Abstract
The vibrations induced by moving trains especially in close distances with high-rise buildings can be destructive. The high technology of wilding rails induced a high train velocity which is associated with high vibrations. The buildings near the railways suffer from the train-induced vibrations. In this paper, a 3D FEM model was constructed to study the train-induced vibrations on a nearby high-rise building (HRB), show its response and investigate the most suitable technique to mitigate the effect of the train-induced vibrations by an open trench or a geofoam-filled trench. Three trench parameters were investigated to enhance the mitigation performance, the distance from the trench to the HRB, the trench depth and the use of either open (empty) trench or geofoam-filled trench. The geofoam-filled trench technique improved the dynamic response of the structure. Thus, trenches filled with geofoam can be considered a protection technique for high-rise buildings constructed near moving trains.
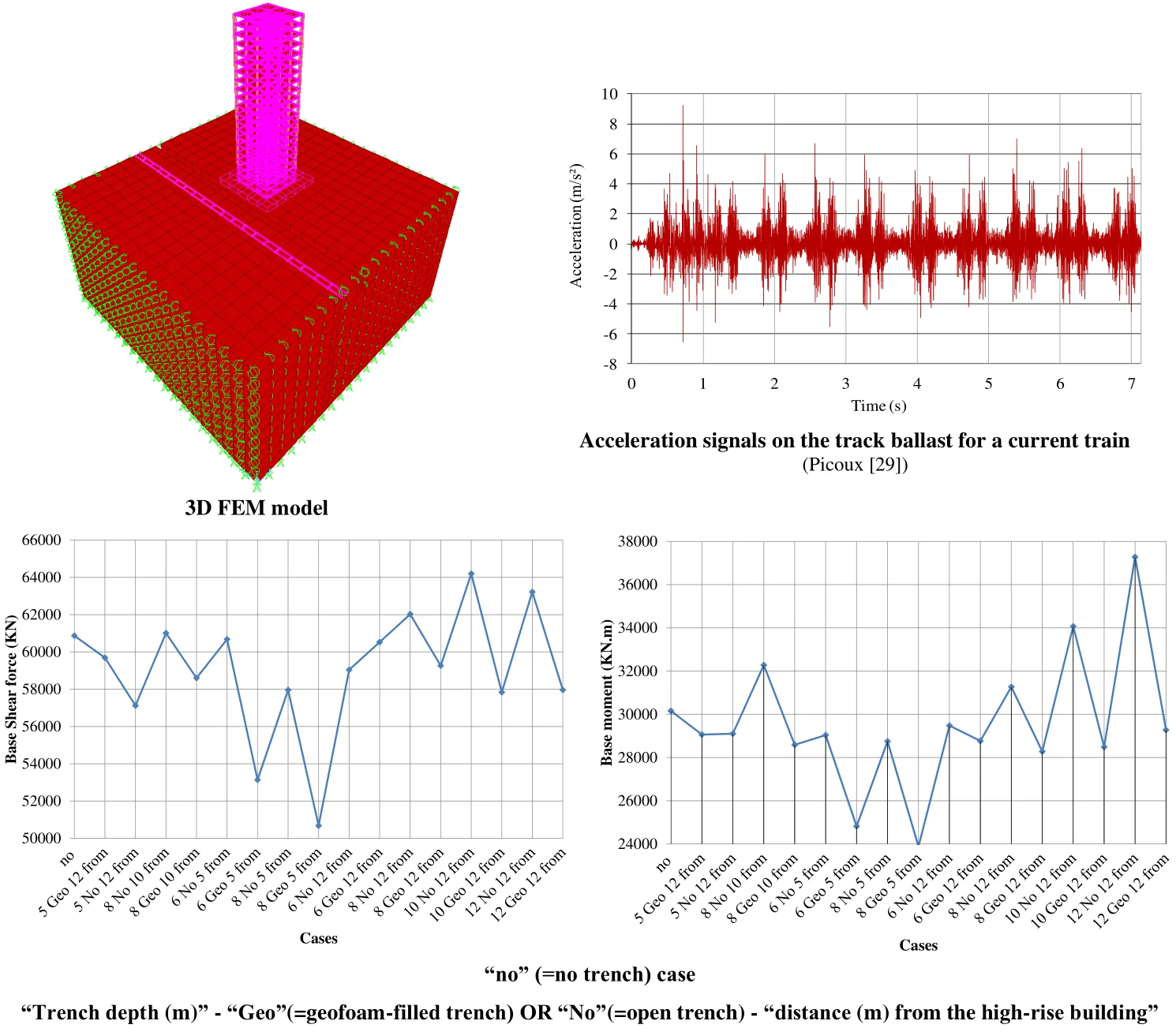
Highlights
- The train-induced vibrations on nearby high-rise buildings are mitigated by open or geofoam-filled trenches.
- The efficiency of vibration mitigation depends on the depth of the trench.
- The distance between the high-rise building and the trench is a very effective factor.
- A trench filled with geofoam is much more effective than an open (empty) trench.
- The depth and location of the trench should be studied individually for each high-rise building.
- Geofoam-filled trenches can successfully protect high-rise buildings constructed near railway tracks of moving trains.
1. Introduction
Overpopulation and rare construction land led to the construction close to the railway lines; also, overpopulation led to vertical expansion resulting in high-rise buildings (HRBs) which have a complex response for different kinds of vibrations especially those induced by moving trains near them. The effect of repeated vibrations from the trains passing near HRBs may affect the survival of such structures as a destructive factor. The distance between the high-rise building and the railway is the most effective factor which may affect the values of vibrations up to the structure. The soil is the most effective component in the system of transient vibrations from the railways to the buildings. The techniques to protect the buildings from the danger of vibrations induced by moving trains varies for each kind of building. The most famous techniques are the open and the filled trenches which are easy to implement and cheap.
In this paper the Finite Element Method (FEM) is employed, however, some authors have analytically addressed the soil-structure interaction problem under vibration, e.g. Ahmadi and Eskandari [1], Dai et al. [2], Zhang and Pan [3], etc.
Celebi et al. [4] studied experimentally the isolation of foundations of buildings near a moving load by using open or in-filled trench barriers, found that the dimensions of the trenches should be studied for each building as an individual case, and concluded that the reduction effects of wave barriers depend on the frequency of vibration source for both passive and active isolation cases.
Galvín et al. [5] studied the effects of vibrations induced by high-speed train (HST) passage on ballast and non-ballast tracks and also studied the floating slab track case and concluded that the critical speed for a ballast track is close to the Rayleigh wave velocity in the soil and that the system of floating slab gives higher vibrations than the slab system at the track.
Connolly et al. [6] developed a 3D FEM model with all components (soil-train-building) to study the vibrations of high-speed trains on a nearby building and to investigate the use of embankments as a method to reduce the train vibration effect on the building. It is found that soft embankments increased the vibration levels both inside the embankment and in the surrounding soil; in contrast, it is found that embankments formed from stiff material reduce vibrations at all distances from the rail track.
Farghaly [7] used a 3D building and soil model to study the seismic response of a high-rise building near existing deep channels and found that the horizontal and vertical displacements, shear forces, axial forces and bending moments induced in the HRB near the excavated channels, highly depend on the shape of the channels, earthquake direction and foundation type.
Saikia [8] investigated the vibration screening effectiveness of dual in-filled trenches where the in-fill trench material is softer and found that such an isolation scheme is advantageous when a single trench requires unrealistic depth.
Sanayei et al. [9] studied experimentally the mitigation of passing train near the buildings by an impedance method (thickened “blocking floor” method) and verified that method by field measurements.
Hasheminezhad [10] studied numerically the mitigation of railway-induced vibrations using in-filled trenches with pipes. The results indicate that in-filled trenches with steel pipes are much more effective than in-filled trenches with concrete pipes. Moreover, filling pipes with loose sand and clay does not have any effect on vibration reduction efficiency.
Kouroussis et al. [11] reviewed and summarized the standards and limits of vibrations induced from railway trains and applied these results to a particular building.
Kouroussis et al. [12] studied a full 3D FEA model with a viscous boundary to predict the ground excitation induced from a moving tram near a building.
Connolly et al. [13] reviewed the train vibrations and their effect on the passenger comfort, rail track and the near buildings with discussing the most effective modeling for this processing.
Zoccali et al. [14] mitigated the vibrations of moving trains by trenches and found that by increasing trenches length, a better isolation effect is performed, but the improvement amount seems to be strongly influenced by the kind of material to be used to fill trenches.
Cacciola and Tombari [15] proposed a vibrating barrier buried in the soil to reduce the vibrations of adjacent structures subjected to ground motion waves, investigated numerically and experimentally its efficiency and noted a significant reduction in the maximum structural acceleration of 87 %.
Ulgen and Toygar [16] studied the isolation effectiveness of open, water filled, and geofoam filled trenches and investigated the effects of frequency, Rayleigh wavelength and trench depth and confirmed that the geofoam filled trench can be used as an efficient wave barrier.
Hesami et al. [17] employed a 2D FEA for modeling of the train movement and its effect on the nearby building and showed that the vibrations increased by increasing the speed of the train and decreased by decreasing the speed of the train while the distance between the railway and the building affects the values of vibrations and proposed a distance of 18m.
Kouroussis et al. [18] presented a combined experimental and numerical study into high-speed rail vibrations for tracks on three types of support: a cutting, an embankment and an at-grade section and found that the embankment profile generates lower vibration levels in comparison to the cutting and at-grade cases.
Persson et al. [19] numerically investigated the reduction in traffic-induced ground vibrations by using barriers and found that the depth of a trench and the elastic modulus of a solid back-fill material are the most important parameters to consider, while the infiltration of water decreases the achieved reduction. They also found that vibration amplification occurs at long distances from the vibration source.
Connolly et al. [20] analyzed a collection of technical ground-borne noise and vibration reports at 1604 various railway track sections, in 9 countries and found that velocity decibels, vibration dose value and peak particle velocity are the most commonly used methods of assessment while the most commonly used abatement strategy is a modification of the rail track structure (active mitigation), rather than the implementation of a passive solution.
Thompson et al. [21] considers the trench as a barrier to ground vibration and is a potential mitigation measure for frequency vibration induced by surface railways. They concluded that the rectangular open trench performs best, the depth is the most important parameter whereas the width has only a small influence on its performance, and that barriers consisting of a soft fill material are shown to be much less effective than an open trench.
Kouroussis et al. [22] presented a hybrid experimental-numerical approach that can predict vibration levels in the presence of a variety of railroad artefacts such as transition zones, switches, crossings and rail joints and can account for railway discontinuities while incorporates the uncertainties related with different soil configurations.
Feng et al. [23] used a 3D FEM model to simulate the high-speed train (HST) vibration and concluded that the subgrade structures must be taken into consideration for reducing the effect of the vibrations of HST.
Farghaly and Kontoni [24] studied the train-induced dynamic response of a pedestrian tunnel under a four-track surface railway for different soil water contents, by 3D FEM modeling of the tunnel and the soil block around it.
Xu et al. [25] introduced a new method to monitor the buildings next railway to calculate the vibrations induce from moving trains and improved that method agreed with the field measurements by 93 % in positive rate and 80 % negative rate.
Bose et al. [26] investigated the use of trenches to mitigating ground vibration caused by the propagation of surface waves by using a FEM software. They found that for open trenches, the normalized depth is the decisive factor and the trench width did not play a very important role except in extremely shallow trenches. They also studied the effectiveness of geofoam trench barriers in damping out the vibrations generated by a moving train and the geofoam barrier efficiency was shown to increase with increasing train speed.
In this paper, a 3D FEM model was constructed to show the effect of a moving train’s vibrations near a high-rise building (HRB) and how traditional techniques like an open trench or a geofoam-filled trench can be relied upon to mitigate the effects of vibrations resulting from the movement of trains near the HRBs. The different variables used to investigate the open or geofoam-filled trench techniques were the depth of the trench and the distance between the trench and the high-rise building.
2. Model description
A 3D model is created to show the effect of the vibrations of a current train moving near a RC HRB of 20 floors and investigate the use of a trench as a solution to resist such train-induced vibrations. The SAP2000 [27] finite element program was used to analyze this model. The soil mass block was modeled as solid elements, the dimensions of the soil block equal to 100 m length, 100 m width and 50 m depth, the boundary conditions of the soil block on the sides of the block are roller supports to enable the model to move in the vertical direction and hinged supports in the base of the model representing the base rock of the model. The RC HRB with height 60 m (where the height of each floor is 3 m) and plan dimensions 15×15 m as shown in Fig. 1, was created from columns with constant square cross-sections of 700×700 mm, with reinforcements 36#18 mm (steel grade St52), modeled as frame elements; the slabs are modeled as shell elements with constant thickness of 120 mm, one mesh reinforcement 7#12 mm/m’; and the foundation (6 m under the ground level) is modeled as shell elements with constant thickness equal to 2500 mm with upper and lower mesh steel bars reinforcements 7#22 mm/m’.
The structure consists of a frame system with the properties of building elements as shown in Table 1. Table 2 shows the properties of the single soil layer under the railway track and the building. Table 3 shows the properties of the Geofoam (InsulFoam GeoFoam EPS22 [28]), used in this study as an in-fill material of the filled trenches.
The loads used in this study are the own weight of the elements and live loads equal to 2 kN/m2 on the slab levels, and the distributed loads on the beams lines equal to 4 kN/m, while the vibration loads result from the moving train and the moving train acceleration is shown in Fig. 2(a) (Picoux [29]).
Table 1Properties of the building
Model | EA (kN/m) | EI (kN.m2/m) | Unit weight per length (kN/m/m) | Poisson’s ratio () |
Elastic | 1.18x107 | 2.329x106 | 12 | 0.1 |
Table 2Properties of the soil layer
Soil thickness (m) | Unit weight (kN/m3) | Poisson’s ratio () | Elastic modulus (kN/m2) |
50 | 20 | 0.38 | 5000 |
Table 3Properties of the Geofoam material (InsulFoam GeoFoam EPS22) [28]
Type – ASTM D6817 | Units | EPS22 |
Density | kg/m3 | 21.6 |
Compressive resistance (1 % deformation) | kPa | 50 |
Compressive resistance (5 % deformation) | kPa | 115 |
Compressive strength (10 % deformation) | kPa | 135 |
Flexural strength (min) | kPa | 276 |
Oxygen index (min) | Volume % | 24.0 |
Dimensional stability | Max. % | < 2 % |
Buoyancy force | kg/m3 | 980 |
Poisson’s ratio | – | 0.05 |
Coefficient of friction | – | 0.6 |
Absorption | Volume % | < 4.0 |
Elastic modulus (min) | kPa | 5000 |
Fig. 1Model description
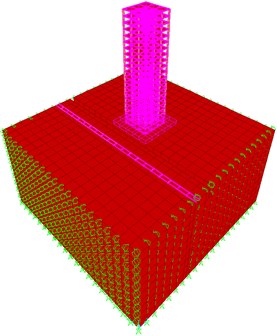
a) 3D model
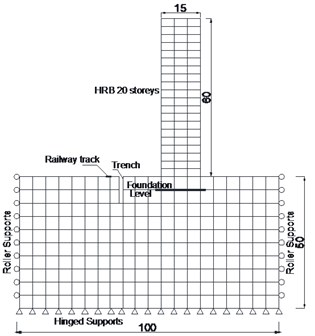
b) A simple 2D cross section of the model
3. Moving train accelerogram
Picoux [29], and Picoux and Le Houédec [30] in order to diagnose and predict the vibration from railway trains near the track, successfully developed a prediction model and also performed in situ measurements with the aim of the validation of their proposed model.
A real accelerogram of a moving train is presented in Fig. 2(a) (Picoux [29]). The measurements for 7 secs of the acceleration signals were on track ballast for a current train (heavy locomotive and many current carriages) moving at 135 km/h (Picoux [29]). The vertical displacement spectrum (m/Hz) calculated by double integration and Fourier transform is shown in Fig. 2(b) (Picoux [29]).
Fig. 2Measurements on the track ballast for a current train (Picoux [29])
![Measurements on the track ballast for a current train (Picoux [29])](https://static-01.extrica.com/articles/20523/20523-img3.jpg)
a) Acceleration signals for a train
![Measurements on the track ballast for a current train (Picoux [29])](https://static-01.extrica.com/articles/20523/20523-img4.jpg)
b) Vertical displacement spectrum
4. Results and discussions
An empty open trench or a trench filled with geofoam is investigated as a solution to isolate the high-rise building (HRB) from the vibrations resulting from the nearby moving train. Herein the distance between the HRB and the center of the rail track is taken as 20 m. In this study, various trench depths were tested (5 m, 6 m, 8 m, 10 m, 12 m) while the width of the trench was 1m in all cases. Moreover, different distances between the trench and the building (5 m, 10 m, 12 m) were examined. The response of the HRB is represented by the lateral displacements, top acceleration, base shear force, base moment, and base axial force.
Fig. 3 shows the lateral displacements (along the height) of the HRB model subjected to moving train vibrations with different trench techniques to mitigate these vibration waves.
Fig. 3(a) represents the lateral displacements of the HRB model subjected to train vibration for different trench mitigation cases; in general all trench mitigation cases including the “no” (i.e., “no trench”) case show distortion (oscillation) of the lateral displacements along the floors whereas the lateral displacements are similar for different floors as the 8th and 14th in the same direction; the reason for these distortions is the vibration wave of the train specially for the narrow pulses of this wave, with no clear trend in these displacements which change their direction along floors, but it may be said that the most clear trend appears in the “8 Geo 10 from” case (i.e., “Geofoam-filled trench of depth 8 m with 10 m distance from the HRB”), and some cases like the “6 No 5 from” (i.e., “open trench of depth 6 m with 5 m distance from the HRB”) amplify the magnitude of the lateral displacements by 1.75 times than the “no” case.
Fig. 3(b) displays the rest trench cases used to mitigate the vibration effect of the moving train near the HRB model; all trench cases show distortion of the lateral displacements along the height of this HRB model, the cases of the “10 Geo 12 from” and “12 Geo 12 from” show the most regular lateral displacements and the lowest one between all cases, all top displacements of these two cases decrease than the “no” case by nearly 1.25 times, while some cases like the “12 No 12 from” amplify the magnitude of the lateral displacements by 2 times than the “no” trench case. As a result of the shape and intensity of the vibration wave of the train movement, the lateral displacements of the HRB model are formed in a manner different from the lateral displacements of the HRB model when exposed to a seismic wave. This explains the oscillation shape of the lateral displacements of the HRB model under the influence of the vibration of the moving train.
Fig. 3Lateral displacements of the HRB model for different trench cases
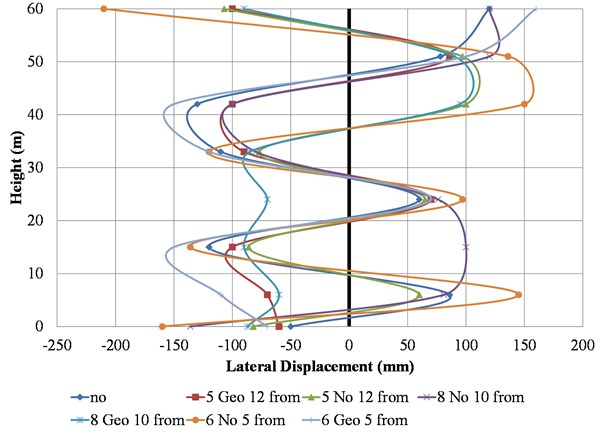
a)
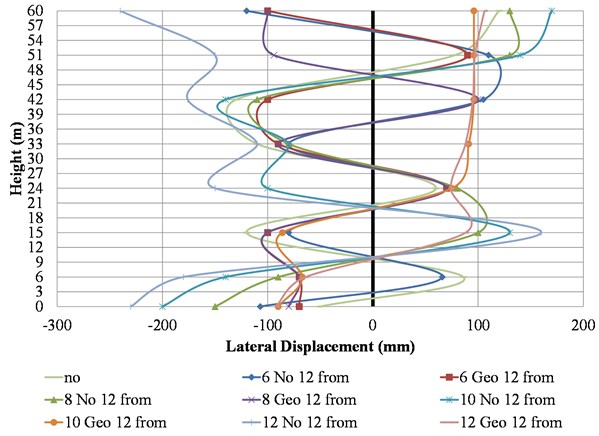
b)
Fig. 4 shows the top lateral displacement of the HRB model for the different trench techniques tested to mitigate the train-induced vibration; the highest top lateral displacement appears in the “12 No 12 from” case, while the lowest lateral displacements appear in the “8 Geo 10 from” and “10 Geo 12 from” cases.
Fig. 5 shows the top acceleration of the HRB model for the different trench techniques tested to mitigate the train-induced vibration; the highest top accelerations appear in the following cases: “6 Geo 5 from”, “8 No 5 from” and “8 Geo 5 from” (more than the “no” case by nearly 1.2, 1.1 and 1.15 times respectively), while the lowest acceleration appears in the “12 No 12 from” case (which corresponds to the highest horizontal displacement.)
Fig. 4Top lateral displacement of the HRB model for different trench cases
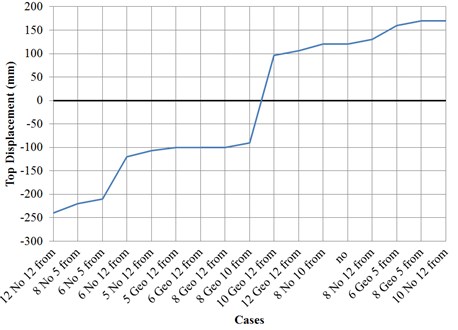
Fig. 5Top acceleration of the HRB model for different trench cases
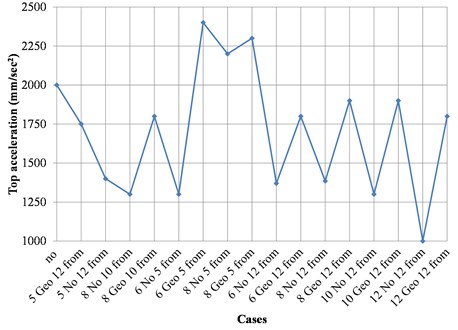
Fig. 6 shows the base shear force of the HRB model for the different trench cases tested to mitigate the train-induced vibration; the minimum base shear appears in the “8 Geo 5 from” and “6 Geo 5 from” cases which is lowest than “no” case by 1.2 and 1.14 times respectively, while the rest of cases have oscillating values around the “no” case base shear values.
Fig. 7 shows the base bending moments of the HRB model for the different trench cases tested to mitigate the train-induced vibration; the minimum base bending moment appears in the “8 Geo 5 from” and “6 Geo 5 from” cases (which are lowest than the “no” case by 1.25 and 1.21 times respectively), the “12 No 12 from” case increases by 1.24 times than the “no” case and the “10 No 12 from” case increases by 1.13 times than the “no” case, while the rest cases have oscillating values around the “no” case base bending moment values.
Fig. 8 shows the base axial force of the HRB model for the different trench cases tested to mitigate the train-induced vibration; the minimum base axial force appears in the “12 No 12 from” case which is lower than the “no” case by about 1.04 times, while the rest cases have oscillating values around the “no” case.
Fig. 6Base shear force of the HRB model for different trench cases
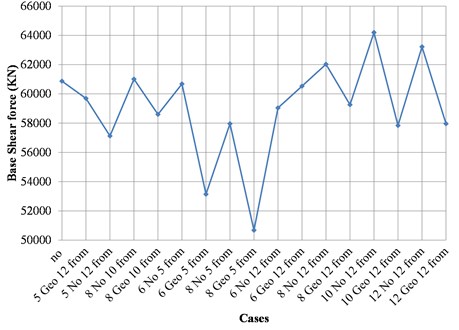
Fig. 7Base bending moment of the HRB model for different trench cases
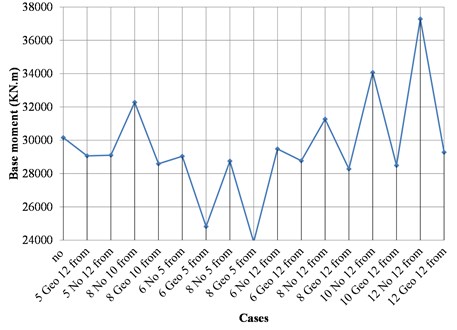
Fig. 8Base axial force of the HRB model for different trench cases
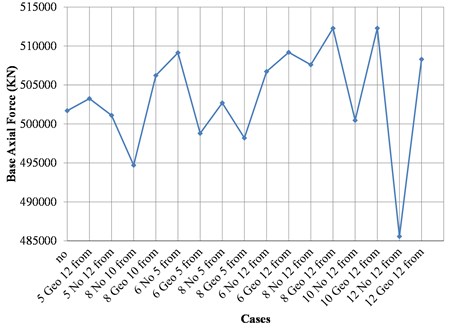
5. Conclusions
A 3D soil block and HRB model subjected to train-induced vibration with different vibration mitigation trench techniques are analyzed to stand on the best mitigation trench technique that can help in improving the performance of the HRB during its exposure to the vibrations of a current train passing near it. The most low-cost technique is used by constructing an open trench between the train track and the HRB, and in order to improve the trench mitigation performance, the trench is filled with geofoam material. Three trench parameters are investigated to enhance the mitigation performance, the distance from the trench to the HRB, the trench depth and the use of either open (empty) trench or geofoam-filled trench. The lateral displacements, top acceleration, base shear force, base bending moment and axial force are measured to judge the performance of each used technique; from the presented results the following conclusions can be drawn out:
1) Trenches can be a successful technique to mitigate the vibrations induced by moving trains.
2) The train-induced vibration wave had an outstanding effect in the shape of the lateral displacements of the HRB with a distortion phenomenon. As a result of the shape and intensity of the vibration wave of the train movement, the lateral displacements of the HRB model respond in a manner different from the lateral displacements of the HRB model when exposed to a seismic wave.
3) The base shear force recorded the minimum value in the “8 Geo 5 from” case, where the base shear was reduced by 1.2 times than the “no” case.
4) The base bending moment recorded the minimum value in the “8 Geo 5 from” case, where the base bending moment was reduced by 1.25 times than the “no” case.
5) The base axial force recorded equal values in the “8 Geo 5” with the “no” case, however, the minimum value “12 No 12 from” case gives base axial force less than the “no” case by 1.04 times.
6) The trenches filled with geofoam are considered a protection technique for high-rise buildings constructed near railway tracks of moving trains.
7) The efficiency of vibration mitigation increases with the depth of the trench which was seemed to be a very important parameter on screening vibrations.
8) The distance between the HRB and the trench is a very effective factor which affects the values of vibrations up to the structure.
9) The location of the trench (i.e., distance from the HRB) and the trench depth should be studied for each HRB as an individual case and the reduction effects of the trenches depend on the frequency of vibration source.
10) A trench filled with geofoam is much more effective than an open trench. However, the geofoam-filled trenches are vulnerable and reduce performance under flood condition.
References
-
Ahmadi S. F., Eskandari M. Vibration analysis of a rigid circular disk embedded in a transversely isotropic solid. Journal of Engineering Mechanics, Vol. 140, Issue 7, 2014, p. 04014048.
-
Dai D., El Naggar M. H., Zhang N., Gao Y., Li Z. Vertical vibration of a pile embedded in radially disturbed viscoelastic soil considering the three-dimensional nature of soil. Computers and Geotechnics, Vol. 111, 2019, p. 172-180.
-
Zhang Z., Pan E. Vertical and torsional vibrations of an embedded rigid circular disc in a transversely isotropic multilayered half-space. Engineering Analysis with Boundary Elements, Vol. 99, 2019, p. 157-168.
-
Celebi E., Fırat S., Beyhan G., Cankaya I., Vural I., Kirtel O. Field experiments on wave propagation and vibration isolation by using wave barriers. Soil Dynamics and Earthquake Engineering, Vol. 29, Issue 5, 2009, p. 824-833.
-
Galvín P., Romero A., Domínguez J. Vibrations induced by HST passage on ballast and non-ballast tracks. Soil Dynamics and Earthquake Engineering, Vol. 30, Issue 9, 2010, p. 862-873.
-
Connolly D., Giannopoulos A., Forde M. C. Numerical modelling of ground borne vibrations from high speed rail lines on embankments. Soil Dynamics and Earthquake Engineering, Vol. 46, 2013, p. 13-19.
-
Farghaly A. A. Seismic analysis of high rise building with deep foundation constructed near deep channel. Electronic Journal of Geotechnical Engineering, Vol. 19, 2014, p. 3099-3124.
-
Saikia A. Numerical study on screening of surface waves using a pair of softer backfilled trenches. Soil Dynamics and Earthquake Engineering, Vol. 65, 2014, p. 206-213.
-
Sanayei M., Kayiparambil P. A., Moore J. A., Brett C. R. Measurement and prediction of train-induced vibrations in a full-scale building. Engineering Structures, Vol. 77, 2014, p. 119-128.
-
Hasheminezhad A. Reduction of Railway-induced Vibration using In-filled Trenches with Pipes. IJR International Journal of Railway, The Korean Society for Railway, Vol. 7, Issue 1, 2014, p. 16-23.
-
Kouroussis G., Conti C., Verlinden O. Building vibrations induced by human activities: a benchmark of existing standards. Mechanics and Industry, Vol. 15, Issue 5, 2014, p. 345-353.
-
Kouroussis G., Van Parys L., Conti C., Verlinden O. Using three-dimensional finite element analysis in time domain to model railway-induced ground vibrations. Advances in Engineering Software, Vol. 70, 2014, p. 63-76.
-
Connolly D. P., Kouroussis G., Laghrouche O., Ho C. L., Forde M. C. Benchmarking railway vibrations – track, vehicle, ground and building effects. Construction and Building Materials, Vol. 92, 2015, p. 64-81.
-
Zoccali P., Cantisani G., Loprencipe G. Ground-vibrations induced by trains: filled trenches mitigation capacity and length influence. Construction and Building Materials, Vol. 74, 2015, p. 1-8.
-
Cacciola P., Tombari A. Vibrating barrier: a novel device for the passive control of structures under ground motion. Proceedings of the Royal Society A: Mathematical, Physical, and Engineering Sciences), Vol. 471, Issue 2179, 2015, https://doi.org/10.1098/rspa.2015.0075.
-
Ulgen D., Toygar O. Screening effectiveness of open and in-filled wave barriers: A full-scale experimental study. Construction and Building Materials, Vol. 86, 2015, p. 12-20.
-
Hesami S., Ahmadi S., Ghalesari A. T. Numerical Modeling of Train-induced Vibration of Nearby Multi-story Building: A Case Study. KSCE Journal of Civil Engineering, Vol. 20, Issue 5, 2015, p. 1701-1713.
-
Kouroussis G., Connolly D. P., Olivier B., Laghrouche O., Costa P. A. Railway cuttings and embankments: Experimental and numerical studies of ground vibration. Science of the Total Environment, Vols. 557-558, 2016, p. 110-122.
-
Persson P., Persson K., Sandberg G. Numerical study of reduction in ground vibrations by using barriers. Engineering Structures, Vol. 115, 2016, p. 18-27.
-
Connolly D. P., Marecki G. P., Kouroussis G., Thalassinakis I., Woodward P. K. The growth of railway ground vibration problems – a review. Science of the Total Environment, Vol. 568, 2016, p. 1276-1282.
-
Thompson D. J., Jiang J., Toward M. G. R., Hussein M. F. M., Ntotsios E., Dijckmans A., Coulier P., Lombaert G., Degrande G. Reducing railway-induced ground-borne vibration by using open trenches and soft-filled barriers. Soil Dynamics and Earthquake Engineering, Vol. 88, 2016, p. 45-59.
-
Kouroussis G., Vogiatzis K. E., Connolly D. P. A combined numerical/experimental prediction method for urban railway vibration. Soil Dynamics and Earthquake Engineering, Vol. 97, 2017, p. 377-386.
-
Feng S.-J., Zhang X.-L., Zheng Q.-T., Wang L. Simulation and mitigation analysis of ground vibrations induced by high-speed train with three dimensional FEM. Soil Dynamics and Earthquake Engineering, Vol. 94, 2017, p. 204-214.
-
Farghaly A. A., Kontoni D.-P. N. Train induced dynamic response of a pedestrian tunnel under a four-track surface railway for different soil water contents. Geomechanics and Engineering, Vol. 16, Issue 4, 2018, p. 341-353.
-
Xu S., Zhang L., Zhang P., Noh H. Y. An information-theoretic approach for indirect train traffic monitoring using building vibration. Frontiers in Built Environment, Vol. 3, Issue 22, 2017, p. 1-22.
-
Bose T., Choudhury D., Sprengel J., Ziegler M. Efficiency of open and infill trenches in mitigating ground-borne vibrations. Journal of Geotechnical and Geoenvironmental Engineering, Vol. 144, Issue 8, 2018, p. 04018048.
-
SAP2000® Version 17, Integrated Software for Structural Analysis and Design. Computers and Structures, Walnut Creek, USA, 2015, https://www.csiamerica.com/products/sap2000.
-
InsulFoam GeoFoam EPS22. https://www.insulfoam.com/wp-content/uploads/2014/04/10005-Geofoam-EPS22-TDS_WEB_-8-16.pdf.
-
Picoux B. Etude Théorique Et Expérimentale De La Propagation Dans Le Sol Des Vibrations Émises Par Un Trafic Ferroviaire. Ph.D. Dissertation, Ecole Centrale of Nantes, Nantes, 2002, p. 155, (in French).
-
Picoux B., Le Houédec D. Diagnosis and prediction of vibration from railway trains. Soil Dynamics and Earthquake Engineering, Vol. 25, Issue 12, 2005, p. 905-921.
About this article
The authors would like to express their gratitude to Dr. Benoit Picoux (Ass. Professor, Department of Civil Engineering and Durability, University of Limoges, France) for providing train accelerograms from measurements on a railway track for a current train.