Abstract
The article presents a method for improving the control system of electric motors driving the electrodes of high-voltage arc furnaces. The developed method today in the field of metallurgy is of great importance in solving problems such as at the first stage of melting and casting metal in arc steelmaking furnaces, when the electrodes are initially lowered into the working bath, the connection point breaks as a result of contact with a metal plate, the incompatibility of the formation of an electric arc on the electrodes, holding the electrodes at a certain distance from the metal charge. Also, automatic control of the speed of movement of the electrodes, i.e. (the time of formation of an electric arc in the electrodes, which reduces the speed of its movement, the time of lifting the electrodes, lowering, increasing the speed of movement), is relevant for solving problems such as welding electrodes into a metal shackle. The main purpose of introducing this method into practice is to reduce electricity consumption and ensure reliable operation of high-voltage electric arc furnaces by reducing the melting time of metal.
1. Introduction
Currently, high-voltage electric arc furnaces are widely used in developed countries of the world for melting and casting various metals, heating them to the desired temperature. Also, high-voltage electric arc furnaces are the most numerous consumers of electricity in the metallurgical industry. Currently, the annual electricity consumption of the Navoi Machine-Building Plant is 75 million kWh. At the same time, more than 80 % of the total electricity consumption is accounted for by high-voltage electric arc steelmaking furnaces (Fig. 1).
Fig. 1Indicators of the distribution of annual electricity consumption by the Navoi Machine-Building Plant
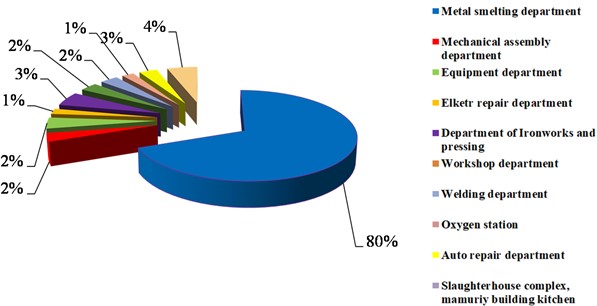
In high-voltage electric arc furnaces at the first stage of melting, the high-speed movement of the electrodes and the mechanical movement of the electrode are negatively affected by the following factors:
– Moving the electrodes in a complete position (electrode with handles).
– When the electrode touches the metal charge, the data values of the measuring transformer change dramatically.
– The higher the impact force of the electrode, the more likely it is that the electrode will break at the junction point [1].
In the electrode control system of high-voltage electric arc furnaces, in order to eliminate the above disadvantages, it is advisable to improve the auxiliary control system of the automatic control power regulator.
Table 1Physical and mechanical properties of graphite electrodes
Properties | Diameter of the electrode, mm | |
To 300 | Up to 300 | |
Mechanical compressive strength, kg/сm2 | 250-300 | 180-250 |
Electrical resistivity, Om mm2/m | 8-9 | 10-11 |
True specific gravity, g/сm3 | 2,21-2,22 | 2,20-2,21 |
Volumetric specific gravity, g/сm3 | 1,58-1,67 | 1,53-1,58 |
Porosity, % | 25-28 | 26-30 |
Ash content, % | 0,10 -1,50 | 0,10 -1,50 |
Permissible current density, А/сm2 | 20-30 | 13,8-30 |
On graphite electrodes, the formation of an electric arc occurs faster than on carbon electrodes, since graphite electrodes have the property of spontaneous combustion (self-igniting). The main working part of high-voltage electric arc furnaces are its electrodes (Fig. 2).
Fig. 2 shows that graphite electrodes with a diameter of 300 mm are used in high-voltage electric arc furnaces of the Navoi Machine-Building Plant. The electrodes are placed in special electrode holders at an angle of 120° to each other in a position where several electrodes are attached to each other, which ensures high furnace performance [3]. Since these electrodes cannot be produced in Uzbekistan, they are imported from the People's Republic of China, so their cost will be high.
Currently, the design diagram of high-voltage electric arc furnaces operating at the Navoi Machine-building Plant (Fig. 3).
Fig. 2The appearance of the electrodes
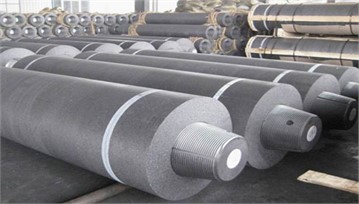
Fig. 3Functional diagram of high voltage electric arc furnaces [2]
![Functional diagram of high voltage electric arc furnaces [2]](https://static-01.extrica.com/articles/23995/23995-img3.jpg)
In high-voltage electric arc furnaces, at the first stage of metal melting and casting, the molten metal is first loaded into a working bath. Then the electrodes are lowered from the top of the furnace into the working bath. The high voltage from the furnace transformer is transmitted to the electrodes via a cable line. Measuring (current and voltage) transformers 1, are connected to a high-voltage line [4]. The frequency converter 2, is used to control the speed of the electric motor. The electric motor 3, converts electrical energy into mechanical energy and transmits it to the converter of the manual transmission. The conversion of the rotational motion of the electric motor into a linear one is carried out using a mechanical gearbox 4. The mechanism of moving the electrode may also include the capture of the electrode 5, the function of which is to hold the graphite electrode 6. An electric arc 7, is formed between the graphite electrodes and the metal charge, 8. The working bath 9, is specially lined with refractory bricks.
An oscillogram of the analysis of a metal charge melting in high-voltage electric arc furnaces of the Navoi Machine-Building Plant with different densities is shown in (Fig. 4).
Fig. 4Oscillograms of electrode motion at electrode voltage and resistance moment
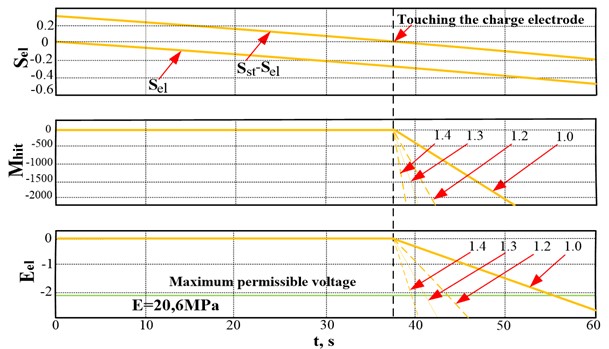
Fig. 4 shows an oscillogram of high-voltage electric arc furnaces with electrode movement in 3 different positions. The period during which the electrode touches the metal charge is described in the acylogram above. At the first stage of melting, the difference between the signal of the electrode movement and the signal of its initial state is indicated until the electrode reaches the metal surface and touches it [5]. Since this does not take into account any restrictions on the movement of the electrode, it slows down at the same speed for 37 seconds (position 1).
Fig. 5The oscillogram of the electrode movement at different speeds at the moment of resistance
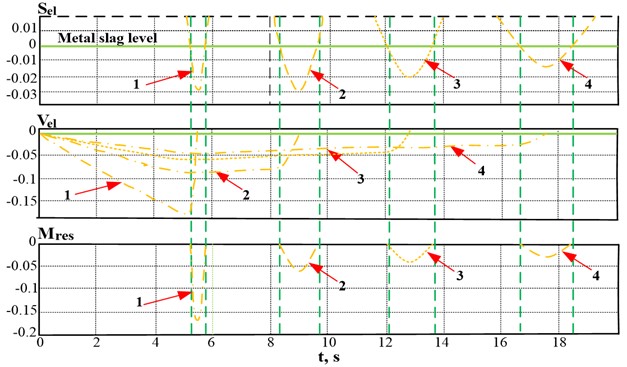
To compare the models, the maximum allowable electrode voltage at a pressure of 20.3 MPa was established. Thus, it follows that intersections with the line of the maximum allowable voltage at the moment will be important points for maintaining the mechanical integrity of the electrode [6]. In addition, the electrodes cannot operate below the maximum permissible voltage line, which will necessarily lead to electrode failure. It is not recommended to work near the maximum permissible voltage line (Fig. 5).
From the oscillograms, we see that the more electric motors can control the movement, the higher the speed of movement of the electrode, which leads to a deeper immersion of the electrode into the metal rod. Movement below the maximum allowable voltage line causes the electrode to break off from the junction point [7].
2. Results and discussion
The electromechanical power regulator has several advantages: the time during which the electrode directly touches the metal charge slows down the electric motor, preventing the electrode from sinking deeper into the metal charge [8]. Appearance in case of application of an electromechanical power regulator to high-voltage electric arc furnaces operating at the Navoi Machine-building Plant (Fig. 6).
Fig. 6Functional diagram of the power regulator of high voltage electric arc furnaces [2]
![Functional diagram of the power regulator of high voltage electric arc furnaces [2]](https://static-01.extrica.com/articles/23995/23995-img6.jpg)
In high-voltage electric arc furnaces, at the first stage of metal melting and casting, the technological parameters of the melting metal are entered into the automatic control unit. Data from measuring transformers (current and voltage) are processed in an automatic control department. The processed data is usually sent to the controller in the form of a 0-20 mA current signal or a 0-10 V voltage signal. According to the algorithm programmed by the controller used, a command signal is generated for the electric motor, and then the electric motor drives the electrode.
The electromechanical power regulator has an additional brake block mounted on the shaft of the electric motor, which allows you to limit the speed of movement of the electrode upon impact [9]. And the acceleration sensor helps to reduce the downtime of the furnace, bring the speed of the electrode to 6 m/s. An oscillogram of the mechanical voltage at the electrode when using acceleration sensors and an additional mechanical brake on the motor shaft at a density of molten metal charge of 1.3 t/m3 in high-voltage electric arc furnaces (Fig. 7).
Fig. 7Electrode braking when using an electromechanical power regulator
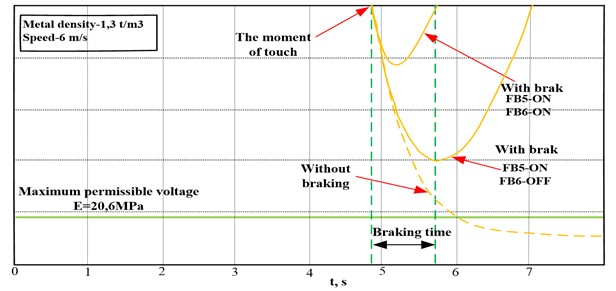
The above oscillogram shows the signals at the output of the acceleration sensor (FB5) and an additional braking sensor (FB6) mounted on the axis of an electric motor driving the electrodes using an electromechanical power regulator, the results were obtained in 3 different states using a virtual scope oscilloscope.
In position 1, the time during which the electrode touches the metal gasket slows down the movement of the electrode by about 1 second.
In position 2, the time the electrode touches the metal charge slows down the movement of the electrode for about 2 seconds.
In position 3, the time the electrode touches the metal gasket slows down the movement of the electrode for the 4th second. The operation of the electrode below the maximum permissible voltage line leads to their breakage at the junction point [10].
An oscillogram of the results of using an electromechanical power regulator in high-voltage electric arc furnaces with use of a mechanical braking sensor and an acceleration sensor (Fig. 8).
Fig. 8Determination of the optimal braking mode
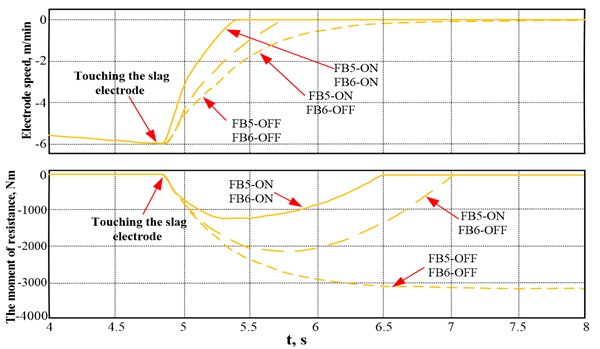
The velocity of the electrode in 3 different positions is shown on the oscillogram above, and the movement of the electrode at the moment of resistance is shown on the oscillogram below.
In position 1 the time during which the electrode touches the metal charge slows down the movement of the electrode for about 1 second.
In position 2, the time during which the electrode touches the metal charge slows down the movement of the electrode for about 2 seconds.
In position 3, the electrode touches the metal gasket slows down the movement of the electrode for the 4th second. The faster we slow down the movement of the electrode at the moment of its contact with the metal charge, the more likely it is that the electrodes will break.
In high-voltage electric arc furnaces, the support of an electromechanical power regulator allows you to optimize the control system of electric motors, saving furnace electrodes, reducing the melting time of metals, increasing energy efficiency.
3. Conclusions
In high-voltage electric arc furnaces, the support of an electromechanical power regulator allows you to optimize the control system of electric motors, saving furnace electrodes, reducing the melting time of metals, increasing energy efficiency.
To avoid disadvantages, an additional power regulator was installed on high-voltage electric arc furnaces. Methods have been developed for welding electrodes to a metal charge, reducing the rate of electric arc formation on the electrodes, preventing electrode breakage from the junction point when the electrodes come into contact with the metal charge, as well as experimental studies and results have been obtained.
The results obtained are positive, therefore, the application of the developed method in practice will allow to avoid breakage of the electrodes of high-voltage electric arc furnaces, ensure reliable operation of the furnace, reduce melting time, increase the electric power efficiency of the furnace, as well as save electricity and resources.
References
-
V. P. Rubtsov, I. Y. Dmitriev, and A. R. Mineev, Arc Discharge Parameters and Their Effect on the Efficiency of Electrical Engineering Installations. (in Russian), Moscow, Russian: Electricity, 2000.
-
Maslov V. V., Development of Algorithms and Control Systems for Arc Steelmaking Furnaces That Reduce Electrode Breakdowns. (in Russian), 2014.
-
J. Mavlonov, D. Mardonov, M. Eshmirzayev, and I. Togayev, “Improvement of methods to ensure energy efficiency of ball mills functioning,” E3S Web of Conferences, Vol. 417, p. 03014, Aug. 2023, https://doi.org/10.1051/e3sconf/202341703014
-
V. A. Besekersky and Y. P. Popov, Management of the Theory of Automatic Systems. (in Russian), Moscow, Russian: Scientific, 1966.
-
A. D. Svenchansky and K. D. Gutterman, Automatic Regulation of Electric Furnaces. Moscow, Russian: Energy, 1965.
-
A. I. Karshibayev and Z. I. Jumayev, “Expanding the level of forecasting and operational planning of electric consumption at mining enterprise,” E3S Web of Conferences, Vol. 417, p. 03015, Aug. 2023, https://doi.org/10.1051/e3sconf/202341703015
-
B. S. Narzullayev and M. A. Eshmirzaev, “Causes of the appearance of current waves in high voltage electric arc furnaces, and methods of their reduction,” E3S Web of Conferences, Vol. 417, p. 03003, Aug. 2023, https://doi.org/10.1051/e3sconf/202341703003
-
I. B. Tog’Ayev, A. A. Tursunova, and M. A. Eshmirzayev, “Center of science and enlightenment,” Problems and scientific solutions, Vol. 4, No. 3, pp. 285–287, 2022.
-
A. I. Qarshibaev and B. Sh. Narzullaev, “Diagnostics of the technical condition of energy devices based on the monitoring of phase voltages and currents,” Journal of Pharmaceutical Negative Results, Vol. 5, No. 2, pp. 5–7, 2022.
-
A. Tovbaev, G. Boynazarov, and I. Togaev, “Improving the quality of electricity using the application of reactive power sources,” E3S Web of Conferences, Vol. 390, p. 06032, Jun. 2023, https://doi.org/10.1051/e3sconf/202339006032
About this article
The authors have not disclosed any funding.
The datasets generated during and/or analyzed during the current study are available from the corresponding author on reasonable request.
The authors declare that they have no conflict of interest.