Abstract
In order to solve the problems of excessive weight and unreasonable structure of anchor machine parts caused by traditional design methods, a lightweight optimization method was proposed based on pre-stressed modal analysis. The design variables were determined, and the parameterized model was established by using ANSYS Workbench. Under ultimate load conditions, the strength of wall frame board and lower box bodies was simulated and calculated. Through modal analysis, the discretized natural frequencies under different design variables could be obtained. The multi-objective genetic algorithm and sequence quadratic programming were respectively used to calculate the lightweight analysis model. The results showed that the weight of the supporting components in ship anchor can be reduced by more than 5 % without reducing strength and equivalent stiffness.
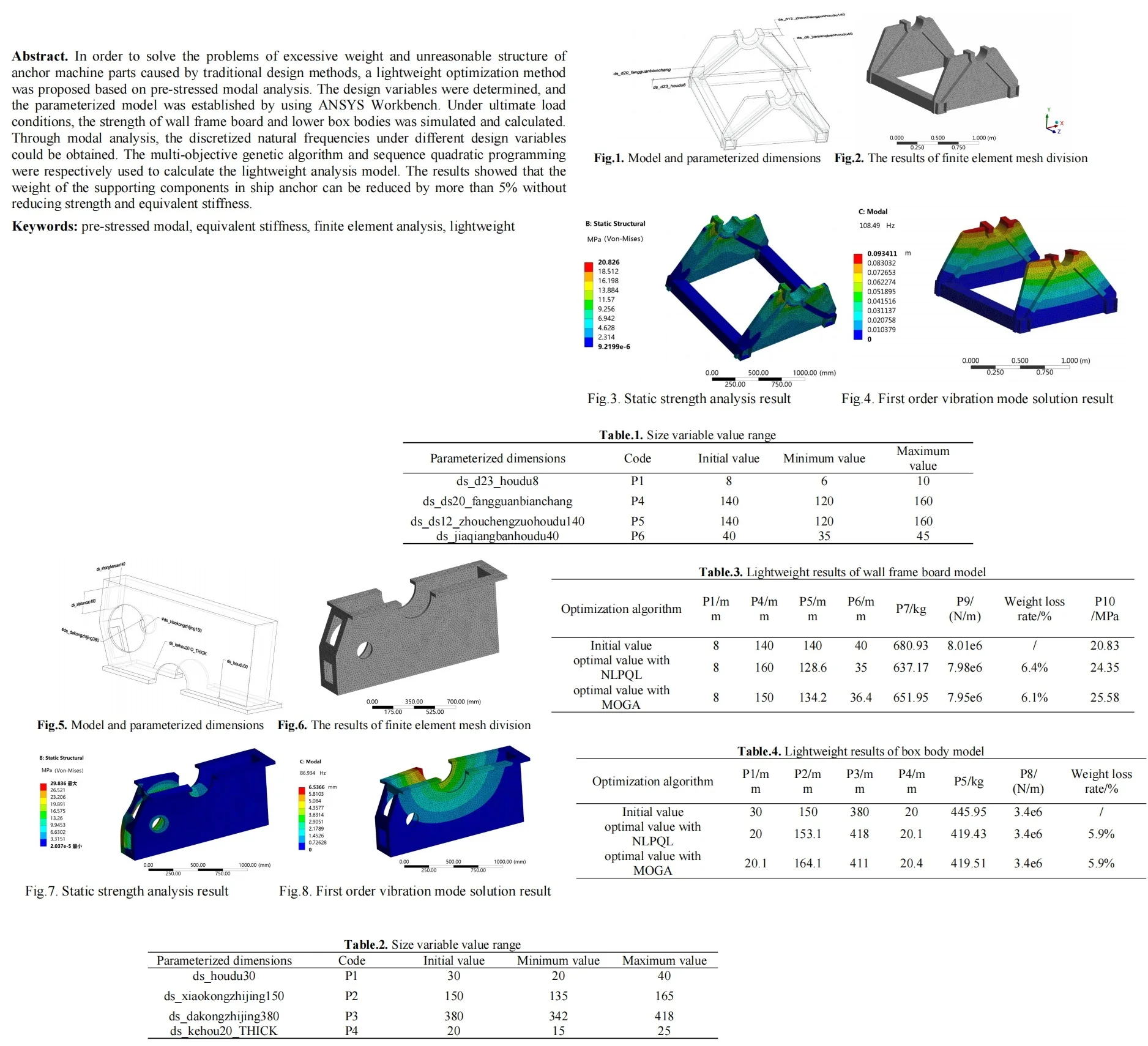
Highlights
- In order to solve the problems of excessive weight and unreasonable structure of anchor machine parts caused by traditional design methods, a lightweight optimization method was proposed based on pre-stressed modal analysis.
- The design variables were determined, and the parameterized model was established by using ANSYS Workbench.
- The multi-objective genetic algorithm and sequence quadratic programming were respectively used to calculate the lightweight analysis model.
1. Introduction
With the development of ocean and shipbuilding technology, the research and development of the shipbuilding industry and its auxiliary equipment has also gained great development space [1]. However, currently, there are still problems with the large volume, bulky structure, and low efficiency of ship auxiliary equipment. In order to ensure the smooth operation of the anchor components, a large support structure needs to be installed. The operating speed of the anchor machine rotor system is not constant, and the resonance problem generated by the rotor must be considered [2, 3]. Pre-stress modal analysis of the support structure must be carried out to obtain the natural frequency and corresponding vibration mode, which can be used as a reference for the operating frequency of the rotor to prevent structural damage caused by resonance and ensure safe operation. Modal analysis studies complex vibrations by superimposing various independent subsystems based on the principle of superposition [4, 5]. At present, the main methods of modal analysis are excitation response modal analysis and finite element analysis. There is no further in-depth research on the lightweight design of the supporting components of ship anchor winches, which is not in line with the development direction of economy, energy conservation, and green environmental protection [6]. Therefore, specific technical methods are needed to reduce the weight of the anchor winch support frame without reducing stiffness. There are three main approaches to the lightweight design of anchor winch structures, including lightweight structural materials, lightweight structural optimization, and lightweight manufacturing processes [7, 8]. Lightweight structural materials refer to the use of reasonable high-strength or lightweight metal and non-metallic materials to replace the original structural materials, such as high-strength steel, titanium alloys, magnesium aluminum alloys, and composite materials. Structural optimization and lightweight design refer to optimizing the size, shape, and topology of the original structure based on different design variables. Lightweight manufacturing technology refers to the use of advanced manufacturing processes such as high-pressure forming, high-strength steel hot forming, and laser welding for production. Regarding the working and production conditions of the anchor machine, especially wall frame board and box body, the lightweight structure method was adopted and studied in the paper. A multi-objective optimization method was innovatively proposed based on the load characteristics of different key supporting components of ships. Through different extreme value algorithms, the optimal values of design variables under constraint conditions can be achieved, and the quality of parts can be effectively reduced without reducing performance or changing the process.
2. Analysis of pre-stressed modal characteristics
2.1. Parameterized wall frame board model
The wall frame board model contains standard square steel components. Therefore, after optimizing the extreme value search of the mathematical model, it is necessary to select the optimal side length and thickness of the square steel nearby. The model and parameterized dimensions of the supporting components in the transmission device are shown in Fig. 1, and there are four parameterized dimensions set according to the structural characteristics. Due to model constraints and reference issues, the dimensions of the square tube thickness are set to three, with codes named P1, P2, and P3, and P1 = P2 = P3. The remaining parameterized dimensions are divided into square tube side lengths ds_ds20_fangguanbianchang, code named P4, bearing seat thickness ds_ds12_zhouchengzuohoudu40, code named P5, reinforced plate thickness ds_jiaqiangbanhoudu140, code named P6. The design range of these four types of parameterized dimensions is shown in Table 1, ensuring that there is no structural interference or reference failure under extreme size conditions.
Table 1Size variable value range
Parameterized dimensions | Code | Initial value | Minimum value | Maximum value |
ds_d23_houdu8 | P1 | 8 | 6 | 10 |
ds_ds20_fangguanbianchang | P4 | 140 | 120 | 160 |
ds_ds12_zhouchengzuohoudu140 | P5 | 140 | 120 | 160 |
ds_jiaqiangbanhoudu40 | P6 | 40 | 35 | 45 |
Fig. 1Model and parameterized dimensions
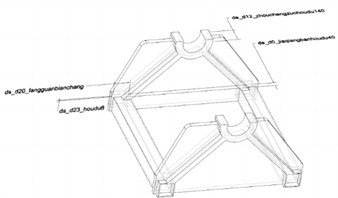
Fig. 2The results of finite element mesh division
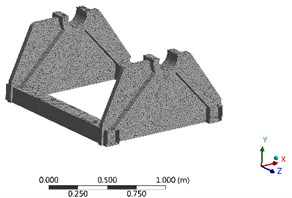
The supporting component is the main load-bearing component of the entire anchor transmission device, and its equivalent stiffness characteristics are one of the key factors to ensure transmission accuracy, reduce wear and noise [9, 10]. Therefore, in lightweight research, it is necessary to assume that the initial equivalent stiffness is not lower. The external gravity load on the wall frame panel component is 10.24 kN, and the torque load is 1.31e8 N·mm, so the prestress cannot be ignored in modal analysis. After importing the supporting component model in Creo into ANSYS through an interface, define parameters in the model design module. Establish a static structural analysis module in ANSYS Workbench and couple the modal analysis module with the structural analysis module. The preprocessing stage of the model includes defining material properties, meshing, applying boundary conditions and loads, and setting modal calculation conditions [11, 12]. Define the material attribute of the model as Q235 in the material library, set the quality parameter as the optimization objective, and code it as P7. For finite element mesh partitioning, an adaptive type was adopted, with a mesh resolution level of 7. Slow mode was used for transitions between different planes, and medium mode was used for the center of the span angle. The final result was 75883 elements and 131611 nodes. The mesh partitioning result is shown in Fig. 2. Through grid optimization and local refinement verification, it is shown that this grid partitioning method can achieve high accuracy and computational efficiency. The bottom surface is defined as a fixed constraint, and the upper end face is subjected to a gravity load. The final static strength and first order vibration mode analysis results are shown in Fig. 3 and Fig. 4. It can be seen that the maximum stress of the lower box is only 20.83 MPa, set as P10, and the first natural frequency obtained under prestressed conditions is 108.49, set as P8. After returning to the parameter definition module, add the equivalent stiffness parameter and define it as P9.
Fig. 3Static strength analysis result
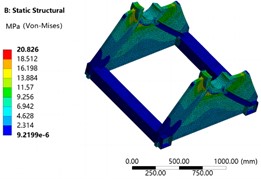
Fig. 4First order vibration mode solution result
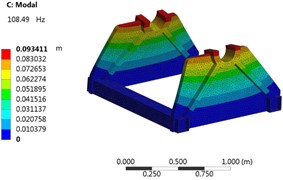
2.2. Parameterized box body model
The model and parameterized dimensions of the lower box cover in the transmission device are shown in Fig. 5. There are 4 parameterized dimensions set according to the structural characteristics, and the range of values is shown in Table 2. The lower box cover in the anchor transmission device bears the gravity load of components such as gear transmission pairs and upper box covers, so it is necessary to consider the prestressing situation and conduct coupled modal analysis on it. Establish a static structural analysis module in ANSYS Workbench, and then couple the modal analysis module with the structural analysis module. In the preprocessing stage, the material attribute of the model is defined as Q235 in the material library, and then the quality parameter is set as the optimization objective, code P5. For grid partitioning, an adaptive type is adopted, with a grid resolution level of 7. Slow mode is used for transitions between different planes, and medium mode is used for the center of the span angle. The final result is 55273 units and 105275 nodes. The grid partitioning result is shown in Fig. 5.
Fig. 5Model and parameterized dimensions
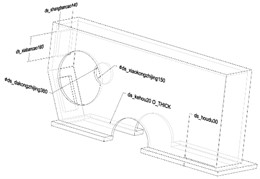
Fig. 6The results of finite element mesh division
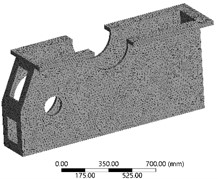
Through optimization and refinement verification of the grid, it is shown that this grid partitioning method can achieve high accuracy and computational efficiency. The bottom surface of the box is defined as a fixed constraint, with a gravity load of 9130 N set on the upper end face and a torque of 4.77 e7 N·mm set at the motor transmission position during normal operation. The final static strength and first order vibration mode analysis results are shown in Fig. 6 and Fig. 7, respectively. It can be seen that the maximum stress of the lower box is only 29.84 MPa, with the code set as P6. The first natural frequency obtained under prestressed conditions is 86.93 Hz, and the maximum relative deformation position is located near the bearing seat. In the post-processing module, set the first natural frequency as the optimization objective and define it as P7.
Table 2Size variable value range
Parameterized dimensions | Code | Initial value | Minimum value | Maximum value |
ds_houdu30 | P1 | 30 | 20 | 40 |
ds_xiaokongzhijing150 | P2 | 150 | 135 | 165 |
ds_dakongzhijing380 | P3 | 380 | 342 | 418 |
ds_kehou20_THICK | P4 | 20 | 15 | 25 |
Fig. 7Static strength analysis result
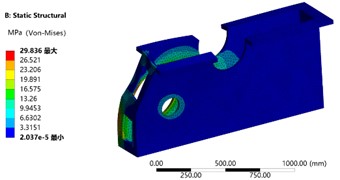
Fig. 8First order vibration mode solution result
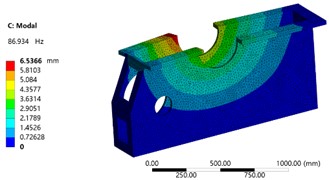
3. Lightweight based on prestressed mode
3.1. Optimization of wall frame board model
The response surface model is an approximate model, whose core idea is to create an approximate mathematical model to replace the finite element analysis model and use this approximate model for optimization design. This method can accurately approximate the function relationship within a local range through fewer experiments and is presented in simple algebraic expressions. Moreover, by selecting regression models, complex response relationships can be fitted, which has good robustness and brings great convenience to design optimization. The error between the response surface model and the actual response value is inevitable and has a decisive impact on the reliability of optimized design. To ensure the accuracy of the fitting function, it is necessary to verify the fitting accuracy. If the error is within the allowable range, it indicates that the optimization function has good feasibility. Otherwise, different experimental sample design methods need to be selected to resample the optimization variables.
Considering that the wall frame panel component is the core load-bearing part of the entire anchor machine, the safety factor is relatively high. Under the combined action of large gravity and bending moment loads, the maximum stress for static strength analysis is only 20.83 MPa. However, after the lightweight design is completed, it is still necessary to verify whether the maximum stress meets safety requirements. After completing the fitting and validation of the response surface function, it is necessary to choose a reasonable optimization algorithm to solve the extreme values of the function. In response to the requirements of lightweight design for wall frame panel components, the optimization mathematical function is defined as min (P7), and the optimization objective P9 is transformed into boundary conditions, that is, the minimum value of part mass is obtained under the premise of equivalent stiffness not less than 8.01e6 N/m. Comparative analysis of multi-objective genetic algorithm MOGA and sequence quadratic programming NLPQL yields parameter variables and target extremum values as shown in Table 3. Due to the square steel being a standard component, after rounding its thickness and side length to the nearest radius, the optimal weight loss rate is 6.4 %. Under this condition, the equivalent stiffness can remain basically unchanged, with a maximum stress of 24.35 MPa, which is much lower than the yield strength of the material, and a very high safety factor. In addition, according to the standard size requirements of square steel, the sample data can be directly calculated, and corresponding response surface functions can be constructed by discretizing the design variables P1 and P2. Through comparative verification, it can be seen that the weight reduction rate under this research scheme is 4.3 %, and the lightweight effect is not as good as the rounding method.
Table 3Lightweight results of wall frame board model
P1 / mm | P4 / mm | P5 / mm | P6 / mm | P7 / kg | P9 / (N/m) | Weight loss rate / % | P10 / MPa | |
Initial value | 8 | 140 | 140 | 40 | 680.93 | 8.01e6 | – | 20.83 |
Optimal value with NLPQL | 8 | 160 | 128.6 | 35 | 637.17 | 7.98e6 | 6.4 % | 24.35 |
Optimal value with MOGA | 8 | 150 | 134.2 | 36.4 | 651.95 | 7.95e6 | 6.1 % | 25.58 |
3.2. Optimization of box body model
Compared to the upper box cover, after completing the lightweight design of the lower box cover, it is necessary to verify whether the static strength meets safety requirements. After completing the fitting and validation of the response surface function, it is necessary to choose a reasonable optimization algorithm to solve the extreme values of the function. In response to the requirements of lightweight design for the lower box cover, the optimization mathematical function is defined as min (P5), and the optimization objective P8 is transformed into a boundary condition, that is, the minimum value of part mass is obtained under the premise of equivalent stiffness not less than 3.4e6 N/m. Comparative analysis of multi-objective genetic algorithm MOGA and sequence quadratic programming NLPQL yields parameter variables and target extremum values as shown in Table 4. It can be seen that, while ensuring the equivalent stiffness does not decrease, the NLPQL algorithm and MOGA algorithm tend to be consistent in searching for the minimum mass value, which can reduce the weight of the lower box cover by 5.9 % and have a significant lightweight effect. Through deviation verification, it can be concluded that the results obtained through the response surface function are consistent with the finite element analysis results, with a deviation of less than 0.32 %. For static strength verification, the MOGA algorithm was used to obtain the maximum stress corresponding to the design variables of 2.65e6 MPa, while the NLPQL algorithm obtained the maximum stress of 2.67e6 MPa, which is much smaller than the yield limit of the material and meets the strength requirements.
Table 4Lightweight results of box body model
Optimization algorithm | P1 / mm | P2 / mm | P3 / mm | P4 / mm | P5 / kg | P8 / (N/m) | Weight loss rate / % |
Initial value | 30 | 150 | 380 | 20 | 445.95 | 3.4e6 | / |
Optimal value with NLPQL | 20 | 153.1 | 418 | 20.1 | 419.43 | 3.4e6 | 5.9 % |
Optimal value with MOGA | 20.1 | 164.1 | 411 | 20.4 | 419.51 | 3.4e6 | 5.9 % |
4. Conclusions
1) The wall frame component is the main load-bearing component in the entire anchor transmission device, and its equivalent stiffness characteristics are one of the key factors to ensure transmission accuracy, reduce wear and noise. Therefore, in lightweight research, it is necessary to take the initial equivalent stiffness as a prerequisite. The lower box cover bears the gravity load of gear transmission pairs, upper box cover and other components, so it is also necessary to consider the prestressing situation and conduct coupled modal analysis on it, with equivalent stiffness as the optimization objective.
2) Different extreme value search algorithms have been applied, and simulation results show that, without changing the original process and stiffness performance, the mass of the wall frame board and lower box body parts can be reduced by 6.4 % and 5.9 %, respectively, with significant economic benefits.
References
-
V. Nicoletti, R. Martini, L. Amico, S. Carbonari, and F. Gara, “Operational modal analysis for supporting the retrofit design of bridges,” Ce/papers, Vol. 6, No. 5, pp. 1182–1188, Sep. 2023, https://doi.org/10.1002/cepa.2125
-
M. Sohrabifard, M. Nategh, and M. Ghazavi, “Evaluation, calibration, and modal analysis for determination of contact stiffness between workpiece and components of milling fixture,” Proceedings of the Institution of Mechanical Engineers, Part B: Journal of Engineering Manufacture, Vol. 237, No. 12, pp. 1819–1835, Nov. 2022, https://doi.org/10.1177/09544054221138165
-
S. de Carolis, A. Messina, and L. Soria, “Modal analysis through response-based FRFs: Additional modes for local diagnoses,” Journal of Sound and Vibration, Vol. 549, No. 1, p. 117574, Apr. 2023, https://doi.org/10.1016/j.jsv.2023.117574
-
M. R. Zarastvand, M. H. Asadijafari, and R. Talebitooti, “Acoustic wave transmission characteristics of stiffened composite shell systems with double curvature,” Composite Structures, Vol. 292, No. 1, p. 115688, Jul. 2022, https://doi.org/10.1016/j.compstruct.2022.115688
-
R. Talebitooti, M. Zarastvand, and H. Darvishgohari, “Multi-objective optimization approach on diffuse sound transmission through poroelastic composite sandwich structure,” Journal of Sandwich Structures and Materials, Vol. 23, No. 4, pp. 1221–1252, Jun. 2019, https://doi.org/10.1177/1099636219854748
-
R. Talebitooti, H. D. Gohari, and M. R. Zarastvand, “Multi objective optimization of sound transmission across laminated composite cylindrical shell lined with porous core investigating Non-dominated Sorting Genetic Algorithm,” Aerospace Science and Technology, Vol. 69, No. 1, pp. 269–280, Oct. 2017, https://doi.org/10.1016/j.ast.2017.06.008
-
I. Aarab, K. E. Amari, A. Yaacoubi, A. Etahiri, and A. Baçaoui, “Optimization of the flotation of low-grade phosphate ore using DOE: a comparative evaluation of fatty acid formulation to sodium oleate,” Mining, Metallurgy and Exploration, Vol. 40, No. 1, pp. 95–108, Dec. 2022, https://doi.org/10.1007/s42461-022-00706-w
-
H. D. Chalak, A. M. Zenkour, and A. Garg, “Free vibration and modal stress analysis of FG-CNTRC beams under hygrothermal conditions using zigzag theory,” Mechanics Based Design of Structures and Machines, Vol. 51, No. 8, pp. 4709–4730, Aug. 2023, https://doi.org/10.1080/15397734.2021.1977659
-
X. Yin, Z. Huang, and Y. Liu, “Damage features extraction of prestressed near-surface mounted CFRP beams based on tunable Q-factor wavelet transform and improved variational modal decomposition,” Structures, Vol. 45, No. 1, pp. 1949–1961, Nov. 2022, https://doi.org/10.1016/j.istruc.2022.10.036
-
R. K. Bhamu, A. Shukla, S. C. Sharma, and S. P. Harsha, “Vibration response of steam turbine healthy and cracked blade under the stress stiffening and spin softening effects,” Proceedings of the Institution of Mechanical Engineers, Part K: Journal of Multi-body Dynamics, Vol. 236, No. 2, pp. 224–243, Feb. 2022, https://doi.org/10.1177/14644193221078656
-
A. Daşdemir, “A modal analysis of forced vibration of a piezoelectric plate with initial stress by the finite-element simulation,” Mechanics of Composite Materials, Vol. 58, No. 1, pp. 69–80, Mar. 2022, https://doi.org/10.1007/s11029-022-10012-7
-
J. Cui, Y. Peng, J. Sun, and B. Li, “Multi-modal stress characteristics under coupling effect of strip and work roll,” International Journal of Precision Engineering and Manufacturing, Vol. 22, No. 10, pp. 1719–1733, Aug. 2021, https://doi.org/10.1007/s12541-021-00559-1
About this article
The authors have not disclosed any funding.
The datasets generated during and/or analyzed during the current study are available from the corresponding author on reasonable request.
The authors declare that they have no conflict of interest.