Mechanical Engineering
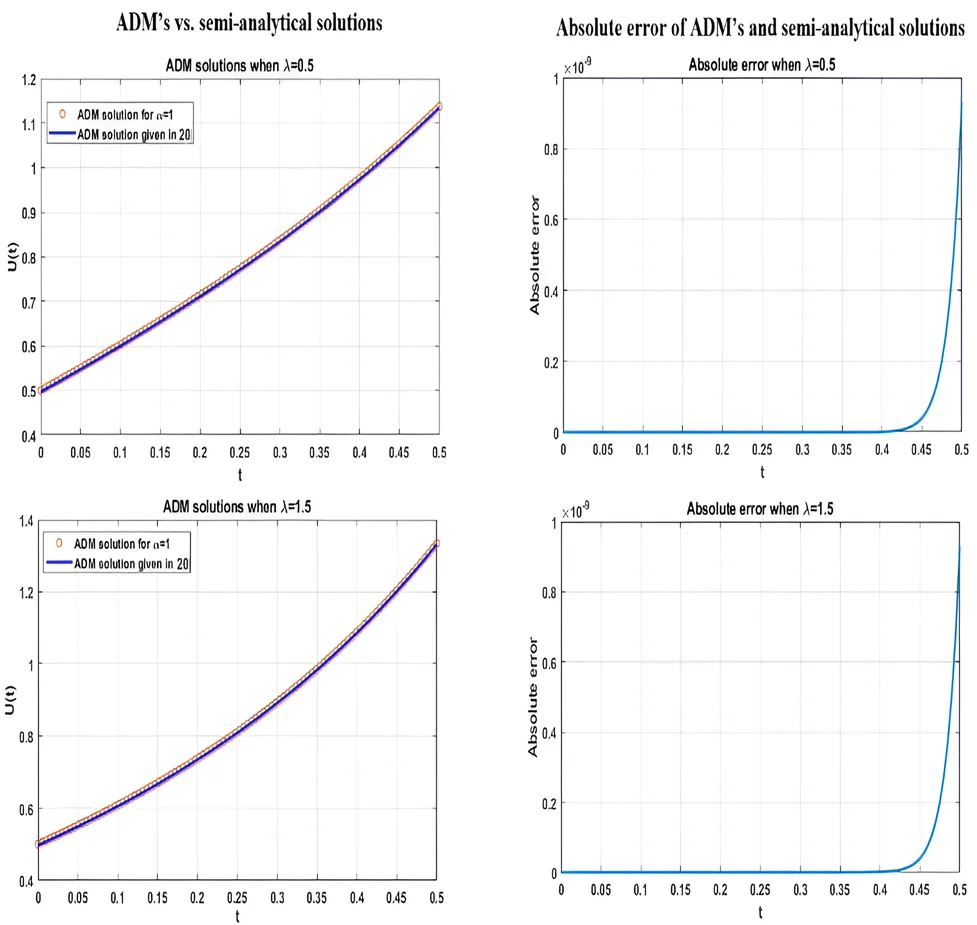
Editor's pick
Research Article
A simple harmonic quantum oscillator: fractionalization and solution
By Iqbal M. Batiha, Iqbal H. Jebril, Abeer A. Al-Nana, Shameseddin Alshorm
A quantum mechanical system that mimics the behavior of a classical harmonic oscillator in the quantum domain is called a simple harmonic quantum oscillator. The time-independent Schrödinger equation describes the quantum harmonic oscillator, and its eigenstates are quantized energy values that correspond to various energy levels. In this work, we first fractionalize the time-independent Schrödinger equation, and then we solve the generated problem with the use of the Adomian decomposition approach. It has been shown that fractional quantum harmonic oscillators can be handled effectively using the proposed approach, and their behavior can then be better understood. The effectiveness of the method is validated by a number of numerical comparisons.
March 2, 2024
Informatics
Most cited
Research Article
A portable breast cancer detection system based on smartphone with infrared camera
By Jian Ma, Pengchao Shang, Chen Lu, Safa Meraghni, Khaled Benaggoune, Juan Zuluaga, Noureddine Zerhouni, Christine Devalland, Zeina Al Masry
September 26, 2019
Biomechanics
Most cited
Research Article
Optimization of palm methyl ester and its effect on fatty acid compositions and cetane number
By Sharath Satya, Aditya Kolakoti, Naga Raju B., Shyam Sundar R., Ranga Rao
March 31, 2019
Informatics
Most cited
Research Article
Mathematical modeling of forced oscillations of semidefinite vibro-impact system sliding along rough horizontal surface
By Vitaliy Korendiy, Volodymyr Gursky, Oleksandr Kachur, Volodymyr Gurey, Oleksandr Havrylchenko, Oleh Kotsiumbas
December 2, 2021
Informatics
Most cited
Research Article
Performance of PID-Fuzzy control for cab isolation mounts of soil compactors
By Vanliem Nguyen, Renqiang Jiao, Vanquynh Le, Anhtan Hoang
December 31, 2019
Informatics
Journal of Mechanical Engineering, Automation and Control Systems
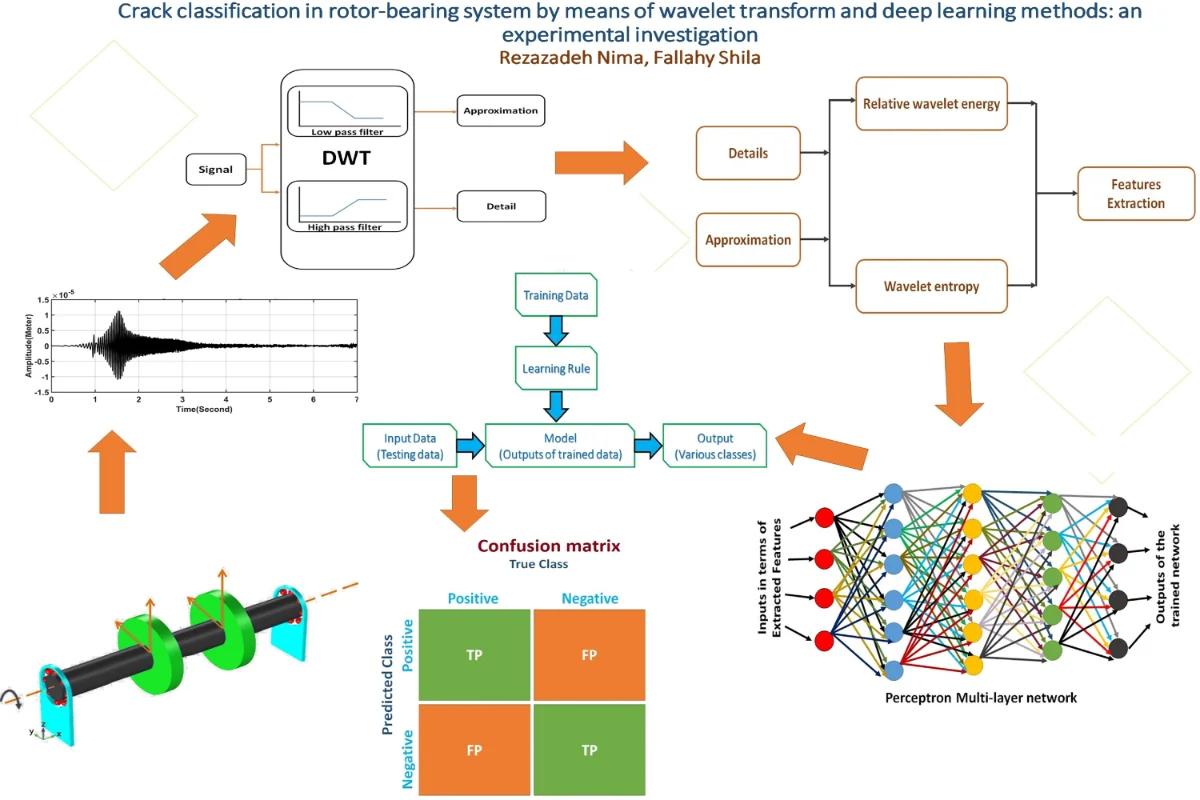
Research Article
Crack classification in rotor-bearing system by means of wavelet transform and deep learning methods: an experimental investigation
Parallel with significant growth in industry, especially mysteries related to energy engineering, condition monitoring of rotating systems have been experiencing a noticeable increase. One of the prevalent faults in these systems is fatigue crack, so finding reliable procedures in identification of cracks in rotating shafts has become a pressing problem among engineers during recent decades. While a vast majority of cracked rotors can operate for a specific period of time, to prevent catastrophic failures, crack detection and measuring its characteristics (i.e. size and its location) seem to be essential. In the present essay, a hybrid procedure, consisting of Deep Learning and Discrete Wavelet transform (DWT), is applied in detection of a breathing transverse crack and its depth in a rotor-bearing-disk system. DWT with Daubechies 32(db32) as wavelet mother function is applied in signal noise reduction until level 6, also its Relative Wavelet Energy (RWE) and Wavelet entropy (WE) are extracted. A characteristic vector that is a combination of RWE and WE is considered as input to a multi-layer Artificial Neural Network (ANN). In this supervised learning classifier, a multi-layer Perceptron neural network is used; in addition, Rectified Linear Unit (ReLU) function is exerted as activation function in both hidden and output layers. By comparing the results, it can be seen that the applied procedure has strong capacity in identification of crack and its size in the rotor system.
December 11, 2020
Industrial Engineering
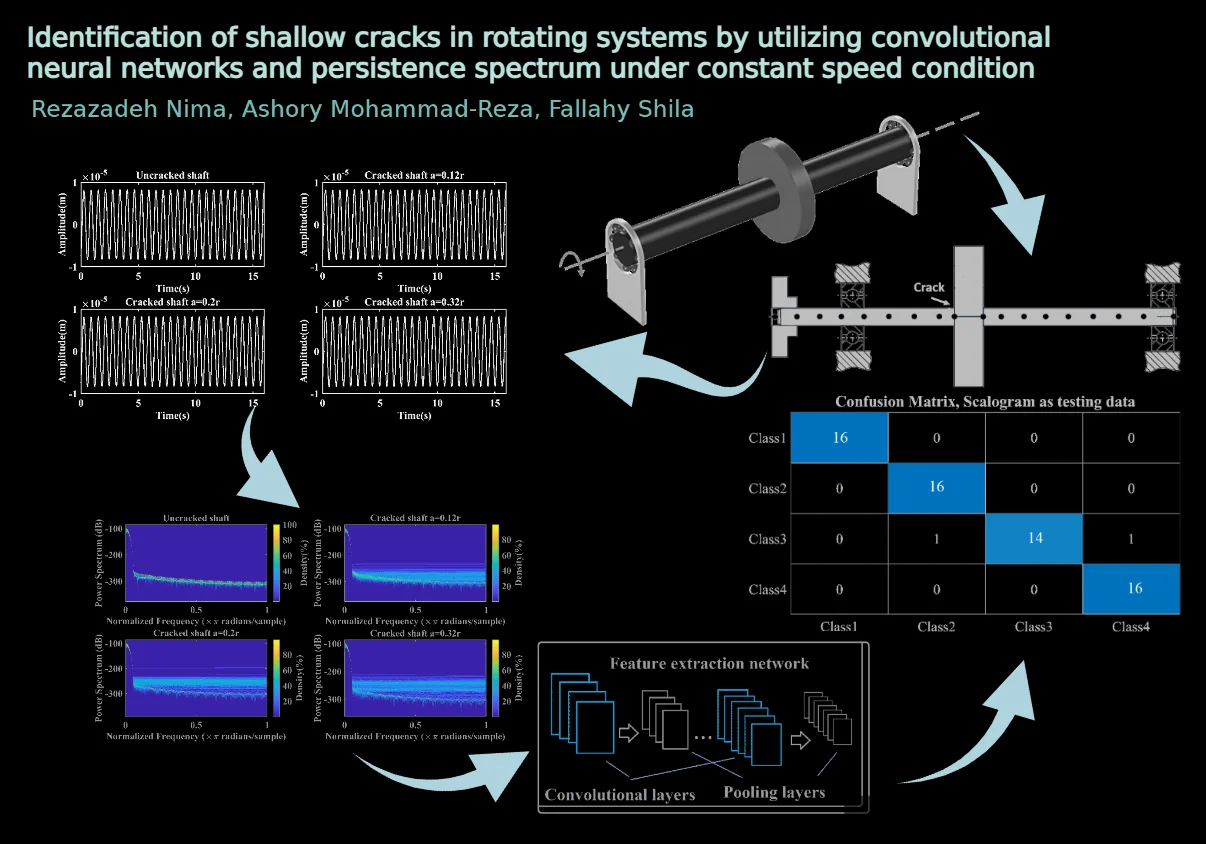
Research Article
Identification of shallow cracks in rotating systems by utilizing convolutional neural networks and persistence spectrum under constant speed condition
The positive benefits of early faults detection in rotating systems have led scientists to develop automated methods. Although unbalancing is the most prevalent defect in rotor systems, this fault normally is accompanied by other defects such as crack. In this article, an effective self-acting procedure is addressed in identifying shallow cracks in rotor systems throughout the steady-state operation. To classify rotor systems suffering cracks with three various depths, firstly, healthy and cracked systems are modeled by employing the finite element method (FEM). In the following, systems' vibration signals are calculated in different situations numerically; for pre-processing stage, the persistence spectrum is implemented. Finally, by using a supervised convolutional neural network (CNN), rotor systems are classified by regarding the crack depths. The result of the testing step revealed that this hybrid method has rational capacity in distinguishing shallow cracks in steady-state operation where many other methods are somehow powerless.
December 15, 2021
Industrial Engineering
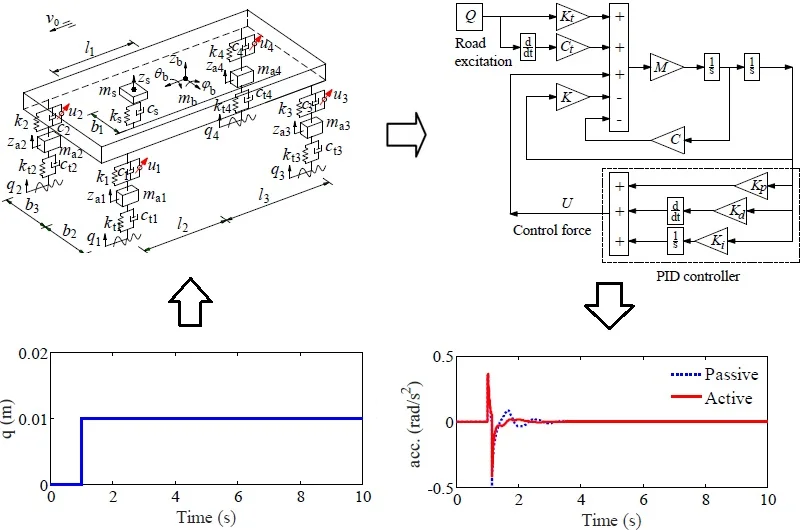
Research Article
Control performance of suspension system of cars with PID control based on 3D dynamic model
To evaluate the control performance of the PID controller for the cars, a 3D car dynamic model with 8-DOF which can fully reflect the pitch and roll of the car body is proposed in this study. The PID controller is then researched and applied to control the active suspension system of the cars under the different excitations of the road surface and the various car speeds. The control performance for improving the ride comfort of the driver is evaluated via the root-mean-square (RMS) of acceleration responses of the vertical driver’s seat, pitching and rolling car body angles. The research results show that the PID controller for the car suspension system have an obvious impact on reducing the vibration and controlling the car body shaking in comparison with the passive suspension system.
June 30, 2020
Industrial Engineering
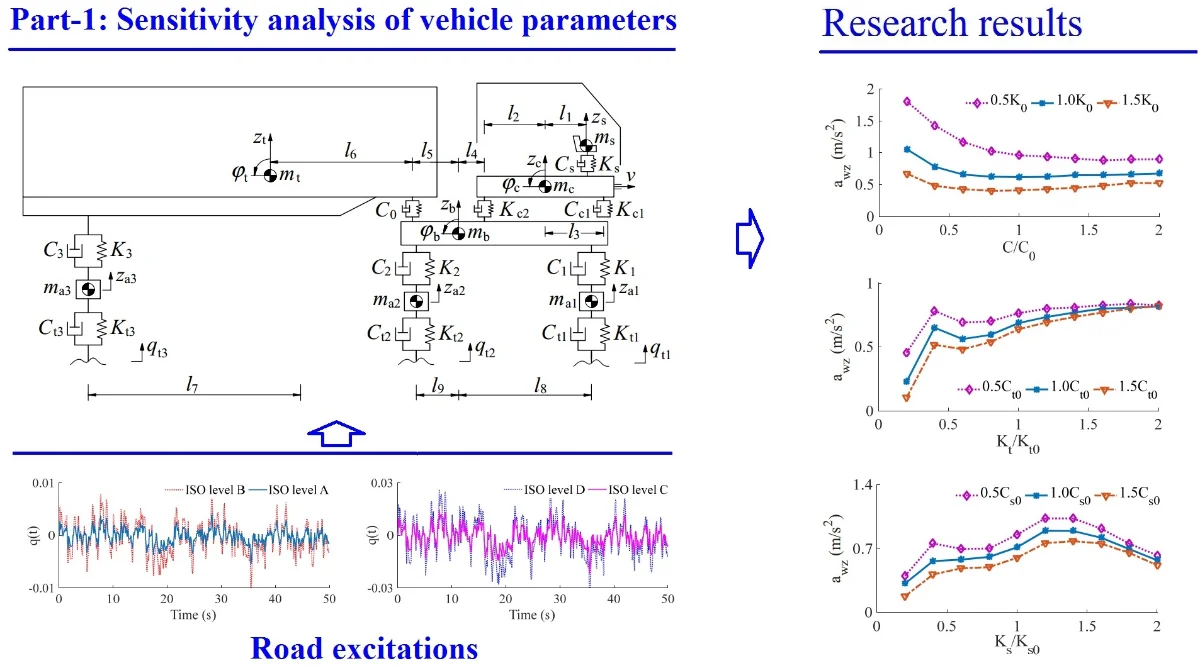
Research Article
Vibration research of heavy trucks. Part 1: Sensitivity analysis of dynamic parameters on ride comfort
In order to study the influence of heavy truck dynamic parameters on the vehicle’s ride comfort under the random road excitation, the weighted RMS (root-mean-square) acceleration responses of the vertical driver’s seat and cab pitch angle are chosen as objective function, a dynamic model of the vehicle with 10 degrees of freedom is established to simulate and analyze the results. The influence of different parameters of all the suspension systems of the vehicle, such as the stiffness and damping of the suspensions of the seat, cab, vehicle, and wheel, on the vertical driver’s seat and cab pitch angle are respectively analyzed. The study results show that the influence of the stiffness and damping parameters in the suspension systems on the vehicle ride comfort is very obvious. The vehicle’s ride comfort changes worse with the increase of the suspension stiffness and the reduction of the suspension damping, and vice versa. The study proposes an optimal range of the stiffness and damping parameters for the optimal design and control of the vehicle suspension systems, concurrently, the study can also provide a theoretical basis for the suspension system designed for heavy trucks.
December 11, 2020
Industrial Engineering
Journal of Mechanical Engineering, Automation and Control Systems
Novel and innovative insights to the field of mechanical engineering
APC
Free of charge
Best of Theme
Most cited
Research article
June 2, 2020
Optimization and modelling of mahua oil biodiesel using RSM and genetic algorithm techniques
By Aditya Kolakoti, Panchanand Jha, Prakasa Rao Mosa, Manohar Mahapatro, Tulasi Ganesh Kotaru
Most cited
Research article
August 11, 2021
Positioning algorithm for AGV autonomous driving platform based on artificial neural networks
By Patryk Bałazy, Paweł Gut, Paweł Knap
Most cited
Research article
November 28, 2019
Dynamic pressure on lock gate structure coupled with fluid
By Deepak Kumar Singh, Priyaranjan Pal, Shashi Kant Duggal
Most cited
Research article
October 19, 2020
An improved mesh stiffness calculation model of spur gear pair under mixed EHL friction with spalling effect
By Siyu Wang, Rupeng Zhu
You might also like
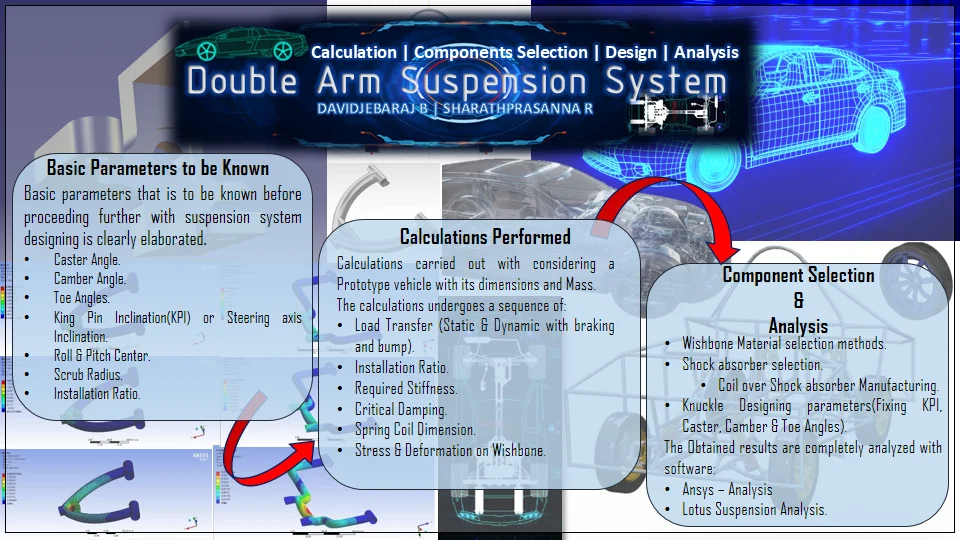
Most downloaded
Research Article
Design and calculation of double arm suspension of a car
By David Jebaraj B, Sharath Prasanna R
Suspension system is one of the challenging portions in designing a vehicle. The complete stability of the vehicle under dynamic conditions depends on the suspension system of the vehicle. Suspension system of a vehicle is interlinked with other systems such as steering, Wheels and Brakes. The main objective of this document is to provide complete guidance in designing and calculation of an independent suspension system with double control arms. The required parameters are calculated on considering a prototype vehicle with gross weight of 350 kg such as required stiffness of shock absorbers, Ride frequency, Motion ratio, Coefficient of damping etc. A CADD model was made with CATIA v5 r20 and SOLIDWORKS on the basis of calculations obtained and stress analysis was carried out for this model in various software such as Ansys. The complete assembled model was tested in LOTUS Shark and the result was obtained.
June 30, 2020
Industrial Engineering
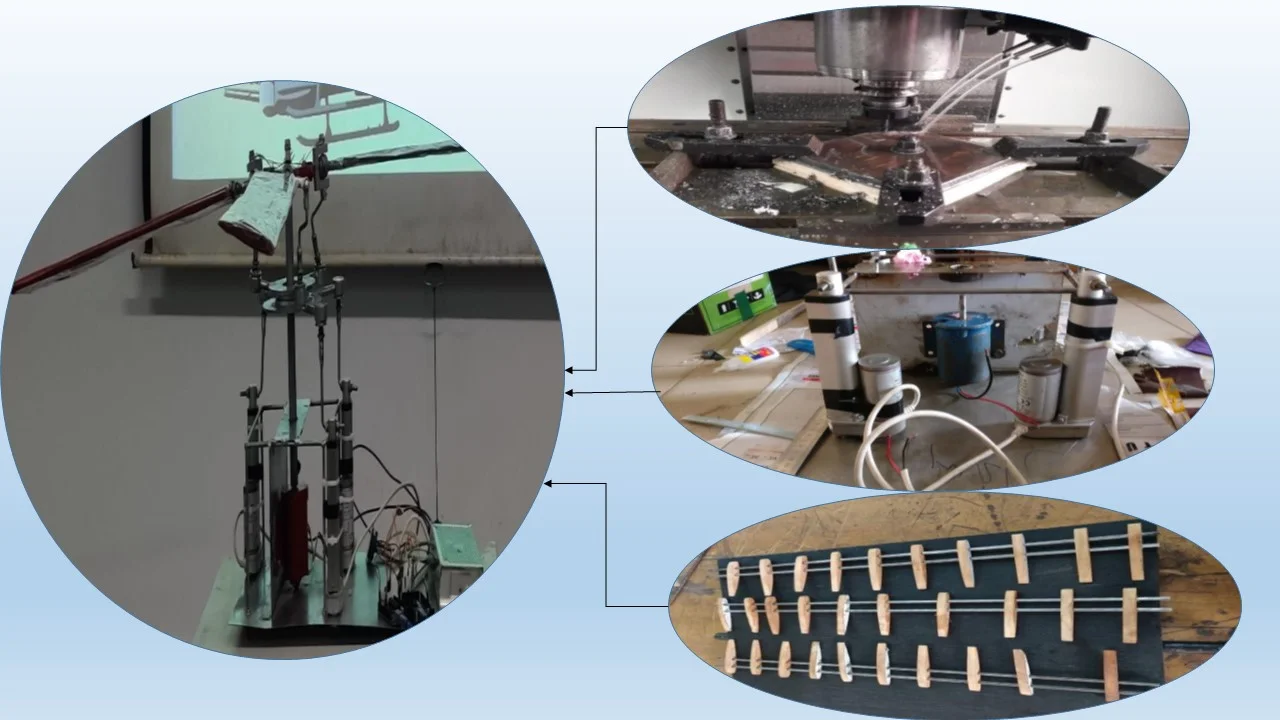
Most downloaded
Research Article
Design, analysis and fabrication of a fully articulated helicopter main rotor system
By Arafat Ahmed Shamol, Samin Yaser Ahmed, Md. Ariful Islam Shubho, Towsibur Rahman
This study describes an integrated framework in which the basic elements of Aerospace Engineering (performance, aerodynamics and structure) and functional elements (suspension, visibility and production) are integrated and considered. In this study, a fully functional rotor system has been fabricated that can be used as one of the training resources for Aeronautical students. For making the rotor system, various parts of the system have been designed on Solidworks and complete mechanism has been simulated with ANSYS. System analysis has been done at various RPM's and Angles of Attack (AOA). In terms of merit the right items have been selected and processed to provide them with the right shape. In terms of the design and implementation, various machines such as gas welding, arc welding, CNC milling and radial machinery have been used. Certain parts such as electric motors, linear actuators and loading cells have been used. All the fabricated components and electric motor, actuator, load cells are then assembled. This rotor system can produce less lift due to high dead weight and low power motor and having some safety issues.
June 11, 2021
Industrial Engineering
Mathematical modeling of first order process with dead time using various tuning methods for industrial applications
The proposed research involves Mathematical modeling for first order process with dead time using various tuning methods for industrial applications. Different tuning methods are proposed. Proposed method selection depends on plant operating conditions and also depending upon the process dynamics. The PID controller is most widely used for industrial process control. Modeling were developed for modified internal control model [4-6] in this proposed research. The proposed work is the modeling and simulation of three different first order processes with dead time. The standard controller tuning method is used to obtain the steady state response of first order with dead time.
Dynamic analysis of offshore wind turbine blades under the action of wind shear and fluctuating wind
Aiming at large-scale offshore wind turbine blades, governing equations in fluid domain and motion equations in structural domain with geometric nonlinearity were built by the aid of ALE method. A three dimensional model under fluid-structure interaction (FSI) was established by using UG software and Geometry module, and numerical calculation for FSI vibration characteristics of wind turbine blades under the effects of wind shear and fluctuating wind was carried out based on ANSYS Workbench. The results indicate that the contribution of the combined action to displacement and Mises stress chiefly derives from the wind shear effect, which not only causes a comparatively larger increase for the maximum displacement and Mises stress, but also becomes bigger and bigger with the increase of average wind speed, and the fluctuating wind effect is insignificant. The maximum value of Mises stress in the blade section appears at the relative wingspan of 0.55, the maximum Mises stress varying with relative span length decreases progressively from the middle to both sides of the blade, and the contribution of wind shear effect alone, the combined action or wind speed increment to stress also shows the same change rule. Furthermore, in the maximum stress section along wingspan, Mises stress along the direction of blade thickness or chord length respectively presents two distribution laws, and reaches the maximum on the blade surface.