Abstract
In order to enhance the performance of magnesium alloy and galvanized steel welds, ultrasonic vibration was applied to the laser welding process, and the effect of ultrasonic on mechanical properties was verified through experimental methods. The laser welding system for the lap weld seam was designed, and the ultrasonic vibration module and image detection module were added, which can obtain the influence of ultrasonic vibration on the molten pool area. Under the conditions of ultrasonic vibration power of 1000 W and 0 W, the characteristics of the weld pool area, metallographic structure, tensile strength, fracture morphology, hardness, residual stress, wear resistance, and corrosion resistance of the weld specimen were compared. The image data acquisition structure indicated that ultrasonic vibration can effectively reduce the ineffective area of the molten pool and make the energy in the molten pool more concentrated. Under the influence of ultrasonic vibration, the maximum molten pool area decreased to 5.38 mm2, with a variation range of 3.9 %, and the proportion of pores was greatly reduced. Research found that ultrasonic vibration can significantly improve the microstructure characteristics of the fusion welding zone, with an average grain size reduced to 23 μm. The reduction of grain size and refinement of microstructure were beneficial to the improvement of mechanical properties of magnesium alloy joints, with a yield strength increase of 6.5 %. Ultrasonic vibration had little effect on the hardness of the heat affected zone, it can increase the average hardness of the weld zone by more than 5 % and reduce the maximum residual stress by more than 50 %. Under different pressure and friction speed conditions, the maximum wear amount can be reduced by more than 25 %. At the same time, the resistance to oxidation corrosion and electrochemical corrosion also can be improved to a certain extent.
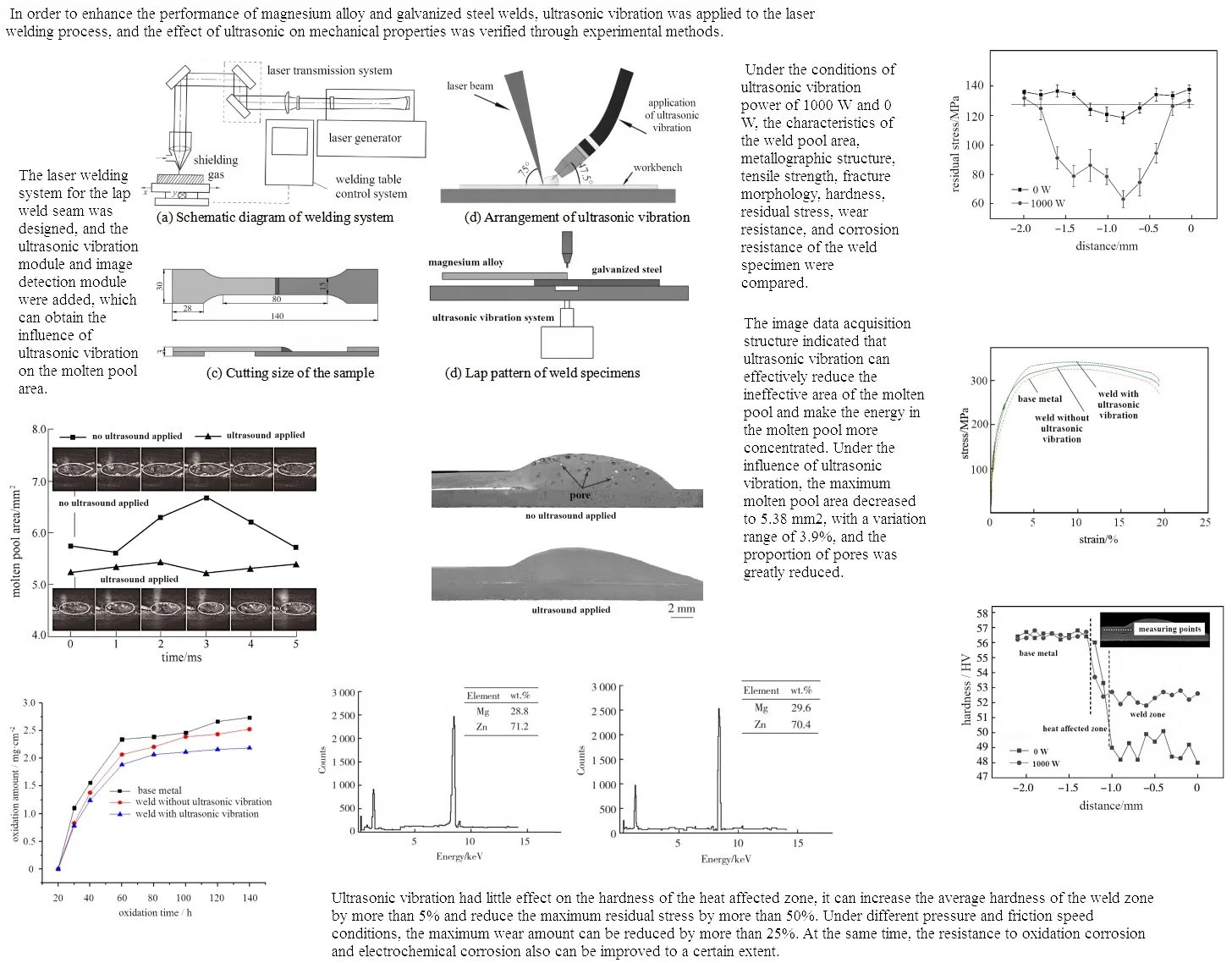
Highlights
- Under the conditions of ultrasonic vibration power of 1000 W and 0 W, the characteristics of the weld pool area, metallographic structure, tensile strength, fracture morphology, hardness, residual stress, wear resistance, and corrosion resistance of the weld specimen were compared.
- The image data acquisition structure indicated that ultrasonic vibration can effectively reduce the ineffective area of the molten pool and make the energy in the molten pool more concentrated.
- The laser welding system for the lap weld seam was designed, and the ultrasonic vibration module and image detection module were added, which can obtain the influence of ultrasonic vibration on the molten pool area.
1. Introduction
Magnesium alloy is manufactured based on magnesium and composed of other elements. Its main features include low density, high specific strength, high specific elastic modulus, good heat dissipation, good shock absorption, greater impact load capacity than aluminum alloy, and good corrosion resistance to organic matter and alkali [1]. At present, the welding of magnesium alloy is mainly used in engineering fields such as aviation, aerospace, transportation, chemical engineering, and rockets [2]. Therefore, the reliable connection between magnesium and galvanized steel has great potential for manufacturing lightweight structural components, and can also expand the application of magnesium alloys in various fields [3, 4]. However, the welding performance of magnesium alloys is relatively insufficient. Magnesium alloy welding is prone to many defects, such as: (1) Due to the accumulation of dissolved hydrogen in the molten pool, magnesium alloy is easy to form pores during welding, and the solidification rate of the molten pool is fast, resulting in the lack of time for hydrogen to escape. (2) Due to the high thermal conductivity, it is necessary to use high-power heat source and high-speed welding when welding magnesium alloys, which may cause metal overheating and grain growth in the weld and near-weld areas. (3) The coefficient of thermal expansion of magnesium alloy is large, about twice that of aluminum, so it is easy to produce large welding deformation and residual stress in the welding process. (4) Because the surface tension of magnesium is smaller than that of aluminum, the weld metal is prone to collapse during welding, which affects the weld forming quality. (5) Magnesium alloy is easy to form a low melting point eutectic structure with other metals, and it is easy to form crystallization cracks in welded joints. When the temperature of the joint is too high, the low melting point compounds in the joint structure will melt and appear holes at the grain boundary, or produce grain boundary oxidation.
In order to improve the fusion effect between different alloys, the following measures are mainly taken in engineering, such as increasing welding temperature, improving welding speed, adjusting welding current, selecting suitable welding materials, etc. However, these improvement of welding effect of magnesium alloys is relatively limited [5]. In recent years, ultrasonic assisted welding technology has received widespread attention. Literature shows that ultrasonic vibration can promote the formation of equiaxed grains in the central area of welded carbon steel [6]. In addition, ultrasonic vibration can effectively promote the gas leakage efficiency in the weld zone, enhance the welding pressure, restrain the excessive grain size, and reduce the thermal stress, which indicates that ultrasonic vibration is very suitable for magnesium alloy welding process. The performance of the weld seam is the result of the comprehensive effect of heat on the structural elements [7, 8]. The higher the welding speed, the more equiaxed grains formed by ultrasonic vibration. In order to verify and improve the welding effect of magnesium alloys, ultrasonic vibration is applied to the molten pool area of lap welds based on laser cladding technology. Compared with the conventional ultrasonic vibration processing research, a highly integrated intelligent welding system was innovatively proposed in this paper, including basic laser welding actuator, ultrasonic vibration transmitter and image data collector. The LINKS series controller was applied in the system, which can be used to synchronize the laser welding parameters and inert gas flow. The ultrasonic vibrator can realize different mechanical vibration frequencies, and the CCD camera can effectively monitor the state of the bubble in the weld zone, which provides a reliable basis for the study of molten pool area. Through the comparison of molten pool area, microstructure analysis, mechanical properties testing and other schemes, the effects of different ultrasonic vibration conditions on the microstructure and mechanical properties of magnesium alloy weld joints can be studied, and the optimal process parameters can be obtained, which has an important role in promoting the application of magnesium alloy welding.
2. Welding system design and sample preparation
2.1. Welding system design
Laser welding, as a new type of welding technology, uses laser as the input source and has advantages such as high power density, low welding heat input, small welding heat affected zone, and small welding deformation. When welding is not as good as alloy, it can ensure maximum product deformation and greatly improve welding efficiency. Meanwhile, laser welding, as a non-contact welding method, is easy to achieve automation. Compared to ordinary arc welding, laser cladding technology can provide a more stable and high-energy heat source. In order to ensure good control effect of ultrasonic vibration, the welding system is designed as shown in Fig. 1. The welding system not only includes basic welding actuators, but also integrates ultrasonic vibration transmitters and image data collectors. The welding base material is magnesium alloy and galvanized low-carbon steel, and the shielding gas is argon. The system is equipped with a LINKS series controller for centralized adjustment of laser welding parameters and inert gas flow rate. The ultrasonic vibrator can input 220 V, 50 Hz, or 110 V, 60 Hz electrical energy into the ultrasonic transducer, converting it into 36 kHz mechanical vibration. The generated ultrasound causes the molten pool to vibrate at a high frequency, with a vibration frequency of up to 36000 times per second, which can cause the weld seam to form a micro suspended state in the molten zone and promote bubble overflow.
Fig. 1Composition of laser welding system
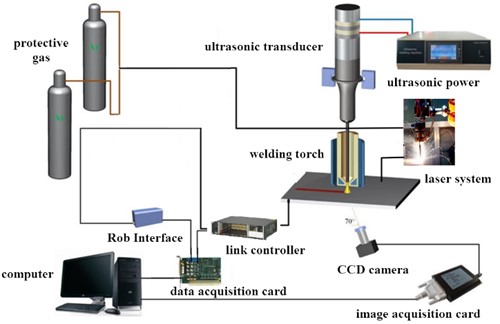
2.2. Preparation of weld specimens
The principle of the laser welding system is shown in Fig. 2(a), where the laser transmission system can effectively ensure the energy density of the laser beam, and the workbench control system can improve the accuracy and efficiency of the welding process. In order to ensure the stability of welding, keep the welding gun and the laser head relatively stationary, and use the lead screw guide rail to achieve uniform movement of the workpiece. The ultrasonic emitting end acts vertically on the welding torch, so that the ultrasonic vibration can be transmitted to the welding pool through the welding torch. As shown in Fig. 2(b), during the welding process, the angle of the laser beam is 75 degree, the angle of the welding wire is 47.5 degree, the distance between the optical wires is 2 mm, the defocusing amount is 2 mm, and the protection gas is selected with the purity of 99.999 % argon.
Fig. 2Principle of laser welding system and sample processing
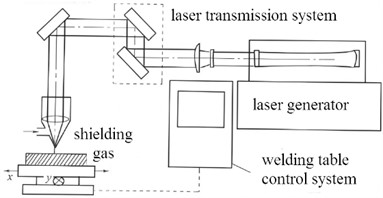
a) Schematic diagram of welding system
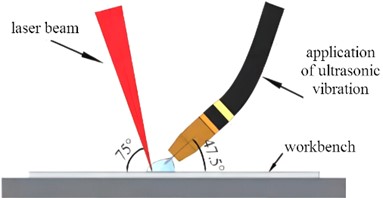
b) Arrangement of ultrasonic vibration
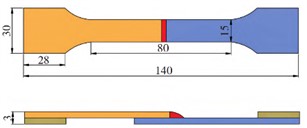
c) Cutting size of the sample
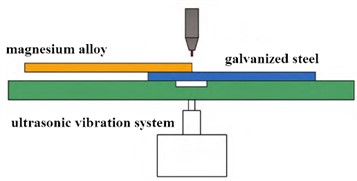
d) Lap pattern of weld specimens
In order to improve the sample preparation process, the substrate to be welded is magnesium alloy of AZ31S and galvanized steel of DX51D with sheet structure, which are processed into square shapes before welding, as shown in Fig. 2(c). The welding material is AZ31 magnesium alloy welding wire, with a diameter of 15 mm. Before the laser welding experiment, clean the oil stains on the surface of the welding plate and wire with anhydrous ethanol, and then polish with water sandpaper of different particle sizes to remove the oxide skin on the surface of the substrate. Assemble the prepared substrate as shown in Fig. 2(d), that is, overlap and fix the magnesium alloy plate on the surface of the galvanized steel plate. The protective gas flow rate is taken as 20 L/min. During welding, connect an ultrasonic generator and a laser welding system to introduce high-frequency ultrasonic vibration into the molten pool area during the welding process. After welding is completed, simultaneously turn off the power supply of the welding machine and ultrasonic generator. The welding parameters used in the test are shown in Table 1. The samples of overlapping welds meet the tensile test standards, so the tensile strength test can be directly conducted after completing the microhardness test. For ultrasonic welding systems, the higher the frequency of ultrasonic vibration, the lower the required power, making them more suitable for processing small welds. For this reason, an ultrasonic vibration frequency of 36 kHz (ultrasonic power is 1000 W) was adopted in the experiment and compared with the same type of experiment without ultrasonic vibration, which can verify the impact of ultrasonic vibration on mechanical properties. In order to further improve the reliability of the experimental results, for the non-continuous test scheme, each type of sample would be tested three times, and the average value was taken as the final result of the comparison curve.
Table 1Main parameters of laser welding
Parameter type | Value |
Laser power / W | 1500 |
Focal length / mm | 189 |
Spot diameter / mm | 2.5 |
Welding gun speed / mm·min-1 | 900 |
Welding wire speed / mm·min-1 | 1000 |
Protective gas flow / L·min-1 | 20 |
3. Experimental results and analysis
3.1. The effect of ultrasonic vibration on the weld pool area
Based on the image data acquisition module in the laser welding system, photos of the molten pool at different times can be obtained. By visual calculation, the effect of ultrasonic vibration on the weld pool area can be obtained, as shown in Fig. 3. It can be seen that ultrasonic vibration can effectively reduce the ineffective area of the molten pool, making the energy in the fusion zone more concentrated. In theory, this is more conducive to the diffusion efficiency of elements. From the data analysis, when there is no ultrasonic vibration, the maximum molten pool area is 6.68 mm2, and the overall fluctuation range is 18.3 %. Under the influence of ultrasonic vibration, the maximum molten pool area decreased to 5.38 mm2 and the variation range decreased to 3.9 %. The effective molten pool area is an important indicator for measuring the crystallization effect of metal in the weld zone. In addition, a smaller pool area also means a lower probability of occurrence of void defects. As shown in Fig. 4, the radiographic image of the weld area shows that ultrasonic vibration greatly reduces the proportion of gas pores. The molten pool pictures in Fig. 3 and Fig. 4 were taken by the author in the materials laboratory with CCD camera.
The molten pool metal is subjected to continuous cyclic alternating ultrasonic vibration. When the half cycle of ultrasonic waves acts on the molten pool liquid, the molten pool liquid is subjected to tensile action, resulting in the formation of a large number of cavitation bubbles, and accompanied by the formation of cavitation bubbles in some dendrites, which will rapidly grow. During the process of growth, cavitation bubbles absorb a large amount of surrounding heat, forming local supercooling and promoting liquid nucleation. According to the literature [9], increasing the ultrasonic power can increase the number of cavitation bubbles, thereby increasing the nucleation rate and achieving grain refinement of the weld microstructure. On the other hand, when the cavitation bubble grows to its limit, it will rupture and generate instantaneous impact force. The magnitude of the impact force is related to the ultrasonic power, and as the ultrasonic power increases, the impact force also continues to increase. When the ultrasonic power reaches a certain threshold, the impact force will break the initial formed dendrites. Throughout the entire welding process, cavitation bubbles continue to form, grow, and break in the liquid metal of the molten pool, ultimately effectively improving the microstructure of the joint weld and enhancing the welding strength.
Fig. 3Melt pool area at different times
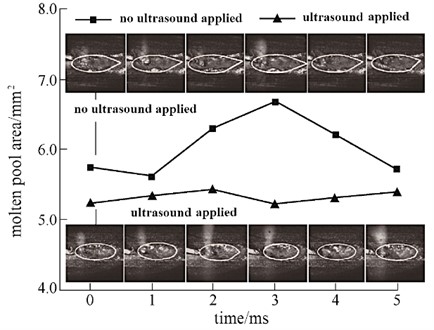
Fig. 4The effect of ultrasonic vibration on pore elimination
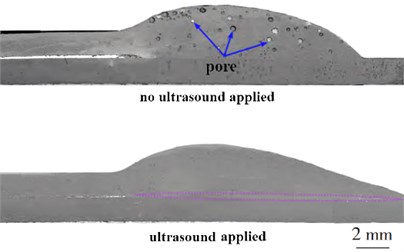
3.2. The effect of ultrasonic vibration on microstructure
In order to study the effect of ultrasonic vibration on microstructure, weld specimens were prepared at 0 and 1000 W ultrasonic power, and the metallographic structure as shown in Fig. 5 was obtained. It can be seen that the magnesium alloy substrate is mainly composed of equiaxed grains, with small grains and an average grain size of about 143 μm. During the welding process, the magnesium alloy base material melts with the welding wire, forming a fusion welding zone. When the ultrasonic power is 0, during the formation of the fusion welding zone, the grains become rough and uneven in shape, with an average grain size of about 51 μm. Compared with the base metal, the microstructure of the fusion welding zone becomes abnormally rough, which is not conducive to improving the mechanical properties of magnesium alloy joints [10]. After introducing 1000 W ultrasonic vibration during the welding process, it was found that the ultrasonic vibration process significantly improved the microstructure characteristics of the fusion welding zone, with grains similar to equiaxed grains, and the average grain size decreased to 23 μm. The reduction of grain size and refinement of microstructure are beneficial to the improvement of mechanical properties of magnesium alloy joints to a certain extent.
The precipitates on the grain boundaries of welds without ultrasonic vibration are a continuous network structure. After ultrasonic vibration treatment, the grain size of the weld alloy is significantly refined, the grain boundary precipitation phase transformation is fine, and the network structure is broken, improving the coarse morphology of the alloy grain boundary precipitation phase. The fusion zone between the magnesium alloy base material and the weld seam is shown in Fig. 6. It can be seen that after increasing ultrasonic vibration, the fusion line is still relatively clear and the layering phenomenon is more obvious. The microstructure images in Fig. 5 and Fig. 6 were taken by the author in materials laboratory with metallographic microscope.
Fig. 5Microstructural morphology of different samples
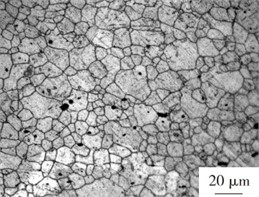
a) Base metal
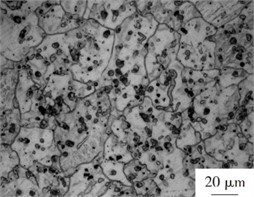
b) Weld without ultrasonic vibration
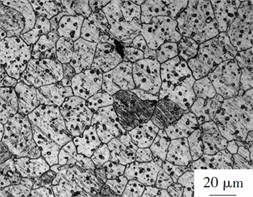
c) Weld with ultrasonic vibration
Fig. 6Microstructural morphology of fusion zone
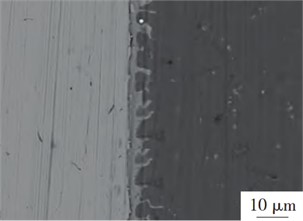
a) Fusion zone without ultrasonic vibration
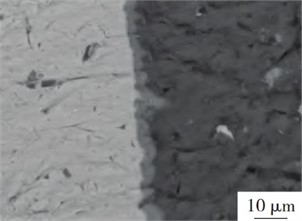
b) Fusion zone with ultrasonic vibration
Fig. 7Atlases of energy distribution of fusion zone
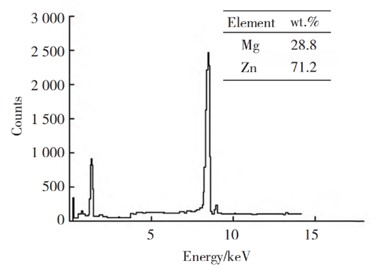
a) Fusion zone without ultrasonic vibration
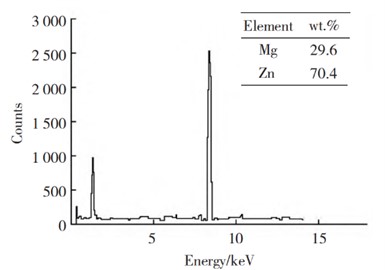
a) Fusion zone with ultrasonic vibration
On the fusion line, take the center point for energy spectrum testing to detect the relative content of magnesium and zinc elements, as shown in Fig. 7. It can be seen that the reaction layer contains a large amount of Zn and Mg elements, indicating that the reaction layer is composed of intermetallic compounds of Mg and Zn, which is the key to achieving reliable connection between magnesium alloy and galvanized steel. When the ultrasonic power is set to 1000 W, a uniform and continuous reaction layer is generated in the welding fusion zone. Compared with welds without ultrasonic vibration, ultrasonic vibration changes the morphology of the reaction layer, making the thickness of the reaction layer more uniform. The reaction layer mainly contains 70.4 % Zn and 29.6 % Mg, similar to the reaction layer without ultrasonic vibration. This indicates that the introduction of ultrasonic vibration can effectively improve the morphology of the reaction layer, but it will not change the composition of the reaction layer. It can also be proved that the effect of ultrasonic vibration on the microstructure is basically consistent with the conclusion obtained in literature [11].
3.3. Testing of tensile strength and impact toughness
When ultrasonic vibration is used to treat metal materials, its excitation effect causes changes in the microstructure of the material, which in turn affects the mechanical properties of the material. Research on metallographic structure has shown that ultrasound eliminates internal defects and bubbles in metal materials, reduces grain size, and improves grain morphology. Therefore, it can be inferred that ultrasonic vibration can enhance the tensile strength of welds. To verify this conclusion, a tensile testing machine model HD-B606B was used for strength testing. This equipment belongs to a microcomputer controlled electro-hydraulic servo universal testing machine, which integrates electro-hydraulic servo automatic control, automatic measurement, data acquisition, screen display, and test result processing. It is equipped with a precision oil pump, an electro-hydraulic servo valve, and a PC servo controller on the platform of a cylinder mounted host, achieving multi-channel closed-loop control and capable of completing fully automatic control and measurement functions during the experimental process. Compared with the research method in reference [12], the test scheme in this paper can better reflect the change law of the whole damage cycle. The strength test results obtained by comparing three different samples are shown in Fig. 9. The microstructure images in Fig. 9 were taken by the author in materials laboratory with scanning electron microscope. It can be seen that ultrasonic vibration has a certain improvement effect on the ultimate strength, yield strength, and proportional limit of the weld, which has a good adaptability to the complex working conditions of the weld. According to the fracture morphology of magnesium alloy, ultrasonic vibration has a certain effect on improving the toughness of the material, with a yield strength increase of 6.5 %. Ultrasonic vibration promotes the formation, growth, and interconnection of hollow nuclei, and the phenomenon of equiaxed dimples is more obvious, which is also an important manifestation of material toughness. The specimen without ultrasonic vibration has relatively more tearing edges in the fracture surface, and the elongation direction is parallel to the fracture direction. Its stress state tends to be tensile tearing type.
Fig. 8Tensile strength test results
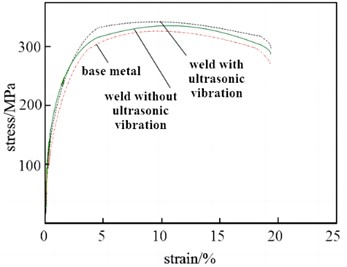
3.4. Testing of hardness and residual stress
Based on the VH3100 microhardness tester, hardness tests were conducted on different points in the horizontal direction of the joint. Each sample was tested three times, and the average value was applied, as shown in Fig. 10. The results indicate that when hardness testing is carried out along the horizontal direction of the joint, the hardness values in different areas of the joint vary significantly. For joints without ultrasonic vibration, the hardness value of the magnesium alloy base material is the highest, the hardness value of the fusion welding zone is the lowest, and the hardness value of the heat affected zone is between the two. When ultrasonic vibration is applied to the joint, the hardness distribution of the magnesium alloy base material, heat affected zone, and fusion welding zone is similar to that of the joint without ultrasonic vibration. However, it is worth noting that the hardness value of the fusion welding zone of joints subjected to ultrasonic vibration is higher than that of joints without vibration, and the fluctuation of hardness value is smaller. In other words, ultrasonic vibration has little effect on the hardness of the heat affected zone, but can increase the average hardness of the weld zone by more than 5 %. This is because the introduction of ultrasonic vibration effectively improves the microstructure of the fusion welding zone, resulting in a decrease in grain size and a more uniform shape, resulting in an increase in hardness value.
Fig. 9Fracture morphology of weld specimen
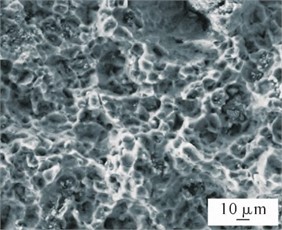
a) Without ultrasonic vibration

b) With ultrasonic vibration
Fig. 10Microhardness test results
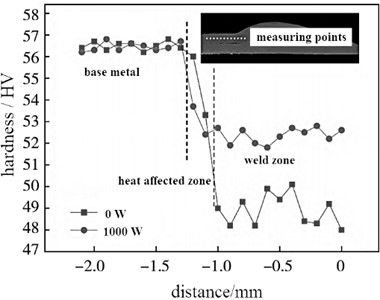
For the testing of residual stress, the indentation strain method is adopted. This testing technique requires using a resistance strain gauge as a sensitive component for measurement, using impact loading to create an indentation at the center of the strain pattern instead of drilling. The strain increment in the elastic zone outside the indentation area is recorded using a strain gauge, in order to obtain the true elastic strain corresponding to the magnitude of residual stress and determine the magnitude of residual stress. Compared with reference [13], the test method is more conducive to analyzing the residual stress analysis rule under a specific path. The residual stress distribution results at different measurement points are shown in Fig. 11, it can be seen that ultrasonic vibration can effectively reduce the residual stress at the heat affected zone position. The maximum residual stress can be reduced by 50 %. Meanwhile, based on the influence of thermal cycling, it can be inferred that the plasticity of this location is relatively poor compared to the base metal and weld zone. Reducing residual stress is beneficial for improving shaping and toughness.
Fig. 11The residual stress distribution test results
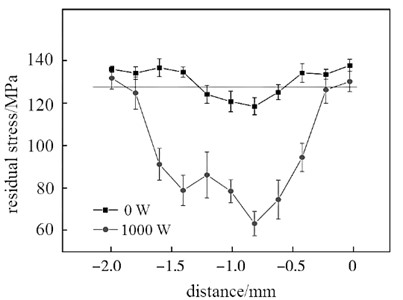
3.5. Analysis of wear resistance and corrosion resistance
To study the effect of ultrasonic vibration on the wear resistance of weld surface, the weld specimen was placed in an RTEC friction testing machine for high-frequency reciprocating friction testing. Compared with conventional friction testing [14, 15], the test scheme is more comprehensive and can directly obtain the internal correlation between friction and wear from the test results. During the test, keeping the reciprocating frequency, relative velocity, temperature, and other conditions of different samples consistent, the transient friction coefficient changes of the base material, welds with ultrasonic vibration, and welds without ultrasonic vibration can be obtained, as shown in Fig. 12. It can be seen that the friction coefficient in the weld zone is lower than that of the base metal, and under the influence of ultrasonic vibration, the fluctuation of the friction coefficient in the weld zone is very small, resulting in higher friction stability. Based on the hardness test results, it can be inferred that ultrasonic vibration can improve wear resistance.
Fig. 12The variation law of transient friction coefficient
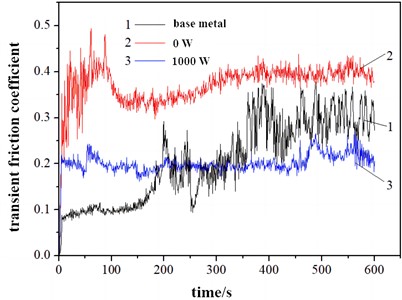
To further verify the effect of ultrasound on the wear resistance of welds, after high-frequency reciprocating friction test under 60 N load, the surface microstructure was observed under FEI scanning electron microscope by the author in materials laboratory as shown in Fig. 13. It can be seen that under the same load conditions, the ultrasonic vibration specimen has stronger resistance to pressure and friction, and its surface groove depth is smaller, and there is no peeling problem. In addition, the scratches inside the weld seam are relatively uniform, which to some extent proves the influence of ultrasonic vibration on toughness.
Fig. 13Friction morphology of weld specimen
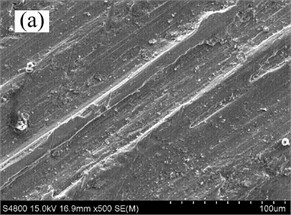
a) Without ultrasonic vibration
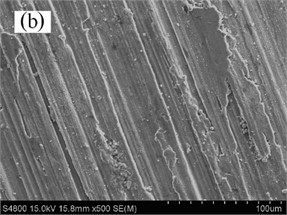
b) With ultrasonic vibration
To verify the improvement effect of ultrasonic vibration on the wear resistance of welds, the wear characteristics were measured under the conditions of dry friction test cycles of 24 hours and 48 hours, respectively. After the test cycle is completed, the sample is placed in an ultrasonic cleaning instrument for processing [16]. Through high-precision balance testing, the wear amount of the weld sample without ultrasonic vibration and of the weld sample with ultrasonic vibration are obtained, as shown in Table 2. It can be seen that under different pressure and friction speed conditions, the wear resistance of the weld specimen subjected to ultrasonic vibration is improved, and the wear amount can be reduced by more than 25 %. The wear amount is not proportional to time, but compared to the initial sample, the sample after ultrasonic vibration has better wear endurance and stability.
Table 2Wear test results
Parameters and conditions | 10 N 10 mm/s | 20 N 20 mm/s | 10 N 20 mm/s | 20 N 10 mm/s | ||||
/ h | 24 | 48 | 24 | 48 | 24 | 48 | 24 | 48 |
/ mg | 18 | 29 | 28 | 44 | 22 | 40 | 25 | 42 |
/ mg | 12 | 20 | 17 | 31 | 16 | 29 | 20 | 33 |
If magnesium alloy welding products are used in corrosive environments, it is required that the welding seam not only meets the mechanical requirements, but also meets the ability to resist oxidation and electrochemical corrosion. In order to determine the effect of weak acid environment on the corrosion resistance characteristics of weld specimens, an acetic acid solution with a pH value of 2.8 was prepared and the specimens were placed in the solution for 140 hours. To enhance the corrosion effect, keep the acetic acid solution flowing and maintain a constant temperature of 80 ℃. Test the mass reduction value every 10 hours. It should be noted that the samples after each corrosion need to undergo ultrasonic cleaning to ensure the accuracy of the testing. The oxidation efficiency of different samples in acidic environments is shown in Fig. 14. It can be seen that the oxidation resistance of the weld seam is slightly stronger than that of the base material, and the corrosion equilibrium is reached after about 60 hours. In addition, the ultrasonic vibration of the weld specimen reduces oxidation to a certain extent, which has an improved effect on oxidation resistance and corrosion resistance.
In order to further verify the corrosion resistance effect, pitting potential testing was applied. This method usually refers to the lowest potential of point corrosion on the surface of metal materials in a certain corrosive medium. The higher the pitting potential, the smaller the tendency of the material to produce pitting in the corrosive medium. Therefore, the greater the pitting potential of the material, the better its corrosion resistance. The polarization curves of different weld specimens in a 3.5 % NaCl solution are shown in Fig. 15. It can be seen that the electrochemical corrosion test results of these three samples are consistent with the results of the oxidation corrosion weight loss rate test. Ultrasonic vibration can significantly refine the grain size of weld alloys. The finer and more uniform the alloy grain, the more uniform and dense the protective film formed by the corrosion products during the corrosion process. The protective film can better prevent the corrosion solution from corroding the alloy surface and improve the corrosion resistance of the alloy. During the corrosion process, the precipitates at the grain boundaries of the alloy serve as the cathode for galvanic corrosion, participating in the corrosion dissolution of the alloy substrate anode, and are prone to severe local corrosion. Therefore, a large amount of coarse precipitates at grain boundaries can lead to poor corrosion resistance of the alloy. Ultrasonic vibration can significantly reduce the number of coarse phases at the grain boundaries of the weld alloy, resulting in finer precipitation and phase transformation, thus improving the corrosion resistance of the alloy. Otherwise, a large number of network phases can lead to a decrease in the corrosion resistance of the alloy.
Fig. 14Friction morphology of weld specimen
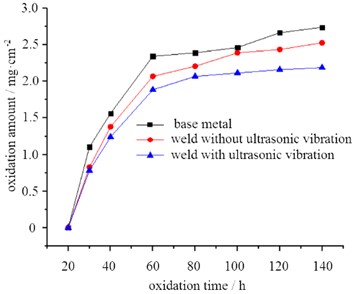
Fig. 15Polarization curves of different samples
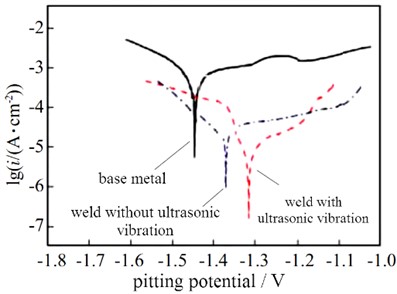
4. Conclusions
Welding with different types of materials is prone to problems such as insufficient fusion, and ultrasonic vibration can effectively solve this problem. Experimental studies were conducted on the actual molten pool area, metallographic structure, strength, toughness, hardness, residual stress, wear resistance, and corrosion resistance of the overlap weld seam between magnesium alloy and galvanized steel. It can be proven that ultrasonic vibration can comprehensively improve the mechanical properties of welds, and the main conclusions are as follows.
(1) Ultrasonic vibration assisted welding technology can effectively improve the weld formation of magnesium alloy and galvanized steel joints, and eliminate defects such as pores in the fusion welding area of the joints. For joints without the application of ultrasonic vibration assisted welding technology, the grain size in the fusion welding zone of the joint becomes coarse and uneven. When ultrasonic vibration with a power of 1000 W is introduced during the welding process, the grains in the fusion welding zone of the joint are approximately equiaxed. In addition, the introduction of ultrasonic vibration can effectively improve the morphology of the reaction layer in the weld zone, making its thickness more uniform.
(2) Ultrasonic vibration can comprehensively improve the mechanical properties of welds, including tensile strength and toughness. Ultrasonic vibration also can effectively improve the hardness and wear resistance of magnesium alloy welds. Under conditions of 10-30 N pressure and 10-20 mm/s relative friction speed, the wear amount can be reduced by more than 25 %. In terms of the types of wear damage, even in weakly acidic oil environments, the damage is mainly small scratches, and there are no phenomena such as pitting, pits, or surface peeling.
(3) From the current development trend, ultrasonic vibration welding can be used in metal, plastic and a variety of other materials, including medical, consumer electronics, automotive manufacturing, safety subsystems, aerospace, precision machinery, industrial parts manufacturing and other fields. However, the ultrasonic vibration welding system is also a machine device, which is prone to failure due to external factors. The future development should be aimed at improving the efficiency of ultrasonic welding, improving the human-machine interface and its control equipment, so that it has automation, intelligence and safety, in order to reduce the dependence on operators.
References
-
M. Kumar, A. Das, and R. Ballav, “Influence of the Zn interlayer on the mechanical strength, corrosion and microstructural behavior of friction stir-welded 6061-T6 aluminium alloy and AZ61 magnesium alloy dissimilar joints,” Materials Today Communications, Vol. 35, No. 1, p. 105509, Jun. 2023, https://doi.org/10.1016/j.mtcomm.2023.105509
-
R. Anand and R. Padmanabhan, “Influence of friction stir welding process parameters and statistical behaviour of the novel interlock aluminum alloys joint with SiCp reinforcement,” CIRP Journal of Manufacturing Science and Technology, Vol. 45, No. 7, pp. 260–270, Oct. 2023, https://doi.org/10.1016/j.cirpj.2023.07.002
-
G. Gohel, C. Z. Soh, K. F. Leong, P. Gerard, and S. K. Bhudolia, “Effect of PMMA coupling layer in enhancing the ultrasonic weld strength of novel room temperature curable acrylic thermoplastic to epoxy based composites,” Polymers, Vol. 14, No. 9, p. 1862, May 2022, https://doi.org/10.3390/polym14091862
-
S. Vulovic, M. Zivkovic, A. Pavlovic, R. Vujanac, and M. Topalovic, “Strength analysis of eight-wheel bogie of bucket wheel excavator,” Metals, Vol. 13, No. 3, p. 466, Feb. 2023, https://doi.org/10.3390/met13030466
-
K. Singh, G. Singh, and H. Singh, “The influence of holding time on the characteristics of friction stir welded dissimilar magnesium alloy joints during post welding heat treatment,” Proceedings of the Institution of Mechanical Engineers, Part L: Journal of Materials: Design and Applications, Vol. 237, No. 1, pp. 170–182, Jun. 2022, https://doi.org/10.1177/14644207221106576
-
Z. Hu, X. Li, H. Yan, X. Wu, H. Qun, and J. Lin, “Effects of ultrasonic vibration on microstructure evolution and elevated-temperature mechanical properties of hot-extruded Mg-6Al-0.8Zn-2.0Sm wrought magnesium alloys,” Journal of Alloys and Compounds, Vol. 685, No. 5, pp. 58–64, Nov. 2016, https://doi.org/10.1016/j.jallcom.2016.05.210
-
B. Yang et al., “Effect of temperature on microstructures and mechanical properties of medium‐carbon low‐alloy steel by caliber rolling,” Materialwissenschaft und Werkstofftechnik, Vol. 53, No. 9, pp. 1106–1120, Sep. 2022, https://doi.org/10.1002/mawe.202200017
-
M. Moorthy, J. Palraj, L. Kannan, S. Katlakunta, and S. Perumal, “Structural, microstructural, magnetic, and thermoelectric properties of bulk and nanostructured n-type CuFeS2 Chalcopyrite,” Ceramics International, Vol. 48, No. 19, pp. 29039–29048, Oct. 2022, https://doi.org/10.1016/j.ceramint.2022.04.287
-
A. Teyeb, M. Salimi, E. El Masri, W. Balachandran, and T.-H. Gan, “Analytical simulation of the microbubble collapsing in a welding fusion pool,” Materials, Vol. 16, No. 1, p. 410, Jan. 2023, https://doi.org/10.3390/ma16010410
-
Q. Luo et al., “Achieving grain refinement of α-Al and Si modification simultaneously by La-B-Sr addition in Al-10Si alloys,” Journal of Materials Science and Technology, Vol. 135, No. 1, pp. 97–110, Feb. 2023, https://doi.org/10.1016/j.jmst.2022.07.009
-
J. Zhao, C. Wu, and H. Su, “Acoustic effect on the tensile properties and metallurgical structures of dissimilar friction stir welding joints of Al/Mg alloys,” Journal of Manufacturing Processes, Vol. 65, No. 1, pp. 328–341, May 2021, https://doi.org/10.1016/j.jmapro.2021.03.057
-
F. Vahid, A. Rezvan, and A. Amir, “Influence of ultrasonic vibrations on the properties of press-and-sintered titanium,” Proceedings of the Institution of Mechanical Engineers, Vol. 236, No. 11, pp. 1518–1525, 2022, https://doi.org/10.1177/0954405422107838
-
D. Venkata Sivareddy, P. V. Krishna, and A. Venu Gopal, “Effect of thermo-mechanical loading on machining induced residual stresses in ultrasonic vibration assisted turning of Ti6Al4V alloy,” Proceedings of the Institution of Mechanical Engineers, Part B: Journal of Engineering Manufacture, Vol. 236, No. 13, pp. 1793–1806, Apr. 2022, https://doi.org/10.1177/09544054221093565
-
H. P. Zhao, “Friction and wear properties of laser remanufactured cobalt based alloy cladding layer on the excessively worn surface of brake disc,” (in Chinese), Mechanical Engineering Materials, Vol. 46, No. 6, pp. 78–83, 2022.
-
L. Zhou and M. Song, “Stability of cracked functionally graded graphene-reinforced beams under magnetic field,” Journal of Scientific Research and Reports, Vol. 28, No. 4, pp. 14–24, Apr. 2022, https://doi.org/10.9734/jsrr/2022/v28i430511
-
Q. Song, H. Wang, S. Ji, Z. Ma, W. Jiang, and M. Chen, “Improving joint quality of hybrid friction stir welded Al/Mg dissimilar alloys by RBFNN-GWO system,” Journal of Manufacturing Processes, Vol. 59, No. 9, pp. 750–759, Nov. 2020, https://doi.org/10.1016/j.jmapro.2020.10.037
About this article
The paper is supported by provincial scientific research projects (2023YFG1066).
The datasets generated during and/or analyzed during the current study are available from the corresponding author on reasonable request.
The authors declare that they have no conflict of interest.