction, molten pool flow, phase transformation, and solid phase nucleation, the growth and evolution of grains in welding were simulated. These results confirm that the growth and evolution of grains in the molten pool during welding exhibit various forms, including refinement, appearance of vertical grains, and merging [8]. Li et al. considered multiple uncertain factors for the bending problem of thin-walled aluminum alloy pipes, including material performance uncertainty, process parameter uncertainty, and load condition uncertainty. By establishing a numerical model and combining multi-objective optimization algorithms, multiple key indicators in the bending process are optimized to seek the best bending results. These results confirm that the optimal bending parameters of thin-walled aluminum alloy pipes can be found under uncertain conditions through sequential multi-objective optimization methods [9]. Mehmood et al. confirmed the residual stress distribution in high-strength aluminum alloys after electric discharge machining. The residual stress in high-strength aluminum alloy after electric discharge machining was measured and analyzed using non-destructive testing methods. The distribution of residual stress was obtained by measuring residual stress at different positions and depths. These results confirm that residual stress in high-strength aluminum alloys is caused during the electric discharge machining process [10].
The aging process can significantly improve the strength, hardness, and corrosion resistance of aluminum alloys. Li et al. performed T651 aging treatment on Alumec89 alloy mold plates. These results confirm that T651 aging treatment can significantly improve the mechanical properties of Alumec89 alloy mold plates and have good tensile strength and corrosion resistance [11]. Fan et al. conducted different aging treatments on 2297 aluminum lithium alloy and evaluated the changes in its microstructure and mechanical properties. These results confirm that moderate aging treatment can refine alloy's grain size and promote the formation of precipitates, thereby improving the strength and hardness of the material [12]. Akhil et al. conducted heat treatment and aging treatment on LM13 aluminum alloy castings and evaluated the impact of the treatment process on the cross-sectional properties of the castings. These results confirm that after appropriate heating and aging, castings’ hardness and strength have been improved. And the treatment improved the corrosion resistance and fatigue resistance of the castings [13]. Deng et al. conducted hardness testing and fatigue performance testing on the aging system of 7050 aluminum alloy. These results confirm that after three stages of aging treatment, the tensile strength of the alloy is 640.2 MPa, which is higher than 477.7 MPa after two stages of aging and 483.5 MPa after four stages of aging [14]. Sylwia et al. analyzed how temperature and time during artificial aging process affected the mechanical properties selected for EN AW-6106 aluminum alloy hot extrusion profiles. These results confirm that the samples aged at 165 °C for 6 hours achieved the highest mechanical property [15].
From the above research, the precipitates and mechanical properties of aluminum alloys are greatly influenced by the conditions and parameters in the production process, while aging process and extrusion deformation can improve the properties of aluminum alloys. In view of this, the paper explored how different conditions and parameters affected 7N01 aluminum alloy's structure and properties. The article expects to obtain the optimal process parameters to improve the comprehensive performance of aluminum alloys.
3. Analysis of aging process and testing methods for 7N01 aluminum alloy
7N01 aluminum alloy is a typical AL-Zn-Mg aluminum alloy with excellent properties such as low density, high plasticity, and easy welding. It is widely applied in aircraft, automotive manufacturing, and so on. However, as the social transportation industry develops, the requirements for the structural strength and plasticity of aluminum alloy materials are also increasing [16]. The study takes 7N01 aluminum alloy as the research object and explores the structural and structural changes, precipitation phase deformation mechanism, and mechanical deformation effect of 7N01 aluminum alloy under different aging process conditions. The organizational structure of the article is shown in Fig. 1.
The material used is commercial aluminum alloy produced by semi continuous casting, with a thickness of 10mm. Due to the problems of numerous defects, poor strength, and plasticity in cast alloys, mechanical extrusion densification and homogenization operations are required [17]. 7N01 sample's chemical composition was tested using spark spectroscopy in Table 1.
Table 1Test chemical composition of 7N01 aluminum alloy experimental samples (Mass Fraction%)
Elemental composition | Zn | Mg | Cr | Mn | Zr | Fe | Si | Al |
Standard value | 4.0-5.0 | 1.0-2.0 | ≤ 0.20 | 0.2-0.7 | ≤ 0.20 | ≤ 0.35 | ≤ 0.30 | Residual |
Measured value | 4.47 | 1.2 | 0.12 | 0.35 | 0.15 | 0.18 | 0.10 | Residual |
7N01 aluminum alloy is an aging strengthened alloy, and its structure and properties are greatly affected by aging process conditions. Fig. 2 shows the aging process flow. 7N01 aluminum alloy is linearly cut into 10 mm thick experimental samples from a hot extrusion device. Then, a solid solution treatment is carried out, which involves dissolving solute atoms in the solid solution into the matrix at high temperatures to increase its solid solubility and uniformity. Its solid solution temperature is 475.3 °C and the time is 1 hour [18]. Then the alloy is rapidly cooling to environmental temperature, keeping the solid solution in a highly saturated state. The cooling method is water quenching. Next, a pre-aging treatment is carried out, which makes this alloy to keep a lower temperature for some time, allowing solute atoms in the solid solution to aggregate into particles and form a dispersed phase. This step helps to improve the strength and hardness of the alloy. Then cold rolling can change the grain structure of aluminum alloy, improve its strength, and improve surface quality. Finally, re-aging treatment is carried out to reheat the alloy to a certain temperature and maintain it for a period of time, to further promote the formation of dispersed phases and the stabilization of grain boundaries. So it can improve the endurance strength and creep resistance of the alloy. The entire aging process has an important impact on 7N01 sample's microstructure and mechanical properties and reasonable control of aging process conditions can achieve excellent comprehensive properties.
Fig. 1Organizational structure of the article
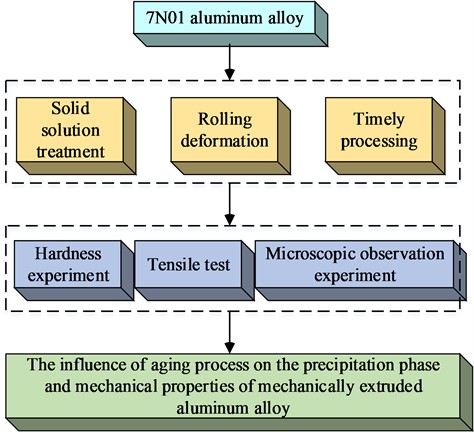
Fig. 2Flow chart of aging process experiment for 7N01 aluminum alloy
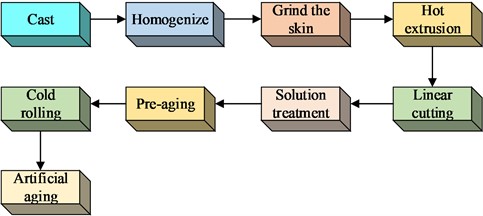
The entire aging process has an important impact on 7N01 sample’s microstructure and mechanical properties, and the reasonable control of aging process conditions can achieve excellent comprehensive properties. The research mainly focuses on controlling the aging time, aging temperature, extrusion deformation, pre-aging treatment state, and other conditions in the aging process. Through these methods, the influence of various variable parameters of aging process on the microstructure and mechanical properties of 7N01 aluminum alloy is explored [19]. Table 2 shows the specific treatment.
In theory, aging treatment improves the strength of alloys by forming small precipitates of solid solution elements at grain boundaries and within the grain. The formation of precipitates can limit grain boundary slip and intragranular slip, thereby effectively enhancing the strength of the alloy. As the precipitate phase forms, the hardness of the alloy also increases. The hardness of precipitates is usually higher than that of solid solutions, so the formation of precipitates can improve the hardness of alloys. In addition, aging treatment can also improve the deformation hardening ability of aluminum alloys. Deformation hardening refers to the hardening phenomenon caused by the increase and movement of internal dislocations when a material undergoes deformation under stress. Aging treatment can form more dislocations in the alloy, making it more resistant to deformation. To further investigate the changes in mechanical properties and microstructure of 7N01 aluminum alloy after aging treatment. 7N01 sample’s mechanical properties after aging are tested using a micro-hardness tester and a universal tensile machine for hardness and tensile testing. Scanning Electron Microscopy (SEM) and accompanying Electron Backcatcher Diffusion (EBSD) are used to characterize the microstructure and identify the precipitates of 7N01 aluminum alloy. And Transmission Electron Microscopy (TEM) is used to study the deformation process and mechanism of 7N01 aluminum alloy. In addition, for the hardness test of 7N01 aluminum alloy, the MH-5L digital micro-hardness tester is used. The loading load is set to 3 kg and the test duration is 20 seconds. After polishing the sample with 120 #-3000 # abrasive paper, polishing treatment is carried out with diamond spray until there is no obvious scratch on the sample surface. 10 different areas of each hardness value are selected for testing, and the average value is taken as the Brinell micro-hardness value at that location [20-21]. Eq. (1) is the calculation:
where, is Brinell hardness. is the test force. is the surface area of the indentation. is the diameter of the ball pressure head. is the diameter of the indentation on the hardness tester. For the hardness testing of 7N01 aluminum alloy, the AG-X50KN universal tensile testing machine is selected, with a temperature of room temperature and a tensile rate of 2 mm/min. Uniaxial tension is performed using a loading extensometer, and the “stress-strain” curves of the test results are plotted using MATLAB plotting software. Fig. 3 shows the plane dimensions of the stretched sample. After the heat treatment, the stretched samples are polished with 120 #, 400 #, and 800 # sandpapers in sequence, and the surface of the sample is then polished to mark the distance with a pencil before conducting a tensile test.
Table 2Setting of aging process parameters for 7N01 aluminum alloy
Process | Handling method | Parameter setting |
Pre-aging | Non-ageing | |
Natural aging | Duration 1 week | |
Temperature 100 °C, duration 8 hours | ||
Artificial aging | Temperature 120 °C, duration 50 hours | |
Temperature 100 °C, duration 8 hours | ||
Rolling deformation | Cold rolling | Shape variable 20 % |
Shape variable 40 % | ||
Shape variable 60 % | ||
Shape variable 80 % | ||
Re-aging | 10 mm and 10 mm samples after cold rolling shall be tested according to ASTM E517-00 standard | 120 °C |
To characterize the microstructure and identify the precipitates of 7N01 aluminum alloy under different aging conditions, the MIRA3 field emission scanning electron microscope is used to observe the morphology of the sample. And the precipitates are identified using the NordlysMax2 EBSD detector. The research mainly utilizes EBSD technology to analyze and explore the recrystallization structure of 7N01 aluminum alloy in the cold rolled state and after annealing treatment. Small samples with dimensions of 4 mm, 4 mm, and 2 mm are used. To obtain clearer photos, the samples are polished with 120 #~3000 # sandpaper and subjected to electrolytic polishing to eliminate surface scratches and the influence of surface stress layers on the test material, thus obtaining better images and data. The obtained data are analyzed using Python software. Fig. 4 shows the core components of the scanning electron microscope.
Fig. 3Shape and size of 7N01 aluminum alloy tensile test sample
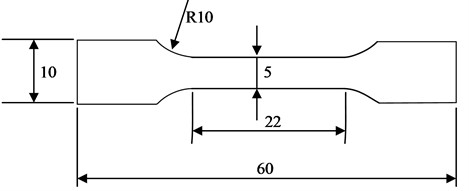
Fig. 4Structure of two microscopes
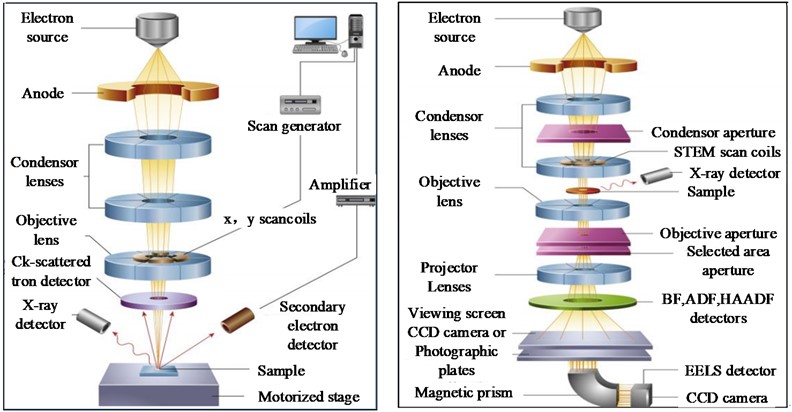
The study uses FEI TECNAI G2 F20 field emission TEM to observe the morphology, size, and distribution of precipitates in 7N01 aluminum alloy samples. And the interaction between precipitates and dislocations during the deformation is studied to reveal 7N01 aluminum alloy;s deformation mechanism. To meet the observing requirements of TEM, the 7N01 aluminum alloy sample needs to be polished first. The experimental sample needs to be polished to around 200 um using a pre-grinder, and then manually polished to 100 um. Then the sample is made into a 3 mm circular shape using a punching machine. Then an electrolytic double spray instrument is used to perform double spray thinning on the original sheet. Finally, a small hole is obtained in the middle and the two sides are bright.
4. Analysis of the effect of aging process and rolling deforming on precipitated phase and mechanical properties of 7N01
7XXX series aluminum alloy is of great significance for the development of aviation, high-speed rail, automotive, shipbuilding, and other fields in China. The effects of aging process variables and parameters on the hardness, conductivity, tensile properties, and microstructure precipitates of 7XXX aluminum alloy are investigated. Thus, the relationship between “aging processing microstructure mechanical properties” of 7XXX series sample is established. Therefore, the study focuses on 7N01 aluminum alloy and conducted relevant experiments with T6 treatment as a reference. The study first conducts a single stage T6 treating on 7N01 sample and tests its Vickers hardness under different aging conditions. And under-aging for 40 hours and peak aging for 100 hours are selected in this experiment to test the tensile properties in Fig. 5.
Fig. 5Results under single stage aging treatment
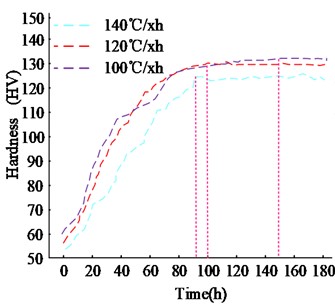
a) Hardness test
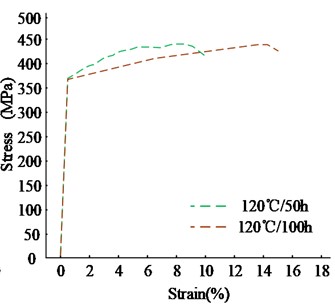
b) Tensile test
In Fig. 5(a), as the aging time increases, the hardness of the samples at the three temperature states begins to rapidly increase. The sample at 140 °C reaches the hardness peak at approximately 93 hours, which is about 124 HV. The sample at 120 °C reaches the hardness peak at approximately 100 hours, which is about 129 HV. The sample at 100 °C reaches its hardness peak in approximately 150 hours, with a peak value of approximately 132 HV. This is because aging treatment can cause the solid solution phase in the material to decompose or precipitate, resulting in aging hardening phenomenon. Although the 140 °C sample reaches its hardness peak 7 hours earlier than the 120 °C sample, the hardness peak is about 5HV less. Although the hardness peak of the 100 °C sample is 3HV higher than that of the 120 °C sample, the time to reach the hardness peak is 50 hours later. Therefore, a sample at 120 °C is selected for testing its peak aging and un-deraged tensile properties. By observing Fig. 5(b), compared with the sample under un-deraged treatment at 120 °C/50 h, the strength difference of the sample under peak aging treatment at 120 °C/100h is not significant, but its ductility is significantly improved. The samples subjected to aging treatment at 120 °C/100 h exhibit good ductility while reaching the peak hardness, so the subsequent experiments use a state of 120 °C/100 h as the reference condition. TEM is used to observe the sample at 120 °C/100 h along the <110>Al direction in Fig. 6.
Fig. 6<110>Al TEM morphology image of the sample along the projection at 120 °C/100 h
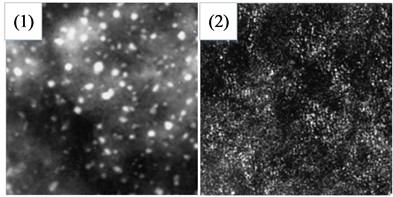
a)TEM image of GP area
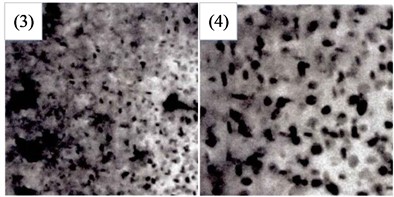
b) TEM image of
Generally speaking, the precipitation sequence of 7N01 aluminum alloy is: supersaturated dissolved solid → GP zone → phase → phase. The GP region and phase are two main strengthening phases. In Fig. 6(a), the shape of GP region of sample is mainly circular small particles. The GP zone is composed of solid solution particles precipitated from supersaturated solution solids, which plays an important role in improving the strength of aluminum alloys. In Fig. 6(b), the phase of sample is mostly disc shaped and short rod shaped. This precipitate is the main strengthening phase of 7N01 aluminum alloy. Next, Fig. 7 explores the impact of deformation treatment and changing the pre-treatment state on the comprehensive performance of sample.
Fig. 7Effect of different pre-treatment conditions and rolling deformation on samples
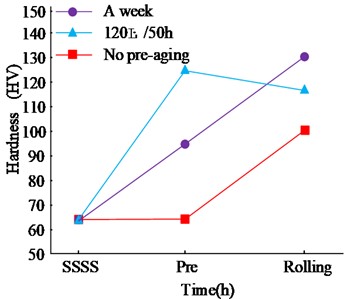
a) Hardness test
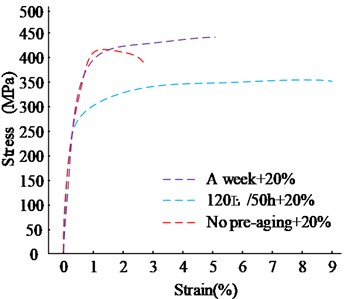
b) Tensile test
Fig. 7(a) is the hardness changing of sample from “solid solution state → pre-aging state → cold rolling state” under three pre-treatment conditions. Different pre-treatment conditions can lead to different hardness of the sample, with the sample in the state of 120 °C/50 h having the hardest hardness. This may be because the formation of certain precipitates during the pre-aging process makes the sample harder. After rolling deformation, there is a significant improvement in the hardness of the samples treated with natural aging for one week and without aging. However, the samples treated at 120 °C/50 h show a decrease, and the maximum hardness after rolling deformation is 126 HV, which does not even exceed the samples treated with traditional aging. Fig. 7(b) shows the tensile force variation curve of the samples under three pre-treatment conditions under 20 % cold rolling deformation, indicating that the elongation of the samples after rolling deformation is very poor. This may be due to lattice distortion and dislocation formation caused by cold rolling deformation, which makes the material brittle and reduces its tensile performance. Based on the above data, it can be concluded that deformation treatment alone cannot improve the hardness and tensile properties of 7N01 aluminum alloy. Next, samples under different pre-treatment conditions are subjected to a one-step aging treatment after rolling deformation operation in Fig. 8.
Fig. 8Hardness and tensile performance results of samples under different pre-treatments
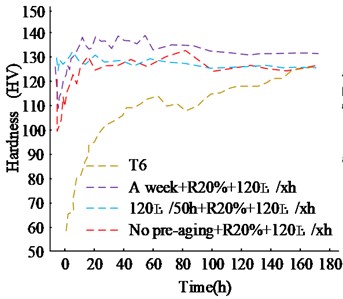
a) Hardness test
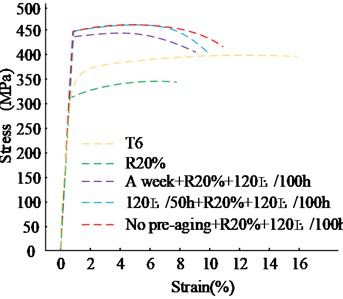
b) Tensile test
In Fig. 8(a), in the initial state, the hardness of the sample is “120 °C/50 h” > “natural aging for one week” > “un-aged treatment” > “T6” as the re-aging progresses. The hardness of the sample under various conditions gradually increases and finally reaches its peak. Moreover, the strengthening effect of natural aging for one week and non-aging treatment on the hardness value of the samples is more obvious, while the strengthening effect of the sample hardness under 20 °C/50 h treatment is relatively small. This may be due to the larger size of precipitates in the samples treated at 20 °C/50 h, while the smaller size of precipitates in the samples treated under the other two conditions. After reaching the peak value and maintaining it for a period of time, the hardness value slightly decreases. The difference in the peak hardness of the samples under the three conditions is not significant, and the decrease is not significant. In Fig. 8(b), under subsequent re-aging treatment, there are significant differences in the elongation of the samples under the three conditions. The elongation of the sample is “un-aged” > “naturally aged for one week” > “120 °C/50 h” > “T6”> “R20 %”. This may be due to the different aggregation states of solute atoms in the samples under different pre-treatment conditions. The main precipitate phase in the samples at 120 °C/50 h is the larger phase, while the main precipitate phase in the samples under natural aging conditions is the smaller GP zone. The samples without aging treatment have no precipitate phase. So during rolling deformation, the obstruction effect of precipitates leads to significant differences in sample plasticity under different pre-treatment conditions. Based on the above data, compared to the traditional single-stage T6 aging treatment, the samples under the other three conditions not only have a higher strength improvement, but also have a significant improvement in elongation. Next, the images of the tensile notches in the deformed, T6, deformed, and aged states of the samples are tested in Fig. 9.
Fig. 9Electronic scanning images of tensile notches in different states of alloy samples
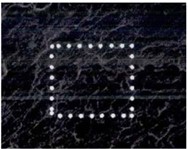
a) R20 % 100 um
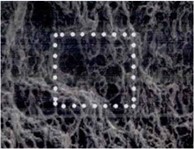
c) 120 °C 100 um
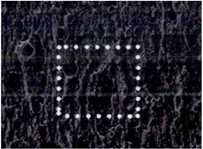
e) R20 %+120 °C 100 um
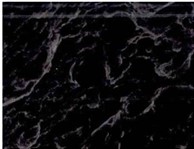
b) R20 % 20 um
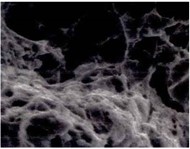
d) 120 °C 20 um
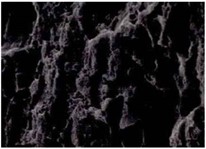
f) R20 %+120 °C 20 um
According to the observation results in Fig. 9, a large number of step structures, dimples, and honeycomb structures appear in the notch morphology of the deformed sample. The sample notch morphology under aging treatment at 120 °C exhibits large initial dimples, and there are large-sized second phase particles at the bottom. This may be because during aging treatment, the alloy undergoes phase transformation, and the formation of initial pits is influenced by the second phase particles. Due to the thermodynamic effects during aging treatment, the morphology of larger initial pits may be related to the rearrangement of grains and the movement of dislocations. In addition, the presence of larger second phase particles at the bottom may be due to the addition of specific alloying elements to the alloy, resulting in precipitation. In alloy notch’s morphology after deformation and aging treatment, it is observed that the initial dimples are small and deep, while the number of these bottom initial dimples' second phase particles is small and fragmented. This indicates that the aging treatment after deformation reduces and deepens the initial dimples in the alloy, and these particles undergo fragmentation and dissolution. In Fig. 10, hardness tests are continued on samples under three different pre-treatments for different rolling deformation variables.
Fig. 10Hardness test results of samples under three different pre-treatments for different rolling deformation variables
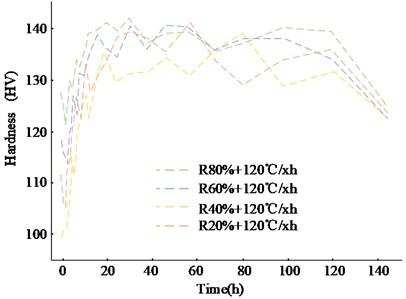
a) No time effective processing
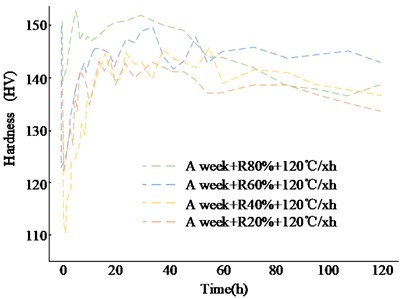
b) Natural aging treatment for one week
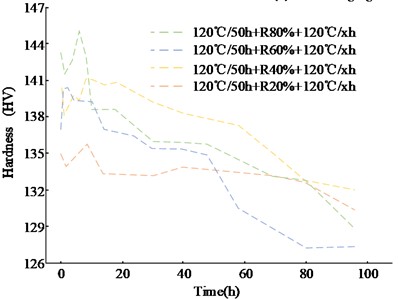
c) 120 °C/50 h aging treatment
Fig. 10(a) shows the hardness curves of samples treated with different deformation variables without pre-aging treatment. The four curves show a trend of first decreasing, then increasing, and then decreasing. The hardness of the sample reaches its peak in about 20 hours, and then continues to decrease until around 120 hours. And with the sample shape variable increasing, its peak hardness reached raises, and the time required to reach the hardness peak also decreases. Samples’ hardness which are treated with different deformation variables under one-week natural aging conditions is displayed in Fig. 10(b). The hardness of the sample reaches its peak in about 16 hours, and then begins to decrease after maintaining it for about 60 hours. Similarly, with rolling deforming increasing, sample’s peak hardness raises, but its hardness decreases faster in the later stage. Fig. 10(b) shows the hardness curves of samples treated with different deformation variables at 120 °C/50 h. Samples’ hardness slightly raises and then decreases, and hardness decreasing rate raises with rolling deforming increasing. Based on these above data, for three different pre-treatments, with rolling deforming increasing, sample’s peak hardness will become higher and higher. However, as the aging process progresses, the rate of decrease in hardness value also becomes faster and faster. Then, in Fig. 11, the mechanical properties of samples under three different pre-treatment conditions are tested for different rolling deformation variables.
In Fig. 11(a), after 100 hours of re-aging without pre-aging treating, samples’ tensile and yield strengths do not significantly increase with rolling deforming increasing, while the elongation decreases significantly. In Fig. 11(b), with the increase of rolling deformation, the strength difference of the sample is not significant, but the elongation decreases significantly, which is consistent with the situation in Fig. 11(a). In Fig. 11(c), under this treatment, with rolling deforming increasing, sample's strength slightly raises, while the elongation still significantly decreases. Based on the above data, alloys with smaller deformation variables have better overall performance. To investigate the reason why the sample has smaller shape variables and better overall performance, the study selects samples with shape variables of 20 % and 80 %, and aged at 120 °C/100 h to observe their microstructure in Fig. 12.
Fig. 11Tensile force test results of samples under three different pre-treatments with different rolling deformation variables
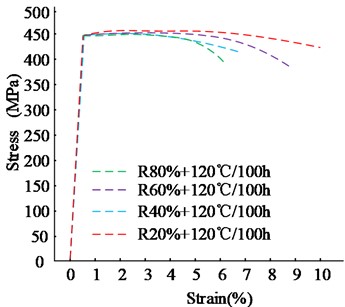
a) No time effective processing
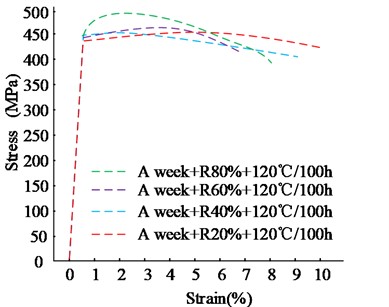
b) Natural aging treatment for one week
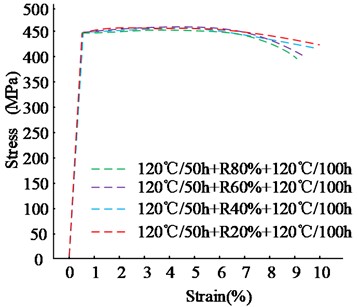
c) 120 °C/50 h aging treatment
By comparing Figs. 12(a) and (b), there is a significant difference in the surrounding observations of the samples after rolling deformation. Both 20 % and 80 % deformed alloys show no complete degradation of dislocations after subsequent aging. There are still many entangled dislocations and dislocating cells in alloy matrix, with dislocation entanglement more severe in 80 % deformed alloys. This phenomenon is caused by different chemical compositions and deformation amounts, which introduce different amounts and forms of dislocations. As the amount of intermediate deformation increases, the strengthening effect brought about by dislocations will also be enhanced. From the HADDF diagram in Fig. 12(a), a large number of small phases are precipitated from the 20 % deformed sample, with slightly larger precipitates on the dislocation cells. And 80 % of the deformed samples have both fine and coarse precipitates in the crystal. Due to the fact that coarse precipitates can easily become the starting point for crack generation and propagation in aluminum alloy deformation, samples with large deformation variables have similar strength and significantly lower ductility compared to samples with small phase variables. Based on the above experiments, the performance of aluminum alloys is determined by both the deformation variable and subsequent aging time.
Fig. 12TEM and HAADF-STEM plots of the sample projected along <112>Al
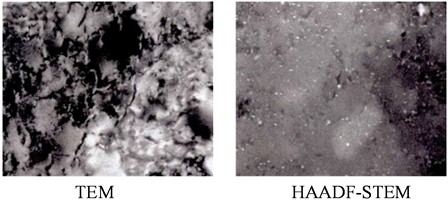
a) R20 %+120 °C/100 h 400 nm
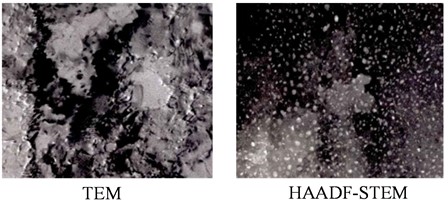
b) R80 %+120 °C/100 h 400 nm
5. Conclusions
To explore the comprehensive properties of aluminum alloys, the study focuses on the typical representative 7NO1 aluminum alloy in the 7xxx series of aluminum alloys. By controlling the aging process and rolling deformation variables, relevant experiments are conducted on the precipitates and mechanical properties of 7NO1 aluminum alloy, and the experimental results are measured using scientific instruments. These results confirm that under single-stage T6 aging treatment, the sample at 120 °C reaches a hardness peak of approximately 100 hours, with a peak value of approximately 129HV. The hardness of the sample at 120 °C is 5HV higher than that of the sample at 140 °C, and the time to reach the hardness peak is 50 hours earlier than that of the sample at 100 °C. The comprehensive performance of the sample at 100 °C is better. Secondly, from the results of sample deformation treatment, the hardness of the sample treated at 120 °C/50 h decreases from 126HV in pre-aging to 117HV in cold rolling state, and the elongation of the sample after rolling deformation is very poor. So relying solely on deformation treatment cannot improve the hardness and tensile properties of 7N01 aluminum alloy. After appropriate pre-aging treatment, the sample can achieve higher strength than T6 aging treated alloy and maintain good ductility. The use of excessively large deformation variables is not conducive to optimizing the alloy material, and this experimental sample's strength and elongation is downward with deformation variables increasing. Although these above experiments have gained some understanding of the characteristics of 7NO1 aluminum alloy, research on other properties like tensile strength, impact toughness, etc. is not sufficient. Further experiments will be conducted to expand the testing scope and comprehensively evaluate the comprehensive performance of 7NO1 aluminum alloy in the future.
References
-
Y. Hu et al., “Correlation analysis of noise sound pressure and vibration in aluminum alloy milling,” Journal of Vibration and Control, Vol. 28, pp. 276–289, 2022, https://doi.org/10.1177/10775463209759
-
E. A. Larson et al., “Optimize multiple peening effects on surface integrity and microhardness of aluminum alloy induced by LSP,” Materials Sciences and Applications, Vol. 14, No. 3, pp. 208–221, Jan. 2023, https://doi.org/10.4236/msa.2023.143012
-
T. Liu et al., “Preparation, structure and properties of Mg/Al laminated metal composites fabricated by roll-bonding, a review,” Journal of Magnesium and Alloys, Vol. 10, No. 8, pp. 2062–2093, Aug. 2022, https://doi.org/10.1016/j.jma.2022.08.001
-
V. Alexandrov, B. Kudryashov, K. Ivanov, and V. Vdovin, “Supersonic oscillation impact upon aging process of different metal alloys,” Science intensive technologies in mechanical engineering, Vol. 2020, No. 2, pp. 10–15, Feb. 2020, https://doi.org/10.30987/2223-4608-2020-2020-2-10-15
-
S. Saravanan and K. Raghukandan, “Microstructure, strength and welding window of aluminum alloy−stainless steel explosive cladding with different interlayers,” Transactions of Nonferrous Metals Society of China, Vol. 32, No. 1, pp. 91–103, Jan. 2022, https://doi.org/10.1016/s1003-6326(21)65780-1
-
L. Ying et al., “Experimental study of interfacial heat transfer coefficient for 7XXX series aluminum alloy in HFQ warm forming,” Chinese Journal of Nonferrous Metals, Vol. 28, No. 4, pp. 662–669, 2018, https://doi.org/10.19476/j.ysxb.1004.0609.2018.04.03
-
Y. Lee, H. Choi, S. Ahn, C. Lee, and S. Kim, “Resistance to stress corrosion cracking of high-strength 7xxx series aluminum alloys in 3.5% NaCl solution,” Korean Journal of Metals and Materials, Vol. 56, No. 10, pp. 708–717, Oct. 2018, https://doi.org/10.3365/kjmm.2018.56.10.708
-
H. L. Wei, J. W. Elmer, and T. Debroy, “Three-dimensional modeling of grain structure evolution during welding of an aluminum alloy,” Acta Materialia, Vol. 126, pp. 413–425, Mar. 2017, https://doi.org/10.1016/j.actamat.2016.12.073
-
H. Li, J. Xu, H. Yang, H. Yang, and G.-J. Li, “Sequential multi-objective optimization of thin-walled aluminum alloy tube bending under various uncertainties,” Transactions of Nonferrous Metals Society of China, Vol. 27, No. 3, pp. 608–615, Mar. 2017, https://doi.org/10.1016/s1003-6326(17)60068-2
-
Z. Butt, S. Mehmood, A. Sultan, N. Anjum, and W. Anwar, “Determination of residual stress distribution in high strength aluminum alloy after edm,” Advances in Science and Technology Research Journal, Vol. 11, No. 1, pp. 29–35, Mar. 2017, https://doi.org/10.12913/22998624/68729
-
H. Li, S. Huang, and Z. Wang, “T651 aging process of Alumec89 alloy tooling plate,” Heat Treatment of Metals, Vol. 43, No. 1, pp. 211–214, 2018, https://doi.org/10.13251/j.issn.0254-6051.2018.01.044
-
X. Fan, Z. Zheng, and X. Chen, “Effect of aging process on microstructure and mechanical properties of 2297 Al-Li alloy,” Materials Science and Engineering of Powder Metallurgy, Vol. 22, No. 2, pp. 184–189, 2017, https://doi.org/10.3969/j.issn.1673-0224.2017.02.006
-
K. T. Akhil, J. Varghese, K. Vinoj, K. Shunmugesh, S. Arul, and R. Sellamuthu, “Influence of heat treatment and aging process on LM13 aluminium alloy cast sections: an experimental study,” Materials Today: Proceedings, Vol. 4, No. 8, pp. 7194–7201, Jan. 2017, https://doi.org/10.1016/j.matpr.2017.07.046
-
P. Gai, X. Huang, Y. Zeng, and M. Wang, “Research on microstructure and properties of aged 7050T451 aluminum alloy,” (in Chinese), Metallurgical and Materials Transactions B, Vol. 45, No. 2, pp. 419–426, May 2013, https://doi.org/10.1007/s11663-013-9873-1
-
P. Romański, “The influence of aging process parameters on selected mechanical properties of profiles from EN AW-6106 aluminium alloy,” Hutnik – Wiadomości Hutnicze, Vol. 1, No. 1, pp. 63–66, Jan. 2017, https://doi.org/10.15199/24.2017.1.17
-
G. Yang et al., “The microstructure evolution of 6061 aluminum alloy during dieless rolling thermal deformation,” Procedia Manufacturing, Vol. 50, pp. 51–55, Jan. 2020, https://doi.org/10.1016/j.promfg.2020.08.010
-
L. Zhao, S. Wei, D. Wu, D. Gao, and S. Lu, “δ-ferrite transformation mechanism and its effect on mechanical properties of 316H weld metal,” Journal of Materials Science and Technology, Vol. 57, pp. 33–42, Nov. 2020, https://doi.org/10.1016/j.jmst.2020.02.085
-
M. Sam, N. Radhika, and K. Pavan Sai, “Effect of heat treatment on mechanical and tribological properties of aluminum metal matrix composites,” Proceedings of the Institution of Mechanical Engineers, Part C: Journal of Mechanical Engineering Science, Vol. 234, No. 22, pp. 4493–4504, Apr. 2020, https://doi.org/10.1177/0954406220922253
-
G. Sirbiladze, B. Midodashvili, L. Midodashvili, and D. Siprashvili, “About one representation-interpreter of a monotone measure,” Journal of Computational and Cognitive Engineering, Vol. 1, No. 2, pp. 51–55, Dec. 2021, https://doi.org/10.47852/bonviewjcce2022010103
-
W. Pan, J. Boyle, M. Ramlan, C. Dun, M. Ismail, and K. Hakoda, “Material plastic properties characterization using a generic algorithm and finite element method modelling of the plane-strain small punch test,” in SPT Conference, May 2010.
-
M. S. Ismail, O. Ifayefunmi, and A. H. Mazli, “Combined stability of cone-cylinder transition subjected to axial compression and external pressure,” Thin-Walled Structures, Vol. 157, p. 107102, Dec. 2020, https://doi.org/10.1016/j.tws.2020.107102
About this article
The authors have not disclosed any funding.
The datasets generated during and/or analyzed during the current study are available from the corresponding author on reasonable request.
Honggang Zhang: conceptualization, formal analysis, writing-original draft preparation. Rui Chen: investigation, methodology, resources, writing-review and editing. Xiaomei Gu: validation, writing-review and editing.
The authors declare that they have no conflict of interest.