Vibration Engineering
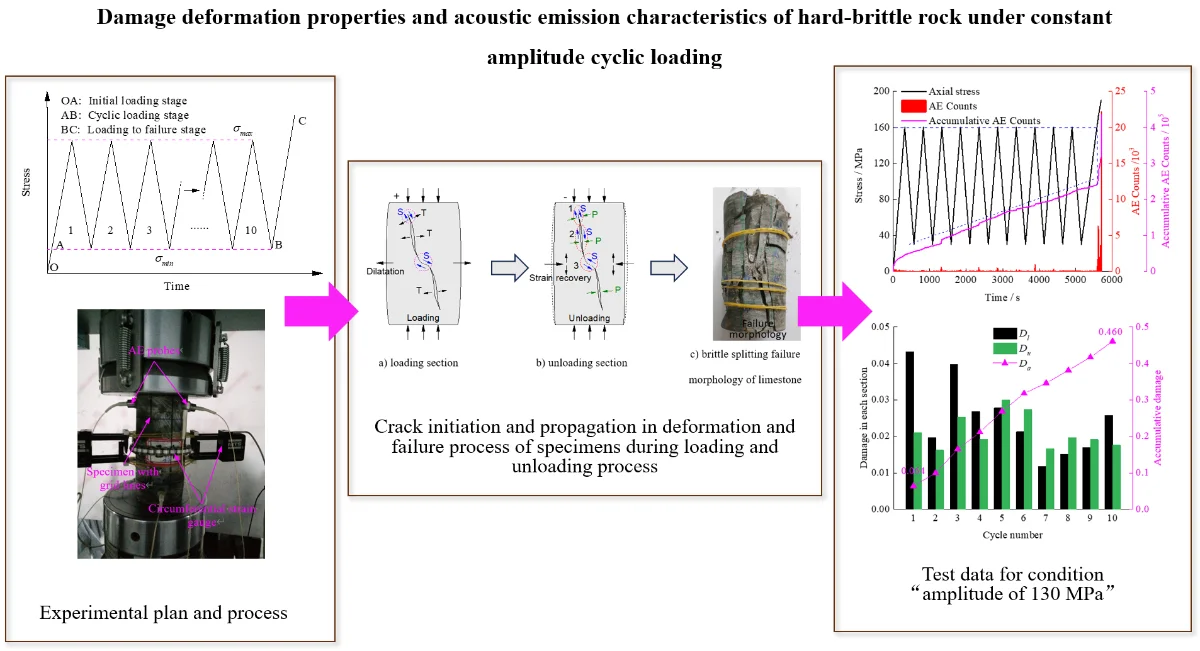
Journal of Vibroengineering
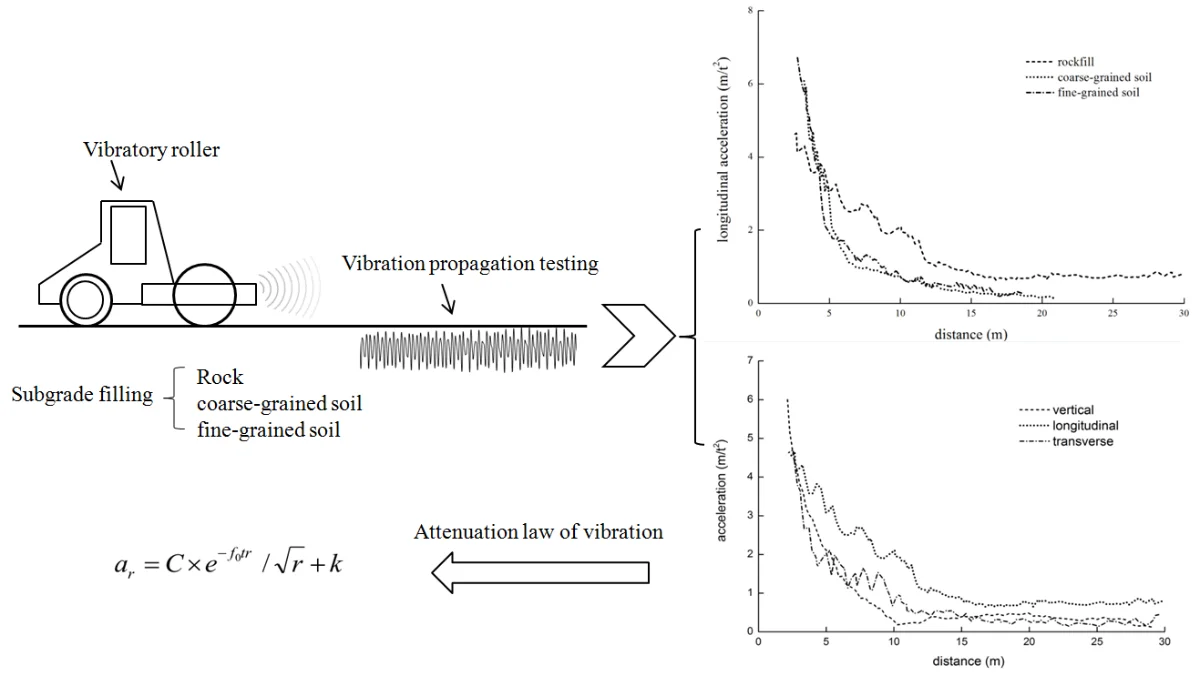
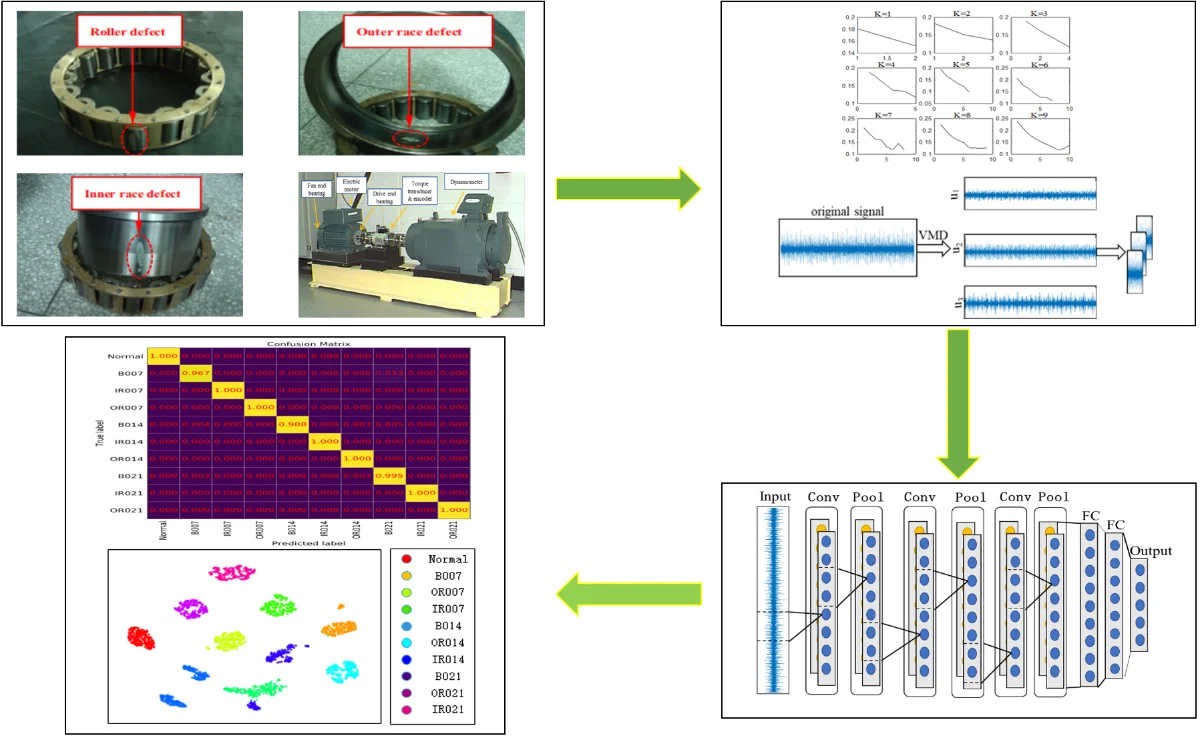
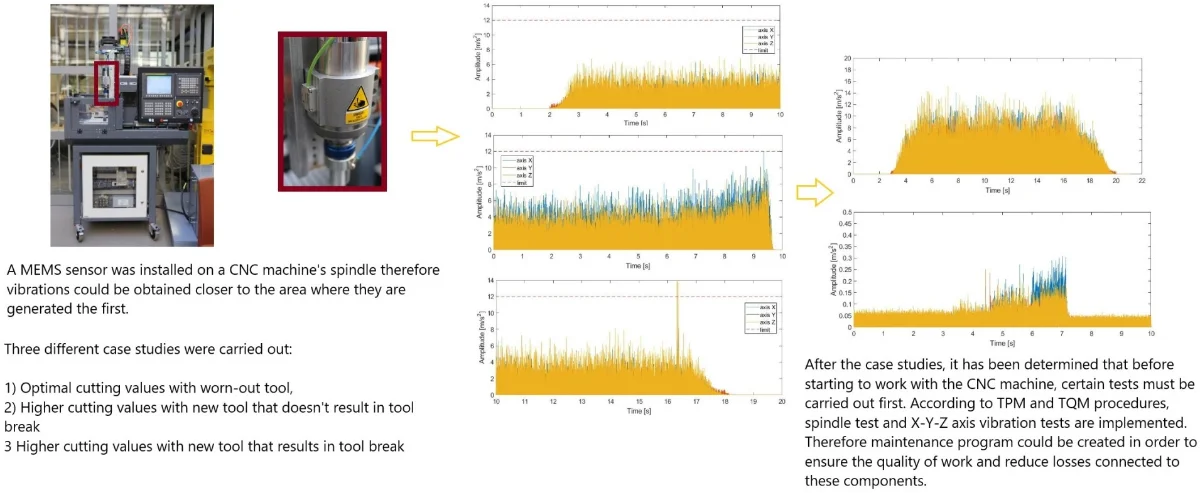
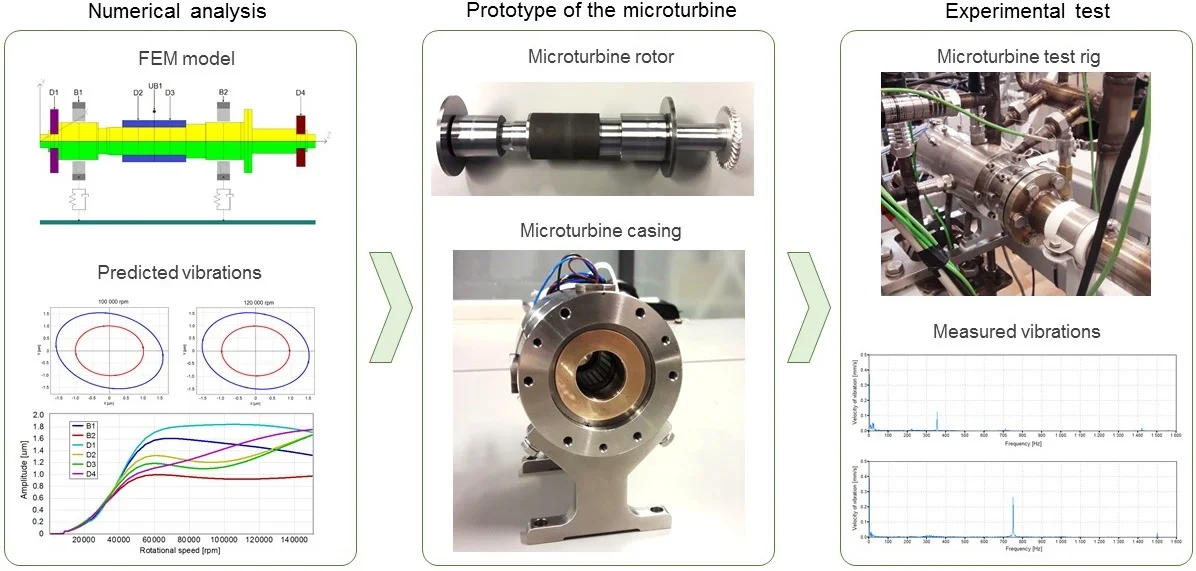
Comprehensive platform for advancements in the field of vibration engineering
Best of Theme
You might also like
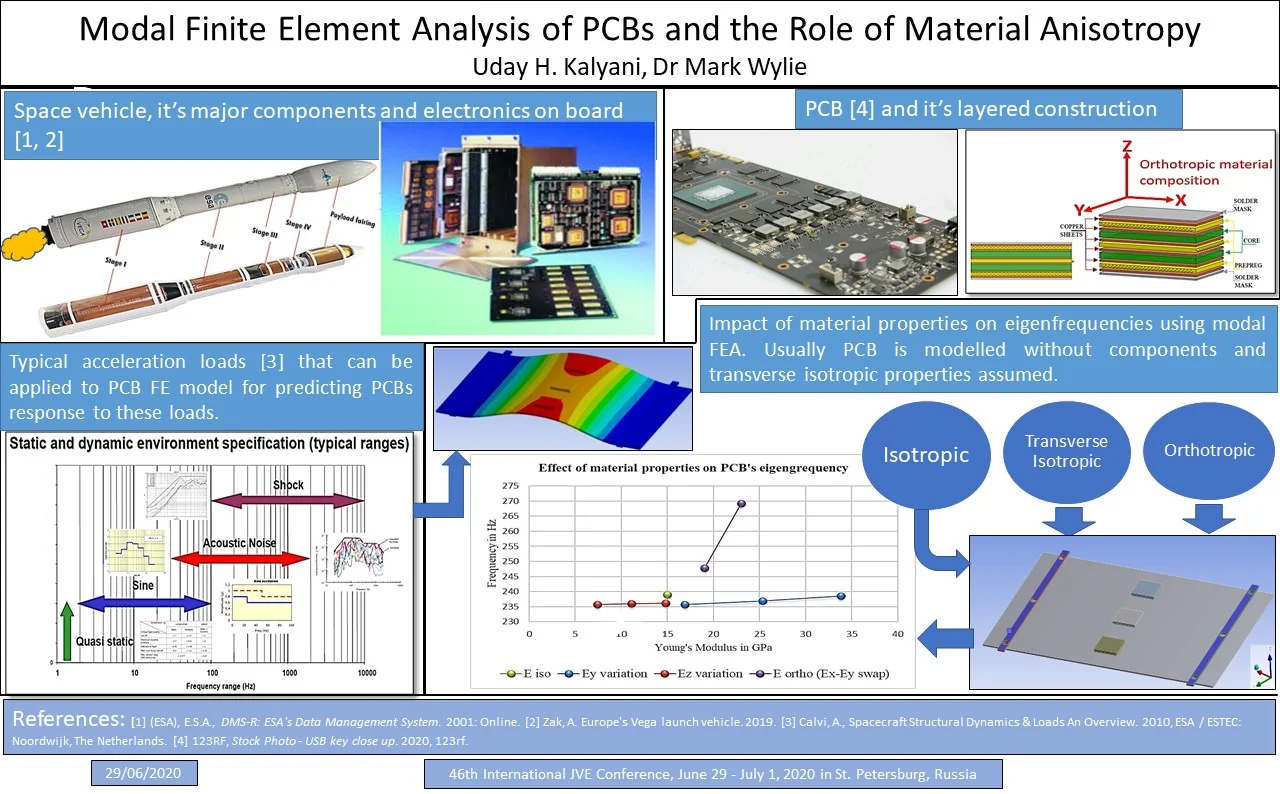
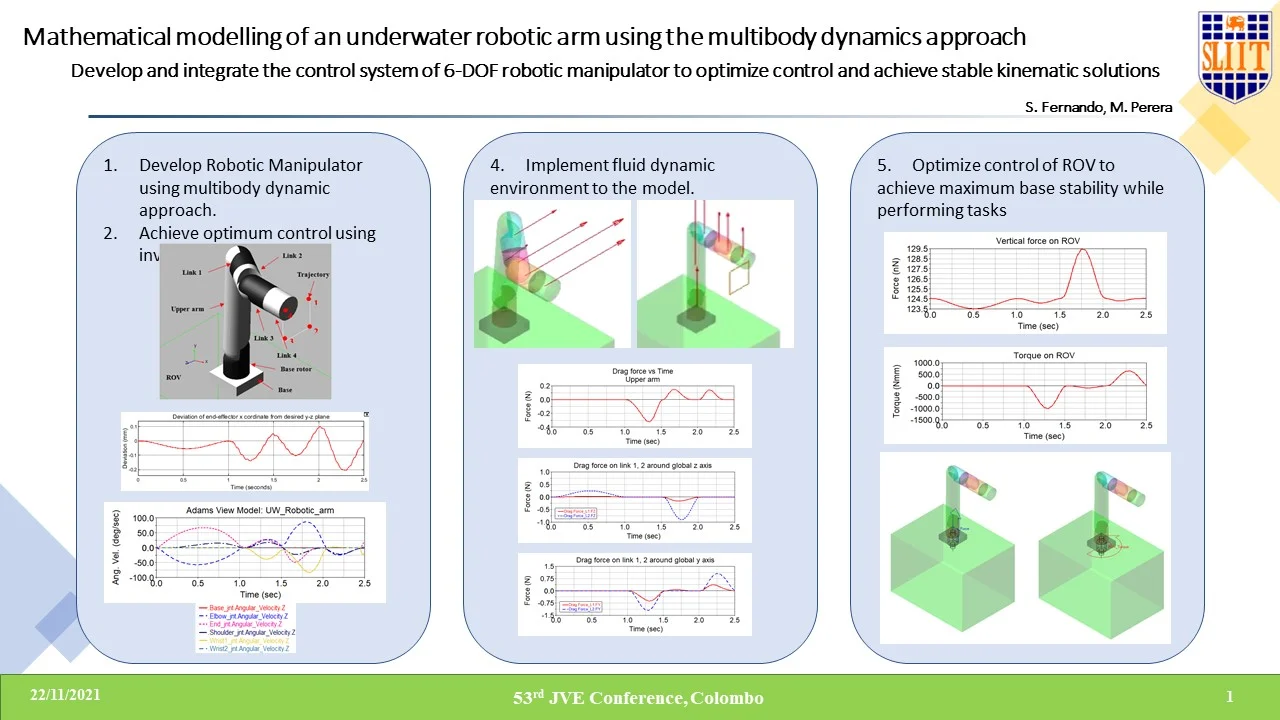
Welcome to Extrica's hub for Vibration Engineering
A leading source for open access journals in the science and engineering realms. Here, you'll find comprehensive coverage of all things related to vibration engineering. Whatever your research or interest in vibration engineering, we provide extensive resources to support your exploration.
Understanding Vibration Engineering
Dive into the world of vibration engineering with an introduction to its core concepts. This field delves into the study of mechanical vibrations and their impact on various structures. Vibration in mechanical engineering is about understanding the oscillatory motions of mechanical systems from their equilibrium positions. Key principles in this area include free and forced vibrations, harmonic motion, damping, natural frequency, and resonance.
Practical Applications in Vibration Engineering
Vibration analysis is crucial across various industries. Applications range from structural health monitoring and aerospace engineering to machinery health, power generation, seismology, consumer electronics, medical imaging, entertainment, and earthquake engineering. These real-world uses underscore the field's significance.
Innovations in Vibration Mitigation
Discover the latest technological breakthroughs in vibration mitigation, enhancing the performance and longevity of various systems. Innovations aim at noise reduction, precision improvement, and increased comfort and safety. The field has evolved through passive and active vibration mitigation techniques, marking significant progress in vibration engineering.
Case Studies in Vibration Engineering
Learn from real-world scenarios where vibration engineering principles have been applied to resolve challenges. For instance, a case study at a hydroelectric dam highlights how addressing vibration issues, due to Rheingans influence, led to redesigning turbine blades, thereby solving the resonance problem.
Your Vibration Engineering Resource
With a solid understanding of vibration engineering's principles and advancements, professionals in this field can make significant contributions across various sectors. Staying updated with the latest developments is key to innovating and ensuring safety in vibration-related projects. Extrica provides the knowledge and tools necessary for tackling vibration challenges effectively.